Frezowanie czołowe
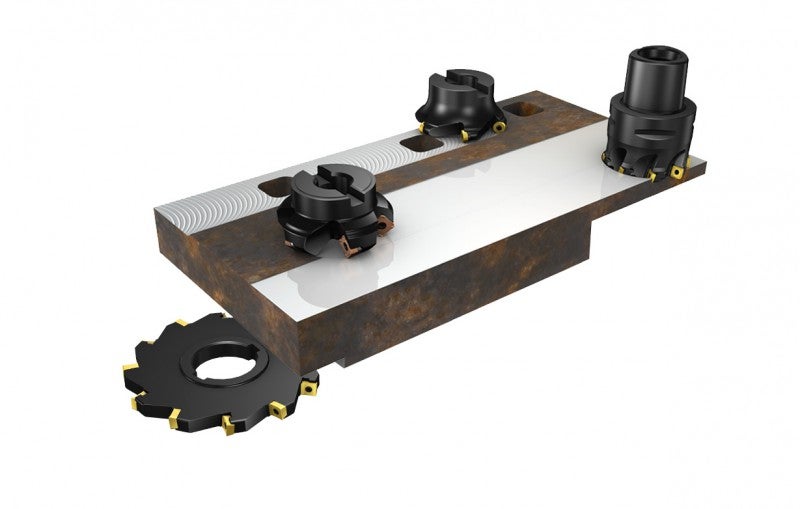
Do frezowania czołowego zaliczamy:
- Frezowanie czołowe płaszczyzn
- Frezowanie z wysokimi posuwami
- Ciężkie frezowanie czołowe
- Obróbka wykończeniowa przy użyciu płytek Wiper
Frezowanie czołowe płaszczyzn
Na czym polega udane frezowanie czołowe?
Frezowanie czołowe to najczęściej występujący zabieg obróbki frezarskiej. Można go realizować za pomocą wielu różnych narzędzi. Najczęściej używane są głowice frezarskie o kącie przystawienia 45º, ale w określonych warunkach wykorzystuje się także frezy na płytki okrągłe, frezy walcowo-czołowe oraz frezy tarczowe. Należy upewnić się, że frez wybrany do wykonania danej czynności zapewni optymalną produktywność (patrz informacje dotyczące wyboru narzędzi poniżej).
Wybór narzędzi
Przegląd frezów do frezowania czołowego
Poniższy diagram ilustruje główne obszary zastosowania dla różnych koncepcji frezu w odniesieniu do głębokości skrawania, ap, oraz posuwu na ostrze, fz.
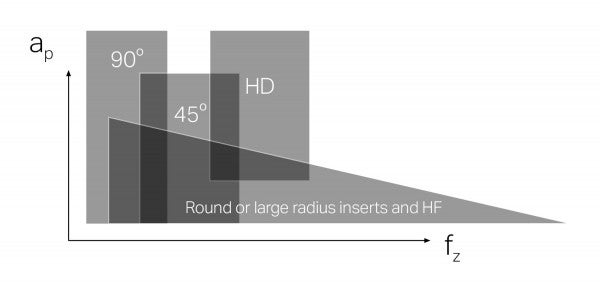
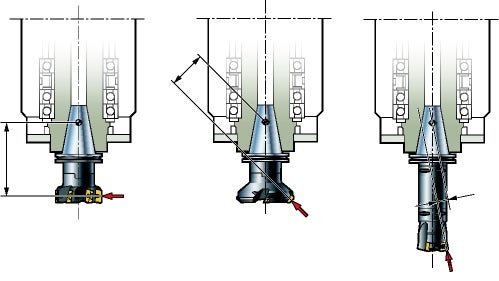
Kierunek oddziaływania całkowitej siły skrawania w zależności od kąta przystawienia.
