Auswahl der korrekten Spindel
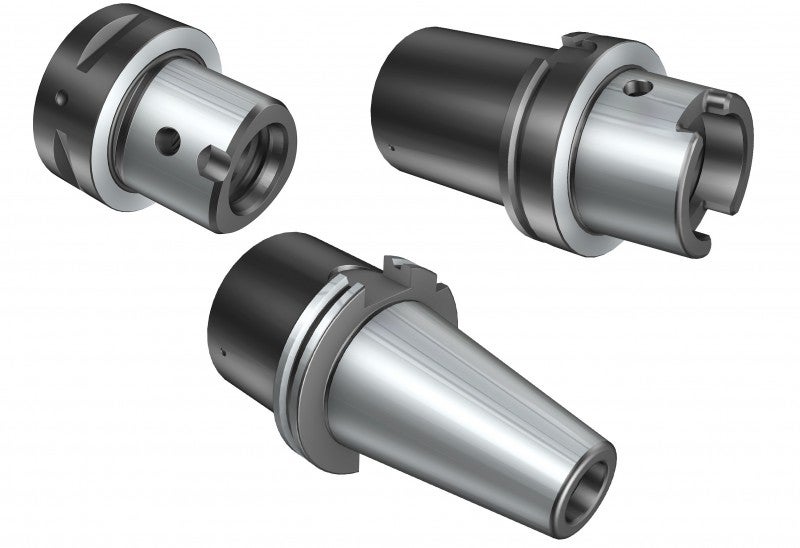
Die Wahl der Spindelschnittstelle ist die wichtigste Entscheidung, da diese oftmals die Beschränkungen hinsichtlich der Zerspanungsleistung festlegt. Es gibt keine schnelle Antwort darauf, welche Schnittstelle die beste ist – tatsächlich hängt sie von den zu bearbeitenden Teilen sowie den durchzuführenden Anwendungen ab. Es sollte nicht immer davon ausgegangen werden, dass die Standardspindeloptionen bei einer Maschine notwendigerweise die beste Schnittstellenwahl darstellen.
Anforderungen an die Maschinenspindel
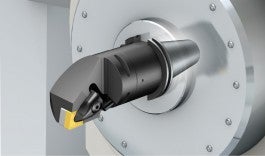
Wird nicht zerspant, muss die Spindelschnittstelle schnell austauschbar sein. Bei der Bearbeitung ist es jedoch wichtig, dass die Verbindung zwischen Spindel und Kupplung stabil ist, auch wenn Schnittkräfte alles versuchen, diese zu lösen. Eine Schnittstelle mit guter Biegesteifigkeit und hervorragendem Drehmomentvermögen zu haben, ist sehr wichtig.
- Biegesteifigkeit: Erforderlich bei großen Werkzeugüberhängen und hohen Schnittlasten
- Drehmomentübertragung: Bearbeitungen mit großen Durchmessern sind am anfälligsten. Die in einem Abstand zur Spindelzentrumslinie einwirkende Last (Drehmoment = Kraft x Radius) muss durch einen größeren Antriebskontaktbereich ausgeglichen werden.
- Präzise Werkzeugmittenposition : Für gute Wiederholgenauigkeit und eine sichere Produktion, was insbesondere bei Drehanwendungen wichtig ist
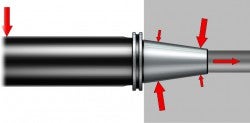
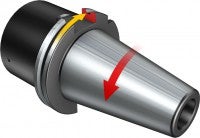
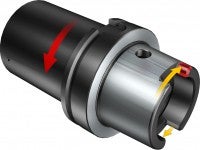
Die Kupplungsmerkmale, die hohen Biegemomenten und hohen radialen Schnittkräfte widerstehen sollen, sind:
- Flanschkontaktdurchmesser: Flanschflächenkontakt erhöht die Plattformgrundlage durch den Einfluss der Schnittkraft
- Spannkraft: Je größer die Spannkraft zur Rückhaltung einer Kupplung, desto größer ist die für das „Umlegen“ der Kupplung notwendige Schnittkraft
- Querschnittsfläche: Die Verkleinerung des Werkzeugdurchmessers im Verhältnis zum Flanschkontaktdurchmesser verringert die Steifigkeit des Werkzeugs
- Drehmomentübertragung: Am besten erkennbar bei Werkzeugen mit großem Durchmesser und beim Drehen, kein Drehmomentwiderstand bedeutet sofortigen Verlust der Mittenhöhe und der Präzision
Historie von Maschinenspindelschnittstellen
Die Maschinenspindelschnittstelle hat sich mit der Weiterentwicklung der Maschinen ebenfalls gewandelt. Zu den wichtigsten Meilensteinen, die unserer Meinung nach die Änderungen stark vorangetrieben haben, gehören:
- Die NC-Steuerung, die zu automatischem Werkzeugwechsel und Werkzeuglagerung geführt hat. Ergebnis war ein Steilkegel mit Anzugsbolzen und Greifernuten.
