Planfräsen
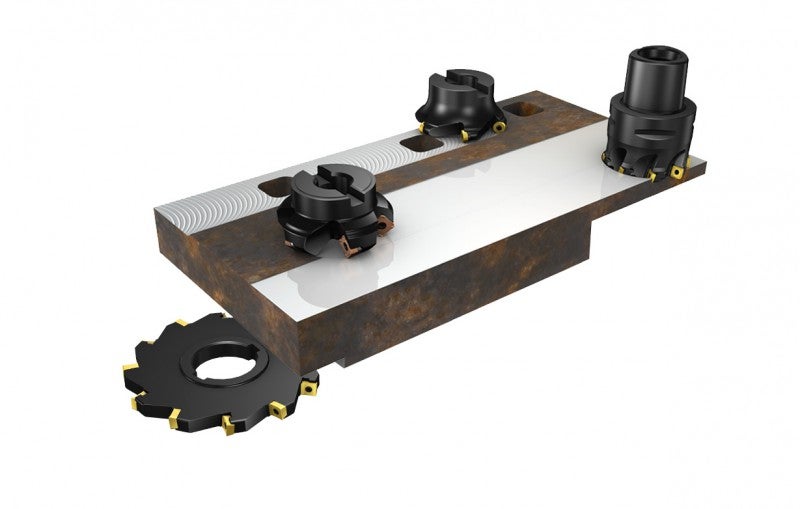
Planfräsbearbeitungen beinhalten:
- Allgemeines Planfräsen
- Fräsen mit hohem Vorschub
- Heavy Duty Planfräsbearbeitung
- Schlichten mit Wiper-Wendeschneidplatten
Allgemeines Planfräsen
Was ist erfolgreiches Planfräsen?
Planfräsen ist die gängigste Fräsbearbeitung und kann mit einer Vielzahl unterschiedlicher Werkzeuge durchgeführt werden. Am häufigsten werden Fräser mit einem Einstellwinkel von 45º verwendet. Aber auch Fräser mit runden Wendeschneidplatten, Eckfräser und Scheibenfräser kommen unter bestimmten Bedingungen zum Einsatz. Stellen Sie sicher, den richtigen Fräser für die Operation zu wählen, um optimale Produktivität zu erzielen (siehe Informationen zur Wahl der Werkzeuge unten).
Wahl der Werkzeuge
Überblick - Planfräser
Das Schaubild unten zeigt die Hauptanwendungsbereiche unterschiedlicher Fräserkonzepte in Bezug auf die Schnitttiefe ap, und den Vorschub pro Zahn, fz.
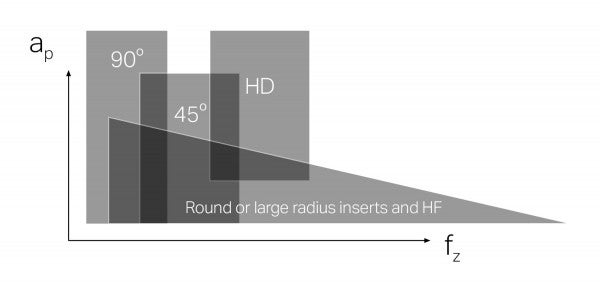
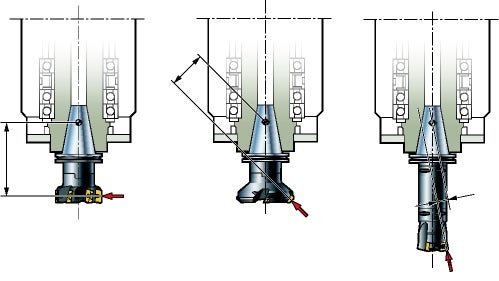
Durch unterschiedliche Einstellwinkel erzeugte Richtung der Schnittkräfte.
