Jak wybrać rodzaj gniazda wrzeciona
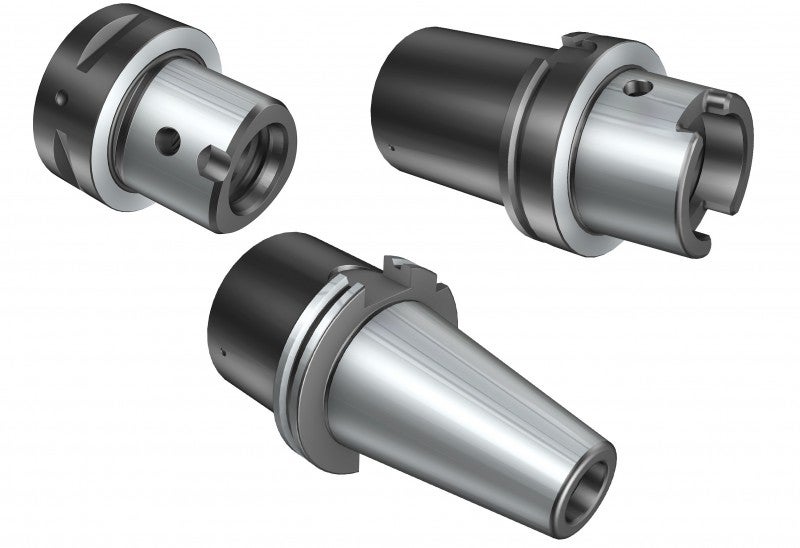
Wybór złącza w gnieździe wrzeciona to ważna decyzja, z którą często wiążą się ograniczenia efektywności obróbki. Nie da się jednoznacznie odpowiedzieć na pytanie, które złącze jest najlepsze – zależy to od obrabianych przedmiotów i rodzaju wykonywanej obróbki. Nie należy zakładać, że typowe złącza wrzeciona dostarczane w zestawie z obrabiarką stanowią najlepszy wybór.
Wymagane parametry złącza gniazda wrzeciona obrabiarki
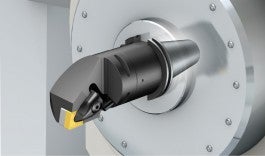
Złącze wrzeciona obrabiarki musi zapewniać szybkie przezbrojenie podczas przerw w obróbce. W trakcie obróbki sprawą kluczową jest, by połączenie między wrzecionem obrabiarki a oprawką zachowywało stabilność, nawet pod działaniem bardzo dużych sił skrawania. Złącze powinno charakteryzować się dużą wytrzymałością na zginanie i skręcanie.
- Wytrzymałość na zginanie: Konieczna dla zapewnienia stabilnych warunków obróbki na długich wysięgach lub przy dużych obciążeniach
- Przenoszenie momentu: Czynności na dużych średnicach wymagają największej ostrożności. Obciążenie znajdujące się w pewnej odległości od osi wrzeciona (moment=siła x promień) należy zrównoważyć większą powierzchnią styku napędu
- Dokładność położenia osi symetrii narzędzi: Konieczne dla zapewnienia powtarzalności i bezpieczeństwa produkcji, co jest szczególnie ważne podczas toczenia
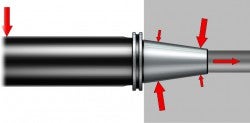
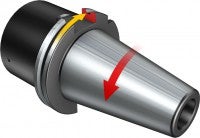
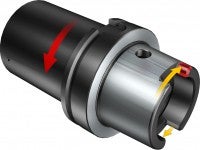
Właściwości złącza zwiększające wytrzymałość na zginanie lub skręcanie to:
- Styk na powierzchni czołowej kołnierza: Oparcie o czoło kołnierza zwiększa pole podstawy, ograniczając ugięcie pod działaniem sił procesu skrawania
- Siła mocująca: Im większa siła mocująca, tym większa może być wartość sił skrawania bez uszczerbku dla stabilności połączenia
- Pole przekroju poprzecznego: Im mniejsza średnica narzędzia w stosunku do średnicy styku na powierzchni czołowej kołnierza tym mniejsza sztywność narzędzia
- Przenoszenie momentu obrotowego: Najlepiej zauważalne dla narzędzi o dużej średnicy i podczas toczenia; zastosowanie złącza niedostosowanego do wartości momentu skręcającego powoduje natychmiastowe przesunięcie względem osi i pogorszenie dokładności obróbki
Historia rozwoju złącz wrzeciona obrabiarki
Złącze wrzeciona ewoluowało wraz z rozwojem obrabiarek. Kamieniami milowymi, jakie zaznaczyły swój wpływ na tej drodze, były:
