正面フライス加工
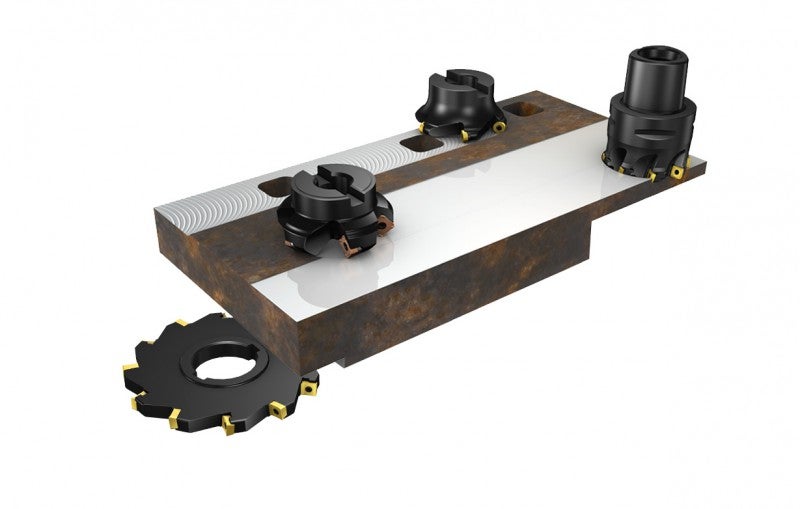
正面フライス加工には以下の加工が含まれます:
- 一般的な正面フライス加工
- 高送りフライス加工
- 重切削用正面フライスカッター
- ワイパーチップによる仕上げ加工
一般的な正面フライス加工
良好な正面フライス加工とは、どのようなものでしょうか?
正面フライス加工は最もよく使用されるフライス加工で、そのための工具が豊富に用意されています。切込み角45ºのカッターを最も頻繁に使用しますが、特定の条件では丸チップカッター、スクエア肩削りカッター、サイドカッターも使用します。最高の生産性を実現するため、加工に適したカッターを確実に選んでください(以下の「工具の選び方 」にある情報を参照してください)。
工具の選び方
正面フライスカッターの概要
以下の図は、切込みapおよび刃当たり送りfzの観点から、さまざまなコンセプトのカッターの主な適用領域を示しています。
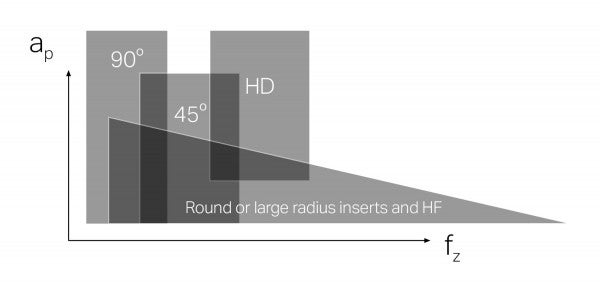
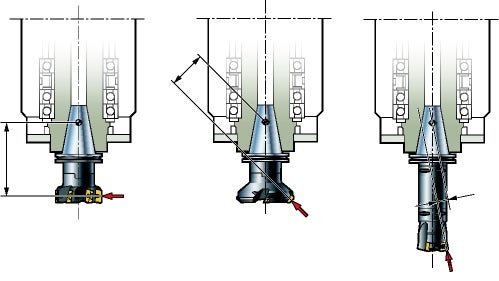
切込み角によって異なる切削抵抗の向き。
10° - 65°正面フライスカッターおよびプランジフライスカッター
この多種多様なカッターは主に正面フライス加工に使用しますが、プランジ加工に適した小さな切込み角のカッターもこのグループに属します。
45°カッター
- 一般的なフライス加工の第一推奨
- 長い突出しと、セットアップ剛性が不十分な場合のびびりを低減
- 切りくずが薄いため生産性が向
90°カッター
- 薄肉部品
- 治具が弱い加工物
- 90°形状が必要とされる場合
丸チップおよび大きなRのカッター
丸チップカッターは非常に汎用性があり、卓越したランピング加工が可能です。難しい正面フライス加工にも、倣い加工にも使用することができます。
- 汎用カッター
- 非常に剛性の高い刃先
- チップ当たりのコーナ数が多い
- 耐熱合金(ISO S)に特に好適。
- スムーズなカッティングアクション
加工方法の選択 - 例
正面フライス加工
![]() |
||||||||
![]() |
||||||||
切込角25-65° | 切込角90° | 切込角10° | ||||||
長所 +高い生産性 +正面フライス加工に最適 +マルチエッジのオプション 短所 –小さな切込み |
長所 +他の多くの加工にも使用することができる汎用カッター +軸方向の切削抵抗が小さい +チップサイズのわりに、比較的大きな切込み 短所 – 低い生産性 |
長所 +高い生産性 +非常に高い送り +軸方向の切削抵抗の向き(スピンドルの剛性に好適) 短所 –小さな切込み |
||||||
高い生産性
ベーシックな選択 |
汎用性
混合生産 |
高い生産性
問題の解決策 |
加工方法
断続加工面の断続正面フライス加工
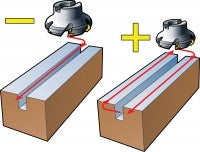
