ねじ切り旋削のヒント
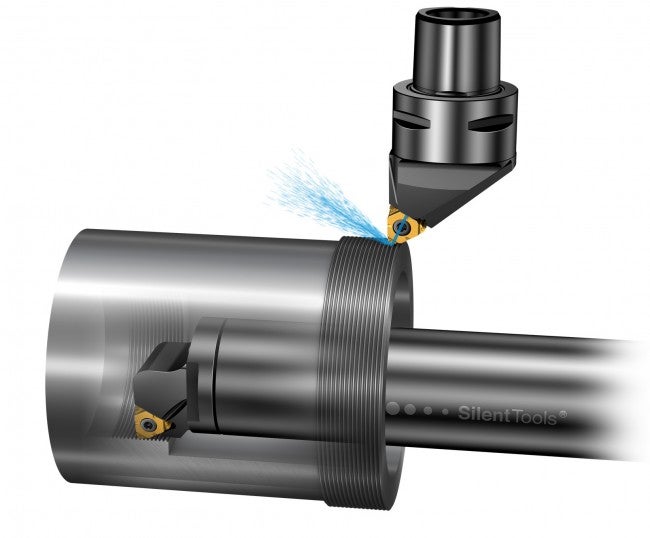
ねじ切り旋削で共通するトラブルは、ロボット、チャック、工具、加工ワーク周辺の切りくずです。切りくずがコンベアに挟まることもあり、損傷や生産加工時間のロスに繋がります。ねじ切り旋削では、スムーズな切りくず処理は良好な加工物品質の鍵になります。良好な切りくず処理と長い工具寿命を達成するためのヒントをご覧ください。
OptiThreading™
最良の可能な切りくず処理を達成するには、OptiThreading™加工法を使用してください。この加工法は、最後のパス以外すべてのパスにおいて断続切削を実現する工具振動動作を可能にします。最高のプロセスコントロールおよびワーク品質を実現します。
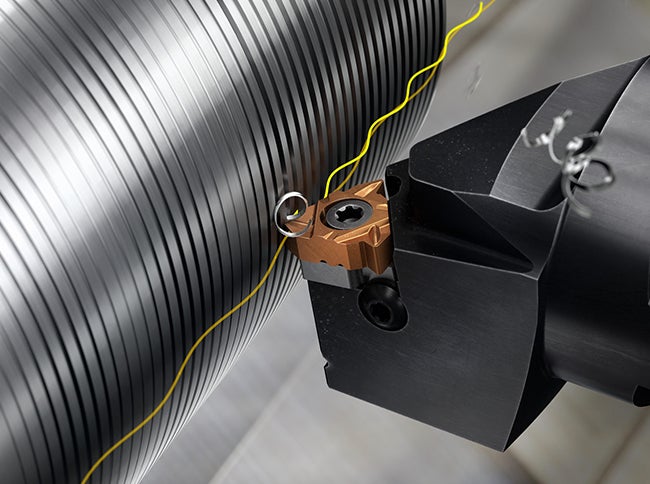
修正フランクインフィード
従来のねじ切り加工では、最良の切りくず処理を達成するために、修正フランクインフィードを使用してください。修正フランクインフィードにより、ねじ切り加工をさらに通常の旋削加工のように行うことができます。。プロセスが制御された状態になり、切りくずの問題もほとんどないため、工具寿命が予測可能になり、ねじ切り品質が向上します。
逆方向フランクインフィード
この切込み方法では、チップは背面の逃げ面を使って切削することができ (逆方向フランクインフィード)、切りくずは正しい方向に進みます。これは内径ねじ切り旋削では重要なことで、特に穴の底面を加工する際は重要です。この方法を使用して、予期せぬ機械停止のない、トラブルのない連続加工ができます。
標準的な修正フランクインフィード | 送り方向 | 逆方向フランクインフィード |
![]() | ||
切りくずの方向 | 切りくずの方向 |
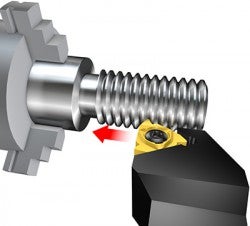
切削油とクーラント
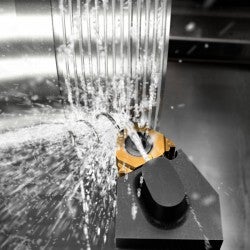
最適な切りくず処理と切りくず排出のために切削油と高精度クーラント対応の工具の使用をお勧めします。ねじ切り旋削における高精度クーラントの使用には以下の利点があります:
- 切刃の切削温度をコントロール可能
- 良好な切りくず排出
- 優れた切りくず処理
外部給油方式でのねじ切り加工では、少量のクーラントがねじ山に入るだけで、冷却効果はごくわずかです。
一方、内部給油方式では、噴射クーラントにより、深いねじ山加工でも切刃にクーラントが供給されます。クーラントが効果的に切削温度を下げることで以下の効果が期待できます。
- 高切削条件での加工、高じん性材種の使用が可能
- 切りくず処理と加工面品質が向上
加工温度が低いと、逃げ面摩耗や塑性変形を減らすことができ、それにより、工具寿命が長くなります。しかし、加工温度が低すぎると工具寿命が短くなります。粘性が高い被削材の加工で温度が低すぎると、構成刃先 (BUE) が発生します。
径の確認
ねじ切り旋削の前にワーク径が仕様どおりかを確認します。
- 外径ねじ切りの場合にワーク径が大きすぎると、または内径ねじ切りの場合にワーク径が小さすぎると、一発目の取り代が非常に大きくなりチップを破損することがあります。
