Chauffé au rouge
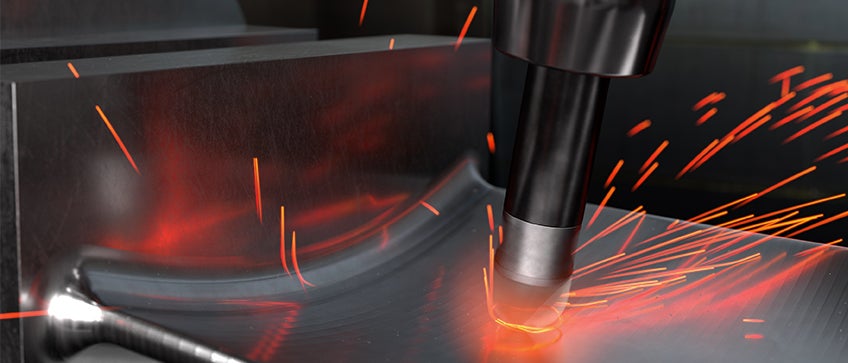
Problème : Usiner efficacement les pièces de moteurs d'avions à partir de superalliages réfractaires.
Solution : Développer une solution globale équilibrée qui englobe la machine, les outils, les géométries et les matériaux des outils ainsi que la stratégie d'usinage.
Les superalliages réfractaires sont les matières les plus utilisées dans les composants des compresseurs et des turbines des moteurs à réaction. Les principales nuances utilisées pour ces applications sont les types à base de nickel tels que l'Inconel, le Waspaloy et l'Udimet.
Les propriétés des superalliages réfractaires varient considérablement en fonction de la composition et de la méthode de fabrication. Le traitement thermique, en particulier, revêt une grande importance : une pièce durcie par précipitation, c'est-à-dire « vieillie », peut présenter une dureté deux fois supérieure à celle d'une pièce recuite ou non traitée.
Les réglementations toujours plus strictes en matière d'émissions exigent des températures de service plus élevées de la part des nouveaux types de moteurs et requièrent de nouvelles matières pour les pièces les plus chaudes. Par ailleurs, la quantité totale de superalliages réfractaires dans un moteur à réaction est en augmentation par rapport aux autres matières.
Cependant, les avantages des superalliages réfractaires posent un problème de fabrication : la résistance aux températures élevées implique des forces de coupe importantes. Une faible conductivité thermique et une excellente trempabilité se traduisent par des températures de coupe élevées. Les tendances à l'écrouissage en coupe favorisent l'usure en entaille.
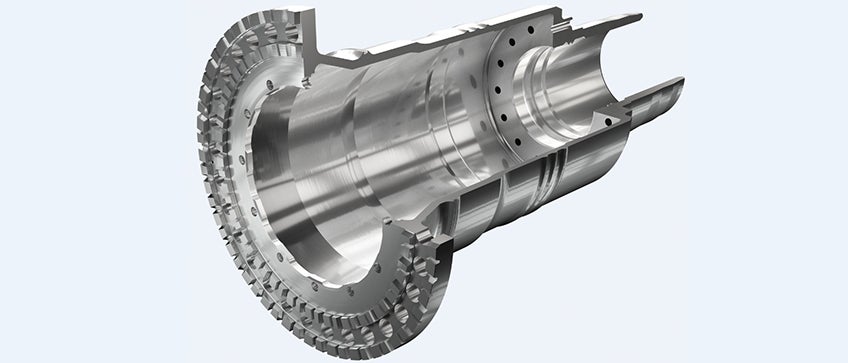
Pièce ; arbre en superalliage réfractaire.
Les pièces, qu'il s'agisse de disques de turbine, de carters, d'aubes ou d'arbres, sont des pièces difficiles à usiner, souvent à paroi mince et de forme complexe. Les pièces du moteur, essentielles pour la sécurité, doivent répondre à des critères de qualité et de précision dimensionnelle très stricts.
Pour réussir, il faut une machine puissante, des outils rigides, des plaquettes performantes et une programmation optimale. Les méthodes prévalentes varient. Les composants des disques, des bagues et des arbres sont généralement tournés, tandis que les carters et les blisks sont souvent fraisés.
L'usinage des superalliages réfractaires est généralement organisé en trois étapes. Au cours de l'ébauche, une pièce brute coulée ou forgée reçoit sa forme de base. La pièce se trouve généralement dans un état avant traitement (dureté typique d'environ 25 HRC), mais elle présente souvent une croûte ou une graduation rugueuse et irrégulière. La priorité principale réside dans une bonne productivité et une surépaisseur d'usinage efficace.
Entre l'ébauche et la semi-finition, la pièce est soumise à un traitement thermique pour atteindre l'état vieilli beaucoup plus dur (généralement autour de 36-46 HRC). La pièce reçoit à présent sa forme définitive, sauf que la surépaisseur est laissée pour la finition. La priorité est à nouveau accordée à la productivité, mais la sécurité des process est également importante.
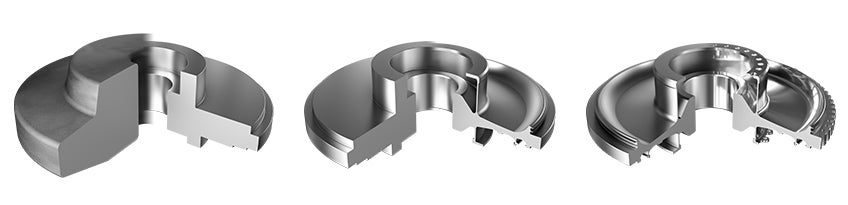
Ébauche, semi-finition et finition de disques de turbines en superalliages réfractaires.
