Entering angle and chip thickness in milling
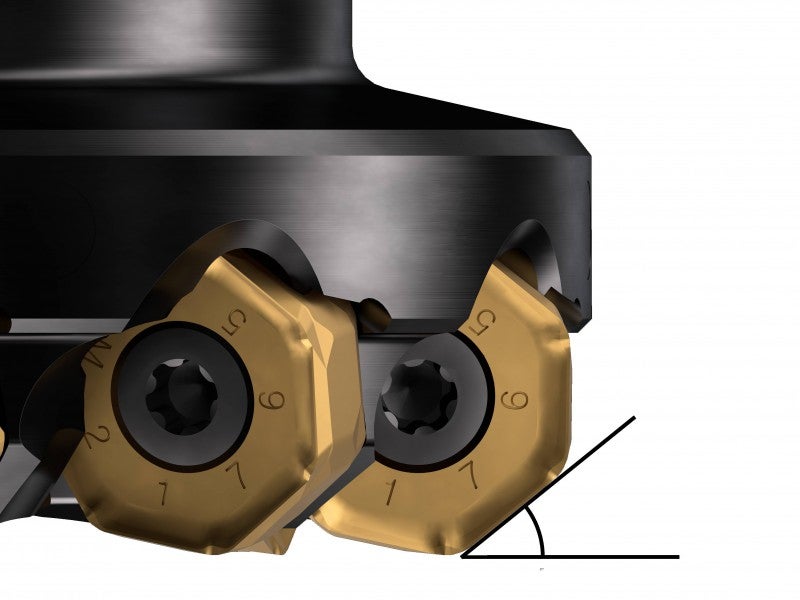
The entering angle (KAPR) is the angle between the main, leading cutting edge of the insert and the workpiece surface. The entering angle affects chip thickness, cutting forces and tool life.
The most common entering angles are 90 degrees, 45 degrees, 10 degrees and those of round inserts.
When decreasing the entering angle, the chip thickness, hex, reduces for a given feed rate, fz. This chip thinning effect spreads the amount of material over a larger part of the cutting edge.
Smaller entering angles also provide a more gradual entry into the cut, reducing radial pressure and protecting the cutting edge. However, the higher axial forces increase the pressure on the workpiece.
Milling with a 90-degree entering angle
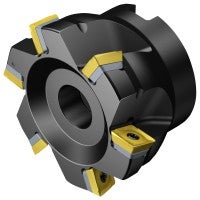
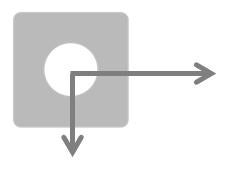
The main application area for a 90-degree cutter is square shoulder milling.
A 90-degree cutter generates mostly radial forces, in the direction of the feed. This means that the surface being machined will not be exposed to high axial pressure, which is advantageous for milling workpieces with a weak structure or thin walls, and in cases of unstable fixture.
Milling with a 45-degree entering angle
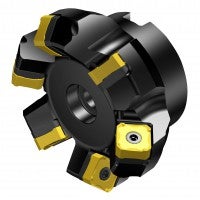
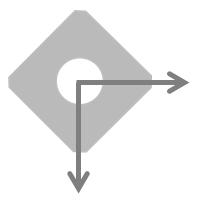
A 45-degree cutter is the general purpose choice for face milling. It generates well-balanced radial and axial cutting forces, which is less demanding on the machine power.
This type of cutter is especially suitable for milling in short-chipping materials that easily fritter if excessive radial forces act on the gradually reduced amount of material left at the end of a cut.
The smooth entry into cut limits vibration tendencies when milling with long overhangs or with smaller/weaker tool holders and couplings.
The formation of a thinner chip allows for high productivity in many applications because of the opportunity for higher table feed while maintaining a moderate cutting edge load.
Milling with 60–75 degree entering angles
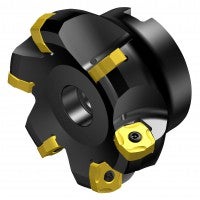
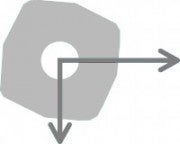
These type of cutters are special-purpose face mills, offering greater depth of cut compared to general choice face mills. The axial forces are lower compared to a 45-degree face mill cutter and the edge strength is better compared to a 90-degree cutter.
Milling with a 10-degree entering angle
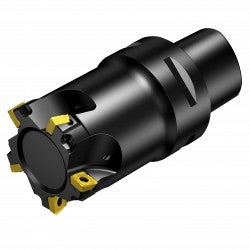
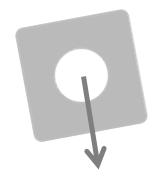
A 10-degree entering angle is used on high-feed and plunge milling cutters. A thin chip is generated that allows for very high feeds per tooth, fz, at small depths of cut and, consequently, extreme table feeds, vf.
The dominating axial cutting force is directed towards the spindle, which stabilizes it. This is favorable for long and weak set-ups, as it limits vibration tendencies.
This type of cutter is effective in hole making when using three axes and for plunge milling of cavities, or whenever the use of an extended cutter is required.
Milling with round inserts or cutters with a large corner radius
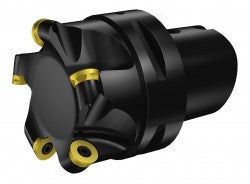
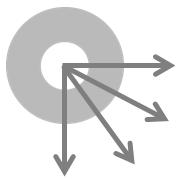
A round insert cutter is for general-purpose milling and is efficient for roughing operations.
The corner radius provides a very strong cutting edge, suitable for high table feed rates because of the thinner chips generated along the long cutting edge. The chip-thinning effect makes these cutters suitable for machining titanium and heat resistant alloys.
