Solutions for cost effective and high-quality machining of aerospace turbine discs
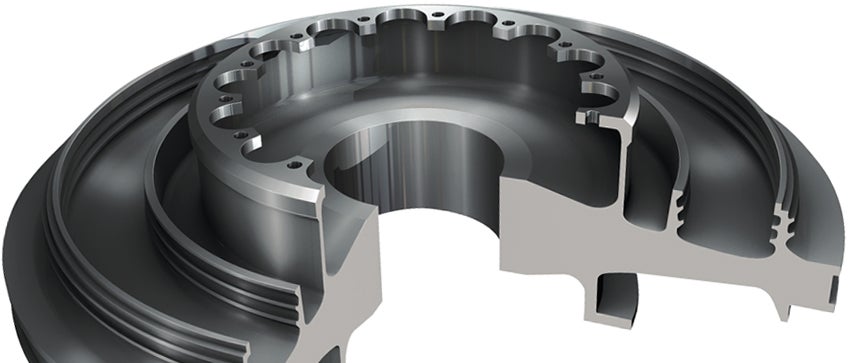
Aerospace turbines must withstand extreme temperatures and pressure differences. They are therefore made of advanced material, such as nickel based super alloys (e.g. Inconel 718, Waspalloy and Udimet 720).
Nickel based super alloys are excellent for their high temperature and stress resistance properties. It is important to apply best practice strategies as these materials are demanding to machine.
Tooling solutions for aerospace turbine discs
Grades optimized for turning of aged nickel-based HRSA
Turning grades GC1205 and GC1210 provide secure and reliable machining with excellent flank and notch wear resistance. A combination of a hard substrate and PVD coating allows for a significant increase in cutting speed (GC1205) and tool life (GC1210).
- GC1205: Finishing grade for machined surfaces. For last stage machining and intermediate stage machining applications
- GC1210: Mainly used in intermediate stage machining applications. Complements GC1205 when more toughness is required
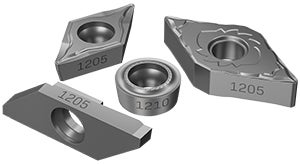
CoroCut® angled inserts
Designed specifically for reaching difficult to access grooves and pockets in complex components.
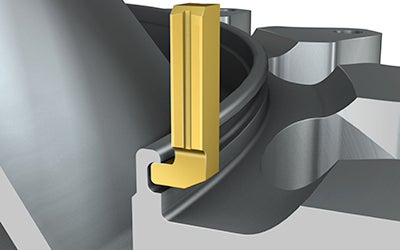
Ceramic turning
Ceramic grades CC6220 and CC6230 are designed specifically for the challenges of new HRSA materials where whisker ceramics and SiAlONs fall short, capable of higher cutting speeds, contributing to reduced cost per component. For high metal removal rates in pocketing and profiling applications, choose grade CC6160. For more demanding HRSA surfaces, choose the tougher grade CC6165.
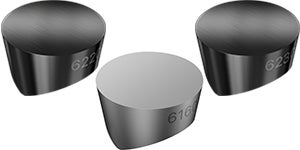
The modular SL70 tooling system for seal fin turning
Due to tough material, accessibility and productivity, round inserts offer the best method and are used in both roughing and finishing.
- CoroTurn SL70 blades are designed to fit the typical profiling and pocketing features
- The oval coupling offers excellent stability and accessibility
- All radial and axial clearance requirements are covered in a compact program
- Multi-task and vertical turning lathe requirements are met with Coromant Capto size C5, C6 and C8
- Carbide RCMT and CoroCut grades have high pressure coolant as standard
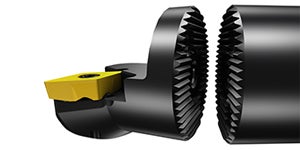
Finishing profile with SL70 CoroCut HP S205
For the highest productive finishing with excellent surface integrity and dimensional accuracy, the combination of S205 and CoroCut® RO geometry sets the standard for critical part finishing.
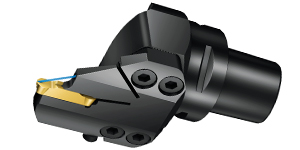
Scallop milling solutions
There are two powerful tools available for this challenging feature and chamfering solutions and inserts are available for both product families.
Use exchangeable-head system with CoroMill® 316 for stable roughing of the scallop feature.
The CoroMill® Plura High Feed Side (HFS) milling concept, combined with a dedicated machining strategy is an efficient solution for increased tool life and to avoid burr formation.
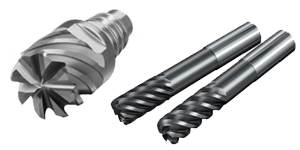
Highly secure drilling with CoroDrill® 860
CoroDrill® 860 with -SD geometry is a short-hole drilling solution optimized for machining nickel-based ISO S materials. This drill offers consistent and predictable tool life with high dimensional accuracy and excellent hole quality.
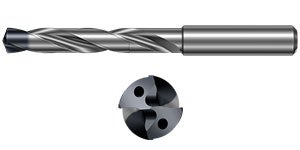
CB7014 high speed CBN turning solution for nickel-based alloys
Finish turning of aerospace components are challenging operations performed in demanding ISO S materials. Using CBN inserts allows for increased cutting speed and improved productivity while maintaining good surface integrity on the component. CBN inserts optimized for high speed finishing of nickel-based heat resistant super alloys are now available as a stocked standard solution.