Rozwiązania służące do szybkiej wymiany narzędzi
W potocznym rozumieniu pojęciem produktywności często określa się efektywność obróbki. Tymczasem wykorzystanie obrabiarki (czyli czas, w którym świeci się zielona lampka) ma równie istotne, a nawet większe znaczenie.
Dzięki szybkowymiennemu rozwiązaniu narzędziowemu można naprawdę zwiększyć stopień wykorzystania maszyny poprzez skrócenie czasu pomiaru, nastawy i zmiany narzędzia.
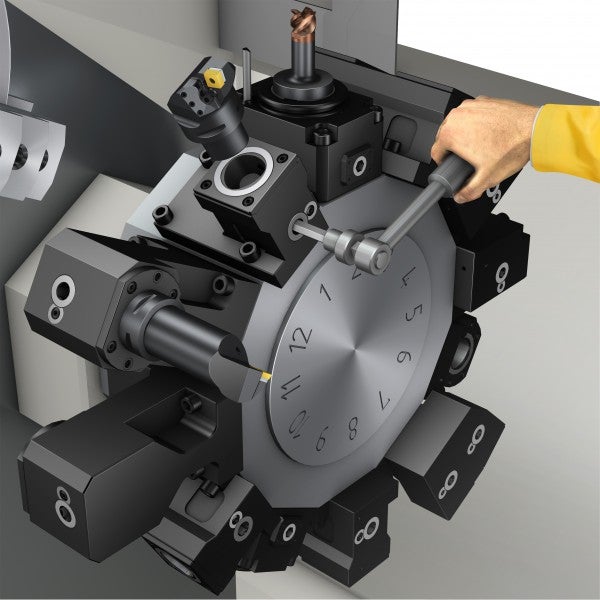
Czynniki wpływające na produktywność
Produktywność to liczba przedmiotów produkowanych podczas jednej zmiany lub w ciągu tygodnia pracy. Ważne jest, by zidentyfikować obszary rokujące największą poprawę przed wyborem konkretnych rozwiązań. Należy uwzględnić dwa główne czynniki:
- Efektywność obróbki materiału – mierzona wydajnością skrawania (cm3/min (cal3/min) danego rodzaju obróbki
- Wykorzystanie obrabiarki – określane ilością czasu, w którym świeci się zielony sygnalizator na obrabiarce (zdolność do podtrzymywania ciągłej produkcji przez dłuższy czas)
Wykorzystanie obrabiarki zależy w dużej mierze od jej konfiguracji i rozwiązań opcjonalnych. Zagadnienia te należy rozważyć przed zakupem nowej obrabiarki, aby mieć gwarancję wykorzystania najlepszych technologii.
W zakładzie produkcyjnym najwięcej czasu zajmuje zwykle:
- Ustawienie systemu przed rozpoczęciem produkcji partii
- Pomiar przedmiotu w obrabiarce
- Ustawienie narzędzia w obrabiarce
- Ustawienie rurek doprowadzających chłodziwo
- Zmiana zużytych narzędzi
- Usunięcie wiórów zgromadzonych wokół narzędzi lub blokujących przenośniki
- Zmiana przedmiotu
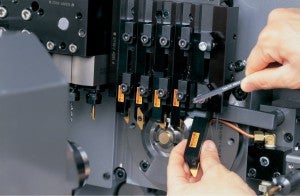
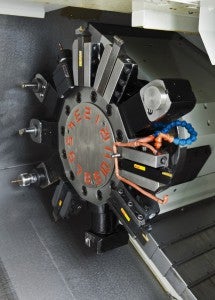
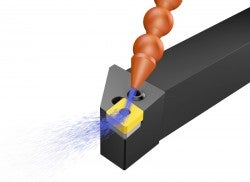
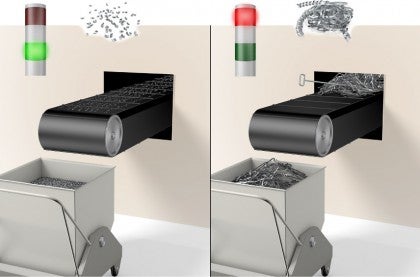
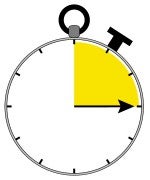
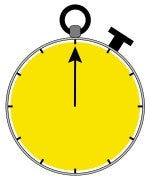
Sposób montażu i pomiaru narzędzi ma istotny wpływ na wykorzystanie obrabiarki. Podobnie jak na wyścigach samochodowych dąży się do skrócenia przerwy technicznej, tak i przy obróbce ważne jest, by ograniczyć przestoje obrabiarki do minimum.
