Co to jest frezowanie profilowe?
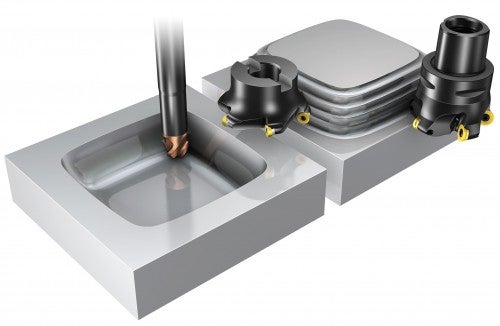
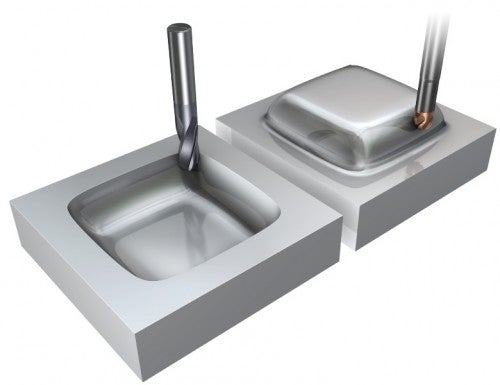
Frezowanie profilowe to często stosowana technologia frezarska. Płytki okrągłe i koncepcyjne z zaokrąglonym narożem używane są we frezach służących do obróbki zgrubnej i półzgrubnej, natomiast frezy z zakończeniem kulistym służą do obróbki wykończeniowej i super-wykończeniowej.
Proces frezowania profilowego
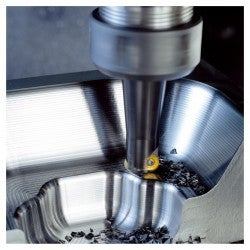
Frezowanie profilowe obejmuje frezowanie wieloosiowe wypukłych i wklęsłych powierzchni 2D i 3D. Im większy przedmiot i im bardziej skomplikowana konfiguracja obrabiarki, tym ważniejsze jest zaplanowanie procesu frezowania profilowego.
Obróbkę należy podzielić na przynajmniej trzy operacje:
- Obróbka zgrubna/pół-zgrubna
- Obróbka pół-wykończeniowa
- Obróbka wykończeniowa
Niekiedy konieczne jest bardzo dobre wykończenie, wykonywane przy użyciu skrawania szybkościowego. Frezowanie pozostałego naddatku, tzw. frezowanie resztkowe, jest częścią obróbki półwykończeniowej i wykończeniowej. W celu osiągnięcia najwyższej precyzji i produktywności zaleca się wykonanie obróbki zgrubnej i wykończeniowej na osobnych obrabiarkach oraz użycie do każdej z tych czynności optymalnych narzędzi skrawających.
Obróbkę wykończeniową należy wykonać przy użyciu obrabiarki 4/5-osiowej dysponującej zaawansowanym oprogramowaniem i możliwościami programowania. Dzięki temu można ograniczyć, a nawet całkowicie wyeliminować czasochłonne wykończanie ręczne. W efekcie uzyskany produkt końcowy będzie cechował się większą dokładnością i lepszą jakością struktury powierzchni.
Wybór narzędzi
Narzędzia skrawające zoptymalizowane pod kątem obróbki zgrubnej i półzgrubnej:
płytki okrągłe i koncepcyjne z zaokrąglonym narożem.
Narzędzia skrawające zoptymalizowane pod kątem obróbki wykończeniowej i super-wykończeniowej:
frez trzpieniowy z czołem kulistym i płytki koncepcyjne z zaokrąglonym narożem.
