フライス加工時のカッターパスと切りくず生成
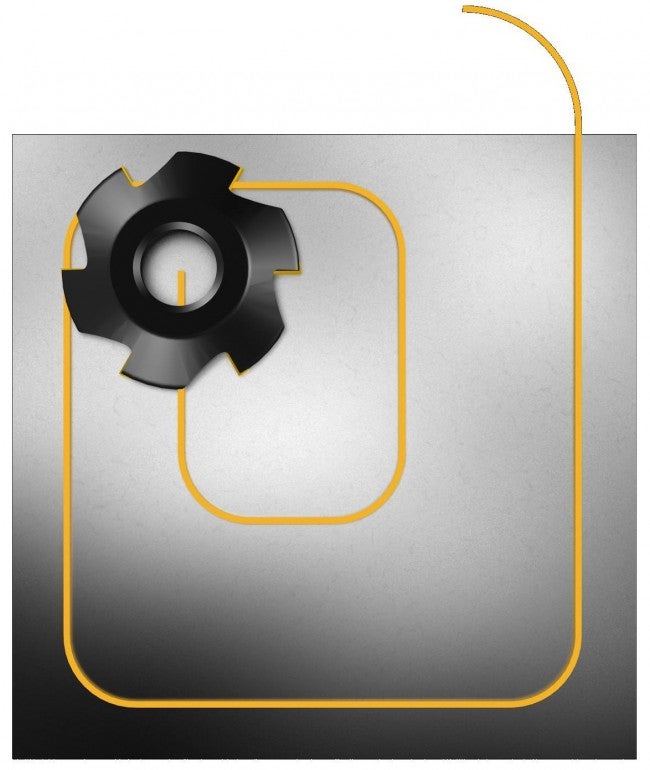
フライス加工時の正しいカッターパスと切りくず生成は、フライス加工において安定した刃先と長い工具寿命を保証するための重要な要素です。
フライスカッターの各刃先は断続的に径方向にワークに食い付きます。それぞれの食い付きにおいて考慮すべき3つの段階があります。
1. 切削部への入り際
2. 切削部における切込みの円弧
3. 切削部からの抜け際
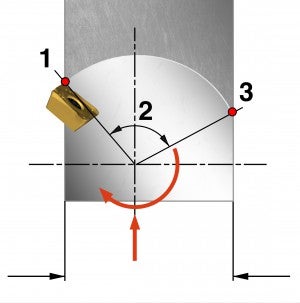
切削部への入り際
カーバイドチップを使用する場合、切削部への入り際は、3つの切削段階の中で最も影響を受けにくい部分です。カーバイドは、切込みウェルの衝撃時の圧縮応力に対処します。
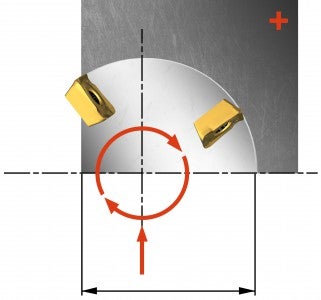
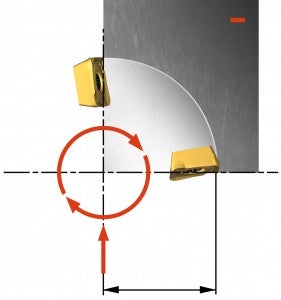
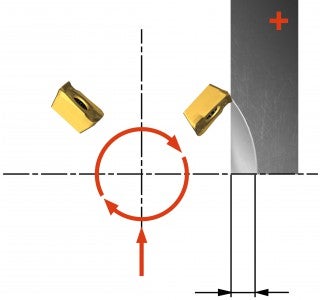
切削部からの抜け際
ワークからの抜け際は、3つの切削段階の中で最も影響を受けやすい部分です。
抜け際では、フライス加工時に厚い切りくず生成を避けるように努めます。厚い切りくず生成は、多くの場合、カーバイドチップ使用時に工具寿命の大幅な短縮をもたらします。切削の最終時点でチップが支持されずに曲がろうとします。このことが、カーバイドに張力を発生させ、刃先の破損を招くことがあります。
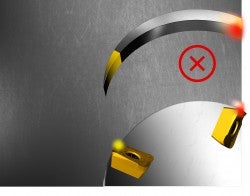
切削部における切込みの円弧
- 溝加工時の最大限の切込みの円弧は180° (ae = 100% DC) です
- 仕上げ加工の場合、弧が非常に小さくなることがあります
- 材種要件は、径方向切込みの割合ae/DCによって大きく異なります
- 切込みの円弧が大きいほど、刃先へより多くの熱が伝達されます
- 切込みの円弧が大きい場合、最も熱が伝達されにくいのはCVDコーティング材種です。
- 切込みの円弧が小さい場合、通常、切りくず厚さはより薄くなります。そして、よりシャープなPVDコーティング材種の刃先の熱発生量が少なく、切削抵抗が減少します。
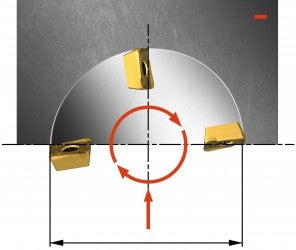
切込みの円弧が大きい(最大)
- 長い切削時間
- 高半径方向力
- 熱大量発生
- CVDコーティング材種
