Informacje o chłodziwie – obróbka z użyciem chłodziwa
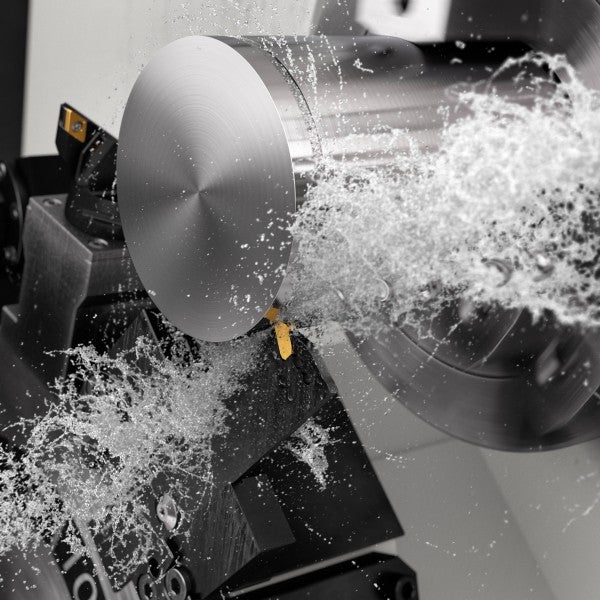
W niektórych przypadkach z ekologicznego i ekonomicznego punktu widzenia korzystna może być eksploatacja obrabiarki bez chłodziwa (obróbka na sucho). Wiele zastosowań wymaga jednak użycia chłodziwa ze względu na konieczność uzyskania odpowiedniej tolerancji wykonania, chropowatości powierzchni i skrawalności. W zastosowaniach wymagających chłodziwa należy zoptymalizować jego użycie, aby jak najlepiej wykorzystać jego możliwości.
Podawanie chłodziwa pod wysokim ciśnieniem
W prawie wszystkich obrabiarkach chłodziwo można dostarczać pod standardowym wysokim ciśnieniem wynoszącym około 70/80 bar (1015/1160 psi). W niektórych obrabiarkach chłodziwo może być dostarczane pod jeszcze wyższym ciśnieniem, wynoszącym 150 bar (2176 psi), do wymagających czynności i zastosowań.
Mimo niezaprzeczalnych korzyści płynących z użycia chłodziwa w obróbce tokarskiej i wiertarskiej, warto podkreślić, że:
- Korzyści zapewnią wyłącznie narzędzia przystosowane do precyzyjnego podawania chłodziwa pod wysokim ciśnieniem, tj. wiertła umożliwiające podawanie chłodziwa przez narzędzie i narzędzia tokarskie z kontrolowanym kierunkiem strumieni chłodziwa
- W przypadku narzędzi tokarskich, ciśnienie chłodziwa wymagane do łamania wiórów zależy od konstrukcji dyszy podającej chłodziwo, obrabianego materiału oraz głębokości skrawania i posuwu
- Wymagane natężenie przepływu chłodziwa zależy od ciśnienia i całkowitej powierzchni przekroju kanałów doprowadzających chłodziwo
Należy wybrać właściwe narzędzia i pompę (ciśnienie i przepływ objętościowy) dla każdego zastosowania. Prawidłowo zastosowany układ doprowadzania chłodziwa pod wysokim ciśnieniem zapewni szybki zwrot z inwestycji dzięki większemu stopniowi wykorzystania obrabiarki i zwiększeniu wydajności skrawania metalu.
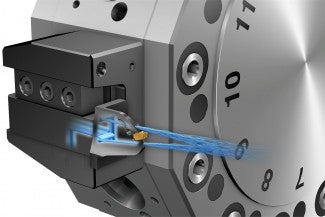
Korzyści płynące z zastosowania chłodziwa do obróbki
Dzięki połączeniu wysokiego ciśnienia ze zoptymalizowanymi narzędziami skrawającymi i rozwiązaniami szybkowymiennymi odniesiesz liczne korzyści.
Kontrola wiórów w przecinaniu i rowkowaniu
Możliwość wyeliminowania dwóch czynników generujących najdłuższe przerwy w produkcji.