![]() | ![]() | ![]() | ![]() | |
Płytki okrągłe | Czoło kuliste, na wymienne płytki | Czoło kuliste, wymienna część robocza | Monolityczny frez węglikowy z czołem kulistym | |
Rozmiar gniazda wrzeciona | ISO 40, 50 | ISO 40, 50 | ISO 30, 40 | ISO 30, 40 |
Wymagania odnośnie stabilności | Duże | Średnie | Średnie | Niskie |
Obróbka zgrubna | Bardzo dobra | Dobra | Dopuszczalna | Dopuszczalna |
Obróbka wykończeniowa | Dopuszczalna | Dopuszczalna | Bardzo dobra | Bardzo dobra |
Głębokość skrawania ap | Średnia | Średnia | Mała | Mała |
Wszechstronność | Bardzo duża | Bardzo duża | Bardzo duża | Bardzo duża |
Produktywność | Bardzo duża | Duża | Duża | Duża |
Uwagi i wskazówki odnośnie frezowania profilowego
Należy starannie zbadać profil przedmiotu, aby dobrać właściwe narzędzia i najbardziej odpowiednią metodę obróbki:
- Obliczyć minimalne długości promieni i maksymalną głębokość zagłębienia
- Ocenić ilość materiału do skrawania
- Rozważyć konfigurację narzędzia i mocowanie przedmiotu obrabianego w celu uniknięcia drgań. Wszelkie czynności obróbkowe należy wykonywać na zoptymalizowanych obrabiarkach, aby uzyskać dobry poziom geometrycznej precyzji profilu
- Dzięki zastosowaniu osobnych, precyzyjnych obrabiarek do obróbki wykończeniowej i super-wykończeniowej można ograniczyć, a w niektórych przypadkach wyeliminować konieczność czasochłonnego polerowania ręcznego
- Może być konieczne zastosowanie zaawansowanego programowania w celu uzyskania znacznych oszczędności. Należy użyć węglikowego frezu trzpieniowego do obróbki szybkościowej w celu obróbki z dużą dokładnością wymiarowo-kształtową i osiągnięcia najwyższej możliwej jakości wykończenia powierzchni
- Zasadniczo najbardziej produktywnym sposobem obróbki zgrubnej i półwykończeniowej dużych przedmiotów jest zastosowanie tradycyjnych metod i narzędzi. Wyjątkiem jest aluminium, w przypadku którego duże prędkości skrawania są używane także podczas obróbki zgrubnej
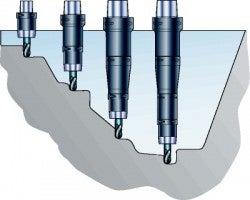
Jak zmniejszyć drgania
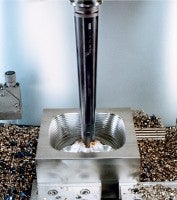
Drgania są przeszkodą podczas frezowania głębokich profili przy zastosowaniu dużych wysięgów. Często stosowaną metodą przezwyciężenia tego problemu jest zmniejszenie głębokości skrawania, prędkości lub posuwu.
- Używać sztywnych narzędzi modułowych charakteryzujących się dużą dokładnością ruchu obrotowego
- Narzędzia modułowe zwiększają elastyczność i zakres możliwych zastosowań
- Używać narzędzi z tłumieniem drgań lub trzonków przedłużających, jeśli całkowita długość narzędzia, od linii pomiarowej do najniższego punktu krawędzi skrawającej, przekracza 4- lub 5-krotność średnicy na linii pomiarowej
- Używać przedłużeń wykonanych z ciężkiego metalu, jeśli trzeba znacznie zwiększyć odporność na zginanie
- Używać wyważonych narzędzi skrawających i uchwytów w przypadku prędkości wrzeciona przekraczających 20 tys. obr./min
- Wybierać przedłużenia i adaptery o możliwie największej średnicy w stosunku do średnicy frezu
- 1 mm (0.039 cala) to wystarczająca różnica promieniowa między uchwytem i narzędziem skrawającym. Używać frezów o nadwymiarowych średnicach
- Frezowanie wgłębne stanowi alternatywną metodę frezowania przy użyciu bardzo długich narzędzi
Długość narzędzia należy zwiększać stopniowo
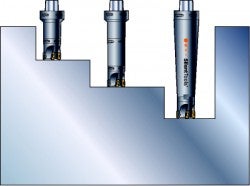

Dla podtrzymania maksymalnego poziomu produktywności podczas obróbki zgrubnej, w trakcie której ostatnie przejście następuje głęboko w przedmiocie obrabianym, ważne jest zastosowanie szeregu przedłużeń frezu.
- Należy zacząć od najkrótszego przedłużenia, gdyż dłuższe przedłużenia ograniczają produktywność i mają tendencję do powodowania drgań
- Zmiany narzędzia na wydłużone należy przeprowadzać w położeniach zdefiniowanych wstępnie w programie. Geometria zagłębienia decyduje o miejscu wymiany narzędzia
- Należy dostosowywać parametry skrawania do poszczególnych długości narzędzia, aby podtrzymać maksymalny poziom produktywności
Efektywna prędkość skrawania
Jeśli do obliczania prędkości skrawania używana jest znamionowa wartość średnicy narzędzia w przypadku frezu z czołem kulistym lub na płytki okrągłe, efektywna prędkość skrawania, vc, będzie znacznie niższa, jeśli głębokość skrawania, ap, jest niewielka. Poważnie ograniczy to prędkość posuwu i produktywność.
