ギア加工

ギアはどのように加工されるのでしょうか?
日々変化するギア加工産業では、最も効率と精度の高い加工方法とギアミリング工具を選定することが最優先事項です。加工する部品、生産工程、およびロットサイズが、工具とギア加工方法の選択を決定します。
旋削加工工程中に行われるギア加工は、厳しい寸法公差が課題になることがよくあります。熱処理前の入念な準備により、高硬度材旋削が比較的容易になり、続いてギアの高硬度材加工が行われます。高硬度材旋削では、予測可能な加工と良好な加工面品質が最も重要です。これらはすべてコスト効率と結びついています。
電動モビリティ、新しいトラスミッションデザイン、そして高い柔軟性と生産性のニーズにより、ギア加工プロセスは大きく変わろうとしています。一般的な従来のギア工作機械は注目されなくなり、代わって、ギア/スプライン部品の複合加工が標準となる傾向にあります。シェーピング加工、ブローチ加工、スプライン転造を置き換え、さらにホブ加工もある程度置き換えることになるパワースカイビングが注目されるでしょう。歯車の精度
通常、歯車は切削加工後の歯車の公差要求を指定している規格に応じて分類されます。円筒歯車の分類に関する最も一般的な規格はDIN 3962で、異なる歯車のパラメーターを1~12の等級で測定・分類しています。他の顧客特有の規格も一般的ですが、すべてDIN 3962の規格とほぼ同じ評価パラメーターで構成されています。
一般的に、歯車精度等級は加工物の要求事項によって決定されますが、歯車の適用領域によって異なります。
優れた歯車精度に必要なその他の要求事項:
- 高品質の工具
- 清潔な接触面
- 工具とワークの両方の振れを最小限にする
- 安定性に優れたクランピング
- 正確で高剛性な機械
ギア加工の適用方法
一般的に工具の形状は歯車の諸元に合わせて特注する必要性があります。つまり、工具によって歯溝のサイズと形状が完全に一致しなければなりません。
ギアミリング加工用の工具を注文する際に考慮すべき重要事項:
- モジュールサイズ
- 圧力角
- 歯車の歯形形状(突起形状、歯先修整または歯先面取り)
- 転位係数
- 先端および谷部径
- ねじれ角
- 要求される歯車精度
- 使用可能な工具径の範囲(最小-最大)
- カップリングタイプとサイズ
必要な情報がすべて記載されている歯車の図面一式があれば望ましい。
ギア加工方法
新しい加工法によりギアミリング加工の製造ビジネスが変わろうとしています。このテクノロジーシフトにどのように対応するかが、今後競争力を持つためのカギとなるかもしれません。
- InvoMilling™
- パワースカイビング
- 小~中規模ロット用のディスク加工
- 歯車のホブ加工
InvoMilling™
InvoMilling™とは何ですか?
ギアの加工には通常、特定のギア形状用の専用工具が必要です。InvoMilling™は、外歯車、スプライン、およびストレートベベルギアを加工するための工程で、標準機械によるインハウスギアミリングを可能にします。工具を交換する代わりにCNCプログラムを変更することで、同一ツールセットで多様なギア形状を加工できます。複合加工機や5軸マシニングセンタを使用して、1回のセットアップで完成部品にまで加工することができます。このようにInvoMilling™は、リードタイムと総加工時間の大幅な短縮を可能にします。InvoMilling™の利点
- 柔軟性 – 同じ工具で複数のギア形状に対応
- 複合加工機や5軸マシニングセンタでのギアの加工
- 1台の機械と1回のセットアップで完成部品を製造
- より環境に優しい、ドライ加工、切削油不使用
InvoMilling™加工の用途
- 外歯車およびスプライン、ダブルヘリカルギア、山歯歯車、ストレートベベルギア
- 専用の工具や機械を必要とせずにギア部品を生産する必要がある場合
- 短いリードタイムが非常に重要な場合
- フランク補正の有無
- モジュールサイズ:0.8‒100
- 荒加工~仕上げ加工
- 小~中ロット生産
InvoMilling™の適用方法
InvoMilling™ CAD/CAMソフトウェアを使用して、3ステップでCNCプログラムを生成する方法を、動画でご紹介します。
- ワーク図面から加工するギアのデータをインポートしてギア形状を定義します。
- 加工方法を選択し、荒加工および仕上げ加工を追加し、ツールライブラリから使用する工具を選択します。
- 使用する加工機用のCNCプログラムを自動的に生成する前に、加工プロセスのシミュレーションを行って、ツールパスを検証します。
パワースカイビング
パワースカイビングとは何ですか?