- Wprowadzenie sterowania numerycznego, które w efekcie doprowadziło do automatycznej wymiany narzędzi i do ich magazynowania. To z kolei prowadziło do zastosowania stożka ze śrubami ściągającymi i rowków dla chwytaka
- Zwiększenie obrotów wrzeciona
- Obrabiarki wielozadaniowe – wykonywanie toczenia, frezowania i wiercenia z użyciem tego samego złącza
Pierwszym, niezwykle popularnym złączem był stożek Morse'a do obróbki wiertarskiej, opracowany w roku 1868. Po nim pojawił się stożek 7/24, nazywany też stożkiem ISO, wprowadzony w 1927 r. Rowki chwytaka i śruby ściągające do zmieniacza narzędzi dodano w latach 60. XX wieku w trzech wariantach lokalnych; MAS-BT w Azji, ISO/DIN w Europie oraz CAT-V w Ameryce.
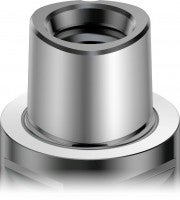
Wadą stożka były ograniczone wytrzymałość na zginanie i prędkość obrotowa z powodu niewielkiej siły mocującej i braku styku czoła kołnierza z czołem końcówki wrzeciona. Doprowadziło to w latach 90. XX wieku do stworzenia nowych rozwiązań: BIG-PLUS® (zaprojektowanego w Japonii przez BIG Daishowa), HSK (stworzonego w Niemczech przez Komitet ds. normy DIN) oraz Coromant Capto® (wprowadzonego na rynek w roku 1990 i będącego jedynym systemem od początku stworzonym do wszelkiego typu zastosowań – toczenia, frezowania i wiercenia).
Rodzaje gniazd końcówki wrzeciona obrabiarki
W poniższej tabeli pokazano cztery główne typy złączy oraz stopniową ewolucję od tradycyjnego stożka do złącza Coromant Capto®. Wszystkie złącza z wyjątkiem BIG-PLUS® są obecnie znormalizowane w systemie DIN, ISO lub ANSI.
Kąt stożka | Styk na czole kołnierza | Sposób mocowania | Przenoszenie momentu obrotowego | |
Stożek 7/24 | 16,26° | Nie | Śruba ściągająca | Zabieraki na kołnierzu |
BIG-PLUS® | 16,26° | Tak | Śruba ściągająca | Zabieraki na kołnierzu |
HSK-A | 5,7° | Tak | Wewnętrzne mocowanie segmentowe | Zabieraki na stożku |
Coromant Capto® | 2,88° | Tak | Wewnętrzne mocowanie segmentowe | Przekrój trygonalny |
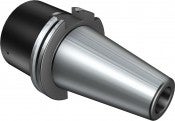
Stożek
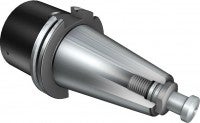
BIG PLUS®
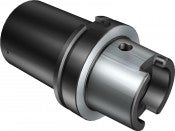
HSK-A
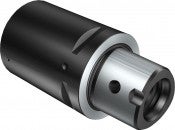
Coromant Capto®
Stożek 7/24
W przypadku stożków ich kąt zbieżności jest zawsze taki sam. Rowek dla chwytaka i gwint śruby ściągającej mogą być różne. Dostępne w wersjach CAT, ISO, DIN oraz MAS BT.