10°- 65° Plan- und Tauchfräser
Das breite Fräserprogramm dient vorwiegend für Planfräsbearbeitungen, doch auch Fräser mit sehr kleinen Einstellwinkeln, die für das Tauchfräsen ausgelegt sind, gehören zu dieser Gruppe.
45° Fräser
- Erste Wahl bei allgemeinen Vorgängen
- Reduziert Vibrationen bei großen Überhängen und schwachen Aufspannungen
- Durch abnehmende Spandicke höhere Produktivität möglich
90° Fräser
- Dünnwandige Bauteile
- Schwach gespannte Bauteile
- Wenn ein 90°-Winkel erforderlich ist
Rundplattenfräser und Fräser mit großem Radius
Rundplattenfräser sind sehr vielseitig, bieten exzellente Ramp-Eigenschaften und werden sowohl für Planfräs- als auch Profilbearbeitungen eingesetzt.
- Universalfräser
- Hoch stabile Schneidkante
- Viele Schneidkanten pro Wendeschneidplatte
- Insbesondere für warmfeste Superlegierungen geeignet, ISO S.
- Leichte Schneidwirkung
Suchen Sie Werkzeugempfehlungen?
Hier finden Sie unsere Zerspanungswerkzeuge chevron_right
Brauchen Sie Beratung?
Stellen Sie uns eine Frage chevron_right
Was es sonst noch über die Grundlagen unserer Metallzerspanung zu lernen gibt?
Registrieren Sie sich für unser kostenloses E-Learning Programm chevron_right
Wahl der Methode - Beispiel
Planfräsen
![]() |
||||||||
![]() |
||||||||
25-65° Einstellwinkel | 90° Einstellwinkel | 10° Einstellwinkel | ||||||
Vorteile + Hohe Produktivität + Optimiert zum Planfräsen + Wendeplattenoptionen mit Mehrzahnausführung Nachteile – Geringe bis mittlere Schnitttiefen |
Vorteile + Vielseitiger Fräser, der sich für viele weitere Operationen einsetzen lässt + Geringe Axialkräfte + Relativ große Schnitttiefe im Verhältnis zur Wendeschneidplattengröße Nachteile – Niedrigere Produktivität |
Vorteile + Hohe Produktivität + Extrem hoher Vorschub + Axiale Schnittkraftrichtung (vorteilhaft für Spindelstabilität) Nachteile – Geringe Schnitttiefe |
||||||
Hohe Produktivität
Die Basiswahl |
Vielseitig
Mischproduktion |
Hohe Produktivität
Problemlöser |
Korrekte Anwendung
Planfräsen von Flächen mit Unterbrechungen
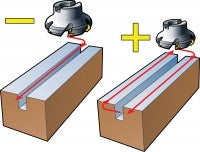
Fräsen über Unterbrechungen vermeiden.
- Wenn möglich, das Fräsen über Unterbrechungen vermeiden (Bohrungen oder Nuten). Solche unterbrochenen Schnitte belasten durch mehrfache Ein- und Austritte die Schneidkanten.
- Alternativ sollte die empfohlene Vorschubgeschwindigkeit im Bereich des Werkstücks, in dem sich die Bohrung befindet, um 50% reduziert werden.
