Solutions for cost-effective and high-quality machining of oil and gas tubing hanger features
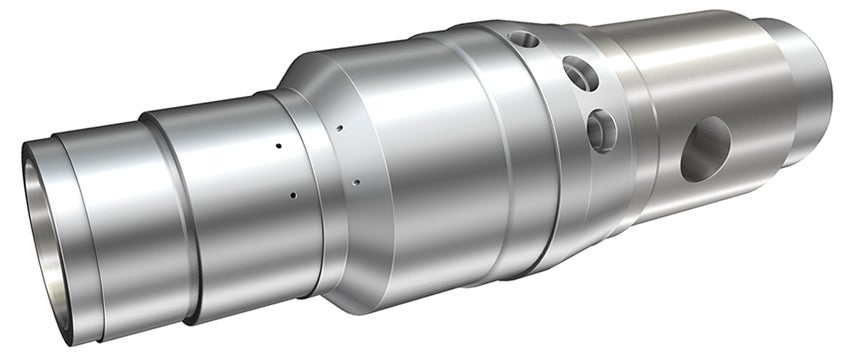
A tubing hanger is a component used in the completion of oil and gas production wells. It is attached to the topmost tubing joint in the wellhead to support the tubing string.
The tubing hanger is typically located in the tubing head, with both components incorporating a sealing system to ensure that the tubing conduit and annulus are hydraulically isolated.
Facts and component characteristics
Material:
- Steel AISO/SAE 4130
- Inconel 625 cladding
- Solid Inconel 718
Key component features:
- External and internal turning
- External turn milling
- Roughing cross hole
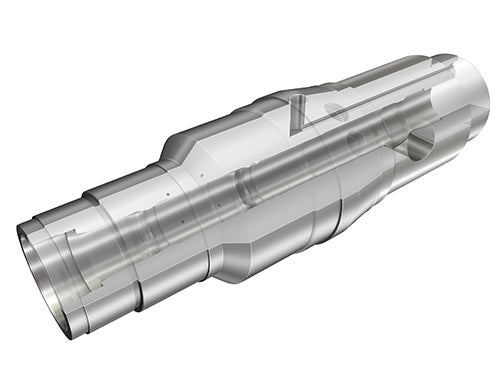
Tooling solutions for machining of oil and gas – tubing hanger features
PrimeTurning™ – all-directional turning with extraordinary productivity for internal and external turning applications
With the CoroTurn® Prime SL head solution, it is now possible to use our PrimeTurning™ methodology for internal turning. The inside-out machining capability allows for excellent chip evacuation and chip control.
Read more about PrimeTurning™
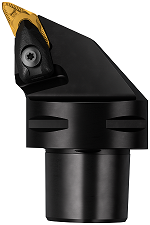
Silent Tools™ – overcome vibration when machining long overhangs
To keep chips flying at a high rate, it is important to reduce vibration as much as possible. Silent Tools™ dampened boring bars minimize vibration. This enables a high rate of metal removal.
Read more about Silent Tools™
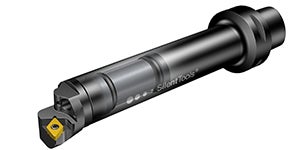
CoroTurn® SL adapter interface
CoroTurn® SL is a modular system of adapters and cutting heads that allows you to build customized tools for a variety of turning applications with a minimum number of items. The robust coupling and many combination possibilities make it ideal for building a tool for machining complex components.
Read more about CoroTurn® SL
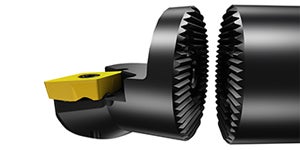
T-Max® P – productive external turning of medium to large components
This is your first choice for general turning, ranging from medium to large components.
Read more about T-Max® P
Top-priority inserts
Insert: CNMG 1125 and 1115
Insert: CNMG 2025
Insert: DNMG 1125 and 1115
Insert: SNMG 4235
Insert: RNGN 6060
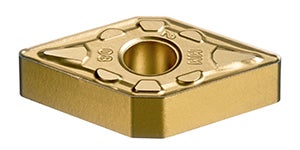
CoroMill® MH20
High-feed milling cutter optimized for:
- Open and closed pocket milling
- Full slotting and hole making with helical ramping cycles
- Long overhang cavity milling
- Low engagement shoulder milling
- Multi-task turn milling
Read more about CoroMill® MH20
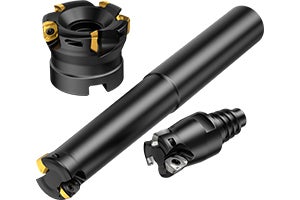
CoroMill® 300 – light-cutting face and profile milling cutters
This is a round insert cutter for a broad range of operations such as face milling, pocketing and profiling.
CoroMill® 300
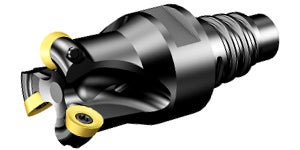
CoroBore® BR30
Three-edge rough boring tools for maximum productivity. Very productive multi-edge tool, available with three to eight cutting edges for maximum metal removal rates.
CoroBore® BR30
CoroBore® 111 insert assortment
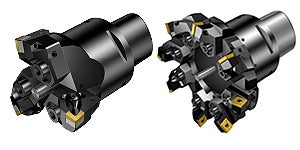
Rough boring tools
Roughing is primarily focused on metal removal and is performed to open up an existing hole made by methods such as pre-machining, casting or forging. Rough boring prepares the hole for finishing.
Click here to see our rough boring tools
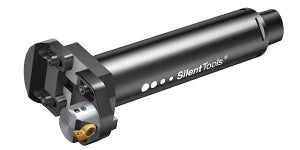
Coromant Capto® is a modular quick-change tooling concept offering three systems in one. Benefits of Coromant Capto®:
- Flexibility with extensive modularity
- High basic stability and accuracy
- Minimized tool inventory
- Reduced setup time
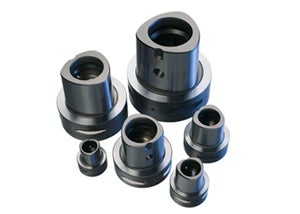
Coromant Capto® Plus – Predictive maintenance
With Coromant Capto® Plus you can predict the maintenance needs of your driven tool holder and plan accordingly.
Coromant Capto® Plus
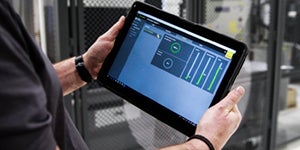
CoroCut® 1-2 – versatile parting and grooving
With more than 700 standard inserts, CoroCut® 1-2 covers all parting and grooving applications in most materials, from standardized grooves to parting off and profiling in heat-resistant super alloys.
CoroCut® 1-2
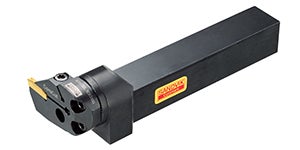
Customer values using tools from Sandvik Coromant
Our tooling solutions offer opportunities to achieve high total productivity in two ways: metal cutting efficiency and machine utilization. Below are some key benefits our tools can offer:
- Increased productivity and tool life
- Secure and predictable processes
- Vibration-free machining with Silent Tools™
- Good chip control thanks to cutting heads with high-precision nozzle technology
- Short tool-change time with quick-change clamping units
- Good reach and accessibility
- Component quality – great surface finish and close tolerances