BIG PLUS®
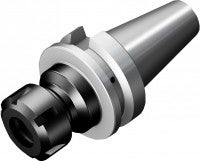
Złącze BIG-PLUS® zostało stworzone do stosowania w centrum obróbkowym. Stożek i rowki dla chwytaka są takie same, jak w konwencjonalnym stożku; większa jest wytrzymałość na zginanie wynikająca z dokładnego styku czołowej powierzchni kołnierza uchwytu z czołem końcówki wrzeciona. Standardowy stożek 7/24 pasuje do gniazada wrzeciona w wersji BIG-PLUS®, jednak nie zaleca się łączenia ze sobą narzędzi z różnych systemów. Dostępne w wersjach CAT, ISO, DIN oraz MAS BT.
HSK
Złącze HSK (DIN 69893) zostało stworzone do stosowania w centrum obróbkowym. Złącze posiada styk na czole kołnierza i mocowanie segmentowe ze stożkiem pustym w środku, nie wymaga zatem użycia śrub ściągających. Ustawienie zabieraków jest różne w zależności od modelu; w niektórych przypadkach, nie nadaje się do obróbki szybkościowej.
- Typ A: Obróbka ogólna, duże momenty gnące i umiarkowane momenty skręcające, do automatycznej wymiany
- Typ B: Zastosowania nieobrotowe, umiarkowane momenty gnące, duże momenty skręcające, zastosowania specjalne, do automatycznej wymiany
- Typ C: Obróbka ogólna, duże momenty gnące i umiarkowane momenty skręcające, ręczna wymiana (patrz: typ A)
- Typ D: Zastosowania nieobrotowe, umiarkowane momenty gnące, duże momenty skręcające, zastosowania specjalne, ręczna wymiana (patrz: typ B)
- Typ E: Obróbka szybkościowa, lekkie i szybkoobrotowe wrzeciona, niskie momenty gnące i skręcające, do automatycznej wymiany, łatwe wyważanie
- Typ F: Obróbka ze średnimi prędkościami, obróbka miękkich materiałów, średnie momenty gnące i skręcające, do automatyczny wymiany, łatwe wyważanie
- Typ T: Zastosowania obrotowe i nieobrotowe wymagające dokładnych tolerancji, wykorzystujące rowek prowadzący do ustawienia narzędzia. Ze względu na brak konieczności użycia „szyjki" można uzyskać wyższe momenty gnące
Uwaga! Większość obrabiarek ze złączem HSK-T nadal wymaga szyjki dla chwytaka automatycznego zmieniacza narzędzi i magazynu narzędzi; z tego powodu, konieczne jest stosowanie narzędzi HSK A/C/T
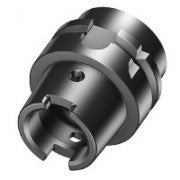
A
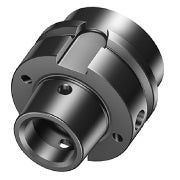
B
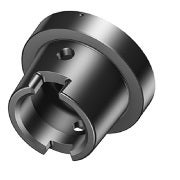
C
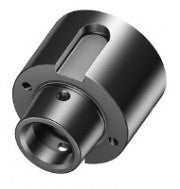
D
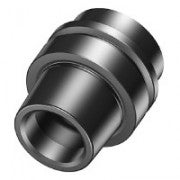
E
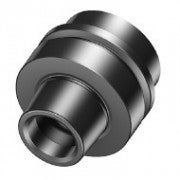
F
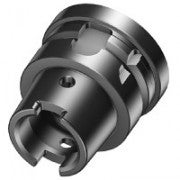
T
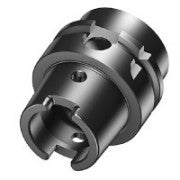
A/C/T
Coromant Capto®
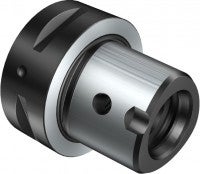
Złącze Coromant Capto® (ISO 26623) łączy w sobie zalety HSK i BIG-PLUS®, ale bez konieczności stosowania zabieraków. Połączenie występuje na powierzchni stożka o przekroju trygonalnym i za pomocą styku na powierzchni czołowej kołnierza. Przekrój tego mocnego złącza zapewnia wystarczającą ilość miejsca na mocowanie segmentowe charakteryzujące się bardzo dużą siłą mocującą, wyjątkową wytrzymałością na zginanie oraz skręcanie i dokładnością pozycjonowania w osi.