System doprowadzania chłodziwa przez narzędzie daje możliwość współpracy obrabiarki z optymalnie dobranymi narzędziami skrawającymi w pełnym zakresie możliwości, dzięki czemu czas ustawiania ulega skróceniu, a chłodziwo jest podawane z dużą efektywnością poprawiającą kontrolę wiórów.
Korzyści płynące z zastosowania narzędzi szybkowymiennych
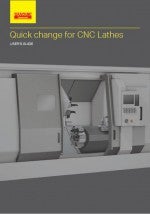
Tokarki numeryczne i obrabiarki z przesuwną głowicą posiadają systemy do szybkiej wymiany ostrza, ale ze względu na długi czas wymiany i ustawienia narzędzia wykorzystanie ich możliwości jest zwykle gorsze niż w przypadku centrów obróbkowych. Jeśli obrabiarka nie jest wyposażona w funkcję automatycznej wymiany narzędzi (ATC), stosowane są ręczne rozwiązania szybkomocujące, sprzyjające wydłużeniu czasu gotowości do produkcji. Stosowanie rozwiązań szybkowymiennych przynosi liczne korzyści.
Skrócenie czasu przestawienia obrabiarki na produkcję nowej partii dzięki zestawom narzędzi
Znaczne skrócenie czasu zmiany z jednego typu narzędzia na drugi.
- Oprawki tokarskie: z 5-10 minut do 30 sekund
- Wymiana wytaczaków zajmuje nieco więcej czasu niż wymiana noży tokarskich z chwytem tradycyjnym, ponieważ konieczne jest ustawienie ostrza narzędzia w osi i podłączenie chłodziwa
- Zalety zastosowania narzędzi szybkowymiennych są jeszcze większe w połączeniu z długimi wytaczakami. Wytaczaki o wymiarach do 10×D można wymieniać z dokładnością do 2 μm (78.7 mikrocala) w czasie krótszym niż 1 minuta
- Narzędzia z napędem: z 5-20 min. do 30 sekund. W zastosowaniach obrotowych najczęściej spotyka się oprawki na tuleje zaciskowe lub trzpienie frezarskie. Tuleje zaciskowe można stosować wyłącznie z frezami trzpieniowymi o średnicy maks. 25 mm (1 cal); dla większych narzędzi potrzebny jest drugi uchwyt z napędem. Uchwyt Coromant Capto® nadaje się natomiast do dowolnych zastosowań
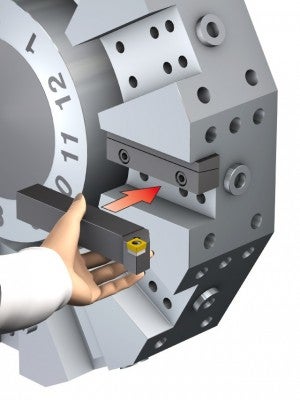
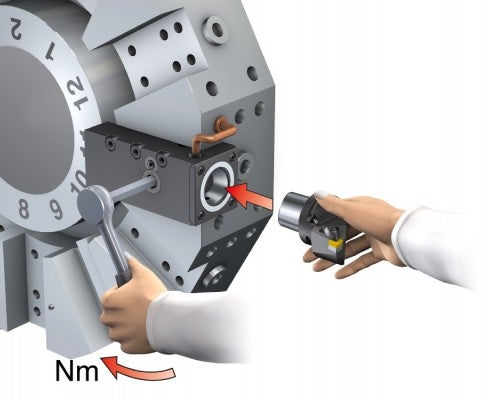
Mniejsza liczba zajmowanych pozycji w magazynie
Zwiększenie liczby gniazd narzędzi dzięki podwójnym uchwytom – możliwość wykorzystywania imaków do obróbki wewnętrznej i zewnętrznej.
