ねじ切り旋削加工でのインフィード 方法の選定方法
OptiThreading™
OptiThreading™はどのような加工法ですか?
OptiThreading™は、ねじ切り加工における制御された切りくず処理を可能にする工具振動動作のある加工法です。このユニークな加工法は、最後のパス以外すべてのパスにおいて反復断続切削を行います。
OptiThreading™のメリット
- 工具、ワークおよび/または切りくずコンベアでの長い切りくずの詰まりを取り除く手作業を少なくすることが可能
- 突発的な機械停止が少なく、高い生産性および良好なオートメーションを達成
- ワークを損傷する長い切りくずがないため、ワーク加工面品質が良好
- この加工法により、良好な加工面品質と制御されたびびりを実現
- 主に大きなねじ/径に対して切削速度を上げることができ、生産性を高めることが可能
- びびりが少なく、工具突出し量を増やすことが可能
OptiThreading™の使用時に考慮すべきこと
- ISOコード (G32/G33/G34) を処理できるCNC機械
- 外径および内径加工
- 通常のねじおよび円錐/テーパねじ
- ねじ径12 mm以上の規格ねじに対応
- 加工にはクーラントの使用を推奨
Optithreading™加工方法
CoroPlus®ツールパスソフトウェアでNCプログラムを生成する方法の動画はこちら。
従来のねじ切り加工方法
主なねじ切り旋削インフィード 加工方法には3種類あります。修正フランクインフィード、ラジアルインフィードおよびインクレメンタルインフィード 。インフィード方法とは、チップがワークに対してどのように切込んでねじを形成するかのことです。
修正フランクインフィード
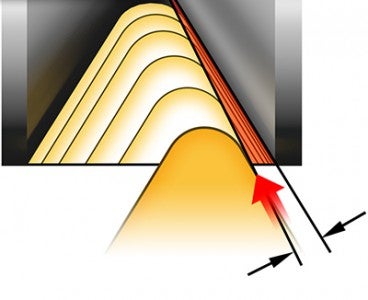
ラジアルインフィード (ストレートインフィード)
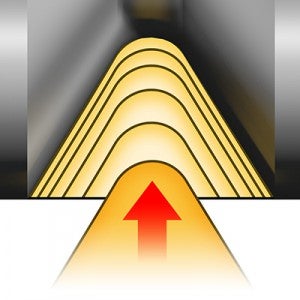
インクレメンタルインフィード
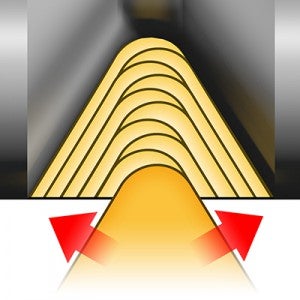
インフィード方法の選定は工作機械、チップブレーカ、ワーク材、ねじ山の形状、ねじ山ピッチに左右されます。
- 切りくず処理
- ねじ加工品質
- チップ摩耗タイプ
- 工具寿命
修正フランクインフィード
修正フランクインフィードは、非常に長い工具寿命と最高の切りくず処理を実現する第一推奨の加工法です。ほとんどのCNCマシンではこの方法で事前にプログラムされており、チップの端が加工ワーク表面をこすらないように若干変更 (角度を変えて) してあります。
- すべてのねじ切り旋削とチップタイプに推奨
- 切りくずは厚くなるが、チップの片側だけに形成されるので、処理しやすい
- チップへ伝わる熱が少ないため、必要なパスは2~3回
- ねじの両方の逃げ面を使用でき、切りくずを適切な方向へ排出します
- 大きなねじ山用に使用してびびりを抑えます
- 切りくず切断ブレーカを備えたチップには、この切込み方法に最適です。インフィード角度は1°にしてください。
機械型番例:
G76、X48.0、Z-30.0、B57 (インフィード角度) D05など
他の機械タイプでは、逃げ面切込み用のパラメータは:G92、G76、G71、G33、G32
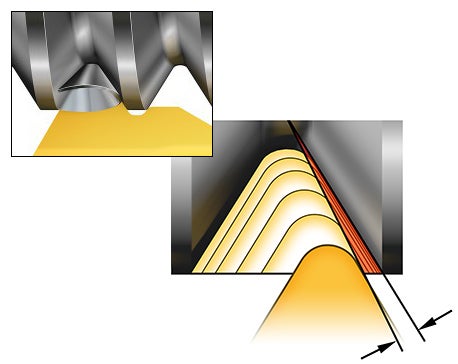
ラジアルインフィード
ラジアル (ストレート) インフィードは最も一般的に使用されている切込み方法で、多くの非CNC旋盤では子御方法のみが可能です。
- 切刃の両面にV形状の硬い切りくずが生成
- 摩耗はチップ両方で均一に発生
- 細かいピッチ (1.5mm未満のピッチ) に適している
- チップ刃先の先端が高温になり、切込み量が制限される
- 大きなピッチの場合、びびりが生じたり切りくず処理が不十分になります。