La forme définitive et l'état de surface sont créés lors de la finition. La préoccupation principale porte sur la qualité de la surface, la précision des tolérances dimensionnelles et l'absence de déformations et de tensions résiduelles excessives. Dans les composants rotatifs critiques, les propriétés de fatigue sont les critères les plus importants et ne laissent aucune place aux défauts de surface qui pourraient entraîner la formation de fissures. La fiabilité des pièces critiques est garantie par l'application d'un process d'usinage éprouvé et certifié.
Les exigences générales pour les plaquettes indexables comprennent une bonne résilience d'arête et une forte adhérence entre le substrat et le revêtement. Si les formes de base négatives sont utilisées pour une résistance et une économie élevées, la géométrie doit être positive.
L'usinage de superalliages réfractaires doit toujours se faire sous arrosage, à l'exception du fraisage avec des plaquettes céramique. Les plaquettes céramique nécessitent un arrosage abondant, tandis que la précision du flux est essentielle pour le carbure cémenté. Avec les plaquettes carbure, un arrosage haute pression offre d'autres avantages, notamment une durée de vie plus longue de l'outil et un contrôle des copeaux efficace.
Les paramètres d'usinage varient en fonction des conditions et de la matière. Pendant l'ébauche, on cherche principalement à obtenir une bonne productivité grâce à des vitesses d'avance rapides et à de grandes profondeurs de coupe. Pendant la semi-finition, les plaquettes céramique sont souvent utilisées pour atteindre des vitesses plus élevées. Les étapes de finition se concentrent sur la qualité, et la profondeur de coupe est faible. Comme une vitesse de coupe élevée peut nuire à la qualité de la surface, les plaquettes carbure sont utilisées pour la finition.
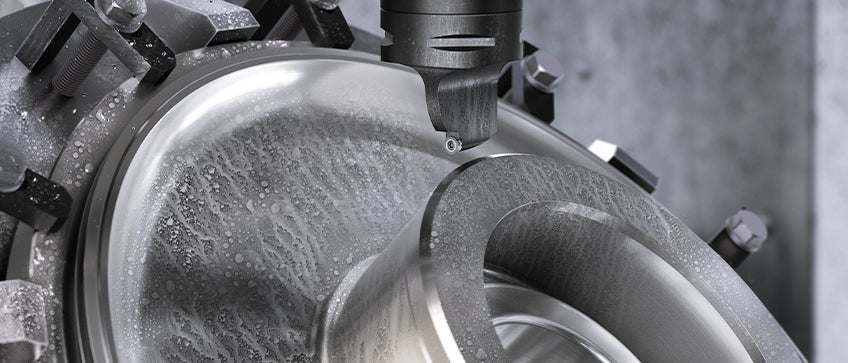
Les disques de turbine sont des pièces critiques fabriquées dans des matières avancées, qui nécessitent un usinage de haute sécurité avec des outils et des solutions de coupe optimisés.
La déformation plastique et l'entaillage sont les mécanismes d'usure typiques des plaquettes carbure, tandis que l'usure de la tranche supérieure est courante dans les plaquettes céramique. La vulnérabilité à la déformation plastique diminue si l'on augmente la résistance à l'usure et la dureté à chaud. Une géométrie positive et une arête tranchante contribuent également à réduire la production de chaleur et les forces de coupe. Les solutions à l'usure en entaille de l'arête de coupe principale consistent à utiliser un faible angle d'attaque, par exemple grâce à l'utilisation d'une plaquette carrée ou ronde, ou une profondeur de coupe inférieure au rayon de bec.
Les plaquettes revêtues PVD sont plus résistantes à l'entaillage sur l'arête principale, tandis qu'une plaquette revêtue CVD a une meilleure résistance à l'usure en entaille sur l'arête secondaire. Lors de la finition, l'usure en entaille sur l'arête secondaire peut nuire à l'état de surface.
Résumé
Pour usiner efficacement les pièces de moteur en superalliages réfractaires, il faut appliquer une solution globale bien équilibrée, qui tient compte notamment de facteurs tels que l'état de la pièce, le matériau de l'outil et les recommandations de conditions de coupe correspondantes, l'utilisation de liquide de coupe et les stratégies d'usinage optimisées.
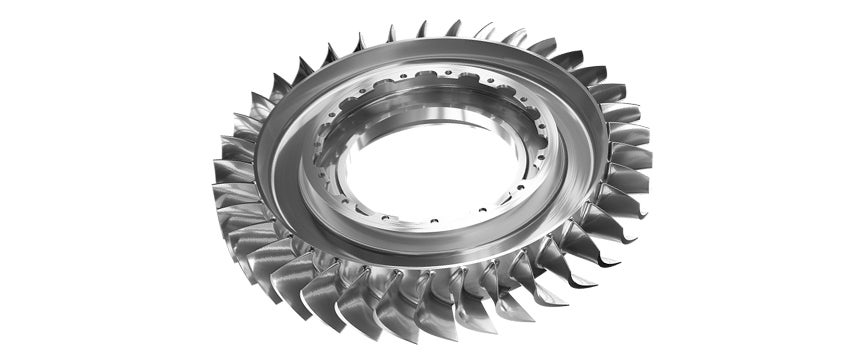
Les outils destinés à la semi-finition et la finition des superalliages réfractaires sont dotés de géométries vives et très positives pour la finition et la semi-finition, ainsi que de géométries pour les opérations nécessitant une plus grande ténacité.