さまざまな被削材のフライス加工方法
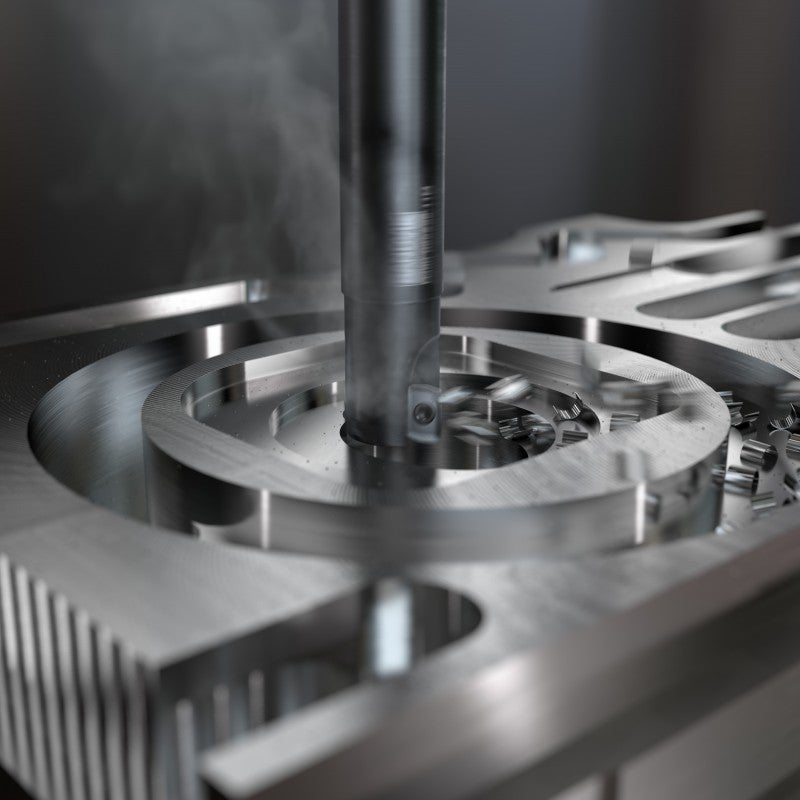
鋼のフライス加工
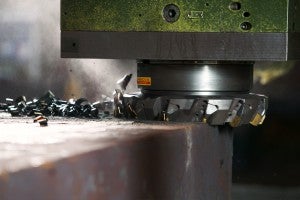
鋼の加工特性は、合金成分、熱処理および製造工程(鍛造、鋳造など)によって異なります。
柔らかい、低炭素鋼においては、構成刃先やワークでのバリの発生が主な問題です。高硬度鋼では、カッターの位置決めが刃先のチッピングを回避するために重要になります。
推奨事項
鋼のフライス加工時には、抜け際で切りくず厚さが大きくなるのを防ぐためにカッターの位置決めなど、必ず当社の推奨事項にしたがってください。特に荒加工においては、切削油なしのドライ加工を常に考慮してください。
ステンレス鋼のフライス加工
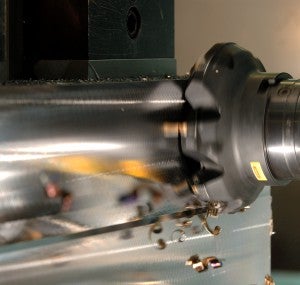
ステンレス鋼は、フェライト/マルテンサイト、オーステナイトおよび二相(オーステナイト/フェライト)に分類することができます。それぞれにフライス加工用の推奨事項があります。
フェライト/マルテンサイト系ステンレス鋼のフライス加工
被削材分類: P5.x
フェライト系ステンレス鋼の加工特性は低合金鋼に類似しているため、鋼フライス加工向けの推奨事を適用できます。
マルテンサイト系ステンレス鋼には高い加工硬化特性があり、食いつく際は非常に大きな切削抵抗が発生します。最良の加工結果のためには、正しいツールパスとロールイン加工法を使用します。切削速度 (vc) を高くすることで加工硬化作用に対抗します。高い切削速度と強化刃先を備えた高じん性材種が高い安全性を実現します。
オーステナイト系および二相ステンレス鋼のフライス加工
被削材分類: M1.x、M2.xおよびM3.x
オーステナイト系および二相ステンレス鋼のフライス加工の主な摩耗基準は、熱亀裂、ノッチ摩耗および構成刃先/溶着による刃先のチッピングです。ワークにおいては、バリの発生および加工面品質が主な問題です。
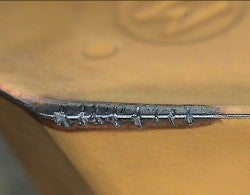
熱亀裂
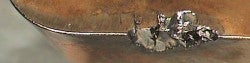
チップの刃先のチッピング
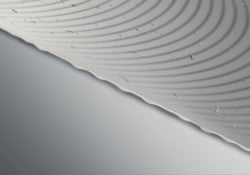
バリの発生および不十分な加工面品質
荒加工における推奨事項
- 高い切削速度 (vc = 150–250 m/min (492–820 ft/min)) を使用して構成刃先を回避する
- 切削油なしのドライ加工で熱亀裂の問題を最小にする
仕上げにおける推奨事項
- 加工面品質向上のために切削油または、できればミストクーラント/最小潤滑が必要になることがあります。仕上げにおいては切削領域で発生する熱が低めのため、熱亀裂はあまり問題になりません
- サーメット材種を使用すると、切削油なしで十分な加工面品質が得られます
- 送り (fz) が低過ぎると、刃先は変形硬化領域で切削を行うことになり」、チップの摩耗が激しくなります。
鋳鉄のフライス加工
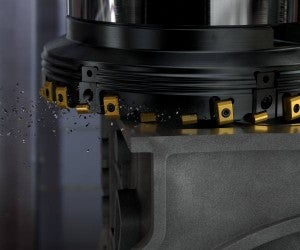
鋳鉄には5つの主要タイプがあります:
- ネズミ鋳鉄 (GCI)
- ダクタイル鋳鉄 (NCI)
- 可鍛鋳鉄 (MCI)
- コンパクト黒鉛鋳鉄 (CGI)
- オーステンパ球状黒鉛鋳鉄 (ADI)
ネズミ鋳鉄
被削材分類: K2.x
ネズミ鋳鉄をフライス加工するときの主な摩耗基準は、摩耗性の高い逃げ面摩耗と熱亀裂です。ワークにおいては、カッター抜け際でのワークのつぶれおよび加工面品質の問題が主な課題です。