Frezy do frezowania czołowego i wgłębnego o kącie przystawienia 10° - 65°
Frezy z tej szerokiej oferty używane są głównie do frezowania czołowego, ale w grupie tej są także frezy o bardzo małym kącie przystawienia nadające się do frezowania wgłębnego.
Frezy o kącie przystawienia 45°
- Pierwszy wybór do frezowania ogólnego
- Ograniczenie drgań przy długich wysięgach i niestabilnych konfiguracjach
- Relatywnie cienkie wióry pozwalają skrawać z wysoką produktywnością
Frezy o kącie przystawienia 90°
- Przedmioty o cienkich ściankach
- Przedmioty słabo zamocowane
- Gdy wymagane jest uzyskanie powierzchni ustawionych pod kątem 90° względem siebie
Frezy na płytki okrągłe i o dużym promieniu zaokrąglenia naroży
Frezy na płytki okrągłe są bardzo wszechstronne, doskonale nadają się do zagłębiania skośnego i są używane tak do ciężkiego frezowania czołowego, jak i do profilowania.
- Frez do wielu różnych zastosowań
- Najbardziej wytrzymała krawędź skrawająca
- Linię krawędzi skrawającej można efektywnie podzielić na ostrza wykorzystywane na wielu pozycjach
- Nadaje się w szczególności do obróbki stopów żaroodpornych, ISO S.
- Stabilny przebieg obróbki
Techniki obróbki - przykład
Frezowanie czołowe
![]() |
||||||||
![]() |
||||||||
Kąt przystawienia 25-65° | Kąt przystawienia 90° | Kąt przystawienia 10° | ||||||
Zalety + Wysoka wydajność + Zoptymalizowany pod kątem frezowania czołowego + Opcje zastosowania płytek z wieloma ostrzami Wady – Umiarkowana głębokość skrawania |
Zalety + Uniwersalny frez nadający się do wielu różnych czynności + Niewielkie naciski w kierunku osiowym
+ Stosunkowo duża głębokość skrawania w stosunku do rozmiaru płytki Wady – Niższa produktywność |
Zalety + Duża produktywność + Bardzo duży posuw + Osiowy kierunek działania całkowitej siły skrawania (sprzyjający stabilności wrzeciona) Wady – Mała głębokość skrawania |
||||||
Duża produktywność
Podstawowy wybór |
Uniwersalność
Produkcja mieszana |
Duża produktywność
Pozwala rozwiązać problemy |
Zasady stosowania
Skrawanie przerywane powierzchni nieciągłych metodą frezowania czołowego
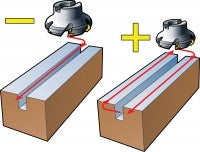
Unikać frezowania nieciągłych powierzchni
- Jeżeli możliwe, nie przeprowadzać ostrzy narzędzia nad przerwą w materiale przedmiotu (otworami lub rowkami). Tego rodzaju skrawanie przerywane bardzo mocno obciąża krawędzie skrawające narzędzia, gdyż powoduje wielokrotne zagłębianie ostrza w materiał i niekorzystne warunki wyprowadzania go z zazębienia
- Alternatywą jest zmniejszenie zalecanego posuwu o 50% nad obszarem przedmiotu obrabianego, w którym występują przerwania, aby przy wyjściu z materiału wióry pozostawały cienkie