Mniejsze odchyłki bicia promieniowego i lepsze przenoszenie momentu obrotowego były wymagane w trzech docelowych obszarach zastosowań:
- Złącze wrzeciona – centra obróbkowe i tokarki pionowe
- Złącze modułowe – centra obróbkowe
- System szybkiego mocowania w przypadku ręcznej zmiany narzędzi – tokarki
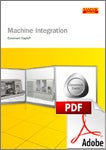
Coromant Capto® jest najczęściej stosowanym złączem do obrabiarek wielozadaniowych, gdyż nadaje się zarówno do zastosowań statycznych (toczenie) i obrotowych (frezowanie/wiercenie).

Zalecenia odnośnie wrzeciona dla różnych typów obrabiarek
Centra obróbkowe (tylko obrotowe)
Zaleca się używanie wrzeciona obrabiarki ze stykiem na czole kołnierza. Złącza BIG-PLUS® i HSK-A zapewniają wystarczającą stabilność w większości zastosowań obrotowych. Do ciężkiej obróbki należy rozważyć zastosowanie Coromant Capto® C10, ewentualnie jednego z dużych złączy, np. HSK-A 125 czy SK60. Do obróbki z dużymi prędkościami obrotowymi może być wskazane użycie złącza HSK-E lub F.
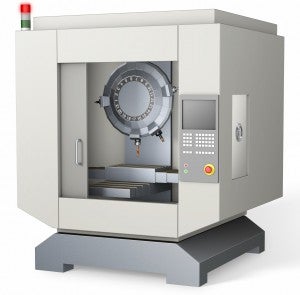
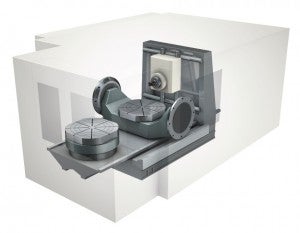
Obrabiarki wielozadaniowe (narzędzia nieobrotowe i obrotowe)
Coromant Capto® to jedyne złącze spełniające wymagania w zakresie momentu skręcającego i gnącego dla zastosowań nieobrotowych i obrotowych.
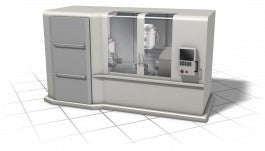

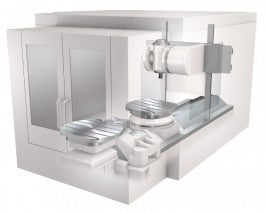
Istnieją różne sposoby mocowania wrzeciona oraz techniki wykonania złączy wrzeciona. Sandvik Coromant działa aktywnie na rzecz integracji złączy Coromant Capto® z obrabiarkami, aktywnie współpracując z producentami obrabiarek. Koncentrujemy się głównie na tych typach obrabiarek i złączy, w których zastosowanie Coromant Capto® przyniesie największe korzyści.
C3 | C4 | C5 | C6 | C8 | C10 | |
Centrum tokarskie | * | * | ||||
Tokarki do ciężkiej obróbki | ||||||
Tokarki karuzelowe | ||||||
Obrabiarki wielozadaniowe | ||||||
Centra obróbkowe z możliwością toczenia | ||||||
Centra obróbkowe do ciężkiej obróbki |
* Długie wytaczaki do dużych centrów tokarskich
Porównanie siły mocującej
Wewnętrzne mocowanie segmentowe stosowane w złączach HSK i Coromant Capto® (typu stożek pusty w środku) zapewnia większą siłę mocującą niż śruba ściągająca stosowana do mocowania zwykłych stożków. W tabeli przedstawiono wartości siły mocującej działającej na poszczególne rodzaje złączy. Dzięki większemu polu przekroju poprzecznego i długości, złącze Coromant Capto® zapewnia znacznie większą siłę mocującą niż HSK-A.