パワースカイビングはギアシェーパー加工より何倍も速く、ブローチ加工よりずっと柔軟性の高い連続切削プロセスです。パワースカイビングがコンセプトとして考案されたのは、もう1世紀以上も前ですが、その開発が新たな展開を見せたのは、ようやく最近のことです。より堅牢で剛性の高い機械と主軸の高精度な同期制御が急速に進化した結果、パワースカイビングは、今や現実的な加工方法として、広く活用されています。
パワースカイビングは、内/外両方の歯車およびスプラインの加工に適用可能ですが、特に内径加工において高い生産性を発揮します。また、この加工方法は、短いリードタイムがきわめて重要な大量生産に最適です。小~中ロット生産の場合は、柔軟性の高いInvoMilling™ テクノロジーが推奨されます。パワースカイビングの利点
- 1回のセットアップで部品を完成させることができるため、総生産時間が短縮され、品質が改善され、ハンドリングとロジスティックスコストが削減される
- ショルダー部周辺を加工できるため、高い自由度で部品を設計可能
- 環境とオペレータに優しい
- ドライ加工条件で非常に効率的に作動
- ブローチング加工、シェーピング加工およびホブ加工を行う加工プロセスと比較して、総生産時間が大幅に短縮
- 管理および予測が可能な部品加工
- 部品品質は、同等のギアミリングソリューションで得られるものと同じか、それ以上の品質向上となります。
- 専用加工機、複合加工機およびマシニングセンタでの加工が可能。
パワースカイビング加工の用途
- 内歯車/外歯車とスプライン
- スパーギアとヘリカルギア
- 荒加工~仕上げ加工
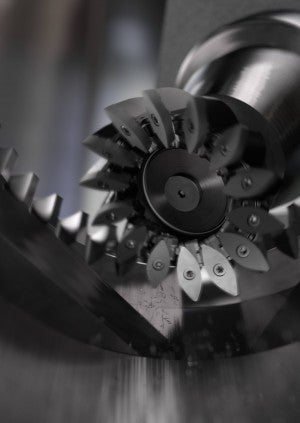
ディスク加工
ディスク加工とは何ですか?
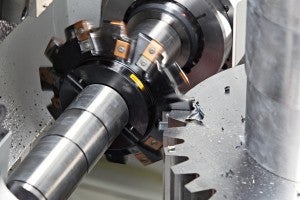
ディスク加工は、一度に1つの歯溝を切削する工程です。ディスク加工方法はマシニングセンタ、複合加工機やターニングセンタへの取付けが簡単で、1回のセットアップで部品を完全に加工することができます。ディスク加工テクノロジーを使用すれば、これまで一般にホブ盤あるいは下請けで製造していたスプラインを、お客様の工場の既存の機械を使って加工できます。このようにディスク加工は、大きな初期投資を必要としません。ディスク加工の利点
- マシニングセンタ、複合加工機、ターニングセンタでのスプライン加工
- 投資コストを削減
- ホブ盤への投資を行わずに、既存の機械でスプライン加工が可能
- ロジスティックスにかかる時間と費用を削減
- 機械や工場間での部品移動が不要
- 高速度鋼 (HSS) 工具の再研磨・再コーティングが不要
- 高い切削速度
- 難削材の切削が可能
- ドライ加工のため、リードタイムが短縮され、クーラント費用が節減される一方で、環境に優しく、作業者にも優しい環境作りに貢献
- コスト効率に優れたソリューションで、小規模から中規模のロットサイズに対応
ディスク加工の用途
- スプラインの外径加工
- 荒加工~仕上げ加工
- 様々な種類の機械に対応可能
- ドライ加工も可能
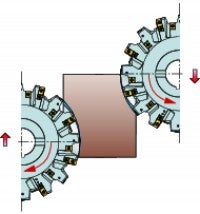
ダウンカット
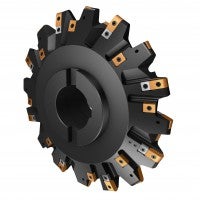
アップカット
歯車のホブ加工
歯車のホブ加工とは何ですか?
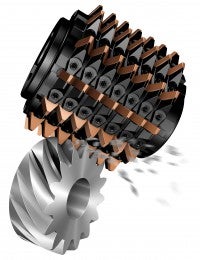
ホブ加工は、ヘリカル切削工具を使用して一連の切削を通じて歯を生成するギア加工工程です。ホブとギアブランクは、すべての歯が切削されるまで連続回転します。ホブ加工が可能なのは外歯車のみです。歯車のホブ加工の利点
- 高速度鋼 (HSS) 工具と比較して、ギア当たりの総コストが低い
- 高い切削速度
- 工具寿命の延長、ダウンタイムの短縮
- 簡単で繰り返し精度の高い工具交換および取扱い
- 新たな再研磨費用や再コーティング費用が不要
歯車のホブ加工の用途
- 荒加工、中仕上げ、仕上げ加工
- DIN 3972-2準拠のギア形状
- モジュールサイズ:3–10
- ホブ盤、複合加工機、5軸加工機
歯車のホブ加工の適用方法
- 全ての歯は異なる切りくずを生成します。工具寿命は最も厳しい重切削と最も厚い切りくずによって制限されます。切りくず厚さを評価するために、最大切りくず厚さhexを計算して、創成送りを決定します。最大切りくず厚さhexはホフマイスターの計算式に基づいて計算されます。
- 推奨最大切りくず厚さhex = 0.18–0.22 mm (0.007–0.009 inch)
- 可能な限り、ホブシフトをして工具寿命の改善をします。
- ドライ加工は超硬工具を使用する方が望ましく、ウェット加工よりも工具寿命が優れています。
- できるだけダウンカットを使用して、工具寿命を改善します。
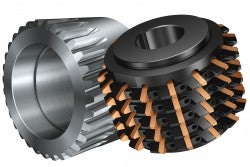