Frezowanie czołowe cienkich, uginających się ścianek
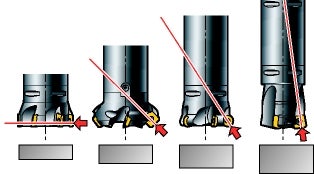
- Należy uwzględnić kierunek oddziaływania głównych składowych siły skrawania w odniesieniu do stabilności przedmiotu obrabianego i zamocowania
- Do frezowania przedmiotów o małej sztywności osiowej należy używać frezu walcowo-czołowego z kątem przystawienia 90°, gdyż siła przyjmuje tam kierunek bardziej promieniowy
- Alternatywnie można użyć frezu czołowego generującego mnimalne opory skrawania
- Unikać osiowych głębokości skrawania mniejszych niż 0.5–2 mm, aby ograniczyć osiową składową siły
- Używać frezu z podziałką rzadką, aby uzyskać możliwie najmniejszą liczbę krawędzi skrawających jednocześnie zazębionych z materiałem
- Używać ostrych, dodatnich krawędzi (-L), aby ograniczyć wartość siły skrawania
- Używać frezu z podziałką nierównomierną jako sposobu rozwiązywania problemów
Obróbka krawędzi cienkich detali za pomocą frezów do frezowania czołowego
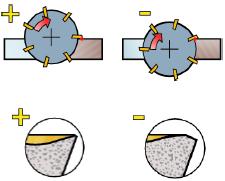
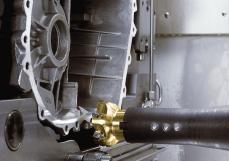
- W celu wykonania czynności frezowania czołowego na krawędziach cienkich detali droga narzędzia nie powinna pokrywać się z osią symetrii detaluW ten sposób przejście staje się bardziej płynne, a rozkład sił jest bardziej równomierny wzdłuż ścianki, co zmniejsza ryzyko wystąpienia drgań
- Wybrać podziałkę frezu, która sprawi, że zawsze zagłębione w materiale będą przynajmniej dwa ostrza
- Użyć geometrii płytki generującej najniższe opory skrawania (tj. geometrii lekkiej zamiast średniej lub średniej zamiast ciężkiej)
- Celem zmniejszenia ryzyka drgań w przedmiotach cienkościennych należy wybierać mniejszy promień płytki i krótszą pomocniczą krawędź skrawającą
- Użyć niższych parametrów skrawania, małej głębokości skrawania, ap, i małego posuwu na ostrze, fz
Uwagi i wskazówki
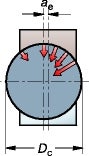

Zagłębianie głowicy w materiał po łuku
- Wziąć pod uwagę stabilność obrabiarki, wielkość i typ wrzeciona (pionowe lub poziome) oraz dostępną moc
- Użyć frezu o średnicy o 20-50% większej od szerokości przejścia
- Przy doborze optymalnego posuwu, uwzględnić parametr maksymalnej grubości wiórów
- Droga osi obrotu głowicy powinna znajdować się poza osią symetrii frezowanej powierzchni, aby uzyskać jak najcieńsze wióry na wyjściu krawędzi skrawającej z materiału
- Frezowanie współbieżne sprzyja tworzeniu wiórów o optymalnym kształcie (najcieńszych w punkcie wyjścia ostrza z materiału)
- Zastosowanie techniki wejścia po łuku lub zmniejszenie posuwu zapewni łagodne zazębienie ostrzy frezu w materiał
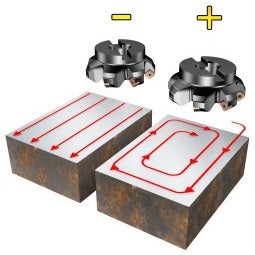
Frez powinien być bez przerwy zazębiony z materiałem przedmiotu obrabianego.