Planfräsen dünnwandiger und ablenkender Bereiche
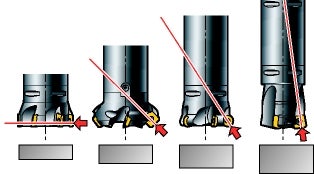
- Richtung der Hauptschnittkräfte in Relation zur Stabilität des Werkstücks und der Montagevorrichtung berücksichtigen
- Bei der Fräsbearbeitung axial instabiler Werkstücke einen 90° Eckfräser verwenden, der den Hauptteil der Schnittkräfte in axiale Richtung lenkt
- Alternativ einen leichtschneidenden Planfräser verwenden
- Schnitttiefen kleiner als 0.5–2 mm vermeiden, um Axialkraft zu minimieren
- Fräser mit weiter Teilung verwenden, damit möglichst wenig Schneidkanten in den Schnitt eingreifen
- Scharfe, positive (-L) Schneiden verwenden, um Schnittkraft zu minimieren
- Fräser mit Differentialteilung als Problemlöser verwenden
Eckenbearbeitung dünnwandiger Bereiche mit Planfräsern
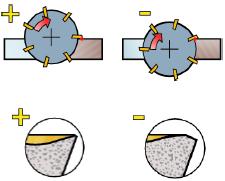
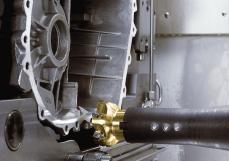
- Beim Planfräsen von dünnwandigen Bauteilbereichen sollte der Fräser außermittig positioniert werden. Die Schneidwirkung ist sanfter und die Schnittkräfte werden gleichmäßiger entlang der Wand gelenkt, was die Vibrationsgefahr reduziert.
- Für diese Anwendungen ist eine Fräserteilung zu wählen, bei der gewährleistet ist, dass stets mehr als eine Wendeschneidplatte eingreift
- Wendeschneidplattengeometrie für „leichte“ Bearbeitung wählen (leicht anstatt mittel, oder mittel anstatt schwer)
- Kleineren Wendeplattenradius und kürzere Planfase wählen, um das Vibrationsrisiko bei dünnwandigen Werkstücken zu vermindern
- Niedrige Schnittdaten, kleine Schnitttiefe, ap, und geringen Vorschub, fz wählen
Checkliste und Hinweise für die Anwendung
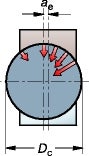

Ein- und Auskopieren um den Radius
- Stabilität der Werkzeugmaschine, Spindelgröße und -art (vertikal oder horizontal) und verfügbare Leistung berücksichtigen.
- Einen Fräserdurchmesser wählen, der 20 bis 50% größer als das Bauteil ist.
- Maximale Spandicke bei der Positionierung des Fräsers für optimalen Vorschub berücksichtigen.
- Für eine minimale Spandicke beim Austritt den Fräser außermittig positionieren.
- Für eine gute Spanbildung (d.h. von großer zu kleiner Spandicke) Gleichlauffräsen wählen
- Für eine minimale Spandicke beim Austritt den Fräser außermittig positionieren
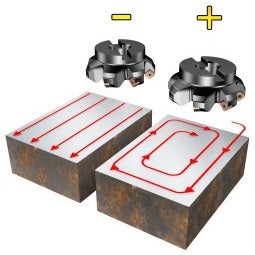
Sorgen Sie dafür, dass der Fräser konstant in Eingriff ist.
- Für eine gute Spanbildung (d.h. von großer zu kleiner Spandicke) Gleichlauffräsen wählen
- Ein- und Austritte durch Werkzeugwegprogrammierung vermeiden
- Häufige Ein- und Austritte aus dem Bauteil sollten möglichst vermieden werden. Diese können ungünstige Belastungen der Schneidkante, Stillstände oder Vibrationen verursachen. Es empfiehlt sich, einen Werkzeugweg zu programmieren, bei dem der Fräser im vollen Kontakt zum Werkstück ist. Das ist besser als mehrere parallele Durchgänge. Bei einer Richtungsänderung stets einen kleinen radialen Werkzeugweg einberechnen, um den Fräser in Bewegung und konstantem Eingriff zu halten.
Fräsen mit hohem Vorschub
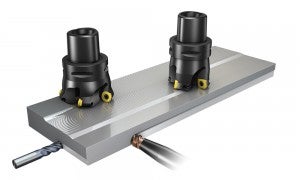
Was ist erfolgreiches Fräsen mit hohem Vorschub? Bei der Bearbeitung von Aluminium oder beim Fräsen von Gusswerkstoffen mit CBN oder Keramik können Schnittgeschwindigkeiten von über 1000 m/min verwendet werden, die in einen sehr hohen Tischvorschub (vf) resultieren. Dieser Bearbeitungstyp wird als Hochgeschwindigkeitsbearbeitung (High Speed Machining = HSM) bezeichnet.
