Le tournage de matières exotiques
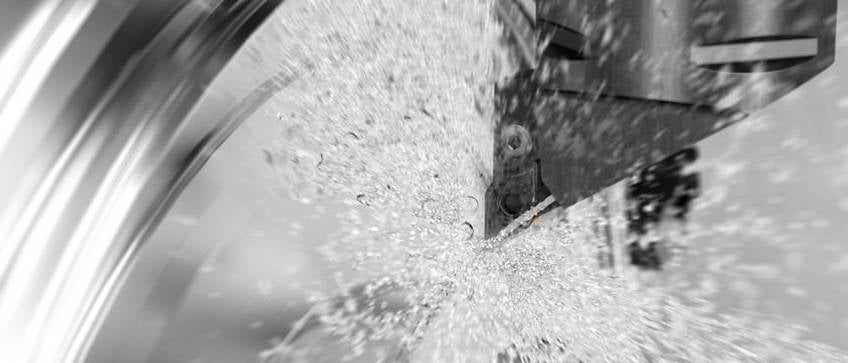
Les superalliages réfractaires et les alliages en titane sont difficiles à usiner. Ils ne ressemblent à aucun autre métal et sont donc considérés comme exotiques. Ils possèdent de remarquables propriétés, telles que le rapport résistance/poids, la conservation de la résistance et de la dureté à haute température et une excellente résistance à la corrosion.
Cependant, comme ces matières sont également difficiles à usiner, elles nécessitent des solutions « exotiques ». Celles-ci doivent être minutieusement planifiées avec des outils dédiés et des méthodes et trajets d'outils soigneusement choisis, afin de garantir l'efficacité, la sécurité et de bons résultats.
Cette vue d'ensemble présente les exigences d'usinage et les développements qui ont permis d'augmenter les performances et la sécurité du process de tournage.
Des pièces aux propriétés uniques, mais difficiles à usiner
Plusieurs facteurs déterminent la capacité à usiner la matière d'une pièce. Ils influencent et dictent les exigences et les résultats des opérations d'usinage des métaux. Dans un sens très large, il s'agit de la capacité de la matière à être coupée par rapport à la tendance à l'usure de l'outil et à la formation de copeaux. À la différence que, sur la plupart des échelles, ces matières exotiques sont difficilement usinables. Elles sont considérées comme difficiles à couper, mais pas si difficiles, si on les aborde correctement.
Les matières les plus exotiques des pièces relativement courantes sont classées dans le groupe ISO S : les superalliages réfractaires et les alliages de titane. En matière d'usinage, elles peuvent toutes être réparties en plusieurs sous-groupes, en fonction de leur composition, de leur condition et de leurs propriétés. La nature chimique et la composition métallurgique d'un alliage classé S déterminent les propriétés physiques et par conséquent son usinabilité. La segmentation des copeaux rend souvent leur contrôle difficile et il n'est pas rare que la force de coupe spécifique soit deux fois supérieure à celle de l'acier (c'est la mesure directe de la dureté de la coupe d'une matière qui détermine la force et la puissance de coupe nécessaires).
Les superalliages réfractaires sont difficiles à couper car ils conservent une résistance élevée à haute température. Ils ne deviennent pas malléables et ne s'écoulent pas comme la plupart des autres matières, et ils s'écrouissent facilement. Une charge mécanique élevée et une chaleur considérable sont concentrées sur l'arête de coupe. Les alliages à base de nickel, de fer ou de cobalt sont des sous-groupes des superalliages réfractaires. Ils possèdent des capacités uniques pour la fabrication de pièces, principalement dans les secteurs de l'aéronautique, de l'énergie et de la médecine, car leurs propriétés ne changent pas beaucoup avant d'atteindre leur point de fusion. Ils possèdent également des propriétés anticorrosives. Mais du point de vue de l'usinabilité, ils ont besoin d'une machine performante, de conditions de montage rigoureuses, de nuances et de géométries de plaquettes spécifiques, d'un arrosage optimisé et enfin, d'une méthode d'usinage et d'une approche de l'outil adaptées. Il est certain qu'une planification plus poussée est nécessaire, ce qui exige plus de travail en amont de la fabrication.