Centra tokarskie wykorzystujące oprawki napędzane często charakteryzuje ograniczona przestrzeń. Zastosowanie podwójnych uchwytów mocujących umożliwia użycie narzędzi bliźniaczych lub większego asortymentu narzędziowego, a w rezultacie ograniczenie konieczności zmiany narzędzi dla większego zakresu przedmiotów. Zastosowanie podwójnych uchwytów mocujących jest możliwe, jeśli obrabiarka posiada oś Y, możliwość użycia pośrednich pozycji na głowicy rewolwerowej lub wrzeciono pomocnicze.
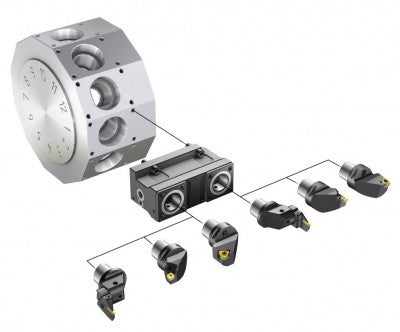
Skrócenie czasu wymiany stępionego narzędzia
Uchwyty przenoszące napęd: przy każdej wymianie narzędzia pełnowęglikowego konieczna jest ponowna kalibracja przesunięcia narzędzia. Frezy/wiertła na płytki wymienne wymagają wymiany kilku płytek. Narzędzia bliźniacze i zmiana frezu poza obrabiarką to znacznie szybsza opcja.
Oprawki nieobrotowe: wymiana pojedynczej, łatwo dostępnej płytki bezpośrednio w obrabiarce może trwać równie krótko. Jednak możliwość demontażu narzędzia zapewnia lepszą konserwację narzędzia, prawidłowy montaż i brak nieoczekiwanych przestojów spowodowanych koniecznością zakupu części zamiennych.
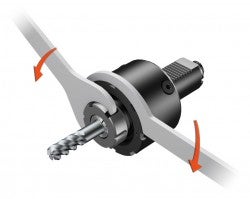
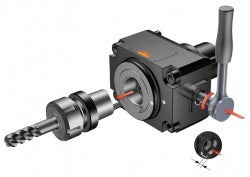
Eliminacja czynności ustawiania rurek doprowadzających chłodziwo
W zależności od zastosowania, prawidłowe ustawienie kierunku strumienia chłodziwa przez operatora wymaga zazwyczaj 2-3 prób, co wiąże się z przerwą w obróbce! Rurki często zmieniają pozycję w wyniku uderzeń niepołamanych wiórów, dlatego regularnie trzeba korygować ich ustawienie.
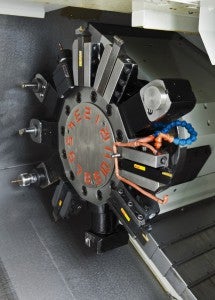
Szybsze wznowienie produkcji
Dzięki wyeliminowaniu próbnej obróbki i przejścia pomiarowego wzrasta produktywność i maleje liczba wybraków. W skali roku, użycie rozwiązań szybkowymiennych pozwala zwiększyć liczbę wykonanych przedmiotów i ograniczyć odsetek wybraków.