- Höhere Spindeldrehzahlen
- Multifunktionale Bearbeitung – Drehen, Fräsen und Bohren mit derselben Schnittstelle
Die erste und wohlbekannte Schnittstelle war der Morsekegel, der bereits 1868 für das Bohren entwickelt wurde. Später wurde der Steilkegel 7/24, auch ISO-Kegel genannt, eingeführt (1927). Greifernuten und Anzugsbolzen für den Werkzeugwechsel kamen in den 60er Jahren auf den Markt, allerdings in regional beschränkten Varianten: MAS-BT in Asien, ISO/DIN in Europa and CAT-V in Amerika.
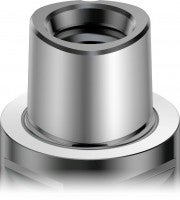
Der Nachteil des Steilkegels betrifft die Biegesteifigkeit und das Drehzahlvermögen aufgrund der geringen Spannkraft und dem fehlendem Flächenkontakt mit der Spindelnase. Dies führte in den 90er Jahren zur Entwicklung von BIG-PLUS® (entwickelt von BIG Daishowa in Japan), HSK (entwickelt vom DIN-Ausschuss in Deutschland) und Coromant Capto® (eingeführt 1990 und das einzige System, das vom ersten Tag ab für alle Anwendungsarten entwickelt wurde – Drehen, Fräsen und Bohren).
Schnittstellentypen für Maschinenspindeln
In der unteren Tabelle werden die vier zentralen Kupplungen und deren schrittweise Entwicklung vom tradidionellen Steilkegel bis hin zu Coromant Capto® gezeigt. Alle Schnittstellen, außer BIG-PLUS®, sind nach DIN, ISO oder ANSI standardisiert.
Kegelwinkel | Flanschkontakt | Spannmethode | Drehmomentübertragung | |
Steikegel | 16.26° | Keine | Anzugsbolzen | Mitnehmersteine am Flanschkontakt |
BIG-PLUS® | 16.26° | Ja | Anzugsbolzen | Mitnehmersteine am Flanschkontakt |
HSK-A | 5.7° | Ja | Interne Segmentspannung | Mitnehmersteine am Kegel |
Coromant Capto® | 2.88° | Ja | Interne Segmentspannung | Polygon |
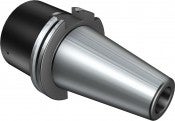
Steilkegel
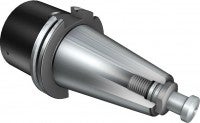
BIG-PLUS®
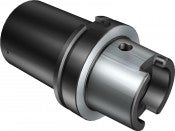
HSK-A
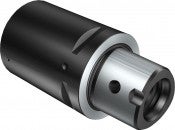
Coromant Capto®
Steilkegel 7/24
Bei Steilkegeln ist der Kegelwinkel immer gleich. Die Greifernut und das Gewinde für den Anzugsbolzen können variieren. Erhältlich als CAT, ISO, DIN und MAS BT.