Les alliages de titane sont également répartis en sous-groupes dont le degré d'usinabilité varie. En général, l'usinabilité est évaluée en fonction de différents degrés de (dureté), qui imposent par conséquent des exigences très particulières aux outils et aux méthodes. La faible conductivité thermique, la résistance élevée à haute température, les copeaux très cisaillés et fins avec une tendance au collage, ce qui crée une zone de contact étroite sur la face de coupe de la plaquette et des forces de coupe élevées concentrées à proximité de l'arête de coupe sont autant d'exigences. Les copeaux peuvent se former de manière cyclique, ce qui entraîne des forces de coupe variables. De plus, certains alliages ont une teneur relativement élevée en carbures, ce qui rend la matière très abrasive. Des vitesses de coupe excessives peuvent provoquer une réaction chimique entre le copeau et le matériau de l'outil, ce qui entraîne un écaillage ou une fracture brusque de l'arête de coupe, ainsi qu'un essuyage ou un soudage de la matière sur les arêtes de coupe. Certains alliages s'écrouissent aussi facilement, ce qui provoque une usure par diffusion, qui entraîne à son tour une formation excessive de bavures. Les opérations suivantes peuvent par conséquent être difficiles.
Exotique, oui, mais la marge pour réussir l'usinage de la plupart des superalliages réfractaires et des alliages de titane est relativement étroite.
Lors du tournage de ces matières, …
… le succès dépend de l'équilibre entre l'effet combiné de la matière et les facteurs d'application. Il existe quelques règles de base qui contribuent grandement à l'obtention de résultats satisfaisants :
- planifier au préalable une bonne stratégie d'usinage, aussi détaillée que possible,
- établir la meilleure approche en termes d'outils,
- établir les meilleurs trajets d'outils et utiliser des porte-outils très stables,
- utiliser le meilleur de la nouvelle technologie dédiée aux outils de coupe,
- appliquer des conditions de coupe adaptées pour garantir la sécurité et la productivité du process,
- utiliser le calcul de la longueur de coupe hélicoïdale pour prévoir les coupes,
- appliquer correctement le liquide de coupe, des solutions modernes à haute pression,
- faire appel aux recommandations et au soutien de spécialistes.
Le process d'usinage doit toujours être soigneusement planifié à cause des facteurs critiques et décisifs concernés, tels que la prise en compte de l'état/condition de la matière usinée. Le choix des outils et méthodes doit être déterminé par les traitements qui affectent la pièce, qu'elle soit coulée, forgée, laminée, vieillie ou recuite. L'état de surface de la pièce varie et affecte l'usinage, tout comme la dureté. La stratégie de tournage doit également tenir compte des exigences des caractéristiques de conception de la pièce à usiner, ainsi que des différentes étapes de l'usinage, à savoir l'ébauche (première étape), la semi-finition (étape intermédiaire) et la finition (dernière étape). Les caractéristiques complexes et l'intégrité de la surface sont des problèmes courants.
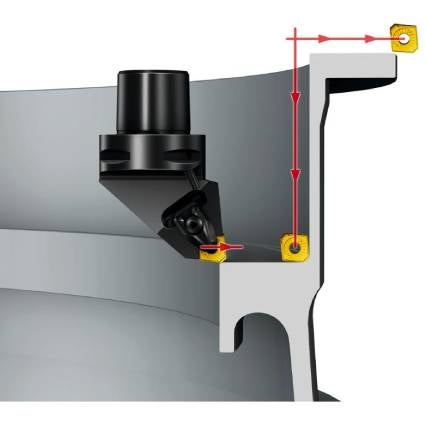
Lors de la planification du tournage de matières exotiques, la conception, la matière et l'état de la pièce sont les critères de base. Le cas échéant, déterminer la méthode d'ébauche, de semi-finition et de finition, en fonction de l'état de la matière et des exigences de qualité. La planification des trajets de l'outil et l'utilisation de la réduction de l'avance lors de la programmation déterminent l'ampleur de l'usure, le type d'outil, les temps de cycle et la sécurité.
L'action de coupe dans ces matières …
… est en grande partie affectée par l'approche de l'arête de coupe de la pièce à usiner. L'angle d'attaque de l'arête de coupe, associé à la géométrie de la plaquette, détermine les performances, la durée de vie de l'outil, la sécurité et les résultats. Les formes des plaquettes doivent souvent être choisies en fonction de la coupe à réaliser. Cependant, il est important de tenir compte de l'effet d'un petit angle d'attaque sur les performances et la durée de vie de l'outil.