断続でのフライス加工は避けてください。
- 可能な場合、断続(穴または溝)でのフライス加工を避けてください。そのような断続加工では切込み回数が増えて抜け際も好ましくないものとなるため、刃先に対する要求が高くなります。
- あるいは抜け際加工時に薄い切りくずを保つため、加工物に断続部がある場合は、送りを推奨の50%に下げてください
薄くたわみのある部分の正面フライス加工
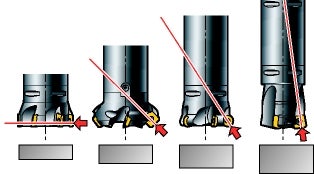
- 加工物および治具の剛性との関係で、主な切削抵抗の方向を検討してください
- 軸方向の剛性が弱い加工部品をフライス加工する場合、90°肩削りフライスカッターを使用してください。これは、このカッターが切削抵抗の大部分を軸方向へ向けるためです
- あるいは、軽切削カッター、正面フライスカッターを使用してください
- 軸方向の切削抵抗を最小限に抑えるため、0.5–2 mm以下の軸方向切込みを避けてください
- 可能な限り最少の切削刃数になるよう、コースピッチカッターを使用してください
- 切削抵抗を最小限に抑えるため、シャープ、ポジチップ(-L)の刃先をご使用ください
- 問題の解決策として不等ピッチカッターを使用してください
正面フライスカッターを使用した、薄い加工部分のエッジ加工
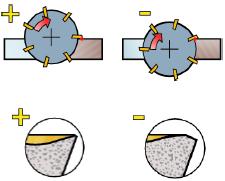
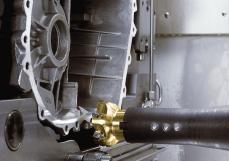
- 正面フライス加工では、カッターの中心をはずした位置で、薄い加工部分のエッジを合わせる必要があります。切削がより円滑になり、切削抵抗はさらに均一に壁面に沿って向けられ、これによりびびりが発生するリスクを低減します
- これらの加工には、切削の際に1刃以上のチップが常に食いつくようなカッターピッチを選定してください。
- 可能な限り軽切削用のチップブレーカを使用してください(中切削の代わりに軽切削、重切削の代わりに中切削)
- 薄肉部品においてびびり発生のリスクを低減するため、より小さなノーズRおよび短い平行ランドのチップを選定してください
- 低い切削条件、小さな切込みapおよび低い刃当たり送りfzを使用してください
加工チェックリストとヒント
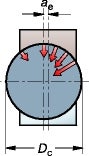

ロールイン
- 工作機械の剛性、スピンドルのサイズおよびタイプ(横型または縦型)および機械動力を検討してください
- 加工物より20~50%大きいカッター径を使用してください
- 最適な送りのためにカッターの位置決めをする際に、最大切りくず厚さを検討してください
- 出口部で最も薄い切りくずを生成するため、中心からずらしてカッターの位置を決めてください
- 最適な切りくず生成、つまり切りくず厚みが入り際で厚く、抜け際で薄くなるように、ダウンカットを行ってください
