倣いフライス加工とは?
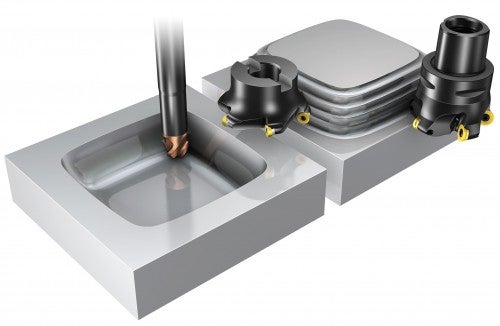
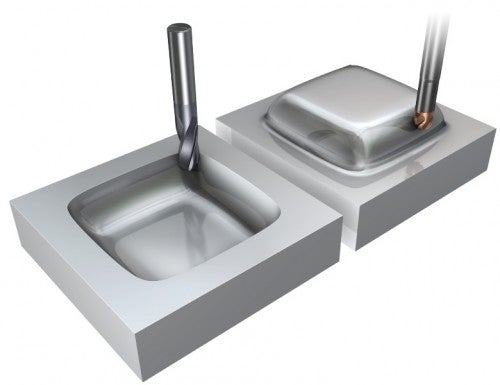
倣いフライス加工は一般的なフライス加工です。 丸チップカッターとR付きコンセプトは、荒加工と中荒加工用のフライスカッターです。一方、ボールエンドミルカッターは、仕上げと超仕上げ用のフライスカッターです。
倣いフライス加工プロセス
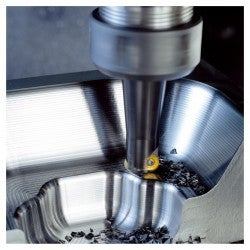
倣いフライス加工とは、二次元および三次元での凸状および凹状形状の多軸フライス加工全般のことです。ワークが大きければ大きいほど、加工する形状が複雑であればあるほど、倣いフライス加工のプロセス計画がますます重要になります。
加工プロセスは少なくとも3つの分けることができます。
- 荒加工/中荒加工
- 中仕上げ加工
- 仕上げ加工
しばしば高速加工技術を使用して行なわれる超仕上げが、必要になることがあります。残りの取代のフライス加工は、レストミリングとも呼ばれ、中仕上げと仕上げ加工に含まれます。最良の精度と生産性を達成するには、 荒加工と仕上げを別々の機械で行ない、それぞれの加工にお最適な切削工具を使用することをお勧めします。
仕上げ加工は、最新のソフトウェアとプログラミング機能を備えた4/5軸工作機械で行なう必要があります。これにより、時間のかかる手作業による完成作業を大幅に低減、または完全になくすことができます。最終仕上がりは、良好な形状精度と高い加工面品質のある製品です。
工具の選び方
荒加工と中荒加工用の最適な切削工具:
丸チップカッターとR付きコンセプト。
仕上げと超仕上げ用の最適な切削工具:
ボールエンドミルカッターとR付きコンセプト。
![]() | ![]() | ![]() | ![]() | |
丸チップカッター | 刃先交換式ボールエンドミル | 刃先交換式ボールエンドミル - ヘッド | 超硬ボールエンドミル | |
機械 / スピンドルサイズ | ISO 40, 50 | ISO 40、50 | ISO 30、40 | ISO 30, 40 |
剛性要件 | 高い | 中加工 | 中加工 | 低 |
荒加工 | 非常に良好 | 良好 | 許容範囲 | 許容範囲 |
仕上げ加工 | OK | OK | 非常に良好 | 非常に良好 |
切込み ap | 中加工 | 中 | 小 | 小 |
汎用性 | 非常に良好 | 非常に良好 | 非常に良好 | 非常に良好 |
生産性 | 非常に良好 | 良好 | 良好 | 優れている |
倣いフライス加工の加工チェックリスト
ワークの形状を慎重に確認して正しい工具を選択し、最適な加工方法を見つける必要があります。
- 最小コーナRとキャビティー深さを決めます
- 除去する被削材の量を見積ります
- びびりを回避するために、工具のセットアップとワークのクランプを検討しますすべての加工を最適な機械で行ない、倣い加工の良好な形状精度を達成してください
- 仕上げ加工と超仕上げ加工にはそれぞれ別々の精確な工作機械を使用すると、時間がかかる手作業の研摩の手間を低減、または場合によっては省くことができます
- 時間を大幅に節約するには、最新のプログラミングが必要になります。高速対応の超硬エンドミルカッターを使用して、ニアネットシェープを加工すると、最高の仕上がりを達成できます