- Obróbka próbna – w produkcji dużych partii: pierwszy przedmiot obrabiany po zmianie narzędzia często jest wybrakiem, dlatego do czasu zmiany narzędzia należy zaliczać: zmianę narzędzia (utrzymanie starego przesunięcia), skrawanie całego detalu, pomiar skończonego przedmiotu i regulację przesunięcia
- Przejście pomiarowe – w produkcji małych/średnich partii: wykonanie przejścia pomiarowego z wycofaniem przesunięcia gwarantuje, że przedmiot nie będzie wybrakowany, natomiast zajmuje więcej czasu. Do czasu zmiany narzędzia należy zaliczać: zmianę narzędzia, odsunięcie przesunięcia, skrawanie, pomiar i regulację przesunięcia
Metoda ta jest ergonomiczna i łatwa do zastosowania przez operatora
Szybka wymiana ma liczne zalety z punktu widzenia operatora, na przykład wymiana narzędzi poza obrabiarką zmniejsza liczbę wypadków, błędów i detali, które zostały upuszczone i trzeba ich szukać. Jest również łatwa do standaryzacji dla wszystkich typów obrabiarek.
Szybka wymiana noży w obrabiarkach z przesuwną głowicą
Ze względu na kompaktowe rozmiary obrabiarek z przesuwną głowicą, obrabiarki te dysponują ograniczoną ilością miejsca na ustawienie i zmianę narzędzi. Narzędzia z chwytem tradycyjnym wymagają często wyjęcia z imaka w celu zmiany ostrza płytki, co wydłuża czas ustawiania w porównaniu z konwencjonalnymi centrami tokarskimi.
Rozwiązanie szybkowymienne, takie jak System mocowania QS™ pozwala maksymalnie wykorzystać czas produkcji na obrabiarkach z przesuwną głowicą względem chwytów tradycyjnych. Narzędzie można wyjąć z obrabiarki w celu zmiany płytki, a następnie szybko i dokładnie wznowić pracę bez konieczności ustawiania/pomiaru.
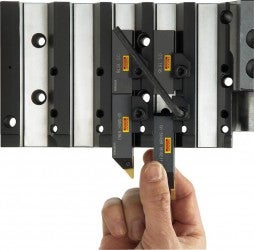
Szybkie ustawianie wytaczaków
Ustawianie wytaczaków w głowicy rewolwerowej zajmuje więcej czasu w porównaniu do narzędzi z chwytem o przekroju prostokątnym ze względu na ich długość/konieczność ustawienia ostrza w osi i doprowadzenia chłodziwa z tyłu narzędzia.
Tuleje, np. EasyFix, umożliwiają szybkie, łatwe i poprawne ustawienie ostrza wytaczaka z chwytem walcowym w osi podczas jego mocowania w obrabiarce. Sprężysty zatrzask umieszczony w tulei z łatwością wpada w rowek nacięty na wytaczaku zapewniając poprawne ustawienie narzędzia w osi i obróbkę ze stałą, wysoką jakością.
Tuleja jest dostępna w wersji z metalowym uszczelnieniem do podawania chłodziwa pod wysokim ciśnieniem oraz w wersji klasycznej z rowkiem wypełnionym uszczelniaczem silikonowym do zastosowań wykorzystujących chłodziwo pod niskim ciśnieniem.
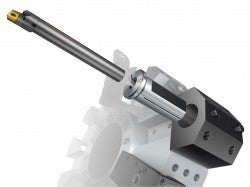
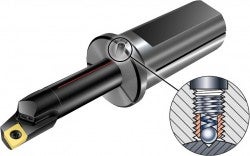
Do szybkiego mocowania system narzędziowy z Coromant Capto®
Coromant Capto® to modułowe rozwiązanie szybkowymienne, które zapewnia maksymalne wykorzystanie obrabiarki, jak i maksymalną wydajność skrawania metalu. Poniżej wymienione są kluczowe korzyści płynące z zastosowania złącza Coromant Capto®.