Beim Fräsen in kurz spanenden Werkstoffen wie Grauguss kann ein Planfräser mit extra enger Teilung für einen hohen Tischvorschub eingesetzt werden. In HRSA-Werkstoffen, bei denen die Schnittgeschwindigkeit normalerweise gering ist, sorgt ein Fräser mit extra enger Teilung für hohe Tischvorschübe.
Planfräsen mit sehr hohem Vorschub pro Zahn (bis zu 4 mm/Zahn) wird durch Einsatz von Fräsern mit kleinem Einstellwinkel oder runden Wendeschneidplatten aufgrund der abnehmenden Spandicke ermöglicht. Obwohl die Schnitttiefe bis auf weniger als 2.8 mm begrenzt ist, gewährleistet diese extreme Hochvorschub-Fräsbearbeitung höchste Produktivität. Bestimmte Fräskonzepte sind für den Einsatz mit extrem hohem Vorschub bei geringen Schnitttiefen optimiert. Ein kleiner Einstellwinkel ist Voraussetzung für eine leichte, schnelle Fräsbearbeitung bei hohem Vorschub.
Wahl der Werkzeuge
Hochvorschubfräser
Max. Schnitttiefe (ap), mm | 1.2 - 2 |
Fräserdurchm. (Dc), mm | 25 - 160 |
Werkstoff | ![]() |
Rundplattenfräser
Max. Schnitttiefe (ap), mm | 1.3 |
Fräserdurchm. (Dc), mm | 10 - 25 |
Werkstoff | ![]() |
Medium HF
Max. Schnitttiefe (ap), mm | 1.3 | 10 | 7/8 | 2.8 |
Fräserdurchm. (Dc), mm | 4 - 20 | 25 - 160 | 10 - 42 / 25 - 125 | 63 - 160 |
Werkstoff | ![]() | ![]() | ![]() | ![]() |
Hochvorschubfräser:
- Produktiver Hochvorschubfräser mit 10° Einstellwinkel für einen hohen Vorschub pro Zahn, fz
- Hohe Vorschubraten bei geringen Schnitttiefen, ap
- Hoch präzise Werkzeuge für die Hochgeschwindigkeitsbearbeitung in gehärteten Stahl
- Schruppen bis Vorschlichten von Konturen und asymmetrischen Konfigurationen bei extrem hohen Vorschüben
Hinweis: Bei Rundplattenfräsern und Fräsern mit großem Radius sollte der ap-Wert weit unter dem Maximalwert liegen, um Hochvorschubfräsen zu ermöglichen
Rundplattenfräser:
- Stärker abnehmende Spandicke bei reduziertem Axialschnitt
- Leichte Schneidwirkung
- Universalfräser für schwierige bis leichte Bedingungen
Korrekte Anwendung
Fräser mit kleinem Einstellwinkel
Fräser mit sehr kleinen Einstellwinkeln ermöglichen eine erhebliche Vorschuberhöhung, fz, aufgrund der abnehmenden Spandicke bei kleinem ap-Wert.
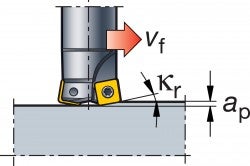
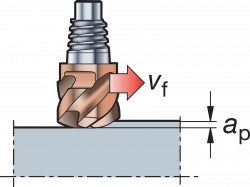
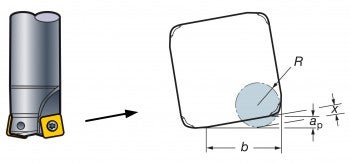
IC | Abmessungen, mm | Unbearbeiteter Werkstoff | ||
iC | R | b | ap | x |
9 | 2.5 | 7.05 | 1.2 | 0.79 |
14 | 3.5 | 12.0 | 2.0 | 1.48 |
Die maximale Spandicke wird durch einen kleinen Einstellwinkel deutlich reduziert. So werden extrem hohe Vorschubraten erreicht, ohne dabei die Wendeschneidplatten zu überlasten.