- 切りくず切断ブレーカは、ラジアルインフィードには適していません。
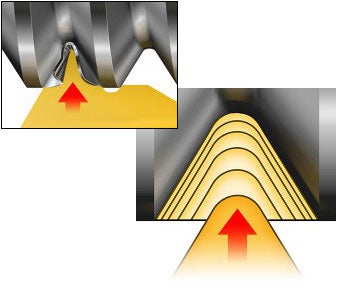
インクレメンタルインフィード
インクレメンタルインフィードは大きなねじ山タイプの第一推奨です (5 mm (5 t.p.i) 以上のピッチに推奨)。
- 切りくずが両方向に向かうため、切りくず処理が難しくなります。
- チップの摩耗が均等で、極めて粗い目のねじ加工で最長の工具寿命を実現
- インクレメンタルインフィードにはどのブレーカも使用することができます。
- 特殊なCNCマシンプログラムが必要
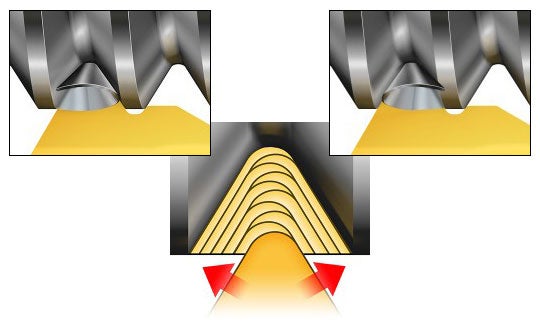
パスごとの切込み深さ
切込み推奨値は、カタログまたはツールガイドに記載されています。これらは推奨初回試行値です。試行によりそれぞれのねじ切り旋削について最適なパス数を求める必要があります。
- 0.05 mm (0.002 inch) 以下の切込みは避けてください。
- CBNチップでは、切込みは0.10 mm (0.004 inch) 以下にしてください。
- マルチポイントチップには、適切な切込み推奨値の使用が必須です。
1回の送りの深さを減少 (切りくず断面積が一定)。
パスごとの切込み深さを減らすことは加工結果を改善するための最も一般的な方法で、すべてのねじ切り旋削では第一推奨になります。
- 一回目のパスを一番深くして最後のパスは切込み深さを0.07 mm (0.003") くらいにします。
- チップへの負荷を均等にし、切りくず断面積を「均一」にします。
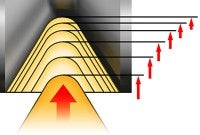
パスごとの切込み深さが一定。
パスごとの切込み深さを一定にして、各パス (最終パス以外) をパス数に関係なく同じにします。以下の場合は生産性が下がります。
- 必要なパス回数が増える
- チップへの負荷が大きい
- よりよい切りくず処理が可能
- ピッチ1.5 mmまたは16山数/インチを超える場合は使用しないこと
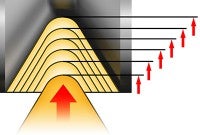
CNC旋盤におけるねじ切り旋削サイクル
標準のCNC旋盤には専用ねじ切り旋削サイクルがあり、一回目と最終パスを含めて、ピッチ、ねじ山深さ、パス数を別々に設定可能です。
最終パスには、スプリングパスの使用を強くお勧めします (最終パスの切込み深さが直前のパスの切込み深さと同じになります)。良好なねじ山品質と長い工具寿命を実現するには、推奨インフィードサイクルの使用が有益です。
工具送り方向
ねじ山はいろいろな方法で加工することができます。スピンドルは時計回り/反時計回りに回転可能で、工具の送りはチャックに向かう方向、またはチャックから離れる方向になります。ねじ切り工具は通常の位置でも逆さまにしても使用することができます (後者は切りくずの排出に役立ちます)。

最も一般的なセットアップは、下の図で緑色でマークされています。
チャックから離れる (引きねじ切り加工)
左ねじ用右勝手工具 (または反対) を使用すると、工具在庫を減らして費用削減ができます。

下図の赤でマークされたセットアップでは、負のシムを使用する必要があります。
外径加工 | |
右ねじ | 左 ねじ |
![]() 右勝手工具/チップ | ![]() 左勝手工具/チップ |
![]() 右勝手工具/チップ | ![]() 左勝手工具/チップ |
![]() 左勝手工具/チップ | ![]() 右勝手工具/チップ |
内径加工 | |
右ねじ | 左 ねじ |
![]() 右勝手工具/チップ | ![]() 左勝手工具/チップ |
![]() 右勝手工具/チップ | ![]() 左勝手工具/チップ |
![]() 左勝手工具/チップ | ![]() 右勝手工具/チップ |
![]() 左勝手工具/チップ | ![]() 右勝手工具/チップ |