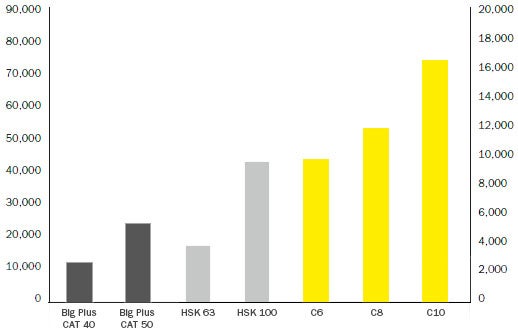
Źródła: HSK Handbook, copyright 1999.
Big Daishowa (system Big plus)
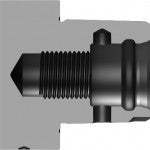
Coromant Capto®
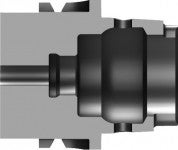
HSK-A
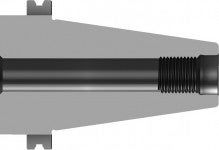
Stożek (SK)
Porównanie przenoszenia momentu obrotowego i wytrzymałości na zginanie
Stożek 7/24 – zabieraki na dużym promieniu zapewniają odpowiedni napęd do zastosowań obrotowych
HSK-A – złącze niezalecane do zastosowań, w których występuje duży moment obrotowy ze względu na małą powierzchnię styku z zabierakami występującymi na stożku, a nie na kołnierzu (mały promień).
Coromant Capto® – obróbka tokarska wymaga dokładnego ustawienia ostrza na poziomie osi obrotu, którą zapewnia złącze o trygonalnym kształcie przekroju poprzecznego.
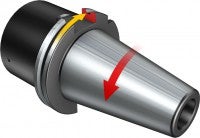
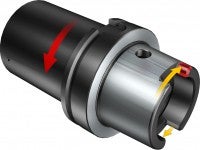
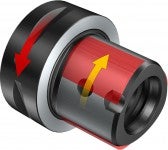
Rozmiar złącza będzie wiązał się z ograniczeniami wytrzymałości na zginanie i maksymalnej prędkości obrotowej. Duże złącze to duża wytrzymałość, ale mała prędkość obrotowa, natomiast małe złącze to duża prędkość obrotowa, ale mniejsza wytrzymałość.
Na wykresie poniżej przedstawiono obliczone teoretycznie (metodą elementów skończonych) ograniczenia różnych złączy w przypadku utraty powierzchni styku (wytrzymałość na zginanie) i osiągnięcia granicy wytrzymałości zmęczeniowej (maks. moment skręcający).
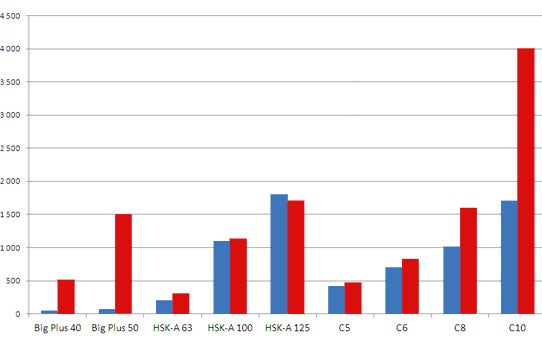
Niebieski: Maksymalny moment gnący (Nm)
Czerwony: Maksymalny moment skręcający (Nm) w granicach wytrzymałości zmęczeniowej
Złącza BIG-PLUS® i HSK zapewniają wystarczającą stabilność w większości zastosowań obrotowych, ale w przypadku obrabiarek wielozadaniowych Coromant Capto® to jedyne złącze spełniające wymagania w zakresie wytrzymałości na skręcanie i zginanie.