- 大型ワークの荒加工と中仕上げでは原則として、従来の加工法とツーリングにより非常に高い生産性が得られます。荒加工でも高い切削速度を使用するアルミ合金は例外です
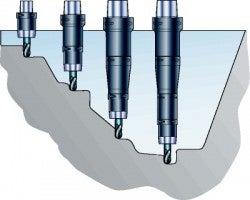
びびりの低減方法
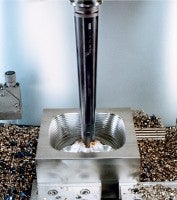
びびりは、長い突き出し量での深いプロファイルにおけるフライス加工ではひとつの障害です。. この問題を克服する一般的な方法としては、切込みと送り速度を低くします。
- 振れ精度の良好な、高剛性のモジュラー式工具を使用します
- モジュラー式工具は、適応性が高く、組み合わせが豊富です
- 全工具長(ゲージライン~刃先の一番低いポイント)がゲージラインのところで径の4–5倍を超える場合は、防振型工具またはエクステンションバイトを使用します
- 径方向の曲げ剛性を大きくする必要が ある場合は、重金属製のエクステンションを使用します
- 20,000 rpm以上のスピンドル回転数に対しては、バランス調整した切削・ホールディングツールを使用します
- エクステンションとアダプタでは、カッター径と比べてできる限り大きな径を選択します
- 保持工具と切削工具間の径の差が1 mm (0.039 inch) あれば十分です。オーバーサイズカッターの使用
- プランジ加工は、エクストラロング工具を使用したフライス加工の代替加工法です
工具長を徐々に延長します
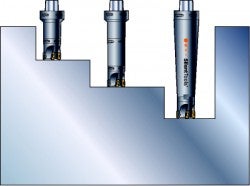

最終パスがワークの深い部分になる場合の荒加工で、最高の生産性を維持するには、カッター用の一連のエクステンションを使用して加工することが大切です。
- 長めのエクステンションでは生産性が制限されびびりも発生しがちですので、エクステンションの選定は、一番長さの短いものから始めるようにします。
- プログラムで事前設定した位置で延長工具を変えます。キャビティの形状により、交換ポイントが決まります。
- それぞれの工具長に切削条件を適用して、最高の生産性を維持します。
実質切削速度
ボールノーズカッターまたは丸チップカッターの切削速度を計算する際に工具の呼び径の値を使用すると、切込み ap が浅い場合は、実質切削速度 vc がずっと低くなります。これは、テーブル送りと生産性にとって非常に不利なものとなります。
実質または有効切込み Dcapにおける切削速度の基本計算。
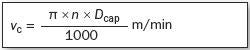
肩削りエンドミルカッター
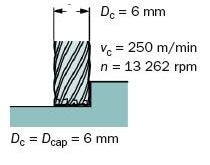
ボールノーズカッター
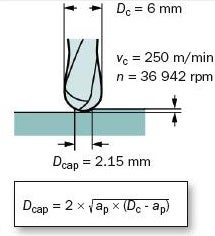
丸チップカッター
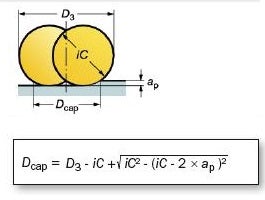
ポイントフライス加工 – 傾斜カッター
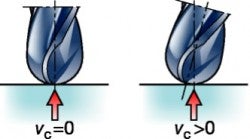
ボールノーズエンドミルを使用する場合、最も問題となる領域は工具中心部です、この領域では切削速度がほとんどゼロに近くなりますが、これは切削プロセスにとっては好ましくないことです。チゼルのスペースが狭いため、工具中心では切くずの排出が問題となります。
このため、スピンドルまたはワークを10~15°傾けてセットすることをお勧めします。これにより、工具中心から切削領域がなくなります。