Podstawą dla obliczeń prędkości skrawania musi być rzeczywista lub efektywna średnica podczas przejścia, Dcap.
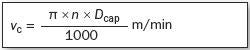
Frez trzpieniowy z czołem prostym
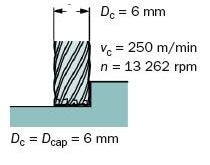
Frez z zakończeniem kulistym
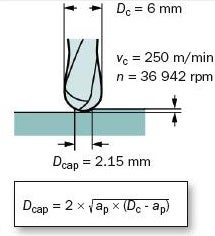
Frez na płytki okrągłe
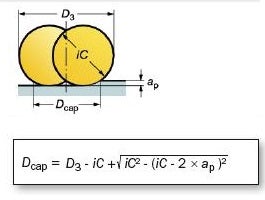
Frezowanie punktowe – nachylony frez
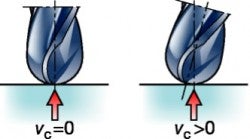
Podczas używania frezu trzpieniowego z czołem kulistym, punktem krawędzi skrawającej o zasadniczym znaczeniu jest jej część na przecięciu z osią obrotu narzędzia, gdzie prędkość skrawania jest bliska zeru, co ma niekorzystny wpływ na proces skrawania. Odprowadzanie wiórów z okolic osi obrotu frezu ma zasadnicze znaczenie ze względu na wąską przestrzeń od jego krawędzi do powierzchni obrabianej.
Dlatego zaleca się przechylenie wrzeciona lub przedmiotu obrabianego o 10–15 stopni, co powoduje odsunięcie strefy skrawania od osi obrotu.
- Minimalna prędkość skrawania będzie mniejsza
- Większa trwałość i lepszy przebieg formowania wiórów
- Gładsza powierzchnia
Przykład frezu z ostrzami centralnymi
Część środkowa, z = 2
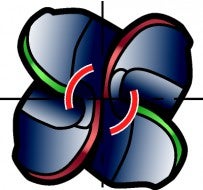
Część zewnętrzna, z = 4
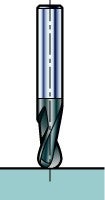
Z = 2
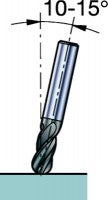
Z = 4
Płytkie przejście
Podczas korzystania z frezu na płytki okrągłe lub frezu z czołem kulistym przy mniejszej głębokości skrawania można zwiększyć prędkość skrawania, vc, z powodu krótkiego czasu zagłębienia krawędzi skrawającej. Skraca się czas rozchodzenia się wysokiej temperatury w strefie skrawania, tzn. temperatura krawędzi skrawającej i przedmiotu obrabianego pozostaje niska. Można zatem zwiększyć posuw/ostrze, fz, dzięki efektowi tworzenia cienkich wiórów.
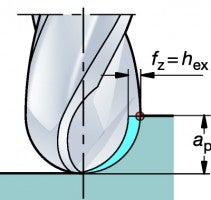
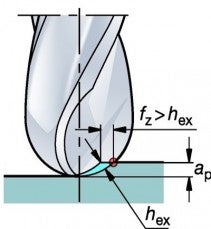
Płytkie przejście
Przykład płytkiego przejścia, porównanie frezu nieodchylonego z odchylonym
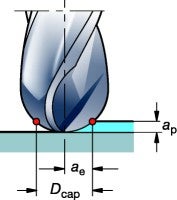
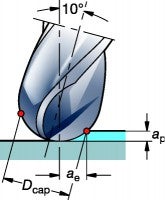
Przykład ten pokazuje możliwości zwiększenia prędkości skrawania, gdy wartość ae/ap jest mała, oraz korzyści płynące z zastosowania frezu odchylonego.
Monolityczny frez węglikowy z czołem kulistym
Dc = 10 mm, gatunek GC 1610.