Sprzęg | Wielkość i typ mocowania | Siła mocująca (śruba ściągająca lub cięgno) | Maksymalna prędkość obrotowa (w zależności od wrzeciona i łożysk) | |
N | lbs | |||
BIG-PLUS® ISO/CAT/BT ze stożkiem 7/24 | Stożek 40 | 12000 | 2703 | 16000 |
Stożek 50 | 24000 | 5405 | 12000 | |
HSK-A | HSK-A 63 | 18000 | 4054 | 20500 |
HSK-A 100 | 45000 | 10135 | 12500 | |
HSK-A 125 | 70000 | 15766 | 9500 | |
Coromant Capto® | C5 | 32000 | 7207 | 28000 |
C6 | 41000 | 9234 | 20000 | |
C8 | 50000 | 11261 | 14000 | |
C10 | 70000 | 15766 | 10000 |
Próby statyczne w celu porównania wytrzymałości na zginanie i skręcanie
W laboratorium WZL renomowanej uczelni RWTH w Aachen (Niemcy) przeprowadzono serię prób statycznych z użyciem obrabiarek. Ich celem było porównanie różnych złączy wrzecion pod kątem wytrzymałości na zginanie i skręcanie.
Pomiary złącza Coromant Capto® przeprowadzono dla dwóch wielkości siły mocującej: takiej samej, jak dla złącza HSK-A (22 kN dla złącza C6 i 50 kN dla złącza C10) oraz większej (45 kN dla złącza C6 i 80 kN dla złącza C10).
Stabilność przy zginaniu
Ugięcie [mm/m]
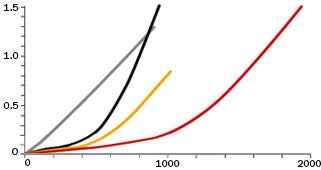
Moment gnący [Nm]




C6 - 45 kN
C6 - 22 kN
HSK-A 63 - 22 kN
Stożek 7/24, wielkość 40 - 15 kN
Stabilność przy zginaniu
Ugięcie [mm/m]
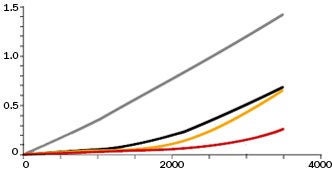
Moment gnący [Nm]




C10 - 80 kN
C10- 50 kN
HSK-A 100 - 50 kN
Stożek 7/24, wielkość 50 - 25 kN
Wyniki wykazały, że nawet po przyłożeniu takiej samej siły mocującej, jak dla złącza HSK-A, mocniejsze złącze ma większą wytrzymałość na zginanie. Przy większej sile mocującej do wybicia złącza C6 konieczne było użycie siły 2,88 raza większej niż dla złącza HSK-A 63, a dla złącza C10 - 2,15 raza większej niż dla złącza HSK-A 100.
Stabilność przy skręcaniu
Ugięcie [mm/m]
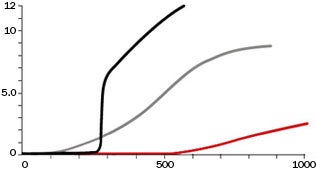
Moment skręcający [Nm]



C6- 46kN
HSK-A 63 - 22 kN
Stożek 7/24, wielkość 40 - 15 kN
Stabilność przy skręcaniu
Ugięcie [mm/m]
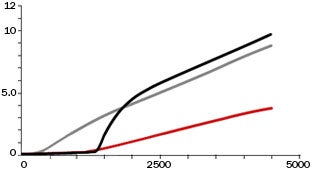
Moment skręcający [Nm]



C10- 50 kN
HSK-A 100 - 50 kN
Stożek 7/24, wielkość 50 - 25 kN
Wykresy pokazują, że złącze Coromant Capto® C6 ma 2,29 większą wytrzymałość na skręcanie niż złącze HSK-A 63. Uzyskano 7,1 raza lepszy kąt skręcenia. Dla złącza C10 uzyskano odpowiednio 1,85 raza lepszą wytrzymałość skręcanie i 4,0 lepszy kąt w porównaniu do złącza HSK-A 100.