Le choix de la nuance de la plaquette doit reposer en partie sur l'angle d'attaque. Cet angle influence, entre autres, le type d'usure qui forme une entaille sur l'arête de coupe, et dont la taille influe sur les résultats et peut provoquer une défaillance prématurée de l'outil. Une bonne approche de l'application implique également qu'il est possible de choisir une nuance de plaquette capable d'offrir une productivité plus élevée et de garantir une longue durée de vie de l'outil ainsi que la sécurité.

L'angle d'attaque de l'outil de coupe affecte l'épaisseur du copeau, le taux d'avance, les forces de coupe ainsi que le type de coupe possible. Dans le cas des matières exotiques, le choix de l'angle a des conséquences directes sur la productivité et la fiabilité du process, car il influence la forme de la plaquette et le rayon du bec ainsi que la capacité d'utilisation du matériau de coupe. Les plaquettes rondes et les plaquettes de type xcel sont généralement les meilleurs choix.
Le choix du matériau de l'outil (nuance de plaquette) doit être influencé par le type d'opération de tournage concerné, ébauche, semi-finition ou finition, ainsi que par l'état de la pièce à usiner et le type de coupe. En raison de la dureté de ces matières, la déformation plastique de l'arête de coupe doit toujours être considérée comme le principal facteur de risque lors du choix de la nuance de plaquette (l'usure en entaille, comme indiqué, est principalement affectée par l'angle d'attaque et la profondeur de coupe). Le choix de la nuance de plaquette doit également être associé à la forme de la plaquette. Il s'agit en effet d'une question de résistance qui doit être évaluée en fonction de l'approche, de la charge copeaux et du type de coupe (continue ou interrompue). Les nuances dédiées sont donc essentielles pour l'usinage des superalliages réfractaires.
Les principales exigences sont les suivantes : un degré élevé de dureté à chaud de la plaquette, un niveau adéquat de ténacité de la plaquette et une adhérence suffisante du revêtement de la plaquette. La plaquette indexable pour ces matières doit se caractériser par une géométrie de coupe positive, une arête de coupe vive, une arête forte et un brise-copeaux relativement ouvert.
La réussite de l'usinage de ces matières repose également sur la définition de conditions de coupe adaptées. La vitesse de coupe dépend essentiellement de la vitesse, de l'avance et de la profondeur de coupe. Elle peut être optimisée pour offrir des niveaux élevés de productivité, de sécurité et de qualité. La vitesse de coupe est liée à la production de chaleur et à la façon dont celle-ci affecte la plaquette ; elle doit être suffisamment élevée pour que le copeau ait une plasticité suffisante, mais pas excessive pour ne pas déséquilibrer le matériau de l'outil. Les vitesses sont généralement de l'ordre de 130 à 260 sfm (40 à 80 m/min) avec des plaquettes en carbure cémenté et de 490 à 1 310 sfm (150 à 400 m/min) avec des plaquettes céramique.
Le taux d'avance est le principal facteur influençant le temps de coupe et l'épaisseur des copeaux. Dans les matières exotiques, l'équilibre est plus délicat car les limites sont relativement étroites : en ébauche, le copeau doit être maximisé mais sans surcharger l'arête, tandis qu'en finition, le copeau doit être suffisamment épais pour éviter une chaleur excessive et un écrouissage.
La profondeur de coupe affecte souvent l'approche de l'arête et doit donc être inférieure à une certaine valeur. Par exemple, lors de l'usinage de superalliages réfractaires avec des plaquettes rondes, la profondeur de coupe ne doit pas dépasser 15 % du diamètre de la plaquette. La profondeur de coupe doit également être programmée avec soin lors du profilage. Des évidements ou des épaulements sont prévus, afin de contrôler l'arc d'engagement de l'arête de coupe.
En ce qui concerne la durée de vie de l'outil, il est important de travailler largement avec la longueur des copeaux développée (SCL). Une bonne méthode SCL permet de prévoir et de programmer les arrêts-machine pour l'indexage des plaquettes et de réaliser des passes à la bonne vitesse sans que l'arête de coupe ne soit incapable de maintenir la qualité de surface requise.