- Przestoje w obróbce: długie wióry gromadzą się wokół narzędzia lub obrabianego przedmiotu
- Napraw: wióry zablokowane w przenośniku wyłączają obrabiarkę z produkcji na długie godziny lub dni
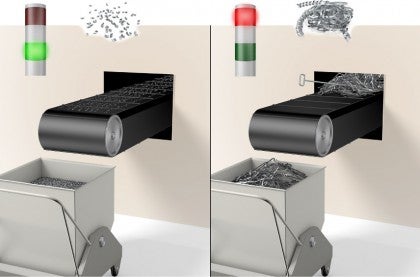
Odprowadzanie wiórów podczas wiercenia
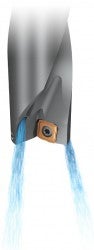
Wewnętrzne doprowadzenie chłodziwa (przez narzędzie) ułatwia odprowadzanie wiórów i zapobiega ich zakleszczaniu się w rowku wiórowym.
Nieruchome dysze
Brak konieczności wprowadzania ustawień przez operatora, co oznacza większy stopień wykorzystania obrabiarki.
Większa prędkość skrawania
Znacznie większa wydajność skrawania metalu.
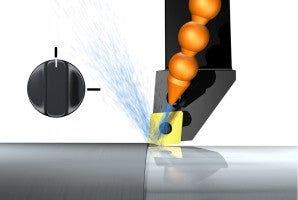
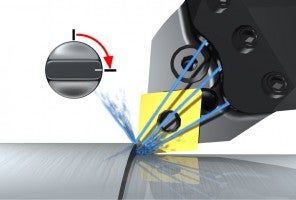
Precyzyjne doprowadzanie chłodziwa pod wysokim ciśnieniem
Wysokie ciśnienie chłodziwa w obrabiarce w połączeniu z nowoczesnymi narzędziami tokarskimi wyposażonymi w dysze zapewniają uformowanie strumienia chłodziwa o wysokiej prędkości. Strumienie chłodziwa są kierowane w stronę strefy skrawania na stronę natarcia płytki i działają niczym klin hydrauliczny, który unosi wiór. Skrócenie kontaktu płytki z materiałem pozwala zmniejszyć siły skrawania, obniżyć temperaturę i poprawić kontrolę wiórów.
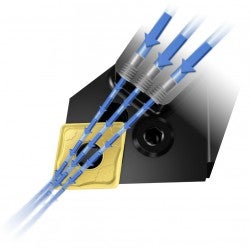
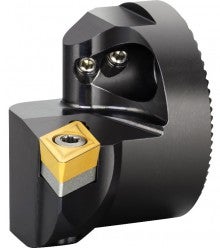
Zasady podawania chłodziwa pod wysokim ciśnieniem
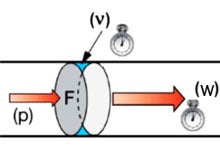
Ciśnienie (p): Siła działająca na jednostkę powierzchni
- Paskal, N/m
- Bar (1 bar = 0.1 MPa)
- psi, funty/cal2 (1 bar = 14.5 psi)
Natężenie przepływu chłodziwa (v): ilość chłodziwa podawana w jednostce czasu, litr/min (galonów/min)
Prędkość strumienia chłodziwa (w): prędkość przepływu cieczy przez przewód, m/s (stóp/s)
Zmniejszenie przekroju przewodu podającego chłodziwo przy określonym ciśnieniu prowadzi do zwiększenia prędkości strumienia chłodziwa i zmniejszenia natężenia jego przepływu. Dysze o odpowiednio dobranej, małej średnicy pozwalają uzyskać dokładny, laminarny strumień cieczy.
Prędkość strumienia chłodziwa w1

Prędkość strumienia chłodziwa w1
w2>>w1

Na wykresie poniżej przedstawiono zależność natężenia przepływu cieczy od średnicy wylotu dyszy przy stałym ciśnieniu 80 bar (1160 psi). Dysze o małej średnicy pozwalają uzyskać dużą prędkość strumienia chłodziwa, nie wymagając od układu zasilania dużego natężenia przepływu i mocy w porównaniu do tradycyjnych systemów podawania chłodziwa.
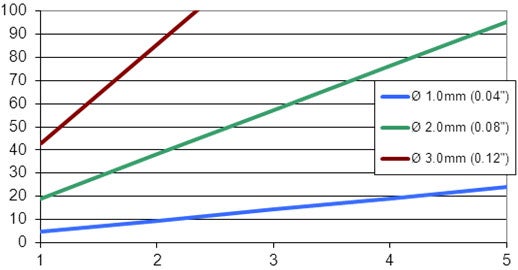
Oś X: Liczba dysz
Oś y: Natężenie przepływu, litrów/min
Wymagania dotyczące pompy
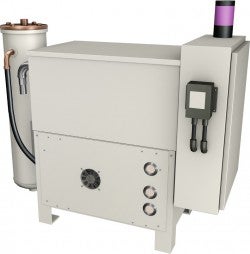
Wymagania dotyczące pompy do skutecznej obsługi systemu podawania chłodziwa pod wysokim ciśnieniem są następujące dotyczą ciśnienia i natężenia przepływu.