- 最低切削速度が高くなります。
- 良好な工具寿命と切りくず生成
- 良好な加工面品質
センターカットカッターの例
中心部分、z = 2
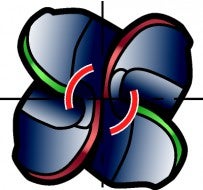
外周部分、z = 4
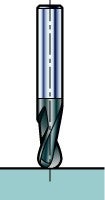
Z = 2
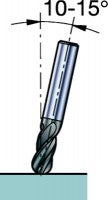
Z = 4
浅い切削
丸チップカッターまたはボールノーズカッターを小さい切込みで使用すると、刃先の食いつき時間が短くなるため、切削速度 vc を上げることができます。刃先が熱をもつ時間が短くなり、刃先とワークの温度が低く保たれます。また、切りくずが薄くなる効果により、刃当たり送り fz を上げることができます。
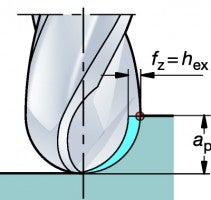
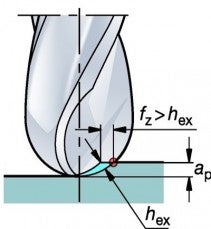
浅い切削
浅い切削の例、非傾斜 対 傾斜カッター
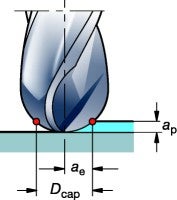
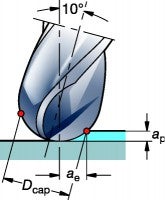
この例は、ae/ap を小さくすると、傾斜カッターを使用するメリットと相まって、切削速度を上げられることを示しています。
超硬ボールノーズ カッター
Dc = 10 mm、材種GC 1610.
被削材: 鋼、400HB
切込み ap - Dc/2 時の推奨切削条件:
vc = 170 m/min
fz = 0.08 mm/r = hex
加工内容 | 非傾斜カッター | 傾斜カッター (10°) |
中仕上げ ap - 2 mm (0.079 inch)
vc - 300 m/min (984 ft/min)
刃当たり送り fz は、非傾斜カッター、傾斜カッターとも同じですが、 | Dc = 10 mm (0.394 inch)
vc = 300 m/min (984 ft/min)
hex = 0.08 mm (0.003 inch)
vf = 2 860 mm/min (113 in/min) | Dc = 10 mm (0.394 inch)
vc = 300 m/min (984 ft/min)
hex = 0.08 mm (0.003 inch)
vf =5 100 mm/min (201 in/min) |
超仕上げ ae - 0.1 mm
vc - 5 * 170 - 850 m/min (557–2789 ft/min)
注意: 超仕上げでは、2枚刃カッター zn = 2を 使用して、振れを最小にします。
fz - 0.12 mm/z (0.005 in/z) | 非傾斜カッターは、超仕上げには お勧めできません | Dc = 10 mm (0.394 inch)
vc = 850 m/min (2789 ft/min)
hex = 0.02 mm (0.0008 inch)
vf =14 600 mm/min (575 in/min) |
倣いフライス加工における生産性: 取り代が一定であること
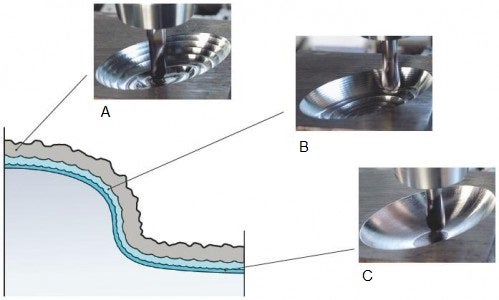
A: 荒加工
B: 中仕上げ
C: 仕上げ加工と超仕上げ
取り代が一定であることは、倣いフライス加工における高い安定した生産性のための非常に基本的な基準です。高送りを使用する場合は特に大切です。