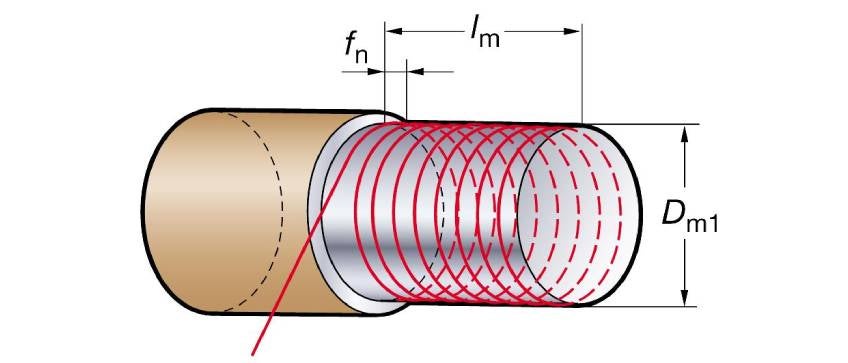
Le calcul de la longueur des copeaux développée permet de prévoir le temps ou la longueur de coupe afin de réduire le temps d'usinage et d'améliorer l'état de surface dans les matières exotiques difficiles. La longueur des copeaux développée permet de planifier les arrêts-machine pour le changement de plaquette afin de mieux s'adapter à l'opération et aux conditions de coupe et d'optimiser la durée de vie de l'outil et l'exploitation des machines.
L'usure de l'outil est fortement affectée …
… par les forces de coupe élevées combinées à des températures plus élevées de l'arête de coupe. Certains types d'usure de l'arête de coupe ont ainsi tendance à se développer. Les principaux sont l'usure en entaille déjà mentionnée (le type d'usure mécanique pour lequel la profondeur de coupe détermine la ligne de la matière usinée) ; la déformation plastique de l'arête de coupe, conséquence d'une température et d'une pression élevées, et enfin l'usure par abrasion causée principalement par les matières plus dures. Un autre type d'usure est l'usure de la tranche supérieure, qui se produit sur les plaquettes céramique, lorsque des couches de la partie supérieure de l'arête de coupe sont tranchées. L'approche de l'arête de coupe joue un rôle majeur.
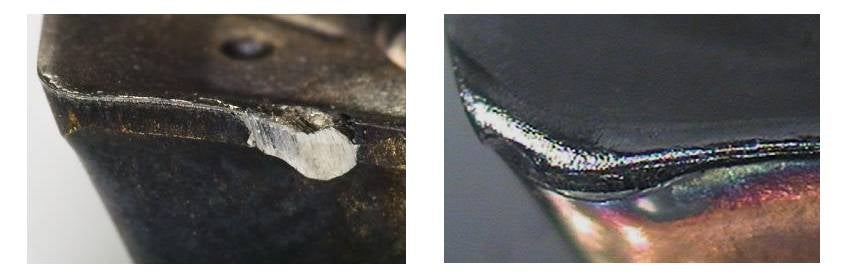
Le choix de la nuance de plaquette n'est pas aussi directement lié à l'ébauche et à la finition des matières exotiques qu'il ne l'est pour les autres matières. Le choix de la nuance est plutôt un facteur d'optimisation, un peu plus complexe, qui dépend de la forme de la plaquette, de l'approche de l'arête de coupe et du type d'opération. Les types d'usure destructive, tels que l'usure en entaille et la déformation plastique, doivent être maîtrisés en associant des outils, des conditions de coupe et une méthode appropriés. Les plaquettes en carbure cimenté ainsi que les céramiques modernes en sialon et, dans une certaine mesure, les céramiques à whiskers, constituent souvent le choix le plus pertinent et le plus largement applicable.
L'angle d'attaque le plus approprié pour le tournage des matières exotiques est un petit angle, égal ou inférieur à 45 degrés. La pire condition survient lorsque l'angle d'attaque est de 90/0 degrés ou lorsque la profondeur de coupe est supérieure au rayon du bec de la plaquette. Un angle grand/petit implique un copeau fin et de plus grandes avances.