- Frezowanie współbieżne sprzyja tworzeniu wiórów o optymalnym kształcie (najcieńszych w punkcie wyjścia ostrza z materiału)
- Unikać wielokrotnego wychodzenia frezu z materiału i ponownego zagłębiania podczas cyklu obróbki
- Jeśli to możliwe, unikać częstego wchodzenia/wychodzenia narzędzia z materiału. Może ono powodować niekorzystne naprężenia na krawędzi skrawającej lub być przyczyną tendencji do zatrzymań obrotu głowicy i generowania zadrgań na powierzchni obrobionej. Zaleca się zaprogramowanie drogi narzędzia w taki sposób, aby frez utrzymywał pełny kontakt z przedmiotem zamiast wykonywać kilka równoległych przejść. Przy zmianie kierunku należy uwzględnić niewielką drogę narzędzia w kierunku promieniowym, aby podtrzymać ruch i stałe zagłębienie frezu
Frezowanie z wysokimi posuwami
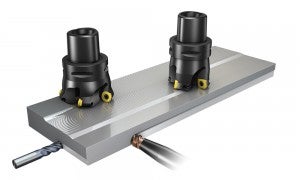
Na czym polega udane frezowanie z dużym posuwem? Podczas obróbki aluminium oraz niekiedy podczas obróbki żeliwa przy użyciu płytek z CBN lub płytek ceramicznych można użyć prędkości skrawania przekraczających 1000 m/min, czego skutkiem jest bardzo duża prędkość posuwu, vf. Ten rodzaj obróbki nosi nazwę obróbki z wysokimi prędkościami albo obróbki szybkościowej (High Speed Machining, HSM).
Podczas frezowania materiałów generujących krótkie wióry, takich jak żeliwo szare, można użyć frezu do frezowania czołowego z bardzo gęstą podziałką, czego skutkiem jest duża prędkość posuwu. Podczas obróbki materiałów z grupy superstopów żaroodpornych, przy której prędkość skrawania jest zazwyczaj mała, bardzo gęsta podziałka powoduje dużą prędkość posuwu.
Frezowanie czołowe z bardzo dużym posuwem na ostrze (do 4 mm/ostrze) jest możliwe przy zastosowaniu frezów o małych kątach przystawienia lub frezów na płytki okrągłe ze względu na powstające wówczas cienkie wióry. Choć osiowa głębokość skrawania jest ograniczona do mniej niż 2.8 mm, bardzo duży posuw czyni tę metodę frezowania wysoce produktywną. Specjalne rodzaje frezów są zoptymalizowane pod kątem frezowania z bardzo dużym posuwem przy niewielkich osiowych głębokościach skrawania. Mały kąt przystawienia jest warunkiem wstępnym wymaganym do zastosowania lekkiego, szybkiego i dużego posuwu.
Wybór narzędzi
Frezy do wysokich posuwów
Maks. głębokość skrawania (ap), mm | 1.2 - 2 |
Średnica frezu (Dc), mm | 25 - 160 |
Materiał | ![]() |
Frezy na płytki okrągłe
Maks. głębokość skrawania (ap), mm | 1.3 |
Średnica frezu (Dc), mm | 10 - 25 |
Materiał | ![]() |
Średni HF
Maks. głębokość skrawania (ap), mm | 1.3 | 10 | 7/8 | 2.8 |
Średnica frezu (Dc), mm | 4 - 20 | 25 - 160 | 10 - 42 / 25 - 125 | 63 - 160 |
Materiał | ![]() | ![]() | ![]() | ![]() |
Frezy do wysokich posuwów:
- Wydajne frezy czołowe do wysokich posuwów o kącie przystawienia 10°, umożliwiające bardzo duży posuw na ostrze, fz
- Duże posuwy przy małych głębokościach skrawania, ap
- Precyzyjne narzędzia zoptymalizowane pod kątem szybkiej obróbki stali hartowanej
- Obróbka zgrubna i półwykończeniowa konturów i asymetrycznych konfiguracji przy bardzo dużych prędkościach posuwu
Uwaga: W przypadku frezów na płytki okrągłe i o dużym promieniu wartość ap powinna pozostawać znacznie niższa od zalecanej wartości maksymalnej, aby możliwe było frezowanie z dużym posuwem
Frezy na płytki okrągłe:
- Wzmocnienie efektu tworzenia cienkich wiórów przy ograniczonym skrawaniu w kierunku promieniowym
- Stabilny przebieg obróbki
- Frezy ogólnego przeznaczenia do stosowania w ciężkich lub lekkich warunkach
Zasady stosowania
Frezy z małym kątem przystawienia
Frezy z bardzo małym kątem przystawienia umożliwiają znaczne zwiększenie posuwu, fz, spowodowane przez efekt tworzenia cienkich wiórów, gdy wartość ap jest niewielka.