Materiał: Stal, 400 HB
Zalecane parametry skrawania dla przejścia głębokiego ap - Dc/2:
vc = 170 m/min
fz = 0.08 mm/obr. = hex
Rodzaj obróbki | Frez nieodchylony | Frez odchylony (10°) |
Obróbka półwykończeniowa ap - 2 mm (0.079 cala)
vc - 300 m/min (984 stopy/min)
Posuw na ostrze, fz, jest w przypadku frezu nieodchylonego i | Dc = 10 mm (0.394 cala)
vc = 300 m/min (984 stopy/min)
hex = 0.08 mm (0.003 cala)
vf = 2 860 mm/min (113 cala/min) | Dc = 10 mm (0.394 cala)
vc = 300 m/min (984 stopy/min)
hex = 0.08 mm (0.003 cala)
vf = 5 100 mm/min (201 cala/min) |
Super-wykończanie ae - 0.1 mm
vc - 5 * 170 - 850 m/min (557–2789 stopy/min)
Uwaga: Do obróbki super-wykończeniowej należy użyć frezu z dwoma ostrzami zn = 2, aby
fz - 0.12 mm/ostrze (0.005 cala/ostrze) | Nie zaleca się używania frezu nieodchylonego do obróbki super-wykończeniowej | Dc = 10 mm (0.394 cala)
vc = 850 m/min (2789 stopy/min)
hex = 0.02 mm (0.0008 cala)
vf = 14 600 mm/min (575 cala/min) |
Produktywność frezowania profilowego: stały naddatek
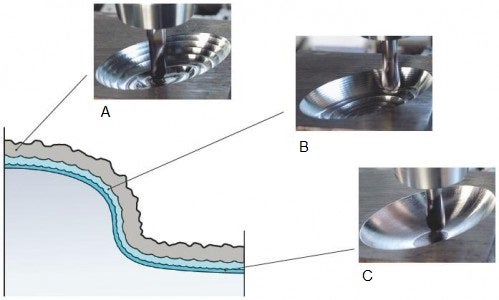
A: Obróbka zgrubna
B: Obróbka półwykończeniowa
C: Obróbka wykończeniowa i super-wykończeniowa
Zachowanie stałego naddatku jest jednym z podstawowych kryteriów wysokiej i stałej wydajności podczas profilowania, zwłaszcza przy użyciu dużych prędkości.
- Ważne jest, aby w celu uzyskania jak najwyższego poziomu produktywności podczas tych czynności, często wykonywanych podczas produkcji form i matryc, dostosować rozmiar frezu do konkretnej czynności
- Celem nadrzędnym jest uzyskanie równomiernego rozkładu luzu roboczego, lub naddatku, aby osiągnąć małą liczbę zmian obciążenia i kierunku dla każdego z używanych narzędzi
Często korzystniejsze jest zmniejszanie rozmiarów różnych frezów, z większych na mniejsze, zwłaszcza podczas lekkiej obróbki zgrubnej lub półwykończeniowej, zamiast używania wyłącznie jednej średnicy podczas każdej z czynności.
- Najlepszą jakość podczas obróbki wykończeniowej uzyskuje się, gdy po zakończeniu czynności pozostaje jak najmniejszej grubości i jak najbardziej równomierna warstwa naddatku
- Celem powinno być zawsze jak największe zbliżenie się do osiągnięcia wymogów odnośnie ostatecznego kształtu
- Bezpieczny proces skrawania
Korzyści płynące ze stałej ilości naddatku
- Niektóre obróbki półwykończeniowe i praktycznie wszystkie obróbki wykończeniowe można wykonać w ramach produkcji z udziałem części załogi, a niekiedy nawet bezzałogowej
- Ograniczenie negatywnego wpływu na prowadnice, gwinty toczne i łożyska wrzeciona
Otwieranie zagłębienia w litym materiale
- Podczas otwierania zagłębienia ważny jest wybór takiej metody, która zminimalizuje wartość ap oraz będzie pozostawiać stałą ilość naddatku dla kolejnego frezowania profilowego
- Frezy walcowo-czołowe/trzpieniowe i frezy z długą krawędzią będą pozostawiać naddatek w postaci stopni, który trzeba usuwać. Powoduje to zróżnicowanie sił skrawania i ugięcia narzędzia. Skutkiem jest nierównomierny rozkład naddatku dla obróbki wykończeniowej, który wpływa na geometryczną precyzję ostatecznego kształtu
- Zastosowanie frezów na płytki okrągłe spowoduje powstanie gładkich powierzchni przejściowych między przejściami frezu i pozostawi mniejszą ilość bardziej równomiernie rozłożonego naddatku dla czynności profilowania, dzięki czemu uzyska się wyższą jakość przedmiotu