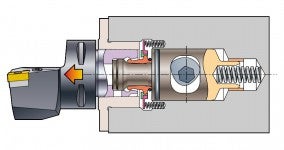
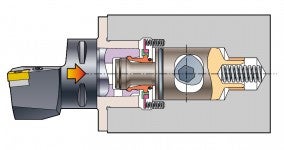
Mocowanie tuleją segmentową
Cięgno poruszane krzywką służy do zablokowania złącza za pomocą tulei segmentowej oraz do wypychania stożka z gniazda. W celu ręcznego zablokowania i odblokowania uchwytu mocującego wystarczy wykonać obrót śrubą. Krzywka jest wyposażona w mechanizm samoczynnej blokady, który chroni przed otwarciem podczas obróbki.
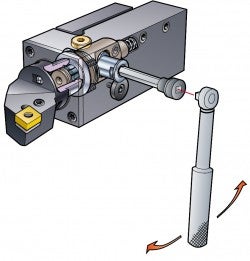
Powtarzalność
Precyzja i samocentrująca konstrukcja złącza zapewniają powtarzalność ustawienia narzędzia skrawającego (wtyk ze złączem męskim) w tym samym uchwycie (gniazdo ze złączem żeńskim) z dokładnością poniżej ±2 mikrometrów w osiach x, y oraz z.
Dzięki temu możliwe jest wstępne ustawienie narzędzia poza obrabiarką przy produkcji dużych partii lub zestawu narzędzi przy przestawianiu obrabiarki na produkcję nowej partii. W obu przypadkach możliwe jest wyeliminowanie przejścia pomiarowego, szybsze wznowienie produkcji i ograniczenie odsetka wybraków.
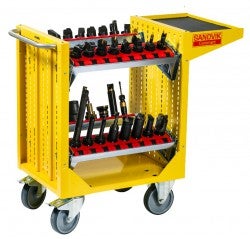
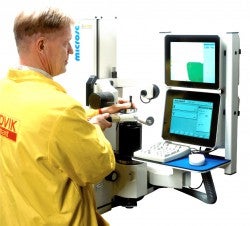
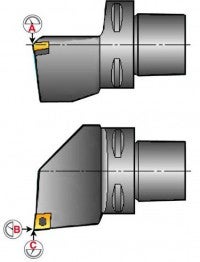
Lepsza stabilność
Stabilność złącza określają takie parametry, jak wytrzymałość na zginanie i skręcanie (przenoszenie momentu obrotowego). Czynniki zapewniające dobrą stabilność to:
- Styk czoła i stożka: przeciwstawia się momentom zginającym i zapewnia precyzyjne pozycjonowanie
- Złącze poligonalne: przenoszenie momentu obrotowego odbywa się poprzez dużą powierzchnię styku, bez pośrednictwa sworzni czy wpustów. Moment skręcający rozkłada się równomiernie w każdym kierunku, a właściwości samocentrujące trygonalnego stożka zapewniają dokładne ustawienie ostrza płytki na poziomie osi obrotu
- Duża siła zacisku: pewne mocowanie tuleją segmentową charakteryzuje się dużą siłą mocującą, a dwie powierzchnie styku zapewniają wytrzymałość na zginanie podczas obróbki
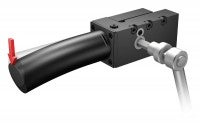
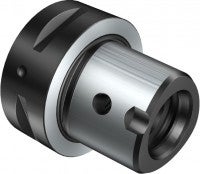
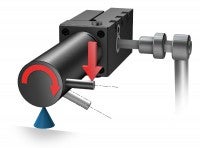
Dowiedz się więcej o skręcaniu (przenoszenie momentu obrotowego) i wytrzymałości na zginanie
Asortyment uchwytów mocujących
Szybkomocujące złącza C3-C10 są wykorzystywane w tokarkach numerycznych. Wielkość złącza zależy od wielkości obrabiarki i parametrów skrawania.
Istnieją różne złącza do tokarek z ramieniem pionowym; blok mocowanych ręcznie uchwytów ze złączami mocującymi Coromant Capto® jest dostarczany przez producenta obrabiarki z maszyną lub zamawiany osobno jako specjalny system.
