Milling tool maintenance
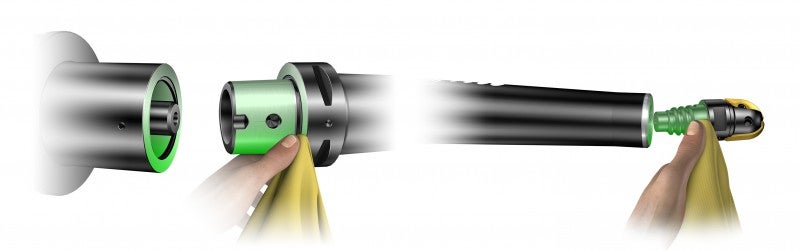
Establishing a routine for tool maintenance in the workshop will improve tool life in milling, prevent problems and save money.
Check the insert seats
Check the insert seats regularly to ensure that they have not been damaged during machining or handling. Make sure that the insert seats are free from dirt or metal chips from machining.
Replace worn or damaged screws and washers. Use a torque wrench to ensure correct screw-tightening.
To get the best performance, we recommend cleaning all connecting parts and lubricating them with oil at least once a year. Lubricant should be applied, when needed, to the screw thread as well as the screw head face.
Torque wrench
To get the best performance out of the milling tools, a torque wrench should be used to correctly tighten the insert. Use the recommended torque for each tool holder.
A torque that is too high will affect the performance of the tool negatively and cause insert, washer and screw breakage.
A torque that is too low will cause slide or insert movement, vibrations and degradation of the cutting result.
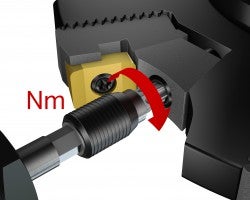
Tubing hanger
A tubing hanger is a component used in the completion of oil and gas production wells.... chevron_right
CoroMill® 245
Milling cutters for high metal removal and mirror finish. The cutter is designed... chevron_right
Metal Cutting Technology Class
Format : In-person training Overview : Having the right tooling strategy significantly... chevron_right
Metal cutting e-learning - metal working courses
Competence in metal cutting is in short supply worldwide, and demand is growing for... chevron_right