- Trzecią alternatywą jest zastosowanie do otwarcia zagłębienia frezu do dużych posuwów. Także w tym przypadku skutkiem będzie niewielka i równomiernie rozłożona ilość naddatku dzięki małej głębokości skrawania, tzn. niewielkim stopniom
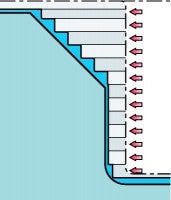
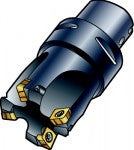
Frez walcowo-czołowy,
pozostaje znaczna i nierównomiernie rozłożona ilość naddatku
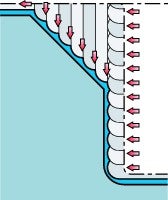
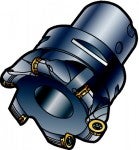
Frez na płytki okrągłe,
pozostaje mała ilość naddatku
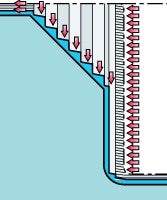
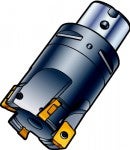
Frez do obróbki z dużym posuwem,
pozostaje mała ilość naddatku
Frezowanie kopiowe
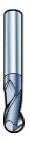
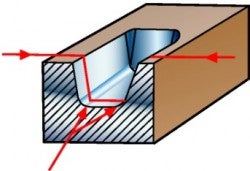
Tradycyjną i najprostszą metodą programowania dróg narzędzia do obróbki zagłębienia jest zastosowanie normalnej technologii frezowania kopiowego, której towarzyszy wiele wejść w materiał i wyjść z niego. Oznacza to jednak, że oprogramowanie, obrabiarki i narzędzia skrawające o dużej mocy są wykorzystywane w bardzo ograniczonym zakresie. Preferowanym rozwiązaniem jest zastosowanie obrabiarki z oprogramowaniem z funkcją przewidywania, umożliwiającą unikanie odchyleń drogi narzędzia.
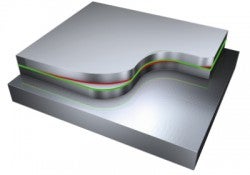
Zasadnicze znaczenie ma otwarte podejście do kwestii wyboru metod, dróg narzędzia, narzędzi frezarskich i uchwytów.
− Duże obciążenie środkowego punktu płytki
− Mniejsze posuwy
− Mniejsza trwałość
− Uderzenia mechaniczne
− Błędy kształtu
− Dłuższe programowanie i czas skrawania
Ścieżka narzędzia do frezowania kopiowego jest często połączeniem frezowania w kierunku do i od dna zagłębienia oraz wymaga wykonania wielu niekorzystnych zagłębień i wyjść podczas przejścia. Każde wejście i wyjście oznacza, że narzędzie odchyli się, pozostawiając wystający ślad na powierzchni. Wówczas wartość sił i wygięcie narzędzia zmaleją, a w obszarze wyjścia pozostanie niewielkie podcięcie materiału.
Wnioski
- Należy w miarę możliwości unikać frezowania kopiowego wzdłuż stromych ścianek. Podczas zagłębiania grubość wiórów jest duża i prędkość skrawania powinna być mała
- Istnieje niebezpieczeństwo zatarcia krawędzi na przecięciu z osią obrotu narzędzia, zwłaszcza wtedy, gdy frez natrafia na dno
- Stosować sterowanie prędkością posuwu z funkcją przewidywania. W przeciwnym wypadku ograniczenie prędkości nie nastąpi na tyle szybko, aby uniknąć uszkodzeń krawędzi w osi narzędzia
- Gdy frez natrafi na ściankę, nastąpi szerokie opasanie krawędzi skrawającej, połączone z niebezpieczeństwem ugięcia, drgań lub pęknięcia narzędzia
- W przypadku stosowania frezów trzpieniowych z zakończeniem kulistym, obszarem mającym zasadnicze znaczenie jest punkt na osi obrotu narzędzia, ponieważ w tym miejscu prędkość skrawania wynosi zero. Należy unikać wykorzystywania obszaru wokół osi obrotu narzędzia i stosować frezowanie punktowe poprzez odchylenie wrzeciona lub przedmiotu obrabianego w celu uzyskania lepszych warunków obróbki
- Rozwiązaniem nieco lepszym dla procesu skrawania jest kopiowanie w kierunku od dna wzdłuż stromych ścianek, gdyż grubość wióra osiąga wartość maksymalną przy bardziej korzystnej prędkości skrawania
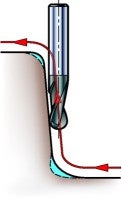
Ryzyko żłobienia
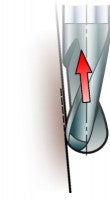
Kopiowanie w kierunku do wrzeciona:
Maksymalna grubość wióra przy zalecanej wartości vc.