- カッターにロールインをプログラムし、スムーズに切削が開始できるよう送りを低減してください
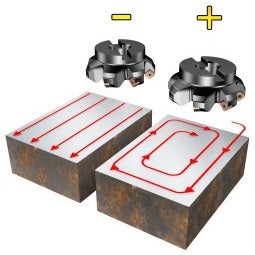
常にカッターを食いつかせておきます。
- 最適な切りくず生成、つまり切りくず厚みが入り際で厚く、抜け際で薄くなるように、ダウンカットを行ってください
- ツールパスプログラミングにより、切込みと抜けの繰り返しを回避してください
- 加工物への切込みと加工物からの抜けを頻繁に繰り返す動作は、可能であれば回避しなければなりません。これは、刃先に好ましくない応力を発生させ、ドウェルやびびりの原因となる可能性があるためです。複数のパスで加工するよりも、フライスカッターが完全に食いついた状態を保つツールパスをプログラムすることを推奨します。工具の進行方向を変える場合、径方向の小さなツールパスを追加して、カッターが動き続け、常に食いついたままにしてください
高送りフライス加工
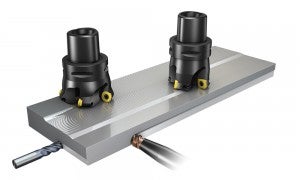
良好な高送りフライス加工とは、どのようなものでしょうか? アルミ合金の加工時に、またCBNチップまたはセラミックチップでの鋳鉄の加工時に、1000 m/min以上の切削速度を使用することができます。結果として非常に高いテーブル送りvfを実現します。この種の加工は高速加工 (HSM) と呼ばれます。
ネズミ鋳鉄など切りくずが短い被削材のフライス加工では、エクストラクロスピッチの正面フライスカッターを使用することが可能です。結果として高いテーブル送りを実現します。通常、切削速度が低い耐熱合金 (HRSA) では、エクストラクロスピッチにより高いテーブル送りを実現します。
切込み角の小さいカッターを使用する場合、または丸チップカッターを使用する場合は、切りくずを薄くする効果があるため、刃当たり送りが非常に高い(最大4 mm/刃)正面フライス加工が可能です。切込みは2.8 mm未満に制限されますが、送りが極めて高いため、非常に生産性の高いフライス加工方法となります。特別なコンセプトのカッターは、軸方向切込みが浅く送りが極めて高いフライス加工用に最適化されています。軽快な速い高送りを実現するためには、切込み角が小さいことが必要な前提条件となります。
工具の選び方
高送りカッター
最大切込み (ap)、 mm | 1.2 - 2 |
カッター径 (Dc)、 mm | 25 - 160 |
被削材 | ![]() |
丸チップ カッター
最大切込み (ap)、 mm | 1.3 |
カッター径 (Dc)、 mm | 10 - 25 |
被削材 | ![]() |
中高送り
最大切込み (ap)、 mm | 1.3 | 10 | 7/8 | 2.8 |
カッター径 (Dc)、 mm | 4 - 20 | 25 - 160 | 10 - 42 / 25 - 125 | 63 - 160 |
被削材 | ![]() | ![]() | ![]() | ![]() |
高送りカッター:
- 生産性の高い、切込み角10°の高送り正面フライスカッターで、非常に高い刃当たり送りfzが可能です
- 浅い切込みapでの高送り
- 高硬度鋼の高速加工用に最適化された高精度工具
- 非常に高い送り速度での、輪郭と非対称な形状の荒加工~中仕上げ加工
注意: 丸チップとラジアスカッターの場合、高送りフライス加工を可能にするためにはap値を推奨最大値より大幅に抑えてください
丸チップカッター:
- 軸方向切込みを小さくすると、切りくずを薄くする効果が高まります
- スムーズなカッティングアクション
- 厳しい加工条件、または軽切削条件用の汎用カッター
加工方法
切込み角が小さなカッター
小さな切込み角のカッターは大幅に送りfzを上げることができます。apが小さい場合、切りくずを薄くする効果があるためです。
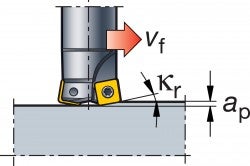
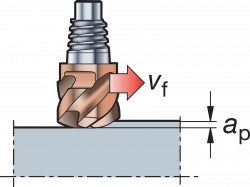
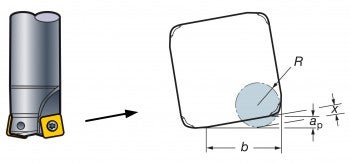
IC(チップ径) | 寸法、mm | 未加工部 | ||
iC | R | b | ap | x |
9 | 2.5 | 7.05 | 1.2 | 0.79 |
14 | 3.5 | 12.0 | 2.0 | 1.48 |
切込み角が小さいため、最大切りくず厚さが大幅に薄くなります。このため、チップに過剰な負荷をかけることなく、極めて高い送り速度を使用することが可能になります。
注意: 90°ショルダー部に対するすべての加工は避けてください。切込みが急激に深くなり、小さなアプローチ角のプラス効果が失われるためです。
チップを損傷させる可能性がある、びびりを回避するために、通常通り、送り速度を下げ特定の加工条件に合わせて対応する必要があります。
丸チップカッター
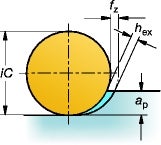
丸チップでは、切込みapによって切りくず厚さhexが変化します。丸チップカッターを使用する高送りフライス加工法を用いる場合は、切込みを小さく保つ必要があります(最大でチップ径iCの10%そうでないと、切りくずを薄くする効果が低下し、送りを下げる必要があります。図を参照)。
注意: 丸チップカッターを使用する場合は、壁面/ショルダー部への接近時に切込みが急に大きくなるため、送りを下げることが重要です。
一般荒加工用の剛性の高いチップ
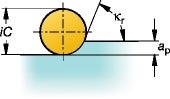
丸チップの場合、切りくず負荷と切込角は切込みで変わります。丸チップでは、切込みに応じて切りくず負荷と切込み角が変わります。​切込みがチップ径iCの25%より小さい場合に、最高の性能を発揮します。
重切削用正面フライスカッター
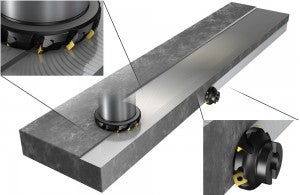
良好な重切削正面フライス加工とは、どのようなものでしょうか?