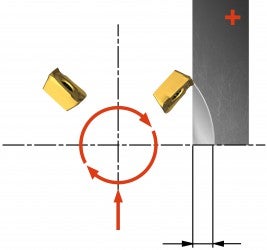
切込みの円弧が小さい
- 切削時間が短く熱発生量が少ないためvcを高くすることが可能
- 切りくずが薄くなるためfzを高くすることが可能
- シャープな刃先
- PVDコーティング材種
部品への食いつき
ワークに真っ直ぐに切り込むようにカッターがプログラムされていると、カッターが完全に切り込むまで抜け際で厚い切りくずが形成されます。これにより、特に硬鋼、チタン合金、および耐熱合金において工具寿命が大幅に短くなることがあります。また、びびりの観点から、ワークをスムーズに切り込むことが必須です。
工具寿命を向上させるには2つの方法があります。
1. 低送り
カッターが完全に食いつくまで送りを50%に減らします。
2. ロールイン加工
時計回りにロールイン加工をプログラムします(反時計回りでは、切りくずの厚さが厚くなる問題が解決されません)。ロールイン加工では抜け際での切りくず厚さが常にゼロになるため、高送りと長い工具寿命が可能になります。
カッター位置
カッターを中心から外れた位置(左寄り)に取り付けて、入り際で厚い切りくずが生成され、抜け際で薄い切りくずが生成されるようにします(ダウンカット法)。より安定した望ましい切削抵抗の方向が得られ、びびり傾向が最小限に抑えられます。
カッターが中心線上で対称的に取り付けられていると、抜け際で厚い切りくずが生成され、びびり傾向のリスクが高まります。
カッター径DCは切削幅 (ae) より20~50%大きくなければなりません。
利用可能なスピンドル動力も、ピッチの選択に影響を及ぼすため考慮しなくてはなりません。
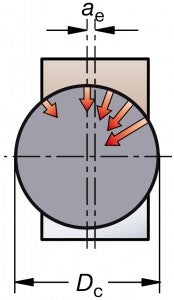
カッターはaeより20~50%大きく、
中心から外れた位置に取り付けること。
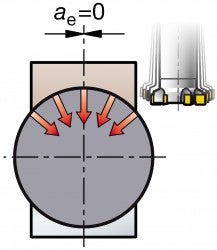
カッターが中心線上にあると
振動が発生することがあります。
カッターが食いついた状態を維持します。
切削中の急激な方向転換は、抜け際で厚い切りくずを発生させます。安定した最適なフライス加工のために、これらの推奨事項に従ってください。
- 常にカッターを食いつかせておきます
- 全てのコーナを回るようにします
- 切削幅 (ae) はDCの70%になるようにして、コーナを最大限にカバーできるようにします
- 外周フライス加工では、コーナーに沿って回ります
- 可能な限り妨害物や穴に沿ってプログラムしてください