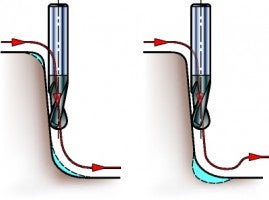
Na dnie zagłębienia:
Niebezpieczeństwo zatarcia krawędzi na osi obrotu narzędzia.
Często występują błędy kształtu, zwłaszcza przy zastosowaniu technologii obróbki z dużą prędkością.
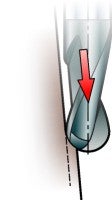
Kopiowanie w kierunku od wrzeciona:
Duża grubość wióra przy bardzo niskiej wartości vc.
Redukcja posuwu w celu uniknięcia zmniejszenia trwałości
Odwracanie kierunku kopiowania do i od wrzeciona narazi narzędzie na naprzemienne kierunki odchylania i działania siły. Poprzez zmniejszenie posuwu na krytycznych odcinkach drogi narzędzia, ogranicza się ryzyko zatarcia krawędzi i uzyskuje większe bezpieczeństwo skrawania oraz większą trwałość.
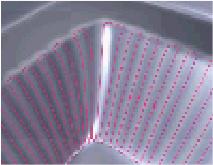
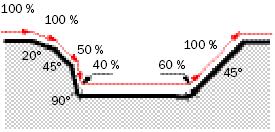
Frezowanie kształtowe
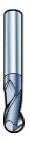
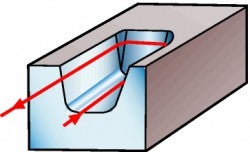
Zamiast korzystania z technik programowania ograniczających się do redukcji materiału „plasterek po plasterku” przy stałej wartości Z, korzystne jest stosowanie kształtowych dróg narzędzia w połączeniu z frezowaniem w kierunku od wrzeciona. Oto rezultaty:
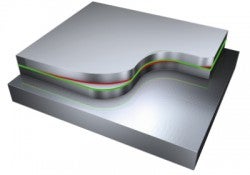
+ Znacznie krótszy czas obróbki
+ Lepsze wykorzystanie obrabiarki i narzędzia
+ Lepsza jakość geometrii obrabianego kształtu
+ Mniej czasochłonna obróbka wykończeniowa i polerowanie ręczne
+ Sterowanie prędkością skrawania - ve
+ Obsługa obróbki z wysokimi prędkościami (HSM)
+ Duże posuwy
+ Duża trwałość ostrzy
+ Bezpieczeństwo
Początkowe programowanie jest trudniejsze i trwa nieco dłużej; jednak można to szybko zrekompensować, gdyż koszt godziny pracy obrabiarki jest zazwyczaj trzykrotnie wyższy niż w przypadku stacji roboczej programisty. Preferowanym rozwiązaniem jest zastosowanie obrabiarki z oprogramowaniem z funkcją przewidywania, umożliwiającą unikanie odchyleń drogi narzędzia.Wnioski
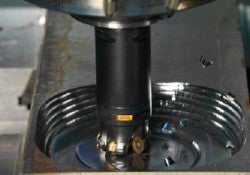
- Należy używać drogi narzędzia typu kształtowego, takiej jak „Waterline milling”, jako najlepszej metody zapewnienia frezowania współbieżnego
- Frezowanie kształtowe przy użyciu zewnętrznej części frezu często skutkuje większą produktywnością, gdyż więcej ostrzy jest zagłębianych podczas przejścia na narzędziu o większej średnicy
- Jeśli prędkość obrotowa wrzeciona w obrabiarce jest ograniczona, frezowanie kształtowe pomoże utrzymać prędkość skrawania i sterować nią
- Ponadto podczas frezowania kształtowego następuje mniej szybkich zmian obciążenia roboczego i kierunku. Ma to szczególne znaczenie w przypadku frezowania z dużymi prędkościami i posuwami oraz w materiałach hartowanych, ponieważ krawędź skrawająca i przebieg procesu są bardziej narażone na zmiany, które mogą powodować różnice odchylenia lub powstawanie drgań
- Aby zapewnić długą trwałość narzędzia, należy jak najdłużej utrzymywać zazębienie w materiale
Uwaga! Unikać skrawania przy użyciu obszaru ostrza w osi obrotu narzędzia, gdzie prędkość skrawania wynosi zero.