- 外径ねじ切りの場合にワーク径が小さすぎると、または内径ねじ切りの場合にワーク径が大きすぎると、ねじ径が不良になることがあります。
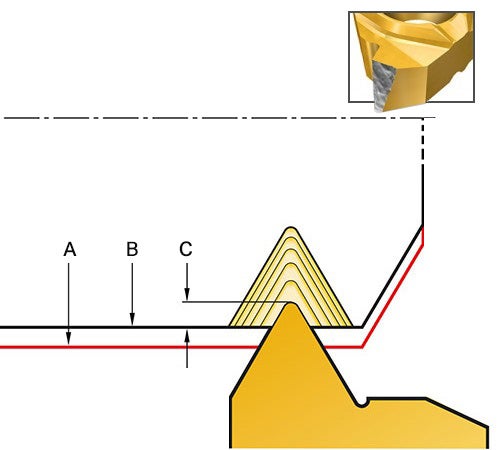
A:外径ねじの場合に、旋削加工径が大きすぎる
B:適切な外径ねじ径
C:ねじ切りサイクルでの一回目のパス
工具寿命
ねじ切り後にチップを注意深くチェックすることで、工具寿命、切削速度、ねじ切り品質で良好な結果を得ることができます。
工具寿命に影響する2つの主な加工パラメータが、加工速度と送りです。これらのパラメータのいずれかを高くすると、加工部品当りの切削時間は短くなりますが、加工温度が高くなります。温度が高すぎると工具寿命が短くなります。
最適な工具寿命を達成するには、まず送り/切りくず厚さを最適にするほうがよりメリットがあります。送り/切りくず厚さを大きくすると、切削速度を上げるときよりも加工温度上昇が少なくなります。一方、切りくず厚さが大き過ぎると、チップに過負荷がかかります。
クーラントを使用して加工温度を下げます。高精度の逃げ面へのクーラントは効果が絶大です。
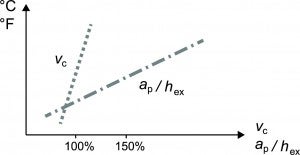
切削速度と送りを上げた時の加工温度への影響
送り ap |
|
|
切削速度、vc |
|
|
切りくず厚さ
加工硬化しやすい被削材の加工では浅い切込み (ワークの硬化した表皮への切込み) は避けてください。
径方向切込みが0.2 mm (0.008") の場合、逃げ面でのチップ厚は、
- 0.05 mm (0.002 inch)、30°タイプ
- 0.1 mm (0.004 inch)、60°タイプ
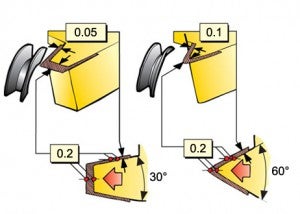
チップのノーズRと工具寿命
ノーズRはチップの最小ポイントで、ねじ切り旋削の非常に大きな圧力により最も破断しやすい箇所です。
ノーズRはチップのタイプによって大きく異なり、性能と機械の安全性を最適化するために、切削速度、パス数を考慮する必要があります。
NPTおよびNPTFねじプロファイルのチップは、標準品の中でもノーズRが最小です。性能を最適化するには、パス数を増やして切削速度を下げます。
内径チップは外径チップよりノーズRがはるかに小さいです。
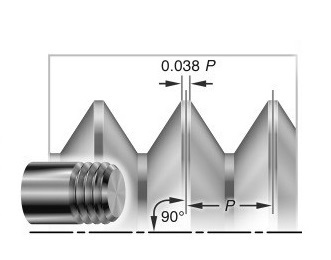
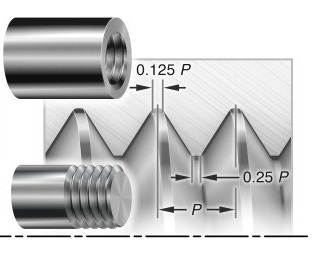
旋削工具での下加工
ねじ切り工具で最終仕上げパスを行う前に、55°または60° チップを装着した旋削工具でねじを下加工することによって、生産性と工具寿命の両方を改善することができます。
小さいノーズRを持つ谷底や山頂部を加工する際にも、角度が同じでノーズRの大きなチップを使用してのねじ切り荒加工を行うことにより同様な下加工を行うことができます。これにより、ねじ切り旋削チップを使用して加工する残りの仕上げパスのための削り代が残ります。
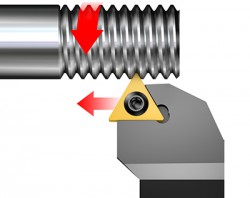
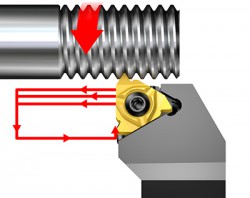
バリ取り
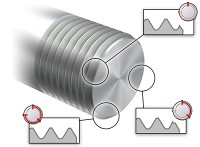