- これらの加工で最高の生産性を達成するには、金型作成で一般的なように、それぞれの加工に合ったサイズのカッターを適用することが大切です
- まずもって、削り代または取代を均等に配分して、使用する各工具においてワーク荷重と方向の変化を少なくすることを目指します。
特に軽荒加工や中仕上げにおいて、1つの加工で1つのカッターのみを使用するのではなく、さまざまなカッターのサイズを、大から小へと下げていくとメリットがある場合がよくあります。
- 仕上げ加工での最高品質は、それ以前の加工において、取代の残量ができる限り少なく、一定であることで達成されます。
- 目標は常に、最終形状に対して指定された要件にできる限り近づけることです
- 安全な切削プロセス
取り代が一定であることのメリット
- いくつかの中仕上げや実際すべての 仕上げ加工は、一部は手動で、または時々は無人で(機械で)行なうことができます。
- 工作機械のガイドウェイ、ボールスクリューおよびスピンドルベアリングへの影響は少なくありません。
中実ワークからの加工
- キャビティーをあけるときは、ap を最小にする加工法を選ぶことと、後続の倣いフライス加工のために一定の取代を残すことも大切です。
- ショルダー 正面/エンドミルカッターまたはロングエッジカッターでは、階段状の取代が残り、これを取り除く必要があります。この作業では、切削抵抗が変動し、工具のたわみが発生します。結果として仕上げ加工の際に不均等な取代が残り、最終形状の形状精度の影響を及ぼします
- 丸チップカッターを使用すると、パス間の軌跡が滑らかで、倣い加工用にさらに均等な量の少ない取代が残り、良好なワーク品質を達成できます
- 3つ目の代替加工は、高送りカッターを使用してキャビティーをあける方法です。この方法でもまた、小さい切込み(小さい階段状)により、小さく、さらに一定の取代が残ります
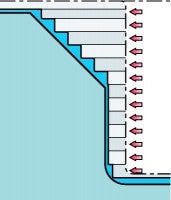
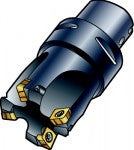
スクエア肩削りカッター,
大きく不均等な取代が残る
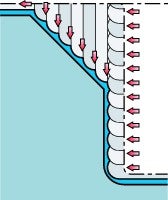
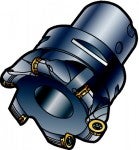
丸チップカッター,
小さな取代が残る
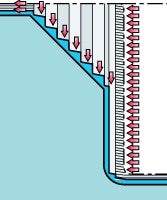
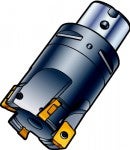
高送りカッター、
小さな取代が残る
コピーミリング
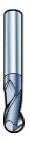
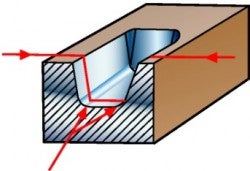
キャビティ用のツールパスをプログラムする従来の最も簡単な方法は、被削材への食いつきと抜け回数が多い、通常の倣いフライス加工を使うことです。しかしながらこれは、ソフトウェアプログラム、機械、切削工具を、その高い性能を十分に発揮させることなく使用することになります。このため、ツールパスが逸れるのを回避するための機能を備えたソフトウェア付きの機械を使用するのが良いでしょう。
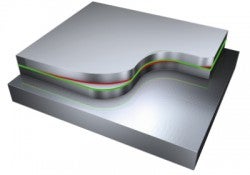
先入観を排したアプローチで、加工方法、ツールパス、フライス加工およびホールディングツールを選定することが大切です。