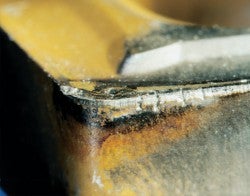
一般的なチップ摩耗
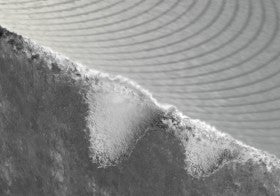
ワークのつぶれ
荒加工における推奨事項
- 熱亀裂の発生を最小にするため、切削油なしのドライ加工を推奨します。厚膜コーティングの超硬チップを使用する
- 加工物の欠損が発生する場合、逃げ面摩耗を点検します。切りくずの厚さを下げるために送り (fz) を下げます。よりポジティブなブレーカーを選択します。できるだけ65/60/45°カッターを使用します。
- 粉塵等を避けるために切削油を使用しする場合は、湿式切削材種を選択してください。
- コーティング超硬は常に第一推奨ですが、セラミックも使用可能です。切削速度 (vc) を非常に速く、800–1000 m/min (2624–3281 ft/min)で設定してください。ワークにおけるバリの発生により、切削速度が制限されます。切削油は使用しないでください。
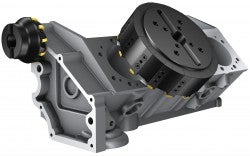
仕上げにおける推奨事項
- 薄いコーティングの超硬チップを使用するか、またはノンコート超硬チップを使用します。
- CBN材種を高速回転の仕上げに使用することができます。切削油を使用しないでください。
ダクタイル鋳鉄
被削材分類: K3.x
フェライト系およびフェライト/パーライトダクタイル鋳鉄の加工特性は、低合金鋼のものと非常によく似ています。そのため、工具、チップブレーカおよび材種の選定に関しては、鋼材用に提供されているフライス加工の推奨事項を適用してください。
パーライトダクタイル鋳鉄は摩耗性が高いため、鋳鉄材種が推奨されます。
最高の加工能力を発揮するためには、PVDコーティング材種およびウェット加工を使用します。
コンパクト黒鉛鋳鉄 (CGI)
被削材分類: K4.x
パーライト含有量 90%以下
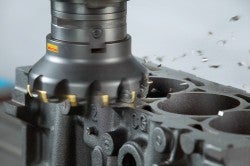
パーライト構造が約80%のこの種のCGIは、フライス加工が最も一般的な加工方法です。一般的な部品としてはエンジンブロック、シリンダーヘッドおよびエキゾーストマニホールドがあります。
カッター推奨事項はネズミ鋳鉄と同じです。しかし、ワークでのバリ発生を最小にするためにシャープなポジチップブレーカを選択してください。
サーキュラフライス加工が、CGIにおける従来の円筒ボーリング加工に代わる非常に良好な加工法です。
オーステンパ球状黒鉛鋳鉄 (ADI)
被削材分類: K5.x
荒加工は通常非硬化状態で行なわれ、高合金鋼のフライス加工比較することができます。
しかし仕上げ加工は、非常に摩耗性の高い高硬度材で行なわれます。これは高硬度鋼 (ISO H) のフライス加工と比べることができます。こすり摩耗に対して高い耐性のある材種が推奨されます。
NCIと比べて、ADIでの工具寿命は約40%短くなり、切削抵抗は約40%高くなります。
非鉄材のフライス加工
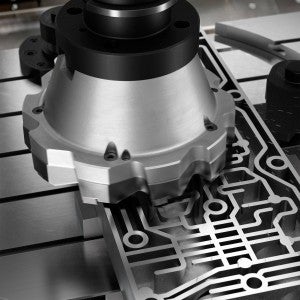
非鉄材にはアルミ合金だけでなく、マグネシウム、銅および亜鉛ベースの合金が含まれます加工特性は主にSi含有量によって異なります。亜共晶アルミ合金はSi含有量が13%以下の最も一般的なタイプです。
Si含有量が13%以下のアルミ合金
被削材分類: N1.1-3