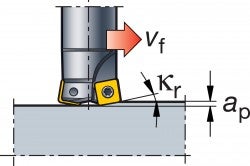
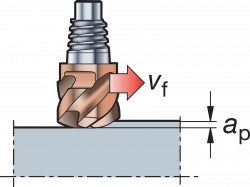
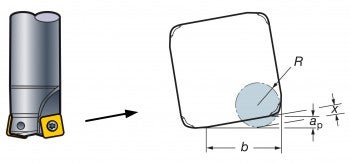
IC | Wymiary, mm | Materiał nieobrabiany | ||
IC | R | b | ap | X |
9 | 2.5 | 7.05 | 1.2 | 0.79 |
14 | 3.5 | 12.0 | 2.0 | 1.48 |
Niewielki kąt przystawienia powoduje znaczne zmniejszenie maksymalnej grubości wióra. Umożliwia to korzystanie z bardzo dużych prędkości posuwu bez przeciążania płytek.
Uwaga: Unikać obróbki do ścianek ustawionych pod kątem 90°, ponieważ pozytywny wpływ niskiego kąta przyłożenia zostanie utracony, gdyż osiowa głębokość skrawania radykalnie wzrośnie.
Jak zawsze posuw należy zmniejszyć i dostosować w zależności od konkretnych warunków oraz w celu uniknięcia drgań, które mogą uszkodzić płytki.
Frezy na płytki okrągłe
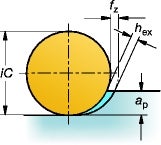
Przy użyciu płytek okrągłych grubość wióra, hex, zmienia się i zależy od głębokości skrawania, ap. Przy korzystaniu z technologii frezowania z wysokimi posuwami z zastosowaniem frezu na płytki okrągłe należy utrzymywać niską głębokość skrawania (maks. 10% średnicy płytki, iC, gdyż w przeciwnym wypadku nastąpi osłabienie efektu tworzenia cienkich wiórów i trzeba będzie zmniejszyć posuw, patrz ilustracja).
Uwaga: Unikać obróbki do ścianek ustawionych pod kątem 90°, ponieważ pozytywny wpływ niskiego kąta przyłożenia zostanie utracony, gdyż osiowa głębokość skrawania radykalnie wzrośnie.
Udarne płytki do ogólnej obróbki zgrubnej
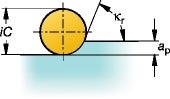
W przypadku płytek okrągłych obciążenia powstające przy formowaniu wiórów i kąt przystawienia zmieniają się wraz z głębokością skrawania. Najlepsze efekty uzyskuje się, gdy głębokość skrawania jest mniejsza niż 25% średnicy płytki, iC.
Ciężkie frezowanie czołowe
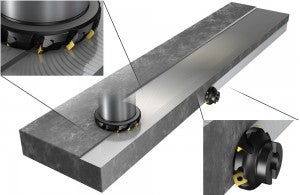
Na czym polega udane ciężkie frezowanie czołowe?
Ciężkie frezowanie czołowe obejmuje frezowanie zgrubne przygotówek walcowanych i kutych, odlewów i konstrukcji spawanych w dużych frezarkach bramowych i frezarkach lub centrach obróbkowych o dużej mocy. Konieczne jest przy tym usunięcie dużych ilości materiału, co powoduje powstawanie dużych temperatur i znacznych oporów skrawania, stawiających specyficzne wymagania przed płytkami frezarskimi:
- Znaczne obciążenia głównej krawędzi skrawającej przy pełnej głębokości skrawania
- Starcie naroży przez ścierny naskórek, kiery głębokość skrawania zbliża się do zera
Kąt przystawienia 60º jest optymalny dla frezu przeznaczonego do frezowania w trudnych warunkach. Konstrukcja ta zapewnia:
- Zdolność osiągania dobrej głębokości skrawania, stosunkowo równomierny rozkład siły skrawania oraz efekt tworzenia cienkich wiórów, co umożliwia pracę z wysokim posuwem
- Osiowe wyluzowanie konstrukcji umożliwia stosowanie płytki o długiej pomocniczej krawędzi skrawającej, co sprzyja odpowiedniemu wykończeniu powierzchni.