Ciśnienie
Ciśnienie wymagane do odłamania wióra jest różne w zależności od materiału i parametrów skrawania. 80 bars (1160 psi) to ciśnienie wystarczające w większości zastosowań. Wyższe ciśnienie (do 150 bar (2176 psi) jest stosowane w obróbce materiałów mało podatnych na łamanie wióra, np. Inconelu czy stali Super Duplex
Natężenie przepływu chłodziwa
Wymagane natężenie przepływu chłodziwa zależy od liczby i średnicy jego wylotów.
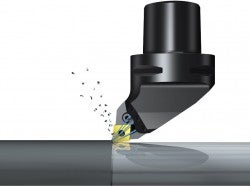
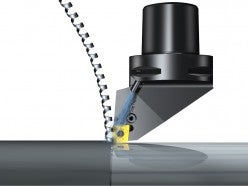
- Używać filtra 20 mikrometrów
- Toczenie: W przypadku korzystania z uchwytów narzędzie z trzema dyszami chłodziwa 1 mm (0.039 cala), wymagane natężenie przepływu wynosi 20 litres/min na każdą pozycję narzędzia. Warto jednak wziąć pod uwagę liczbę narzędzi zasilanych równocześnie chłodziwem (liczba narzędzi x 20 litrów/min). Ze względu na rozmiary obrabiarki, potrzebny jest duży zbiornik zapewniający czas na rozprowadzenie chłodziwa
- Wiercenie: Średnica kanaliku chłodziwa w wiertle wzrasta wraz ze średnicą wiertła, co oznacza, że wiertła o większej średnicy wymagają większego natężenia przepływu chłodziwa. Celem jest natężenie przepływu, a nie ciśnienie. Zalecane jest stosowanie pompy zmiennociśnieniowej oraz niższych wartości ciśnienia przy większych średnicach wierteł
Średnica wiertła | 20 l/min | 40 l/min |
12 | 70 bar | 70 bar |
20 | 30 bar | 70 bar |
25 | 12 bar | 50 bar |
30 | 6 bar | 23 bar |
40 | 1 bar | 3 bar |
60 | | 1 bar |
Złącze chłodziwa
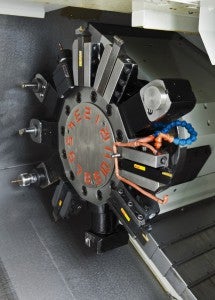
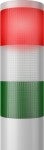
Jedną z największych zalet systemów podawania chłodziwa pod wysokim ciśnieniem jest ograniczenie konieczności ustawiania rurek doprowadzających chłodziwo. W przypadku rurek biegnących na zewnątrz, prawidłowe ustawienie strumienia chłodziwa wymaga zazwyczaj dwóch lub trzech prób. Przy niekorzystnej kontroli wiórów rurki często ulegają zatkaniu, dlatego regularnie trzeba korygować ustawienie, co wiąże się z małą przewidywalnością przebiegu skrawania i przerwami w obróbce.
Zastosowanie uchwytów narzędzi z dyszami precyzyjnymi sprawia, że warunki pracy ostrza są niezmienne w czasie, ale mimo to konieczne jest zasilanie w chłodziwo oprawek. Można do tego celu użyć rurek połączeniowych mocowanych w oprawce z chwytem tradycyjnym, należy jednak pamiętać, że takie rozwiązanie zwiększy czas obsługi technicznej przy każdej zmianie oprawki, istnieje też ryzyko kolizji i gromadzenia się wiórów.
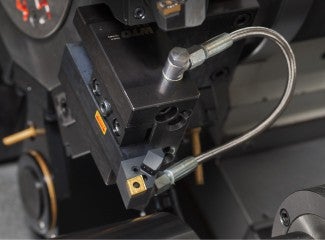
Najlepszym sposobem jest użycie szybkowymiennego rozwiązania typu „podłącz i używaj”. Chłodziwo jest stale doprowadzane do uchwytu mocującego oprawki narzędziowej. To rozwiązanie jest korzystne także ze względu na krótszy czas ustawiania, lepszą kontrolę wiórów i większą efektywność obróbki.