主な摩耗基準は、バリの発生と加工面品質問題を引き起こす構成刃先/切りくずの刃先への溶着です。ワーク表面の引っかき傷を避けるために、良好な切りくず生成および切りくず排出が非常に重要です。
推奨事項
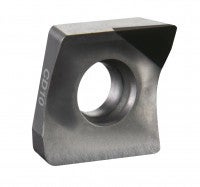
PCDヘッドチップ
- 良好な切りくず破断能力および構成刃先耐性のために、シャープな研磨刃先を備えたPCDヘッドチップを使用します。
- シャープな刃先のポジチップブレーカを選択します。
- その他のほとんどのフライス加工とは違い、刃先への切りくずの溶着をさけるため、および加工面品質の向上のために、アルミ合金の加工では常に切削油を使用してください。 Si含有量 < 8%: 濃度5%の切削油を使用するSi含有量 8–12%: 濃度10%の切削油を使用するSi含有量 >12%: 濃度15%の切削油を使用する
- 高切削速度は一般的に加工性能を向上させ、工具寿命への悪影響はありません
- hex 値 0.10–0.20 mm (0.0039–0.0079 inch) が推奨されます。この値が低過ぎると、バリが発生することがあります。
警告: カッターの最大回転数を超過していないかを確認してください
- テーブル送りが高いため、「先読み」機能を備えた機械を使用して寸法誤差を回避してください
- バリの発生やワークの加工面品質により、常に工具寿命が制限されます。チップの摩耗は、工具寿命基準として用いるには難点があります
熱耐合金 (HRSA) のフライス加工
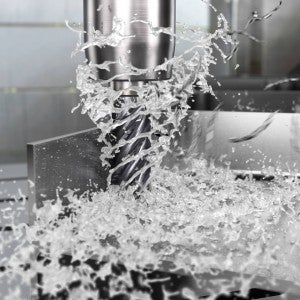
熱耐合金 (HRSA) は以下の3つの被削材グループに分類されます。ニッケルベース、鉄ベースおよびコバルトベース合金です。チタンは純チタンか合金です。熱耐合金 (HRSA) とチタンの加工特性は両方とも良くありません。特に時効状態での加工特性は好ましいものではなく]切削工具に関して特別な要件が求められます。
耐熱合金 (HRSA) およびチタン合金
熱耐合金 (HRSA) やチタン合金のフライス加工には、高剛性および低回転速度での高動力および高トルクを備えた機械が必要になります。境界摩耗や切れ刃の欠けは頻繁に起こります。高い発熱により切削速度が制限されます。
推奨事項
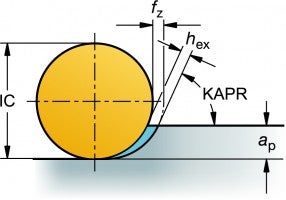
堺界摩耗が最小になるよう丸チップカッターを使用してください。
- 可能な限り丸チップカッターを使用して、切りくずを薄くする効果を高めます。
- 切込みが5 mm (0.197 inch) 以下の場合は、切込み角を45°以下にすること。実際には、ポジティブなすくい角の丸チップが推奨されます
- 径方向、軸方向両方のカッター精度は、一定の刃先負荷および滑らかな加工を維持し、カッターの個々の刃の早期破損を防ぐために不可欠です
- 切れ刃が切削から抜けるときに切りくずが溶着するのを防ぐために、刃先形状はは常にポジティブで刃先が最適な丸みを帯びていること
- フライス加工サイクル中、実際に切削している刃数はできる限り多くしてください。加工が安定していれば、これにより良好な生産性が実現します。エクストラクロスピッチカッターを使用してください。
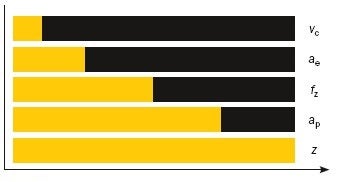

= 工具寿命

= 切削条件が上がるにつれて工具寿命が短くなる
切削条件を変えると、工具寿命への影響が変化します。切削速度 (vc) が工具寿命に一番大きく影響し、次に切削幅 ae 等が続きます。
切削油/クーラント