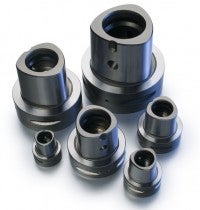
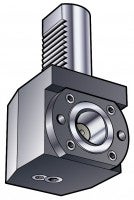
VDI-DIN 69880
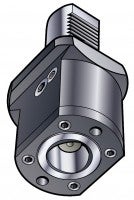
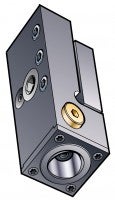
Chwyt
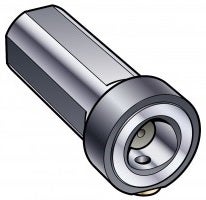
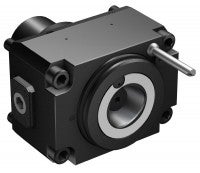
CBI (Mocowanie śrubami)
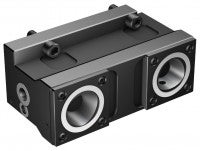
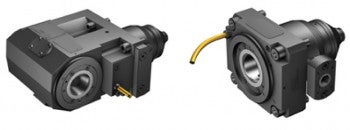
CDI
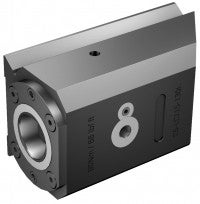
Złącze typu jaskółczy ogon VDI-DIN 69881
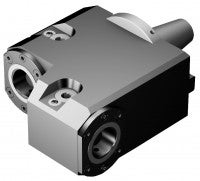
Do poszczególnych modeli tokarek pionowych
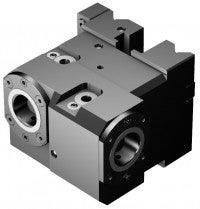
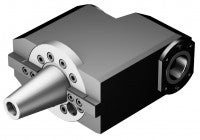
Uchwyty mocujące Coromant Capto® do mocowania śrubami (CBI)
W asortymencie standardowym uchwytów mocujących przystosowanych do obrabiarek dostępne są uchwyty do złączy głowic rewolwerowych obrabiarek wielu marek.
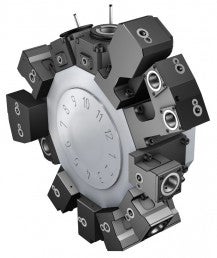
Automatyczna zmiana narzędzi w centrach tokarskich
Dostępny opcjonalnie automatyczny zmieniacz narzędzi do dużych pionowych centrów tokarskich posiada magazyn bębnowy umożliwiający przechowywanie długich wytaczaków. Zwiększa się liczba dostępnych pozycji narzędzi, wzrasta elastyczność i pojawiają się możliwości produkcji bezzałogowej.
W centrach tokarskich wyposażonych w głowicę rewolwerową ATC-MACU automatyczna zmiana narzędzi jest dostępna dla statycznych i napędzanych oprawek narzędziowych. Z powodu częstych ręcznych zmian narzędzi stopień wykorzystania centrów tokarskich jest zazwyczaj niewielki. Automatyczna zmiana narzędzi rozwiązuje ten problem, ponieważ umożliwia produkcję bezzałogową, która z kolei zwiększa wydajność i stabilizuje proces produkcji.
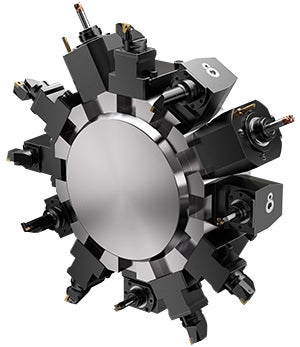
Automatyczna zmiana narzędzi w centrach tokarskich to przełomowe rozwiązanie, które umożliwia produkcję bezzałogową i zwiększa do maksimum wydajność.