Podłączanie doprowadzania chłodziwa do centrów tokarskich i tokarek
W uchwytach mocujących Coromant Capto® chłodziwo jest doprowadzane przez tuleję zaciskową, umożliwiając szybką wymianę i wstępny pomiar na zewnątrz obrabiarki. Dostępne są uchwyty mocujące dla wszystkich typów tokarek (centrów tokarskich, tokarek pionowych i tokarek o poziomym łożu), a nowe zestawy mocujące umożliwiają zastosowanie ciśnienia 200 bar (2900 psi).
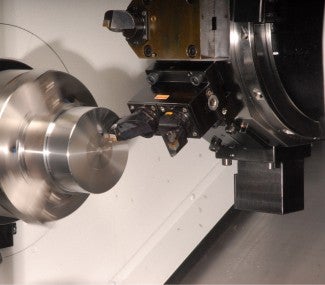
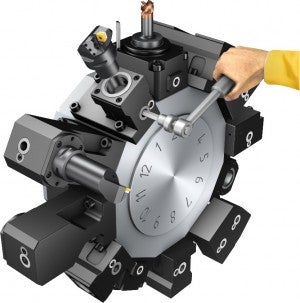
Podłączanie doprowadzania chłodziwa w obrabiarkach z przesuwną głowicą
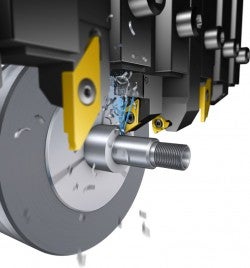
Podawanie chłodziwa w obrabiarce z przesuwną głowicą przebiega inaczej niż w centrum tokarskim. Częściej stosuje się olej syntetyczny niż emulsję, odpowiednio do konstrukcji przesuwnej prowadnicy, a ciecz obróbkowa jest doprowadzana do wszystkich narzędzi jednocześnie, niezależnie od tego, które z nich w danym momencie jest zagłębione w materiał.
Wprawdzie większość obrabiarek jest wyposażona w pompy wysokociśnieniowe, ale bez specjalnych narzędzi sumaryczna powierzchnia przekroju kanalików podających chłodziwo (pole wylotu chłodziwa × liczba wylotów) będzie zbyt duża w stosunku do wydajności pompy, co uniemożliwi zapewnienie maksymalnego ciśnienia.
Wskazane jest ograniczenie powierzchni przekroju kanalików podających chłodziwo poprzez:
- Zastosowanie narzędzi umożliwiających wewnętrzne podawanie chłodziwa i zablokowanie zewnętrznego podawania chłodziwa do tych narzędzi
- Dobór optymalnej powierzchni przekroju kanalików podających chłodziwo w celu zminimalizowania natężenia przepływu chłodziwa
System oprawek QS™ obejmuje oprawki narzędziowe, w których chłodziwo doprowadzane do ogranicznika zamontowanego na stałe w obrabiarce. W momencie zamocowania narzędzia, umieszczona z tyłu oprawki QS™ rurka doprowadzająca chłodziwo kieruje je prosto do dysz.
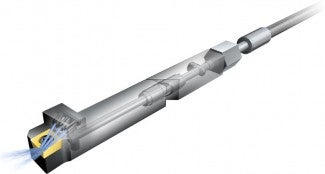
Dysze mają średnicę 1 mm (0.039 cala), a wydobywający się z nich precyzyjny strumień chłodziwa zapewnia odpowiednią kontrolę wiórów i najmniejsze użyteczne natężenie przepływu chłodziwa.
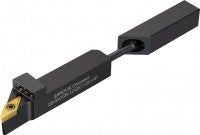
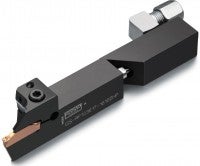
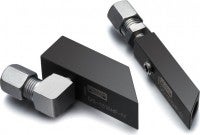
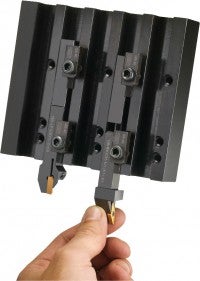
Tuleje do szybkiego ustawiania wytaczaków z chwytem cylindrycznym (walcowym)
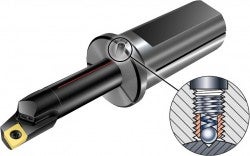
Szczelne metalowe tuleje przystosowane do wysokiego ciśnienia chłodziwa, takie jak EasyFix, umożliwiają szybkie ustawienie wytaczaków z chwytem cylindrycznym. Napinana sprężyną kulka zapada się w rysę na trzonku wytaczaka, dzięki czemu ustawienie ostrza w osi zajmuje kilka sekund.