重切削正面フライス加工には、大型ガントリーフライス盤および高出力フライス加工機、またはマシニングセンタでの、大型の鍛造または熱間圧延素材、鋳物および溶接部品の荒フライス加工が含まれます。多量の切りくずを排出する必要があります。その際に、フライス加工用チップに特別な要求を課す、高温の切削熱と大きな切削抵抗が発生します:
- 切込みが深いと主切刃に大きな負荷がかかります
- 切込みがゼロに近づくと、粗い鍛造肌によりコーナ部に摩耗が発生します
重切削用フライスカッターには切込み角60ºが最適です。この加工の特徴:
- 優れた切込み能力、比較的均一な切削抵抗、高い送り速度を可能にする切りくずを薄くする効果
- この設計の軸方向の削り代により、チップに十分な平行ランドがあり、優れた加工面品質を実現します
工具の選び方
重切削フライス加工
切込み角 (κr)、 mm | 60° | 45° | 90° | 丸チップ |
最大切込み (ap)、 mm | 13/18 | 10 | 15.7 | 12.5 |
カッター径(Dc)、mm | 160 - 500 | 80 - 250 | 40 - 200 | 66 - 200 |
被削材 | ![]() | ![]() | ![]() | ![]() |
60°重切削用フライスカッター
- 工具を効率よく取り扱うことができるように設計されているため、短いダウンタイムでチップを安全に素早く機械で交換することができます
- 最大18 mmの切込み能力を持ち、凹凸のある均一でない加工面においても優れた切りくず排出と加工を実現します
- 高い生産性、刃当り送り0.4–0.7 mm
- 優れた中仕上げ結果を実現する十分な平行ランド
- 浅い切込みで生じる粗い酸化膜に耐える、剛性の高いチップコーナ
- 非常に厳しい切削条件でも、確実性を発揮する強靭なカッター
45-90°中切削フライスカッター
- 軽快な切削能力を提供する中切削正面フライスカッター
- 0.2–0.6 mmの送り範囲内の切込み6–8 mmに対応可能
- 大型マシニングセンタでの厳しい加工条件用
- ワイパーチップを使用することで、フライス加工で優れた仕上げ面を得ることが可能
- 中切削正面フライス加工および肩削りフライス加工用の第一推奨
大型の丸チップカッター
- 鍛造肌のフライス加工や断続加工のように、厳しい加工条件に対応する強靭な切刃付きの中切削用カッター。丸チップ用ブレーカーによって、滑らかな切削アクションを実現します
- 安定条件下では8コーナを使用することが可能です
- 最大切込みapは10 mmです。最大推奨切りくず厚さは、チップブレーカと切込みに応じて、1刃当たり最大0.55 mmまで幅広く対応可能です
加工方法
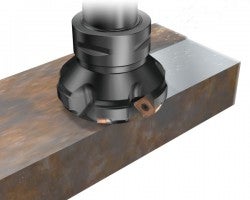
重切削加工では、チップ付きの大径の大型カッターを使用します。切削速度は普通ですが、大きなapとfzを大きなaeと組合せることで、非常に生産性が向上します。
切削の入り際
重切削フライス加工では基本的に加工条件が厳しいため、多くの場合、カッターの食い付きが重要です。
- 可能であれば、ロールインするようにツールパスをプログラムします
- これができない場合は、カッターが十分に食いつくまで、送りを下げます
カッター位置とサイズ
重切削フライス加工では、大きな面をフライス加工するために複数のパスで加工する必要があるため、以下の推奨事項を守ることが重要です:
- カッター位置および食いつき
- 工作機械の加工能力に対するカッターサイズ
- 不安定な抜けを回避するためのツールパス
高温に注意してください
難しい重切削フライス加工では高温が発生します。磁気テーブルを使用して加工物をクランプする場合、生成された多量の切りくずは多くの場合カッター周辺に残ります。これは、断続的または部分的な切りくず排出を引き起こし、工具寿命を短くする切りくずのリカットの原因になります。これを回避するには、切りくずが加工領域に入らないようにします。切込みを大きくして面接点をより強靭な主切刃に移動させることにより、損傷しやすいチップコーナ部が粗い表皮黒皮および鍛造肌と擦れるのを防ぎます。
注意: カッターのチップを交換する際には、高温で火傷を負わないように手袋を着用してください。
ワイパーチップによる仕上げ加工
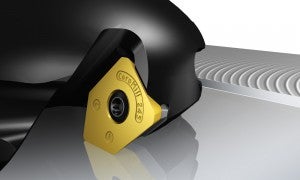
正面フライス加工で良好な加工面品質を達成する方法