Hinweis: Vermeiden Sie es, bis ganz an eine 90°-Schulter zu bearbeiten, da der positive Effekt eines geringen Einstellwinkels verloren geht, d.h. die Schnitttiefe vergrößert sich dramatisch.
Wie in allen Fällen muss die Vorschubgeschwindigkeit vermindert und den spezifischen Bearbeitungsbedingungen angepasst werden, um Vibrationen zu vermeiden, welche die Wendeschneidplatten beschädigen können.
Rundplattenfräser
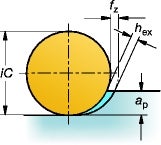
Spandicke, hex, variiert mit runden Wendeschneidplatten und ist abhängig von der Schnitttiefe, ap. Wird eine Planfräsbearbeitung bei hohem Vorschub mit Rundplattenfräsern durchgeführt, sollte dieSchnitttiefe niedrig gehalten werden (max. 10% des Wendeschneidplattendurchmessers, iC, anderenfalls wird der Effekt einer abnehmenden Spandicke reduziert und der Vorschub muss verringert werden, siehe Abbildung.
Hinweis: Beim Einsatz von Rundplattenfräsern ist es wichtig, den Vorschub beim Erreichen einer Wand/Schulter zu reduzieren, da sich die Schnitttiefe schlagartig erhöht.
Robuste Wendeschneidplatten für allgemeines Schruppen
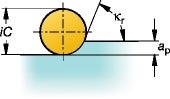
Bei runden Wendeschneidplatten variiert die Spanlast und der Einstellwinkel mit der Schnitttiefe. Die beste Leistung wird erzielt, wenn die Schnitttiefe kleiner als 25% x Wendeplattendurchmesser (iC) ist.
Suchen Sie Werkzeugempfehlungen?
Hier finden Sie unsere Zerspanungswerkzeuge chevron_right
Brauchen Sie Beratung?
Stellen Sie uns eine Frage chevron_right
Was es sonst noch über die Grundlagen unserer Metallzerspanung zu lernen gibt?
Registrieren Sie sich für unser kostenloses E-Learning Programm chevron_right
Heavy Duty Planfräsbearbeitung
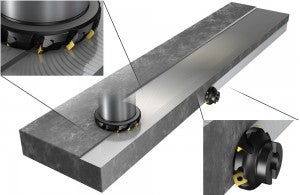
Was ist erfolgreiches Heavy Duty Planfräsen?
Heavy Duty Planfräsbearbeitungen umfassen das Schruppen von warmgewalzten oder schweren geschmiedeten Werkstückrohlingen, Gehäusen, und geschweißten Strukturen in großen Portalfräsmaschinen und leistungsstarken Fräsmaschinen oder Bearbeitungszentren. Große Mengen an Werkstückstoff müssen zerspant werden, wobei hohe Temperaturen und Schnittkräfte entstehen und besondere Anforderungen an die Wendeschneidplatten stellen:
- Hohe Belastung der Hauptschneidkante im Bereich der max. Schnitttiefe
- Verschleiß der Schneidkante durch abrasive Schmiedehaut, wenn Schnitttiefe nahe Null
Für einen Heavy Duty Planfräser ist ein 60º Einstellwinkel optimal. Diese Ausführung gewährleistet:
- Gute Schnitttiefenkapazität, relativ gleichmäßige Schnittkräfte und eine abnehmende Spandicke ermöglichen hohe Vorschubraten