Pour le tournage de superalliages réfractaires, l'angle d'attaque de l'outil déterminera s'il faut choisir une plaquette revêtue de PVD ou de CVD. Le but est de prévenir les effets thermiques. Le PVD convient pour un angle d'attaque de 90/0 degrés et le CVD pour 45 degrés. En revanche, le revêtement des plaquettes ne joue aucun rôle dans le tournage du titane. Dans ce cas, il est plus important de choisir la forme de l'arête le plus approprié, par exemple des plaquettes rondes en finition. De nouvelles familles de plaquettes PVD offrent une dureté élevée et une bonne résistance à la déformation de l'arête et aux chocs thermiques. Associées à des arêtes vives, elles peuvent également exceller dans les opérations d'ébauche à la finition de matières collantes.
La bonne forme de plaquette …
… est un facteur d'application important pour l'usinage de ces matières. La plaquette ronde (forme R) est la forme privilégiée pour ces matières. La plaquette ronde procure résistance pour une arête vive et positive ; une épaisseur de copeaux qui varie le long d'une longue arête de coupe permettant des vitesses d'avance rapides ; un grand rayon de plaquette, qui ne limite pas le taux d'avance en raison de l'état de surface créé. La plaquette ronde apporte également la flexibilité de programmation nécessaire pour effectuer les opérations de profilage et d'usinage de poches nécessaires à de nombreuses formes de pièces.
Une plaquette carrée (forme S) est dans certains cas la plus adaptée à l'ébauche, car elle permet de réaliser des coupes d'ébauche dans différentes directions avec un angle de 45 degrés. La plaquette rhombique (forme C) offre une grande flexibilité en termes de trajets d'outils et, lorsqu'elle est prolongée pour devenir une plaquette de type Xcel, elle offre encore plus d'accessibilité aux outils dans les coins, les épaulements et les évidements. Cette combinaison de la forme de la plaquette et de l'angle d'attaque de 45 degrés permet également de réduire les forces de coupe radiales, d'obtenir une épaisseur de copeaux constante et de réduire l'usure en entaille. Grâce à cela, la productivité est plus élevée, la durée de vie des outils est plus longue et la sécurité est améliorée.
L'optimisation du programme …
… est importante et les recommandations suivantes permettent d'améliorer les performances, notamment avec les plaquettes rondes, qui sont en principe adaptées aux matières exotiques :
- éviter le tréflage dans les coupes et amortir les impacts ; si ces coupes sont nécessaires, diviser le taux d'avance par deux,
- lors du tournage vers un épaulement, l'avance doit également être réduite de moitié ou l'outil doit rouler jusqu'à l'épaulement où le rayon programmé est égal au diamètre de la plaquette. (Selon les indications, le rayon minimum programmé doit correspondre à environ 25 % du diamètre de la plaquette et le rayon de la pièce à 75 % du diamètre de la plaquette. L'avance centrale correspond au rayon programmé.),
- pour l'ébauche avec des plaquettes rondes, le rayon programmé doit être égal au diamètre de la plaquette et pour la finition, le rayon programmé doit être supérieur au diamètre de la plaquette,
- envisager différents trajets d'outils, des passes multiples et l'usinage dans les deux sens pour utiliser pleinement les plaquettes,
- protéger les plaquettes céramique grâce au préchanfreinage de la pièce et à l'avance dans le chanfrein,
- respecter un équilibre satisfaisant de l'angle d'attaque par rapport à l'arc d'engagement de la plaquette pendant toute la durée de l'usinage. il est essentiel de limiter l'angle pour obtenir de bonnes performances et l'utilisation de plaquettes rondes est un atout important pour exploiter les possibilités offertes par les plaquettes modernes,
- éviter tout effet d'enveloppement lors du profilage ou du tréflage afin de ne pas surcharger la plaquette, utiliser d'autres trajets d'outil ou un diamètre de plaquette plus petit,
- envisager le tournage trochoïdal, en décomposant la coupe en petites coupes bien adaptées, notamment lors de l'usinage de poches.
