Solutions for cost effective and high-quality machining of aerospace pylon brackets
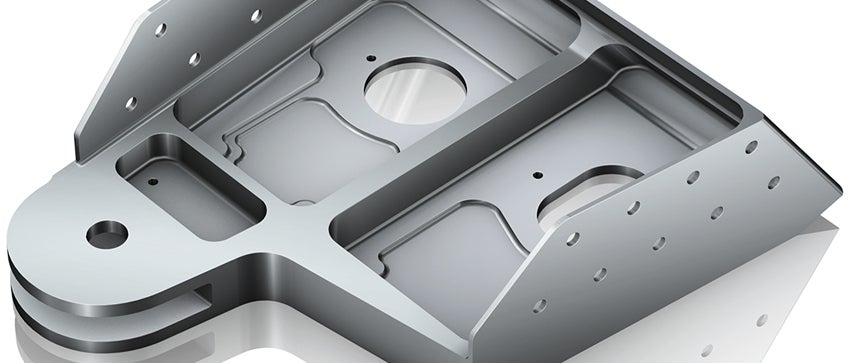
The pylon brackets found on the wing of the aircraft can be of open and closed design. The main challenge for the closed components is the closed angle and the deep slots.
Tooling solutions for aerospace Pylon bracket
CoroMill® MS20 – pocketing
- M-M20 geometry gives higher security in tougher applications
- In case of sensitive / vibration prone applications and / or applications requiring a sharper cutting edge, the E-L50 geometry can be used
- The higher edge line toughness of these geometries allows the inserts to be used with higher productivity (high cutting data) in stable operations
- Robust steel shank design ensures better stability and less deflection. The improved tool body material can withstand chip rubbing better
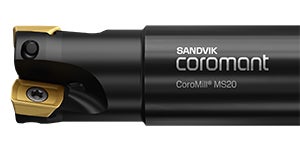
CoroMill® 316 - exchangeable-head milling system
The CoroMill® 316 end mill with the exchangeable-head milling system. It is designed to work throughout a diameter range of 10-25 mm.
Better levels of productivity, versatility, inventory, quality and tool costs are the main advantages that can be achieved with CoroMill® 316. The concept provides high strength for roughing operations and high rigidity for finishing operations. Available with solid carbide shank for long-overhang milling features.
Read more about CoroMill® 316
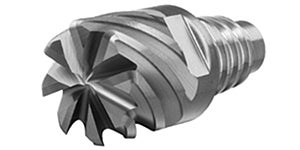
Slotting solution
When the slot is deep and narrow, side and face cutters provide the best stability and productivity. The cutters can be built into a gang to machine more than one surface in the same plane at the same time.
CoroMill® 331 with internal coolant, dedicated light-cutting geometries for ISO S and with S30T and S40T is an optimized solution with adjustable cartridges.
Read more about CoroMill® 331
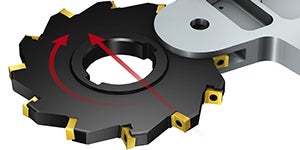
Roughing and finishing 3D pockets with closed angles
Closed angles; less than 90 degrees, are a common component feature in pockets and cavities. Depending on the stability of machine set-up, the slicing method using CoroMill® Plura ball nose end mill is the best choice.
A machine with 4 or 5 axes is needed to machine a closed angle. 4 axes: If only one side of the pockets has a closed angle and the bottom shape is flat. 5 axes: if there is a corner with closed angles on both sides and a radius at the bottom profile.
The conical ball nose end mills give the choice for high quality surface finish.
Application knowledge – closed pockets or angles
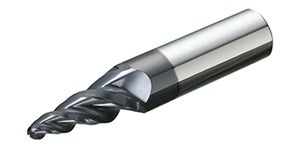
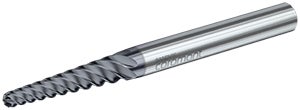
CoroChuck™ 930
Thanks to its excellent clamping performance this chuck offers the best pull-out security on the market, for excellent stability and accessibility in milling and drilling operations. A solution that doesn’t just helps increase machining safety and precision, but also increases production efficiency through quick and easy tool set-ups and changes. For 100% pull-out prevention, a collet with mechanical locking interface is available for Weldon shanks.
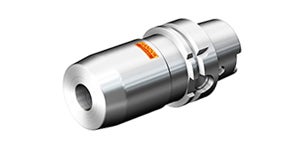