ねじ山の開始部のバリ取り
バリが発生する場合、チップが (ねじ山の) 完全な形状を生成する前に、ねじ山の開始部にバリができる傾向があります。これらのバリは問題を引き起こす事があるため、特に公差や品質要求が厳しい油圧や食品加工業界では、取り除く必要があります。
バリは難削材のステンレス鋼や2相被削材でもっともよく発生します。
ねじのバリ取りは、標準旋削工具で行えます。考慮すべき重要なことはねじ山、ピッチ、ねじ切りサイクルに合わせてバリ取りチップを適切に位置決めすることです。
ねじ山のバリの取り方
- 推奨切込みデータで標準のねじ切りサイクルを使用します。工具のねじ山からの抜け際は45°であること。
- 同じ切削速度と突切り・溝入れチップでパス数を半分にして、同じねじ切りプログラムを使用します。抜け際45°の前のバリ取り長さを1 x ピッチにプログラムして、下記の設定要領したがってゼロ点を測定します。
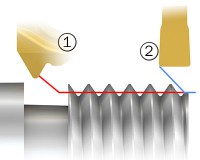
設定方法
- ねじ切りチップのゼロ点を設定します。
- 突切り・溝入れチップ上でゼロ点を測定します。
- 突切り・溝入れチップをゼロ点から適切な距離でオフセット
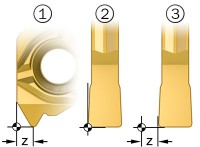
ねじ径のバリ取り
V形状チップでねじ切りする際、ねじ山の山頂部にしばしばバリが発生します。高品質のねじでは、このバリを取り除く必要があります。
多条ねじ
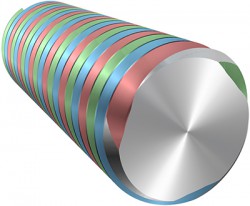
2本以上の並行ねじ溝があるねじは2つ以上のねじ開始ポイントが必要になります。このタイプのねじ山のリードは、1条ねじの2倍です。
リードはピッチの条数倍で増加します
- 1条ねじ - リードとピッチが同じ
- 2条ねじ - リードはピッチの2倍
- 3条ねじ - リードはピッチの3倍
多条ねじを作るには複数パスで1本目のねじ溝を作ってから、複数パスで2本目のねじ溝を作り、さらに複数パスで3本目のねじ溝を作ります。
適切なシムを選択することが大切です。リード値を使用して正しい傾斜角 (ねじれ角) を計算し、対応するシムを選択します。以下のセクションを参照してください。ねじ切り旋削チップとシムの選定方法
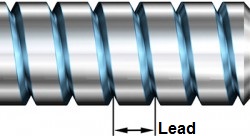
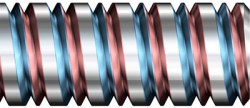
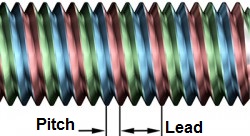
外径シャンクバイトの調整
リードがピッチの2倍、3倍と大きくなるにつれて、アプローチ角は急激に変化し、極端な場合にはシムによりカバーできる範囲を超えてしまうことがあります。このような極端な場合、外径シャンクバイトをアプローチ角の方向に削る/研磨することができます。
- シムにかかる部分は削らないでください。システム全体の安定性に影響を及ぼします。
- アプローチ角φ (ねじれ角) を計算して特注ホルダを注文します。
- 小径でピッチを大きくすると、アプローチ角が大きくなります。
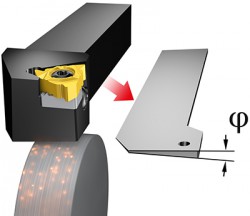
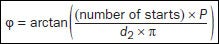