Wybór narzędzi
Frezy do ciężkiej obróbki
Kąt przystawienia (κr), mm | 60° | 45° | 90° | Płytki okrągłe |
Maks. głębokość skrawania (ap), mm | 13/18 | 10 | 15.7 | 12.5 |
Średnica frezu (Dc), mm | 160 - 500 | 80 - 250 | 40 - 200 | 66 - 200 |
Materiał | ![]() | ![]() | ![]() | ![]() |
Frezy do ciężkiej obróbki z kątem przystawienia 60°
- Zaprojektowane tak, by umożliwiać wydajną obsługę narzędzi, co skutkuje skróceniem przestojów oraz bezpieczną i szybką wymianą płytek w obrabiarce
- Zdolność frezowania z osiową głębokością skrawania do 18 mm, umożliwiająca wydajne skrawanie metalu oraz obróbkę nierównych i pofalowanych powierzchni
- Duża produktywność – posuwy wynoszące 0.4 – 0.7 mm na ostrze
- Duża pomocnicza krawędź skrawająca, dzięki której obróbka półwykończeniowa daje dobre rezultaty
- Wytrzymałe naroże płytki, odporne na wpływ ściernego naskórka przy niewielkiej głębokości skrawania
- Udarność frezu, zapewniająca bezpieczeństwo podczas wymagających przejść
Frezy do średnio ciężkiej obróbki z kątem przystawienia 45-90°
- Frez czołowy do średnio ciężkiej obróbki z możliwie niskimi oporami skrawania
- Zdolność do pracy z głębokością skrawania 6 – 8 mm przy posuwach z zakresu 0.2 – 0.6 mm
- Do stosowania w ciężkich warunkach w dużych centrach obróbkowych
- Możliwość stosowania razem z płytkami wiper dla uzyskania bardziej gładkich powierzchni
- Pierwszy wybór do frezowania w średnio ciężkich warunkach i frezowania walcowo-czołowego
Duże frezy z płytkami okrągłymi
- Frez do średnio ciężkiej obróbki, z udarnymi krawędziami do pracy w trudnych warunkach, takich jak frezowanie w zgorzelinach i przerwaniach. Okrągła geometria płytki zapewnia płynny przebieg skrawania
- W sprzyjających warunkach można używać ośmiu odcinków krawędzi skrawającej płytki
- Maksymalna głębokość skrawania wynosi 10 mm. Maksymalna zalecana grubość wióra waha się znacznie do maksymalnie 0.55 mm na ostrze, w zależności od geometrii płytki i głębokości skrawania
Zasady stosowania
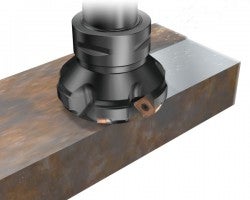
Do pracy w trudnych warunkach używa się frezów z dużymi płytkami o dużej średnicy. Frezy te cechuje normalna prędkość skrawania, ale wysokie wartości parametrów ap i fz, w połączeniu z dużą wartością ae, czynią je bardzo produktywnymi.
Wejście w materiał
Ze względu na trudne warunki występujące zazwyczaj podczas ciężkiego frezowania wejście w materiał obrabiany podczas przejścia ma często decydujące znaczenie.