- Bedingt durch die axiale Toleranz der Fräserausführung ist eine große Planfase der Wendeschneidplatte möglich, die für eine hohe Oberflächengüte sorgt
Wahl der Werkzeuge
Planfräser für die Heavy Duty Bearbeitung
Einstellwinkel (κr), mm | 60° | 45° | 90° | Runde Wendeschneidplatten |
Max. Schnitttiefe (ap), mm | 13/18 | 10 | 15.7 | 12.5 |
Fräserdurchm. (Dc), mm | 160 - 500 | 80 - 250 | 40 - 200 | 66 - 200 |
Werkstoff | ![]() | ![]() | ![]() | ![]() |
60° Planfräser für die Heavy Duty Bearbeitung
- Ausgelegt für ein effizientes Werkzeughandling, mit der Folge kurzer Nebenzeiten und sicherer, schneller und schneller Wendeschneidplattenwechsel in der Maschine
- Schnitttiefen bis zu 18 mm möglich, dadurch hohes Zeitspanvolumen und Bearbeitung ungleichmäßiger, unebener, welliger Flächen
- Hohe Produktivität – Vorschubgeschwindigkeiten von 0,4 – 0,7 mm pro Zahn
- Großzügige Planfase für gute Ergebnisse beim Vorschlichten
- Stabile Schneidkante für hohen Widerstand gegen abrasive Guss- und Schmiedehaut bei geringer Schnitttiefe
- Robuster Fräser, für Prozesssicherheit bei anspruchsvollen Bearbeitungen
45-90° Planfräser für die Medium Duty Bearbeitung
- Ein Planfräser für mittlere Bearbeitungen und dabei besonders leichtschneidend
- Schnitttiefen von 6–8 mm innerhalb eines Vorschubbereichs von 0,2 – 0,6 mm/Zahn möglich
- Für anspruchsvolle Bedingungen in größeren Bearbeitungszentren
- Einsatz mit Wiper-Wendeschneidplatten zum Fräsen hochwertiger Oberflächen möglich
- Erste Wahl für Medium Duty Planfräs- und Eckfräsanwendungen
Fräser mit großen, runden Wendeschneidplatten
- Ein Medium Duty Fräser mit stabilen Schneiden für schwierige Zerspanungsbedingungen, wie die Bearbeitung von Guss- und Schmiedehaut und unterbrochene Schnitte. Die runde Wendeschneidplattengeometrie sorgt für eine leichte Schneidwirkung
- Bei günstigen Bedingungen lassen sich bis zu acht Schneidkanten einsetzen
- Die maximale Schnitttiefe beträgt 10 mm. Die maximal empfohlene Spandicke variiert stark bis zu 0.55 mm pro Zahn, je nach Wendeschneidplattengeometrie und Schnitttiefe
Korrekte Anwendung
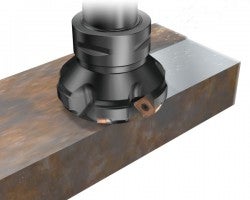
Bei Heavy Duty Anwendungen werden Fräser mit großen Wendeschneidplatten und großen Durchmessern eingesetzt. Die Schnittgeschwindigkeit ist normal, aber ein hoher ap und fz-Wert, in Kombination mit einem großen ae-Wert machen diesen Fräser zu einer sehr produktiven Lösung.
Eintritt in den Schnitt
Aufgrund der bei der Heavy Duty Fräsbearbeitung üblichen schwierigen Bedingungen ist der Eintritt in den Schnitt häufig entscheidend.