Quels sont les types d'outils et les méthodes à privilégier pour l'usinage des superalliages réfractaires et du titane ? Voici les principaux aspects à rechercher :
- L'arrosage de précision doit toujours être envisagé. Grâce aux jets de précision ciblant l'arrière et l'arête de coupe et alimentés par un outillage d'arrosage par l'intérieur, les avantages sont nombreux pour les opérations de tournage, de fraisage et de perçage. La technologie de pointe des buses, disponible sous forme de solutions standard ou sur mesure avec différentes plages de pression, peut être appliquée à tous les types de machines avec une alimentation en liquide de coupe adéquate. Lors d'un investissement dans une nouvelle machine, la pression du liquide de coupe doit toujours inclure une possibilité de 70 bars pour le tournage du titane afin d'améliorer le bris des copeaux, mais une pression allant jusqu'à 200 bars est préférable pour le tournage des superalliages réfractaires, car les copeaux sont plus durs à briser.
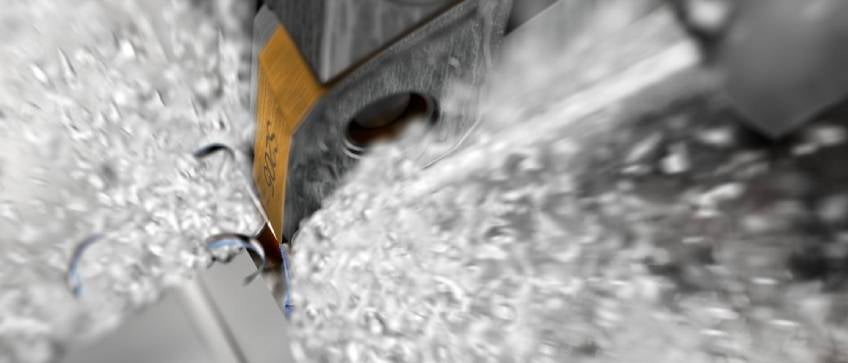
L'arrosage est un facteur d'application décisif pour l'usinage des matières exotiques. L'arrosage de précision est aujourd'hui une technologie de pointe standard ou sur mesure et si efficace qu'elle fait une nette différence sur la coupe, la formation des copeaux, la durée de vie de l'outil et la productivité. En général, les températures élevées générées dans ces matières nécessitent un effet de refroidissement, mais lorsque le liquide de coupe est appliqué en abondance, à haute pression et avec précision, avec des plaquettes dédiées et un arrosage par l'intérieur, les performances et les résultats sont optimisés.
- Lors du tournage de matières exotiques, l'accessibilité est souvent un problème. Les caractéristiques complexes et les porte-à-faux des outils exigent de choisir les bons outils et les bonnes méthodes. Il faut donc opter pour des systèmes modulaires qui proposent un concept fiable avec des lames d'outils présentant les arêtes de coupe à différents angles et porte-à-faux. La gamme d'adaptateurs et de lames doit permettre de composer presque n'importe quel outil à partir d'un inventaire limité d'outils standard, afin de s'adapter aux configurations et de permettre l'accès à des espaces confinés externes ou internes. Les lames doivent présenter les dépouilles radiales et axiales requises pour pénétrer profondément dans les rainures angulaires avec un arrosage de précision par l'intérieur jusqu'à l'arête de coupe.
- Le matériau de l'outil est un élément essentiel de toute opération d'usinage et pour les matières exotiques, il s'agit d'un facteur critique. Ce domaine nécessite des nuances de plaquettes spécifiques ainsi qu'une géométrie de plaquette adaptée, généralement les dernières nouveautés en matière de carbure cémenté et de céramique. Les nuances carbure non revêtu occupent toujours une place importante. Toutefois, les dernières avancées en matière de technologie de revêtement des plaquettes ont permis d'obtenir des plaquettes en carbure cémenté spécialement revêtu qui ont amélioré les capacités de coupe en réduisant le temps de coupe et en prolongeant la durée de vie de l'outil.
- Les barres d'alésage, les lames voire les fraises doivent être dotées de caractéristiques antivibratoires intégrées pour minimiser les tendances aux vibrations. La technologie antivibratoire a fait d'énormes progrès et doit être une option évidente lorsque les porte-à-faux des outils ont tendance à produire des effets d'instabilité. La productivité, la sécurité du process et la qualité des composants sont des facteurs directement liés à la qualité et à la disponibilité de l'outillage antivibratoire. Sans lui, de nombreuses opérations sont impossibles à réaliser : aujourd'hui, le tournage intérieur impliquant des porte-à-faux allant jusqu'à quatorze fois des diamètres allant jusqu'à 250 mm, peut être effectué très efficacement avec une haute finition.