標準チップと1個以上のワイパーチップを組合わせることによって、優れた加工面品質を実現することができます。チップ調整機能を備えたエクストラクロスピッチの大径カッターにおいて、回転当たり送りfnが高いときに、ワイパーチップは最も有効に機能します。
優れた表面品質を維持しながら、回転当たり送りを約4倍に上げることができます。ほとんどの被削材の正面フライス加工において、不安定な加工条件下でも優れた表面粗さを生成するために、ワイパーチップを使用できます。
工具の選び方
カッター
切込み角 (Kr)、 mm | 45° | 45° | 65° | 90° | 25° | 90° |
最大切込み (ap)、 mm | 6 | 10 | 6 | 10 | 0.9 | 8.1 |
カッター径 (Dc)、mm | 40 - 250 | 32 - 250 | 40 - 250 | 40 - 200 | 80 - 250 | 125 - 500 |
加工面品質 (Ra) | < 1.0 | < 1.0 | < 1.0 | < 1.0 | < 1.0 | < 1.0 |
被削材 | ![]() | ![]() | ![]() | ![]() | ![]() | ![]() |
ワイパーチップはさまざまな長さ (Bs) で、またしばしば各チップの右勝手と左勝手で使用することができます。ほとんどの被削材用に材種を使用することが可能です。仕上げ加工用に専用に開発された、あるいはカセットを使用したソリューションを提供するカッターコンセプトの場合、専用チップシートは調整可能なものであるのが一般的です。
加工方法
大型の正面フライスカッターを使用した仕上げ加工では、通常、送りfzを低く保つ必要があります。しかし、ワイパーチップのカッターを使用すると、加工面品質を損なうことなく、送りを2-3倍上げることができます。
高送り鏡面仕上げ
加工面粗さ | ||
![]() |
送り fn | |
fn1 <= 0.8 * bs1 | fn2 <= 0.6 * bs2 |
A:標準チップのみ
B:ワイパーチップ1個
C:fn = 回転当たり送り
bs1 | bs2 | |
![]() |
- 回転当たり送りfnが標準チップの平行ランド長さBsの80%を超える場合は、ワイパーチップによって表面品質が改善されます
- チップ数の多い大径カッターで回転当たり送りfnが上がると、加工面品質を維持するためにワイパーチップが必要となります
- カッターの軸方向の振れは、スピンドルの傾き、カッターサイズ、取付け、設定精度によって決まり、加工面のうねりに影響します。クラウン形状のワイパーランドがこれを補正し、段差のない面を生成します。回転当たり送りをワイパーランドの60%に制限することで、これを実現します
- 固定チップシートタイプのカッターにワイパーチップを取り付けると、ワイパーランドは約0.05 mm他の刃先より高くなります。カセット設計のカッターの場合、ワイパーチップを非常に正確にこの位置に調整することができます。突起により従来のチップより大きな負荷が、ワイパーチップにかかります。その結果、びびりが発生することがあります。このため、ワイパーは適切な切込みで限られた刃数の軽切削に使用してください
- 軸方向力を制限し、びびり発生のリスクを低減するには、切込みを小さくしてください。仕上げ加工での推奨軸方向切込みは0.5–1.0 mmです
- ワイパーチップの取付けは十分注意し、長い切れ刃を正しく位置決めしてください
例:
- チップの平行ランド幅Bsは1.5 mm
- カッターにはチップが10個あり、刃当たり送りfzは0.3 mmです。そのため回転当たり送りfnは3 mmになります(平行ランドの長さの2倍)
- 優れた加工面粗さを実現するには、回転当たり送りを最大で1.2 mm(1.5 mmの80%)にする必要があります
- 類似したワイパーチップには、幅約8 mmの平行ランドがあります
- 結果:回転当たり送りは1.2 mmから4.8 mm(8 mmの60%)に上げることが可能です
注意:機械動力などその他の制限を考慮する必要があります。
加工チェックリストとヒント
「鏡面仕上げ」を実現するためのヒント:
- 光沢ある仕上げ面を得るには、高い切削速度および/またはサーメットチップを使用します
- 粘性の高いステンレス鋼 (ISO M) および耐熱合金 (ISO S) の加工には、切削油またはオイルミストを使用してください
- 最高の加工面品質を生成するには、シャープな刃先のPVDコーティングチップを使用し、切込みapを0.5 – 0.8 mmに設定します
- 加工チップで使用されているのと同一の材種を、ワイパーチップでも使用するようにしてください