- Jeśli to możliwe, należy zaprogramować drogę narzędzia na prowadzenie po łuku, a nie prostoliniowe
- Jeśli nie jest to możliwe, należy zmniejszyć posuw do momentu całkowitego zagłębienia frezu
Położenie i rozmiar frezu
Podczas frezowania w trudnych warunkach, gdy trzeba wykonać kilka przejść w celu obróbki dużej powierzchni, ważne jest przestrzeganie zaleceń dotyczących:
- Położenia i zagłębienia frezu
- Rozmiaru frezu w odniesieniu do możliwości technicznych obrabiarki
- Drogi narzędzia, w celu uniknięcia niekorzystnych warunków wychodzenia ostrzy z materiału
Należy zwracać uwagę na wysokie temperatury
Frezowanie w wymagających, ciężkich warunkach powoduje powstawanie wysokich temperatur. Jeśli do zamocowania przedmiotu używane są stoły magnetyczne, znaczne ilości wytwarzanych wiórów mogą często gromadzić się dookoła frezu. Powoduje to przerywane lub niekompletne odprowadzanie wiórów oraz ich ponowne skrawanie, co jest zagrożeniem dla trwałości narzędzia. Aby tego uniknąć, należy utrzymywać obszar roboczy w stanie wolnym od wiórów. Należy chronić podatne na ścieranie naroża płytek przed tarciem o ścierny naskórek i zgorzelinę poprzez zwiększanie głębokości skrawania w celu przesunięcia punktu styku z powierzchnią bliżej bardziej udarnej głównej krawędzi skrawającej płytki.
Uwaga: Podczas zakładania płytek wymiennych na frez należy używać rękawic, aby uniknąć obrażeń spowodowanych przez wysokie temperatury.
Obróbka wykończeniowa przy użyciu płytek wiper
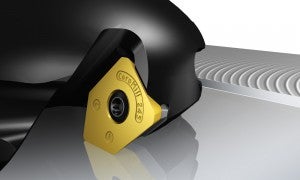
Jak osiągnąć dobrą jakość powierzchni podczas frezowania czołowego
Poprzez zastosowanie jednej lub kilku płytek wiper na głowicy frezarskiej można uzyskać bardzo gładką powierzchnię obrobioną. Płytki wiper sprawdzają się najlepiej przy dużym posuwie na obrót, fn, i frezach o większych średnicach z bardzo gęstą podziałką i możliwością regulacji.
Posuw na obrót można zwiększyć mniej więcej czterokrotnie, utrzymując zarazem dobrą chropowatość powierzchni. Płytek wiper można używać do frezowania czołowego większości materiałów, aby osiągnąć dobre faktury powierzchni – nawet w niesprzyjających warunkach.
Wybór narzędzi
Frezy
Kąt przystawienia (Kr), mm | 45° | 45° | 65° | 90° | 25° | 90° |
Maks. głębokość skrawania (ap), mm | 6 | 10 | 6 | 10 | 0.9 | 8.1 |
Średnica frezu (Dc), mm | 40 - 250 | 32 - 250 | 40 - 250 | 40 - 200 | 80 - 250 | 125 - 500 |
Chropowatość powierzchni (Ra) | < 1.0 | < 1.0 | < 1.0 | < 1.0 | < 1.0 | < 1.0 |
Materiał | ![]() | ![]() | ![]() | ![]() | ![]() | ![]() |
Dostępne są płytki z krawędziami wiper o różnej długości (Bs), często w wersji prawo- i lewostronnej każdej płytki. Dostępne są gatunki dla większości materiałów przedmiotów obrabianych. Regulacja gniazd płytek jest często dostępna w przypadku konkretnych gniazd płytek, jeśli konstrukcja frezu powstała specjalnie z myślą o obróbce wykończeniowej lub oferuje rozwiązania z użyciem kaset.
Zasady stosowania
Podczas obróbki wykończeniowej z użyciem dużego frezu do frezowania czołowego należy zazwyczaj utrzymywać niewielką wartość posuwu, fz. Jednak w przypadku stosowania frezu na płytki wiper posuw można zwiększyć dwu- lub trzykrotnie bez pogorszenia chropowatości powierzchni.