BIG-PLUS®
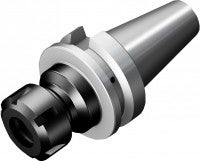
BIG-PLUS® ist für Anwendungen in Bearbeitungszentren ausgelegt. Kegel und Greifernut sind dieselben wie beim herkömmlichen Steilkegel, allerdings wird der Flächenkontakt über enge Toleranzen erreicht, wodurch sich die Biegesteifigkeit erhöht. Ein Standard-Steilkegelhalter passt in eine BIG PLUS® -Spindel, allerdings wird eine Kombination nicht empfohlen. Erhältlich als CAT, ISO, DIN und MAS BT.
HSK
HSK (DIN 69893) ist für Anwendungen in Bearbeitunsgzentren ausgelegt. Er zeichnet sich durch Flanschkontakt und Segmentspannung des Hohlkegels aus, was Anzugsbolzen überflüssig macht. Die Mitnehmersteine haben, je nach Variante, unterschiedliche Konfigurationen und sind in einigen Fällen nicht für Hochgeschwindigkeitsanwendungen geeignet.
- Typ-A: Allgemeine Bearbeitung, hohe Biegelasten und moderates Drehmoment, automatischer Werkzeugwechsel
- Typ-B: Stationäre Anwendung, moderate Biegelasten, hohes Drehmoment, Sonderanwendungen, automatischer Werkzeugwechsel
- Typ-C: Allgemeine Bearbeitung, hohe Biegelasten, moderates Drehmoment, manueller Werkzeugwechsel (Ref. Typ-A)
- Typ-D: stationäre Anwendung, moderate Biegelasten, hohes Drehmoment, Sonderanwendungen, manueller Werkzeugwechsel (Ref. Typ-B)
- Typ-E: Hochgeschwindigkeitsanwendungen, leichte und schnelle Spindeln, niedrige Biegemomente und geringes Drehmoment, automatischer Werkzeugwechsel, einfaches Auswuchten
- Typ-F: Moderate Geschwindigkeiten, Bearbeitung weicher Werkstoffe, mittlere Biegemomente und Drehmomente,automatischer Werkzeugwechsel, einfaches Auswuchten
- Typ-T: Rotierende und stationäre Anwendungen mit engeren Toleranzen in der Mitnehmernut (für die Werkzeugpositionierung). Es ist kein „Hals“ erforderlich, somit sind die Biegemomentfähigkeiten besser
Hinweis! die meisten Maschinen mit HSK-T Spindelschnittstelle benötigen immer noch den Hals für automatischen Werkzeugwechsel und Magazine – das bedeutet, dass HSK A/C/T-Werkzeuge erforderlich sind
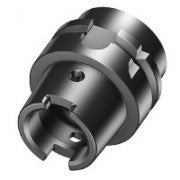
A
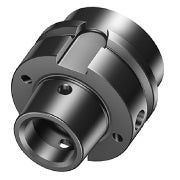
B
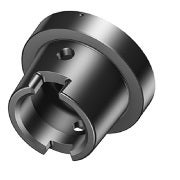
C
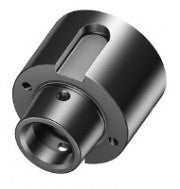
D
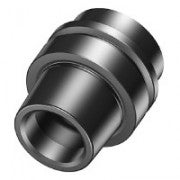
E
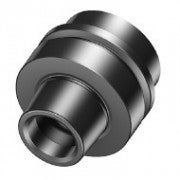
F
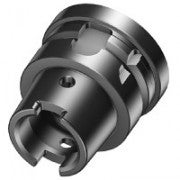
T
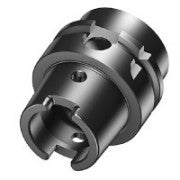
A/C/T
Coromant Capto®
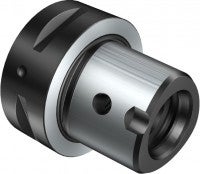
Coromant Capto® (ISO 26623) vereinigt die Vorteile von HSK und BIG-PLUS®, erfordert jedoch durch die konische Polygonform mit Flächenkontakt keine Mitnehmer. Dank des robusten Kupplungsquerschnitts ist Platz für eine Segmentspannung mit der höchsten Spannkraftleistung, was für unübertroffene Biegesteifigkeit, Drehmomentübertragung sowie Genauigkeit der Mittenposition sorgt.