- Falls möglich, Ein- und Austritt des Fräsers mit Einlaufradius programmieren
- Wenn nicht, Vorschub reduzieren, bis der Fräser komplett im Schnitt ist
Fräserposition und -größe
Bei der Heavy Duty Fräsbearbeitung, bei der häufig viele Durchgänge durchgeführt werden, um eine große Oberfläche zu bearbeiten, ist es wichtig, die folgenden Empfehlungen besonders zu berücksichtigen:
- Fräserposition und -eingriff
- Fräsergröße in Relation zur Werkzeugmaschinenkapazität
- Werkzeugweg zur Vermeidung eines ungünstigen Austritts
Hohe Temperaturen berücksichtigen
Anspruchsvolle Heavy Duty Fräsbearbeitungen erzeugen hohe Temperaturen. Werden magnetische Tische zur Spannung des Werkstücks verwendet, bleiben die Späne häufig am Fräser haften. Folge davon ist eine unterbrochene oder nur partielle Spanabfuhr ebenso wie ein erneutes Schneiden der Späne, was die Standzeit beeinträchtigen kann. Um dies zu vermeiden, muss darauf geachtet werden, dass der Arbeitsbereich frei von Spänen bleibt. Um zu vermeiden, dass die anfälligen Wendeplattenecken gegen die abrasive Schmiedehaut reiben, die Schnitttiefe erhöhen, damit der Kontaktpunkt an der stabileren Hauptschneide liegt.
Hinweis: Zum Schutz vor Wärme und daraus resultierenden Verletzungen sind bei der Montage der Wendeschneidplatten im Fräser Handschuhe tragen.
Schlichten mit Wiper-Wendeschneidplatten
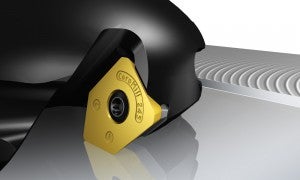
Erzielung einer erfolgreichen Oberflächengüte beim Planfräsen
Durch die Verwendung von Standard-Wendeschneidplatten in Kombination mit einer oder mehreren Wiper-Wendeschneidplatten kann eine ausgezeichnete Oberflächengüte erzielt werden. Wiper-Wendeschneidplatten arbeiten am erfolgreichsten bei hohen Vorschüben, fn, in Fräsern mit größerem Durchmesser, extra enger Teilung und Einstellmöglichkeiten.
Der Vorschub pro Umdrehung kann bei gleichbleibend hoher Oberflächengüte um circa das Vierfache erhöht werden. Wiper-Wendeschneidplatten können für Fräsbearbeitungen in den meisten Werkstückstoffen eingesetzt werden, um eine hohe Oberflächengüte auch bei ungünstigen Bedingungen zu erzielen.
Wahl der Werkzeuge
Fräser
Einstellwinkel (Kr), mm | 45° | 45° | 65° | 90° | 25° | 90° |
Max. Schnitttiefe (ap), mm | 6 | 10 | 6 | 10 | 0.9 | 8.1 |
Fräserdurchm. (Dc), mm | 40 - 250 | 32 - 250 | 40 - 250 | 40 - 200 | 80 - 250 | 125 - 500 |
Oberflächengüte (Ra) | < 1.0 | < 1.0 | < 1.0 | < 1.0 | < 1.0 | < 1.0 |
Werkstoff | ![]() | ![]() | ![]() | ![]() | ![]() | ![]() |
Wiper-Wendeschneidplatten sind in verschiedenen Längen (bs) erhältlich, wobei beide Schneidkanten oft in Rechts- und Linksausführung vorhanden sind. Es sind Sorten für die meisten Werkstoffe erhältlich. Einstellbare Plattensitze für spezielle anwendungsspezifische Fräser zum Schlichten oder Kassettenlösungen sind ebenfalls verfügbar.
Korrekte Anwendung
Bei Schlichtanwendungen mit einem großen Planfräser sollte der Vorschub, fz, in der Regel niedrig gehalten werden. Allerdings kann der Vorschub bei Einsatz von Wiper-Wendeschneidplatten ohne Einbußen an Oberflächenqualität um das Zwei- bis Dreifache erhöht werden.
Hochglanzoberflächen bei hohen Vorschüben
Oberflächenrauheit | ||
![]() |
Vorschub fn | |
fn1 <= 0.8 * bs1 | fn2 <= 0.6 * bs2 |
A : Nur Standard-Wendeschneidplatten
B : Mit einer Wiper-Wendeschneidplatte
C : fn = Vorschub/Umdrehung
bs1 | bs2 | |
![]() |
- Wenn fn 80% der Länge der Planfase, bs, einer Standard-Wendeschneidplatte übersteigt, sorgt eine Wiper-Wendeplatte für eine höhere Oberflächengüte.