その他のほとんどの被削材におけるフライス加工とは違い、切りくず除去のサポート、刃先の熱制御、切りくず噛みの回避のために、切削油が常に推奨されます。低圧外部給油に代わって、スピンドル/工具を介して供給される高圧クーラント (70 bar (1015 psi)) が常に推奨されます。
例外:セラミックチップでのフライス加工では熱亀裂が発生するため切削油を使用しないでください。
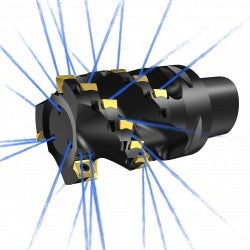
超硬チップを使用する際は切削油がカッターを介して供給されることにメリットがあります
チップ/工具摩耗
工具破損および加工面品質が不十分なことの最も一般的な原因は、堺界摩耗、過度の逃げ面摩耗および刃先のコバ欠けです。
最善の予防法は刃先を頻繁に交換して高信頼性のプロセスを実現することです。刃先付近の逃げ面摩耗は、90°切込み角のカッターでは0.2 mm (0.0078 inch) を超えないようにしてください。丸チップカッターでは最大 0.3 mm (0.0118 inch) です。
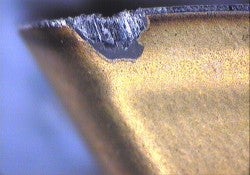
一般的なチップ摩耗
耐熱合金材 (HRSA) の荒加工用セラミックチップ
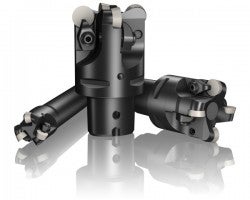
セラミックチップでのフライス加工では、低送り速度時 (~0.1 mm/z (0.0039 in/z)) でも、回転速度が一般的に超硬チップでの加工の20~30倍速くなります。これにより高い生産性が達成されます。断続加工のため、旋削加工より加工温度がはるかに低いです。このためフライス加工の回転速度は、回転速度が200–300 m/min (656–984 ft/min) の旋削加工に比べて、700–1000 m/min (2297–3280 ft/min) になります。
推奨事項
- 主に丸チップを使用して切込み角を小さくし、堺界摩耗を回避します
- 切削油/クーラントは使用しないでください。
- チタン合金を加工する際はセラミックチップは使用しないでください。
- セラミックチップは、表面性状と仕上がり形状に好ましくない影響があります。このため、仕上げ部品形状に近い加工では使用されません
- 耐熱合金材 (HRSA) の加工でセラミックチップを使用する場合の最大逃げ面摩耗は0.6 mm (0.024 inch) です
耐熱合金 (HRSA) およびチタン合金についての詳細はこちら
高硬度鋼のフライス加工
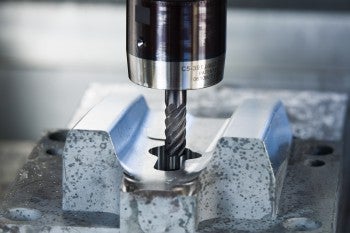
このグループには硬度が45–65 HRC以上の焼入れ焼戻し鋼が含まれます。
フライス加工される一般的なワークは、
- プレス金型用工具鋼
- 塑性鋳型
- 鍛造金型
- ダイキャスト金型
- 燃料供給ポンプ
主な課題は、チップのアブレーシブ性逃げ面摩耗とワークのびびりです。
推奨事項
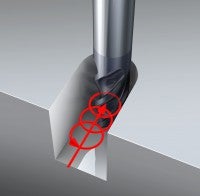
- シャープな刃先のポジチップブレーカを使用する。これが切削抵抗を低減し滑らかな切削アクションをもたらします。
- ドライ加工を行ない、切削油を使用しないでください。
- トロコイドフライス加工はこれに適した加工法です。切削抵抗が低い高テーブル送りが可能です。刃先やワークの発熱も低く、生産性、工具寿命およびワーク公差に対してメリットがあります。
- 正面フライス加工に対しても、軽切削かつ高回転という方針を適用する必要があります。つまり、aeおよびapの両方とも切込みを小さくします。エクストラクロスピッチカッターを使用して、比較的高い切削速度にします