Strategia drogi narzędzia
Frezowanie kształtowe ze stałą wartością Z, dwie osie. Obróbka zgrubna i wykończeniowa
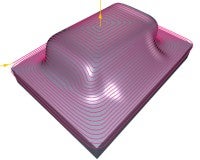
Frezowanie kształtowe Waterline milling ze stałą wartością Z
- Stosowane często, gdy dostępna jest funkcja maksymalnego zagęszczenia dróg sterowana przez CAM
- Płynne zagłębianie i wycofywanie
- Łatwy sposób programowania
- Szeroki wybór narzędzi
Frezowanie kształtowe z interpolacją śrubową, od trzech do pięciu osi. Obróbka wykończeniowa
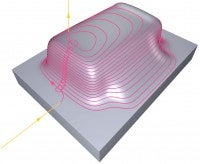
Frezowanie kształtowe wzdłuż zagłębiającej się drogi narzędzia
- Łagodne zmiany kierunku
- Dobra precyzja kształtu i chropowatość powierzchni
- Sterowana wysokość przejścia
- Stałe zagłębienie
- Krótkie programy
- Krótkie narzędzie
Tworzenie powierzchni rzeźbionych
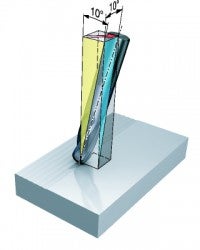
Frezowanie współbieżne za pomocą frezu odchylonego o ok. 10° w obydwu kierunkach zapewnia dobrą chropowatość powierzchni i niezawodność działania. Frez z czołem kulistym lub z zaokrągleniem na narożach (tzw. z promieniem) ukształtuje powierzchnię z określoną wysokością przejścia, h, zależną od:
- Szerokości, ae, przejścia
- Posuwu na ostrze, fz
Inne ważne czynniki to głębokość skrawania, ap, wpływająca na rozkład siły, oraz odczyt odchyłki bicia narzędzia – TIR. Aby uzyskać jak najlepsze wyniki należy:
- Stosować precyzyjną oprawkę z mocowaniem hydraulicznym ze złączem Coromant Capto®
- Zastosować jak najkrótszy wysięg
Obróbka zgrubna i półzgrubna
Jeśli posuw na ostrze jest znacznie mniejszy od szerokości i głębokości skrawania, wytworzona powierzchnia będzie cechować się znacznie mniejszą wysokością śladu obróbkowego w kierunku posuwu.
Frezy do obróbki wykończeniowej i obróbki super-wykończeniowej
Korzystne jest uzyskanie gładkiej, symetrycznej faktury powierzchni we wszystkich kierunkach, którą można później wypolerować z łatwością niezależnie od wybranej metody polerowania.
Efekt ten uzyskuje się, gdy fz ≈ ae.
Aby uzyskać jak najlepszą fakturę powierzchni, należy zawsze używać do obróbki super-wykończeniowej nachylonego frezu z dwoma ostrzami.
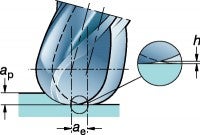
Obróbka półzgrubna przy wartości fz znacznie mniejszej niż ae
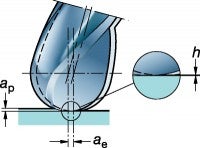
Obróbka super-wykończeniowa przy użyciu nachylonego frezu i wartości fz równej ae
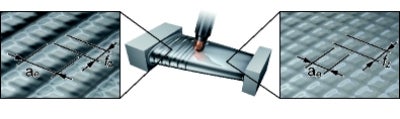