- Nimmt der Vorschub pro Umdrehung fn, bei Fräsern mit großem Durchmesser und einer großen Anzahl Wendeschneidplatten zu, dann sind zur Bewahrung der hohen Oberflächengüte der Einsatz von Wiper-Wendeschneidplatten unverzichtbar.
- Der axiale Rundlauffehler des Fräsers, der von der Spindelneigung, Fräsergröße, der Positionierung und der Präzision der Einstellung abhängig ist, beeinflusst die Welligkeit der hergestellten Oberfläche. Die Wiper Schneidkante ist ballig (großer Radius) und stellt somit eine stufenlose Oberfläche her. Dabei sollte der Vorschub pro Umdrehung auf 60% der Wiper-Planfase begrenzt sein, um die hohe Oberflächengüte zu gewährleisten.
- Bei der Montage in Fräsern mit festen Plattensitzen steht die Wiper-Wendeplatte um ca. 0,05 mm im Vergleich zu den anderen Wendeschneidplatten vor. Bei CoroMill Fräsern in Kassettenausführung ist eine hochpräzise Einstellung der Position der Wiper-Schneidkante möglich. Durch die hervorstehende Position ist die Wiper- Wendeschneidplatte größeren Belastungen ausgesetzt, als herkömmliche Wendeschneidplatten, was zu Vibrationen führen kann. Daher sollten Wiper-Wendeplatten zur leichten Zerspanung bei mittleren Schnitttiefen und in begrenzter Zahl eingesetzt werden.
- Die Schnitttiefe sollte gering sein, um die Axialkräfte und Vibrationsgefahr gering zu halten. Für Schlichtanwendungen beträgt die empfohlene Schnitttiefe 0.5 – 1.0 mm
- Beim Klemmen der Wiperplatte ist darauf zu achten, dass die lange Schneidkante richtig positioniert ist.
Beispiel:
- Die Breite der Planfase bs, der Wendeschneidplatte beträgt 1,5 mm.
- Es befinden sich 10 Wendeschneidplatten im Fräser und der Vorschub pro Zahn beträgt fz 0.3 mm. Der Vorschub pro Umdrehung, fn, ist daher 3 mm (d.h. ist doppelt so groß wie die Länge der Planfase)
- Um eine hohe Oberflächengüte sicherzustellen, muss der Vorschub pro Umdrehung maximal 80% von 1.5 mm = 1.2 mm betragen
- Eine entsprechende Wiper-Wendeschneidplatte verfügt über eine Planfase mit einer Breite von 8 mm
- Ergebnis: Vorschub pro Umdrehung konnte von 1.2 mm auf 60% von 8 mm = 4.8 mm erhöht werden
Hinweis: Weitere Begrenzungen wie die Maschinenleistung müssen berücksichtigt werden.
Checkliste und Hinweise für die Anwendung
Tipps zur Erzielung einer „Hochglanzoberfläche”:
- Für eine glänzende Oberfläche hohe Schnittgeschwindigkeiten und/oder Cermet-Wendeschneidplatten wählen
- Für adhäsive ISO M und S Werkstoffe Kühlschmierstoff oder Ölnebel verwenden
- PVD-beschichtete Wendeschneidplatten mit scharfen Schneiden und einem ap-Wert von 0.5 – 0.8 mm erzeugen die beste Oberflächengüte
- Dieselbe Sorte für die Standard- und Wiper-Wendeschneidplatten verwenden
Suchen Sie Werkzeugempfehlungen?
Hier finden Sie unsere Zerspanungswerkzeuge chevron_right
Brauchen Sie Beratung?
Stellen Sie uns eine Frage chevron_right
Was es sonst noch über die Grundlagen unserer Metallzerspanung zu lernen gibt?
Registrieren Sie sich für unser kostenloses E-Learning Programm chevron_right