Depending on the cutting depth variation, ap, the entering angle changes from zero to up to 90 degrees, altering the cutting force direction along the edge radius, and consequently the resulting pressure during the milling operation as well.
Maximum chip thickness in milling
Maximum chip thickness is the most important parameter for achieving a productive and reliable milling process. Effective cutting will only take place when the hex value is correctly matched to the milling cutter in use.
- A thin chip with an hex value that is too low is the most common cause of poor performance resulting in low productivity. This can negatively affect tool life and chip formation
- An hex value that is too high will overload the cutting edge, which can lead to breakage
Chip thinning allows for increased feed
Feed per tooth can be increased in the three following situations due to the chip thinning effect:
- Using straight edge cutters with entering angles lower than 90°.
- Using round inserts or large radius inserts at smaller depths of cut, ap.
- Peripheral milling at a small radial engagement, ae/De.
Chip thickness calculations for straight edge insert
With 90-degree cutters, the feed per tooth equals the maximum chip thickness (fz=hex). When decreasing the entering angle, increase feed per tooth to make sure to keep the same chip thickness.
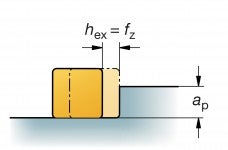
KAPR = 90°
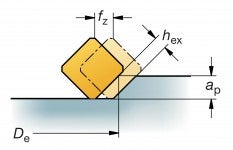
KAPR = 45°
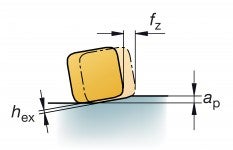
KAPR = 10°
Example:
If maximum hex = 0.1 mm and KAPR = 45°
Recommended feed, fz = 1.4 x 0.1 = 0.14 mm/tooth
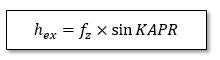
Entering angle, KAPR | Modification factor | fz (mm/tooth) | fz (mm/tooth) | fz (mm/tooth) |
hex (mm) | hex (mm) | hex (mm) | ||
min. 0.1 | start 0.15 | max. 0.2 | ||
90° | 1.0 | 0.10 | 0.15 | 0.20 |
75° | 1.0 | 0.10 | 0.16 | 0.21 |
65° | 1.1 | 0.11 | 0.17 | 0.22 |
45° | 1.4 | 0.14 | 0.21 | 0.28 |
10° | 5.8 | 0.58 | 0.86 | 1.15 |
Watch how much you can increase feed per tooth on the high-feed, 10-degree cutter. This is because you are thinning the chip out by a factor of almost six times.
Chip thickness calculations for round and radius insert cutters
The chip thickness, hex, varies with round inserts and depends on the entering angle. With low ap/i C ratios, the feed can be increased considerably in order to raise the chip thickness to a desired level.
Best performance is achieved when the entering angle remains under 60 degrees and with a depth of cut that not exceeds 25% x insert diameter. For greater depths of cuts, it is more beneficial to use a 45-degree square insert.
Round inserts have a higher maximum chip thickness capability than straight edge solutions, due to the stronger insert shape and longer cutting length.
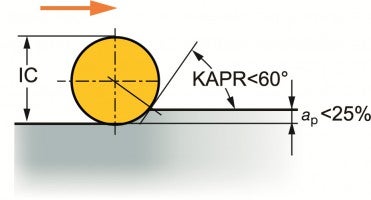
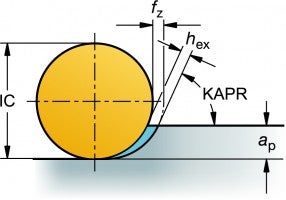
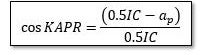
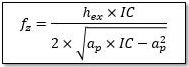
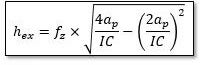
Round inserts are unique, in that the chip thickness changes based on the depth of cut. Therefore, at lower depths of cut you need to increase your feed to be sure to obtain the proper chip thickness.
Chip thickness calculations for peripheral milling
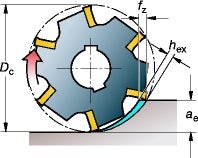
The hex value varies depending on the cutter diameter and working engagement, the radial immersion of a cutter, ae/DC. When this is smaller than 50%, maximum chip thickness is reduced relative to fz.
Feed can be increased by the modification value in the table below, depending on the ratio, ae/DC.
Example:
DC 20 mm – ae = 2 mm, ae/DC = 10%
hex = 0.1 mm, fz = 0.17 mm/tooth
Width of cut diameter ratio, ae/DC | Modification factor | fz (mm/tooth): | fz (mm/tooth): | fz (mm/tooth): |
hex (mm) | hex (mm) | hex (mm) | ||
min. 0.1 | start 0.15 | max. 0.2 | ||
50-100% | 1.0 | 0.10 | 0.15 | 0.20 |
25% | 1.16 | 0.12 | 0.17 | 0.23 |
20% | 1.25 | 0.13 | 0.19 | 0.25 |
15% | 1.4 | 0.14 | 0.21 | 0.28 |
10% | 1.66 | 0.17 | 0.25 | 0.33 |
5% | 2.3 | 0.23 | 0.34 | 0.46 |
External turning
External turning operations machines the outer diameter of the workpiece. Since external... chevron_right
Face milling
Face milling operations include: General face milling High-feed milling Heavy-duty... chevron_right
Milling
Find the cutting tool for your specific task and get instant cutting data recommendations. Go... chevron_right
Milling
Product overview There is a wide range of Silent Tools milling adaptors available... chevron_right