Die höhere radiale Präzision und verbesserte Drehmomentübertragung wurde notwendig, um die Anforderungen von drei wichtigen Anwendungsbereichen zu erfüllen:
- Maschinenspindelschnittstelle – Bearbeitungszentren und Vertikal-Drehmaschinen
- Modulare Kupplung – Bearbeitungszentren
- Manuelles Schnellwechselsystem – Drehmaschinen
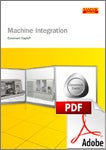
Coromant Capto® ist die gängigste Schnittstelle für Multi-Task-Maschinen, da sich sowohl für stationäre (Drehen) und rotierende Anwendungen (Fräsen/Bohren) einsetzen lässt.

Suchen Sie Werkzeugempfehlungen?
Hier finden Sie unsere Zerspanungswerkzeuge chevron_right
Brauchen Sie Beratung?
Stellen Sie uns eine Frage chevron_right
Was es sonst noch über die Grundlagen unserer Metallzerspanung zu lernen gibt?
Registrieren Sie sich für unser kostenloses E-Learning Programm chevron_right
Empfehlungen zu Maschinenspindeln für unterschiedliche Maschinentypen
Bearbeitungszentren (nur rotierende Anwendungen)
Hierfür wird eine Spindelschnittstelle mit Flächenkontakt empfohlen. BIG-PLUS® und HSK-A bieten eine gute Stabilität für die meisten rotierenden Anwendungen in Bearbeitungszentren. Für Heavy Duty-Anwendungen C10 sollte im Voraus eine größere Kupplung wie HSK-A 125 oder SK60 in Betracht gezogen werden. Bei hohen Drehzahlen empfehlen sich HSK-E oder F.
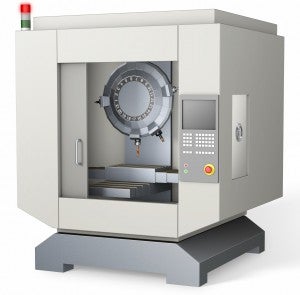
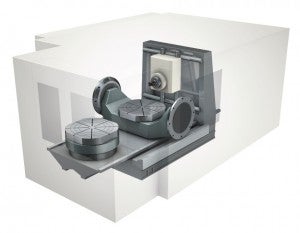
Multifunktionale Maschinen (stationär und rotierend)
Coromant Capto® ist der einzige Kupplungstyp, der die Anforderungen an Drehmoment und Biegesteifigkeit für stationäre und rotierende Anwendungen erfüllt.
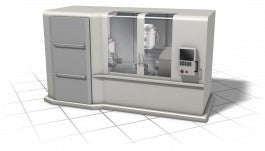

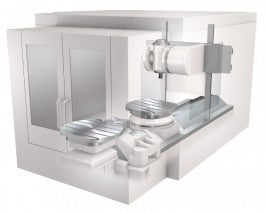
Es gibt verschiedene Lösungen für die Spindelbefestigung sowie die Spindelschnittstellenproduktion. Sandvik Coromant arbeitet aktiv mit Werkzeugmaschinenbauern zusammen, um die Integration von Coromant Capto® in Maschinen voranzutreiben. Unser Hauptaugenmerk liegt dabei auf den Maschinenausführungen sowie -schnittstellen, bei den die Vorteile von Coromant Capto® noch nicht optimal ausgenutzt werden können.
C3 | C4 | C5 | C6 | C8 | C10 | |
Drehzentrum | * | * | ||||
Heavy Duty Drehmaschine | ||||||
Vertikal-Drehmaschine | ||||||
Multi-Task-Maschine | ||||||
BAZ mit Drehoption | ||||||
BAZ, Heavy Duty |
* Lange Bohrstangen auf großen Drehzentren
Vergleich der Spannkräfte
Die interne Segmentspannung bei Hohlkegeln (HSK und Coromant Capto®) kann eine höhere Spannkraft liefern, als es der Anzugsbolzen an einem Steilkegel vermag. Die Tabelle zeigt die aufgewendete Spannkraft bei den entsprechenden Schnittstellen. Der größere Querschnitt und die höhere Kupplungslänge von Coromant Capto® erlauben sehr viel höhere Spannkräfte im Vergleich zu HSK-A.
