Solutions for cost effective and high-quality machining of aerospace engine mount in titanium
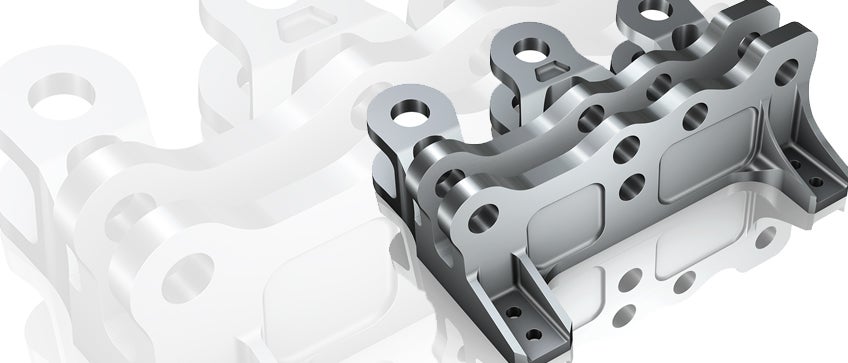
The most difficult feature on these engine mounts is the deep slot in the centre. Depending on the conditions, different methods can be used.
Tooling solutions for aerospace engine mounts
test
CoroMill® MS20 – pocketing
- M-M20 geometry gives higher security in tougher applications
- In case of sensitive / vibration prone applications and / or applications requiring a sharper cutting edge, the E-L50 geometry can be used
- The higher edge line toughness of these geometries allows the inserts to be used with higher productivity (high cutting data) in stable operations
- Robust steel shank design ensures better stability and less deflection. The improved tool body material can withstand chip rubbing better
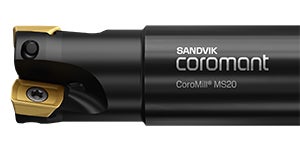
Deep slotting different methods
Solution 1
If the conditions are stable and the machine has enough power and torque the CoroMill® 331 is the ideal choice. This multi-purpose side and face milling cutter has high-precision capability.
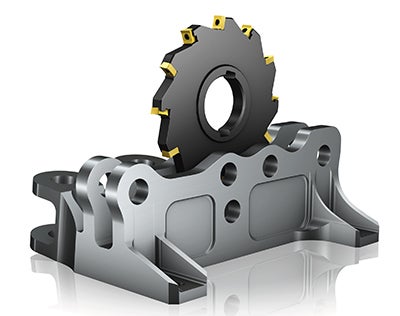
Solution 2
Light and fast method using the high feed cutter CoroMill 210. High feed cutters are being employed to a great extent on lighter machines for a light and fast approach. Low depth of cut but up to 1.0 mm feed per tooth provides good metal removal rate.
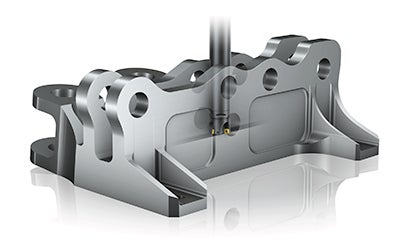
Solution 3
Plunging is a good solution for weaker set-ups and long overhangs. To maintain a good degree of productivity, it is important to be able to take a reasonable step over. The engineered special plunge tool using the CoroDrill 880 inserts can be a good problem solver.
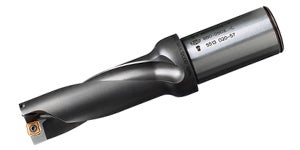
Drilling solution - CoroDrill® 880
The first choice drill for high productivity and low machining cost per hole with high penetration rate. The drill has been developed for up to 100% higher productivity, closer hole tolerance and improved surface finish. The CoroDrill 880 has four true cutting edges with wiper geometry on the peripheral insert offering better surface finish.
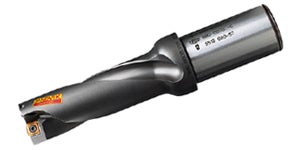