Wykończenie na tzw. lustrzany połysk przy dużych posuwach
Chropowatość powierzchni | ||
![]() |
Posuw fn | |
fn1 <= 0.8 * bs1 | fn2 <= 0.6 * bs2 |
A : Tylko płytki standardowe
B : Z jedną płytką wiper
C : fn = posuw/obrót
bs1 | bs2 | |
![]() |
- Jeśli wartość fn przekracza 80% długości krawędzi pomocniczej, Bs, dla płytek standardowych, krawędź wiper umożliwi uzyskanie lepszej chropowatości powierzchni
- W przypadku stosowania frezu o dużej średnicy z dużą liczbą płytek zastosowanie płytek wiper w celu utrzymania chropowatości powierzchni staje się konieczne wraz ze wzrostem posuwu na obrót, fn
- Bicie osiowe frezu, które zależy od nachylenia wrzeciona, rozmiaru frezu, jego mocowania i dokładności regulacji, wpływa na pofalowanie obrabianej powierzchni. Wystająca krawędź wiper skompensuje efekt bicia i umożliwi uzyskanie powierzchni wolnej od resztek materiału po przejściach. Zapewni to posuw na obrót wynoszący 60% szerokości krawędzi wiper
- Krawędź wiper wystaje poniżej płytek frezarskich na około 0.05 mm po zamocowaniu na frezach z gniazdami płytek zintegrowanymi z korpusem, tzw. stałymi gniazdami płytek. W przypadku frezów o konstrukcji kasetowej często możliwe jest precyzyjne ustawienie krawędzi wiper w tym położeniu. Taka pozycja naraża płytki wiper na większe obciążenia niż w przypadku płytek tradycyjnych, co może powodować drgania. Dlatego płytek wiper należy używać do lekkiej obróbki przy umiarkowanych głębokościach skrawania i niewielkich partiach
- Należy utrzymywać niewielką głębokość skrawania w celu ograniczenia wartości składowej siły w kierunku osiowym i ryzyka wystąpienia drgań. Podczas obróbki wykończeniowej zalecana osiowa głębokość skrawania wynosi 0.5 – 1.0 mm
- Podczas mocowania płytki wiper należy postępować ze szczególną starannością, aby prawidłowo ustawić jej długą krawędź
Przykład:
- Szerokość krawędzi pomocniczej, Bs, na płytce wynosi 1.5 mm
- We frezie znajduje się 10 płytek, a posuw na ostrze, fz, wynosi 0.3 mm. Dlatego posuw na obrót, fn, wyniesie 3 mm (podwojona długość krawędzi pomocniczej)
- Aby zapewnić dobrą chropowatość powierzchni, posuw na obrót powinien wynosić maksymalnie 80% z 1.5 mm = 1.2 mm
- Odpowiednia płytka wiper będzie mieć krawędź pomocniczą o szerokości około 8 mm
- Wynik: Posuw na obrót można zwiększyć z 1.2 mm na 60% z 8 mm = 4.8 mm
Uwaga: Należy uwzględnić także inne ograniczenia, np. moc obrabiarki.
Uwagi i wskazówki
Wskazówki umożliwiające osiągnięcie tzw. „wykończenia na lustrzany połysk”:
- Zastosować dużą prędkość skrawania lub płytki cermetalowe, aby uzyskać błyszczącą powierzchnię
- Zastosować ciecz obróbkową lub rozpylony olej do obróbki przywierających do ostrzy materiałów z grup ISO M i S
- Stosowanie płytek z pokryciem PVD z ostrymi krawędziami i wartością ap wynoszącą 0.5 – 0.8 mm daje najlepszą gładkość powierzchni
- Należy dążyć do stosowania płytki wiper w tym samym gatunku co płytki robocze