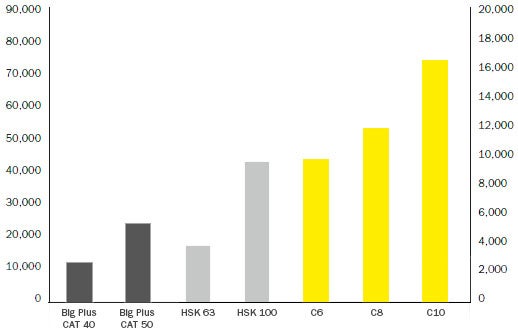
Quelle: HSK-Handbuch, Copyright 1999.
Big Daishowa (BIG PLUS Spindelsystem)
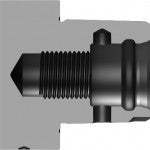
Coromant Capto®
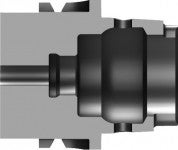
HSK-A
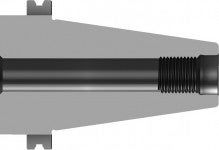
Steilkegel (SK)
Vergleich von Drehmomentübertragung und Biegesteifigkeit
Steilkegel – die Mitnehmersteine auf einem großen Radius sorgen für einen guten Antrieb bei den rotierenden Anwendungen
HSK-A – eine kleine Kontaktfläche mit Nuten auf dem Kegel eher als der Flanschdurchmesser (kleiner Radius), deshalb nicht für Anwendungen mit hohen Drehmomentwerten empfohlen.
Coromant Capto® – für Drehanwendungen, bei denen die Genauigkeit der Mittenposition notwendig ist, wofür der Polygonantrieb die beste Lösung ist.
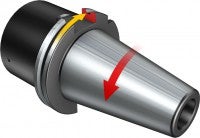
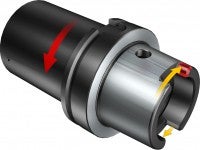
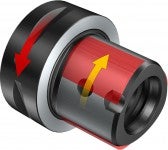
Die Kupplungsgröße hat Auswirkungen auf die Biegesteifigkeit und die maximale Drehzahl. Eine große Kupplung bietet gute Biegesteifigkeit aber geringe Drehzahlen, während eine kleine Kupplung eine höhere Drehzahl ermöglicht, die Biegesteifigkeit jedoch verringert.
Das Diagramm unten zeigt die Beschränkungen für die jeweilige Kupplungsausführung nach theoretischen (FEA)-Berechnungen für den Zeitpunkt, wenn der Flächenkontakt verloren geht (Biegesteifigkeit) und die Ermüdungsgrenze erreicht ist (max. Drehmoment).
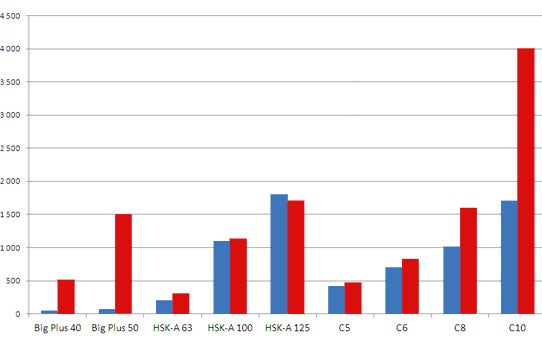
Blau: Maximales Biegemoment (Nm)
Rot: Maximales Drehmoment (Nm) innerhalb der Dauerfestigkeit
BIG-PLUS® und HSK sorgen für ausreichende Stabilität bei den meisten rotierenden Anwendungen; für Multi-Task-Maschinen jedoch ist Coromant Capto die einzige Kupplung, die in der Lage ist, die Anforderungen an Drehmoment und Biegesteifigkeit bei stationären und rotierenden Anwendungen zu erfüllen.