− チップ中心点の重切削負荷
− 低い送り速度
− 短い工具寿命
− 機械的な衝撃
− 形状エラー
− より長いプログラムと加工時間
倣いフライス加工パスはしばしばアップカットとダウンカットの組み合わせで、切削において好ましくない食いつきや抜けが何回も必要になります。それぞれの入り際や抜け際では工具がたわみ、加工面に段差のある傷痕が残ります。切削抵抗と工具のたわみが低くなり、抜け際において被削材のわずかなぬすみ加工が必要になります。
結論
- 急勾配の壁に沿ったコピーミリングはできる限り避ける必要があります。プランジ加工では、切りくず厚さが大きくなるため、切削速度を下げること
- 特にカッターが底面に当たると、工具中心で切れ刃が剥離するリスクがあります
- 先読み機能を使用して送り速度を制御してください。そうしないと、減速が遅くなり、工具中心へのダメージを避けられません
- カッターが壁に当たると、接触長さが大きくなり、たわみ、びびりまたは工具欠損のリスクが生じます。
- ボールエンドミルカッター使用時の最も重要な部分は、切削速度がゼロになる工具中心です。工具中心部分の使用を避けて、スピンドルまたはワークを傾けてポイントフライス加工を使用して、加工条件を改善します
- 好ましい切削速度では切りくず厚さが最大になるため、急勾配の壁に沿った切削プロセスとしてはアップカットで倣い加工を行なうほうが若干良くなります
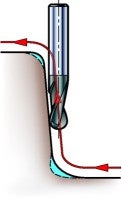
抉れのリスク
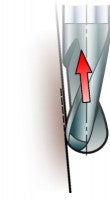
アップカットの倣い加工:
推奨vcでの最大切りくず厚さ
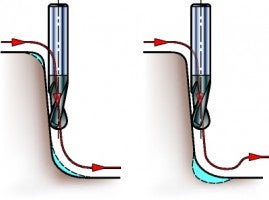
キャビティの底で:
工具中心でつぶれるリスク。
特に高速加工方法を使用すると、形状エラーは一般的な問題です。
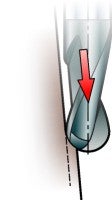
ダウンカットの倣い加工:
非常に低いvcでの大きな切りくず厚さ
送りを下げて工具寿命の短縮を避ける
アップカットとダウンカットを繰り返すと、工具が変動するたわみと切削抵抗にさらされます。ツールパスの重要部分で送り速度を下げることで、切れ刃が剥離するリスクが下がり、安全な切削プロセスと長い工具寿命が得られます
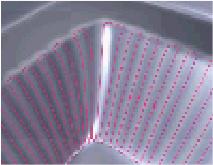
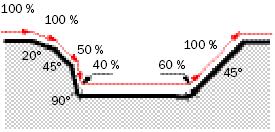
輪郭加工
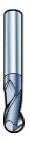
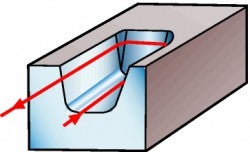
一定のZ値で被削材の「削り取り」に限定したプログラミング手法を使用する代わりに、輪郭削り加工ツールパスをダウンカットと組み合わせて使用すると大きなメリットがあります。以下の結果が得られます:
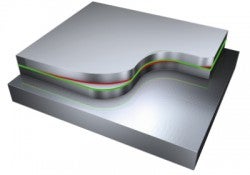
+ 大幅に短い加工時間
+ より良い機械と工具の活用
+ 加工済み形状の良好な形状品質
+ 時間のかかる仕上げ加工と手動研磨作業時間を低減
+ 切削速度制御 - ve
+ HSMが可能
+ 高送り速度
+ 長いチップ寿命
+ 安全性