Złącze Coromant Capto® Disc Interface (CDI)
CDI to złącze do głowic rewolwerowych, które można stosować w obrabiarkach dowolnego typu zamiast złącza VDI. Głowice rewolwerowe przystosowane do złącza CDI posiadają obrabiarki wielu marek.
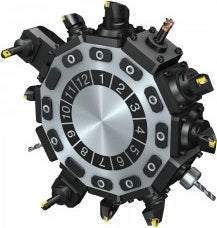
Niestandardowe uchwyty mocujące – zestawy
Zestawy elementów uchwytów mocujących umożliwiają przystosowanie uchwytu mocującego do określonych wymagań. Zestawy są powszechnie stosowane z imakami blokowymi w tokarkach karuzelowych, z oprawkami podwójnymi lub jako rozwiązanie szybkowymienne umożliwiające przystosowanie uchwytu do wykorzystywanej głowicy rewolwerowej.
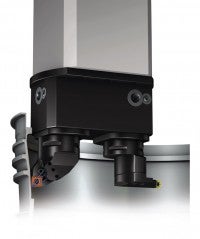
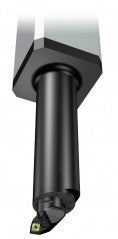
Z zestawem elementów uchwytów mocujących, w zależności od zastosowania, dostępne są różne tuleje.
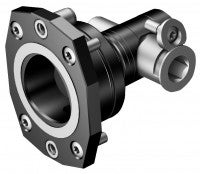
Informacje ogólne
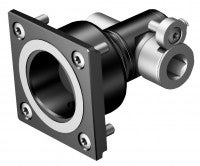
Prostokątne – podwójne gniazda
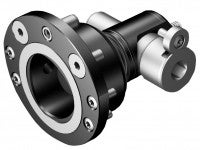
Z przesunięciem – do użytku z wytaczakami
Rodzaje uchwytów mocujących przystosowanych do obrabiarki
Obróbka zewnętrzna – toczenie średnic zewnętrznych
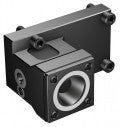
Cx-TRE-xxxxA
Pojedynczy uchwyt do obróbki zewnętrznej
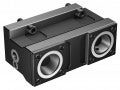
Cx-TRE-xxxxA-DT
Podwójny uchwyt do wrzeciona pomocniczego
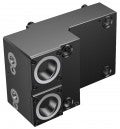
Cx-TRE-xxxxA-YT
Oś Y
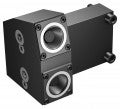
Cx-TRE-xxxxA-TT
Do obrabiarek z funkcją pośredniego pozycjonowania głowicy
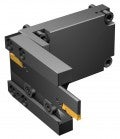
APB-TNE-xxxxA-25
Z adapterem listew przecinakowych
Obróbka wewnętrzna – toczenie średnic wewnętrznych/wiercenie
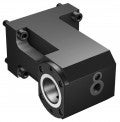
Cx-TRI-xxxxA
Pojedynczy uchwyt do obróbki wewnętrznej
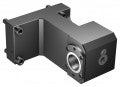
Cx-TRI-xxxxA-SS
Do wrzeciona pomocniczego
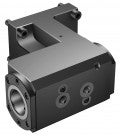
Cx-TRI-xxxxA-DT
Podwójny uchwyt do wrzeciona pomocniczego
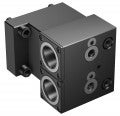
Cx-TRI-xxxxA-YT
Oś Y
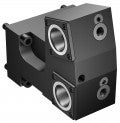
Cx-TRI-xxxxA-TT
Do obrabiarek z funkcją pośredniego pozycjonowania głowicy
Napędzany
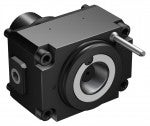
Cx-DTE-xxxxA-E/I
Do obróbki zewnętrznej
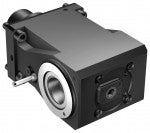
Cx-DTI-xxxxA-E/I
Do obróbki wewnętrznej