Kupplung | Größe und Spannart | Spannkraft (Anzugsbolzen oder Zugstange) | Max. Drehzahl (abhängig von Spindel und Lagern) | |
N | lbs | |||
BIG-PLUS® ISO/CAT/BT Kegel 7/24 | Kegel 40 | 12000 | 2703 | 16000 |
Kegel 50 | 24000 | 5405 | 12000 | |
HSK-A | HSK-A 63 | 18000 | 4054 | 20500 |
HSK-A 100 | 45000 | 10135 | 12500 | |
HSK-A 125 | 70000 | 15766 | 9500 | |
Coromant Capto® | C5 | 32000 | 7207 | 28000 |
C6 | 41000 | 9234 | 20000 | |
C8 | 50000 | 11261 | 14000 | |
C10 | 70000 | 15766 | 10000 |
Statikprüfung - Vergleich von Biegesteifigkeit und Drehmomentfestigkeit
Die renommierte RWTH Aachen führte eine Reihe von Statikprüfungen im Werkzeugmaschinenlabor (WZL) durch, bei denen die Biegesteifigkeit sowie die Drehmomentfestigkeit von unterschiedlichen Spindelschnittstellen ermittelt wurden.
Coromant Capto® wurde mit zwei Spannkräften gemessen: dieselbe wie für HSK-A, (22 kN für C6 und 50 kN für C10) und anschließend die höhere Standardspannkraft (45 kN für C6 und 80 kN für C10).
Biegesteifigkeit
Ablenkung [mm/m]
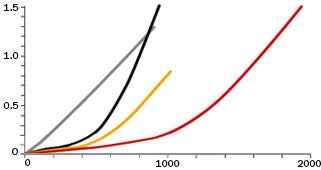
Biegemoment [Nm]




C6- 45kN
C6- 22kN
HSK-A 63- 22kN
7/24 Kegel, Größe 40-15kN
Biegesteifigkeit
Ablenkung [mm/m]
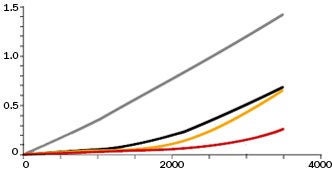
Biegemoment [Nm]




C10- 80kN
C10- 50kN
HSK-A 100- 50kN
7/24 Kegel, Größe 50-25kN
Die Ergebnisse zeigen, dass selbst mit derselben Spannkraft wie bei HSK-A die stärkere Kupplung eine höhere Biegesteifigkeit aufwies. Allerdings war die Kippkraft bei einer höheren Spannkraft für C6 2,88-mal besser als bei HSK-A 63 und für C10 2,15-mal besser im Vergleich zu HSK-A 100.
Drehmomentfestigkeit
Ablenkung [mm/m]
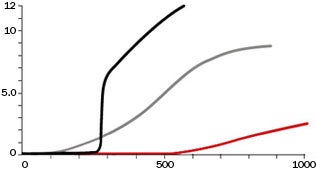
Drehmoment [Nm]



C6- 46kN
HSK-A 63- 22kN
7/24 Kegel, Größe 40-15kN
Drehmomentfestigkeit
Ablenkung [mm/m]
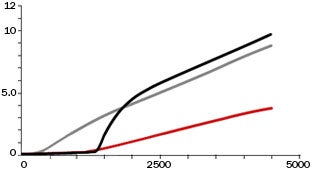
Drehmoment [Nm]



C10- 50kN
HSK-A 100- 50kN
7/24 Kegel, Größe 50-25kN
Die Kurven beweisen, dass Coromant Capto C6® über eine 2,29-mal höhere Drehmomentfestigkeit als HSK-A 63 verfügt. Der Verdrehwinkel ist 7,1-mal höher. Entsprechende Zahlen gelten auch für C10, wobei für C10 eine 1.85-mal höhere Drehmomentfestigkeit und einen 4.0-mal höheren Verdrehwinkel als bei HSK-A 100 ermittelt wurde.
Suchen Sie Werkzeugempfehlungen?
Hier finden Sie unsere Zerspanungswerkzeuge chevron_right
Brauchen Sie Beratung?
Stellen Sie uns eine Frage chevron_right
Was es sonst noch über die Grundlagen unserer Metallzerspanung zu lernen gibt?
Registrieren Sie sich für unser kostenloses E-Learning Programm chevron_right