初めのプログラミング作業は、より難しく幾分長くかかります。しかしながら、時間当たりの機械コストは通常、ワークステーションの3倍のため、これはすぐに取り戻せます。このため、ツールパスが逸れるのを回避するための機能を備えたソフトウェア付きの機械を使用するのが良いでしょう。結論
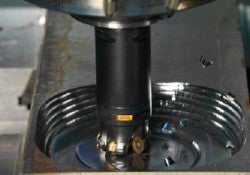
- 確実なダウンカットの最良の加工方法として「ウォーターラインフライス加工」のような輪郭削りタイプのツールパスを使用する
- 大きな工具径で多数の刃が効率的に切削できるため、フライスカッターの外周を使用した輪郭削りがしばしば高い生産性をもたらします
- 機械でのスピンドル回転数が制限される場合、輪郭削りは切削速度を維持、制御する手助けになります。
- また輪郭削りでは、ワークへの負荷と方向の急激な変化が少なくなります。高速および高送りのフライス加工、また高硬度材では、刃先とプロセスは、たわみの変動あるいはびびりを引き起こし得るいかなる変動からもより大きな影響を受けるため、このことは特に特に重要です。
- 良好な工具寿命のためには、連続して、できる限り長く切削してください。
注意! 切削速度がゼロのときには、工具中心の切削を避けてください。
ツールパス戦略
Z – 一定の輪郭削り、2軸。 荒加工~仕上げ加工
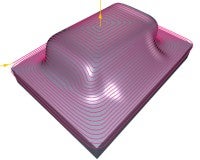
ウォーターラインフライス加工 Z - 一定の輪郭削り
- CAM制御の最大削り残し機能が利用できる場合に共通している
- 滑らかな食いつきと吸いもどし
- 容易なプログラミング
- 幅広い工具選択
らせん輪郭削り、3–5軸。 仕上げ加工
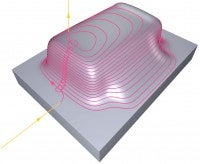
ランピング加工のツールパスにおける輪郭削り
- 滑らかな加工方向の変換
- 良好な形状精度と加工面品質
- 制御された削り残し高さ
- 一定の食いつき
- 短い加工プログラム
- 短い工具
段差面の生成
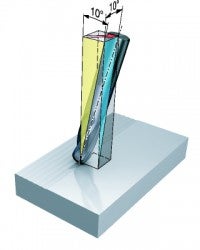
カッターを約10°傾けたダウンカットを2方向で行なう、加工面が良好になり、確実な加工性能が得られます。ボールノーズカッターまたはR形状の刃先では、以下のパラメータによっては、加工面にある程度の高さ h の段差ができます:
- 切削幅 ae
- 刃当たり送り fz
その他の重要な要因としては、切削抵抗に影響する切込み ap とツールインジケーターの振れの読み取り値 TIR があります。最良の結果を得るには、
- Coromant Capto®対応の高精密ハイドロチャックを使用する
- 工具の突出し量を最小にする
荒加工と中荒加工
切込み幅と深さより刃当たり送りがずっと小さいと、生成された加工面の送り方向の段差高さが大幅に小さくなります。
仕上げ加工と超仕上げ
選択した研磨歩法に関係なく、後で容易に研磨できる、全方向滑らかで対称的な加工面のテクスチャを得ることにメリットがあります。
fz ≈ aeのときにこれが得られます。
加工面の最良のテクスチャをえるには、超仕上げには常に2枚刃のカッターを使用してください。
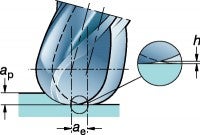
ae
よりずっと小さいfzでの中仕上げ
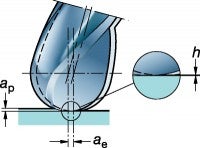
傾斜カッターとae
と同じfzを使用しての超仕上げ
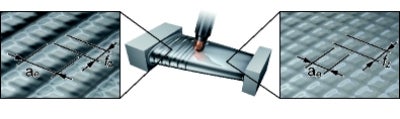