Une bonne façon de supprimer les micro-défauts
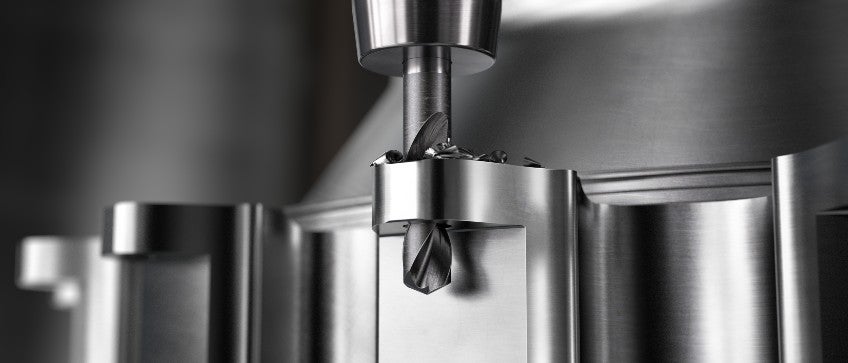
Des essais effectués avec un foret carbure à la conception améliorée ouvrent de nouvelles possibilités en termes de qualité de trou.
« Mesurer deux fois, couper une fois » : cette expression est courante dans les ateliers, mais c'est plus facile à dire qu'à faire lorsqu'on usine des matières difficiles. C'est pour cette raison qu'un grand fabricant international de pièces aéronautiques qui cherchait à éliminer une étape d'un process de perçage tout en améliorant la qualité des trous s'est adressé au leader mondial des outils de coupe. James Thorpe, responsable produits chez Sandvik Coromant, nous explique en quoi la conception des forets est essentielle pour la qualité des trous.
Le perçage est une des opérations d'usinage les plus courantes, et elle est souvent considérée comme allant de soi. Dans beaucoup d'ateliers, on considère que les outils et les conditions de coupe en place pour le perçage depuis des années ne nécessitent pas d'être révisés ou améliorés. Mais avec les changements imprévisibles dus à la crise du COVID-19, beaucoup de certitudes ont dû être remises en cause. Les fabricants se sont heurtés à des changements imprévisibles et durables sur les marchés des clients et reconnaissent aujourd'hui la nécessité d'adapter leur fabrication.
La plupart des fabricants explorent déjà de nouvelles bases de fournisseurs et de produits. C'est dans cette optique que beaucoup d'ateliers d'usinage autrefois spécialisés dans certaines productions mettent désormais leurs machines CNC au service de productions et matières plus diversifiées présentant des difficultés jusqu'alors inconnues. Dans le même temps, des efforts sont aussi faits pour trouver de nouvelles manières d'améliorer la rentabilité et réduire les temps de cycle, sans pour autant sacrifier la qualité.
En un mot, le temps est venu de revoir la manière dont les trous sont usinés.
La couche blanche
L'intégrité de la surface des trous est une préoccupation majeure dans l'aéronautique ainsi que dans les ateliers de mécanique générale qui diversifient leurs activités, notamment au profit de l'aéronautique. Une bonne qualité de trou est essentielle pour la fiabilité des pièces et dépend du process de production utilisé pour le perçage et la finition.
Les solutions d'outillage et la géométrie des arêtes de coupe des forets évoluent constamment afin de répondre aux normes les plus élevées. L'utilisation de l'arrosage permet aussi de réduire la chaleur pendant le perçage. Les essais ont montré que ces différents paramètres ont une influence sur ce que l'on appelle la « couche blanche » à l'intérieur des trous.
Cette couche blanche a été identifiée par un grand fabricant international du secteur aéronautique, client de Sandvik Coromant. Il s'agit d'une fine couche à grain très fin créée par l'élévation de la température lors du perçage. La couche blanche modifie les propriétés de la matière et elle est considérée comme inacceptable au niveau du contrôle qualité en vigueur chez le fabricant.
Celui-ci a un process de finition des trous très strict pour les pièces aéronautiques, notamment les disques de turbine, les compresseurs, les carters et les arbres. C'est ce qui l'a amené à travailler en partenariat avec Sandvik Coromant afin de comprendre le processus de formation de la couche blanche et la manière de le contrôler.
Les questions de qualité ne sont pas les seules motivations dans cette démarche. En effet la direction de l'entreprise souhaitait aussi réduire le temps global d'usinage et améliorer la rentabilité, et, plus particulièrement, éliminer une opération secondaire.
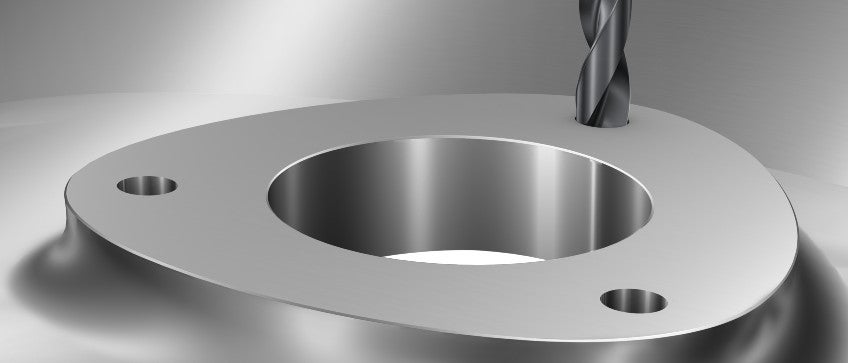
L'intégrité de la surface des trous est une préoccupation majeure dans l'aéronautique ainsi que dans les ateliers de mécanique générale qui diversifient leurs activités, notamment au profit de l'aéronautique. Ici, le bossage d'un carter en superalliages réfractaires avec le CoroDrill 860 dans la géométrie -SM
.
Deuxième acte
L'opération secondaire en question est une opération de finition par alésage, fraisage en plongée ou en bout qui intervient après le perçage des trous avec un foret carbure. Cette opération est motivée par des questions d'intégrité de la surface – notamment l'élimination de la couche blanche – plutôt que par des préoccupations sur la dimension des trous, exception faite des trous qui requièrent des tolérances très serrées.
Du point de vue du coût, cette opération de finition revient plus cher que si le perçage était effectué avec des conditions de coupe basses, un autre moyen de préserver l'intégrité de la surface des trous. C'est pour cela que le fabricant, en partenariat avec Sandvik Coromant, souhaitait explorer une nouvelle approche du process dans son ensemble. La possibilité de produire des trous avec des cotes et une qualité conformes aux besoins sans opérations secondaires est un atout pour les affaires car cela représente une réduction du coût à la pièce.
La recherche des causes et des moyens de prévention de la couche blanche dans l'alliage de nickel-chrome haute résistance Inconel 718, une matière très utilisée dans l'aéronautique, a demandé quatre essais. C'était la première fois que le fabricant effectuait ce type de recherche.
Les essais ont été effectués avec deux forets carbure monobloc de Sandvik Coromant, CoroDrill® R840 et CoroDrill® R846. Des conditions de coupe spécifiques ont été utilisées avec chaque foret : vitesses de coupe de 58 mm/min et 98 mm/min et vitesses de rotation de 829 tr/min et 757 tr/min, respectivement. Les forces de coupe et le couple ont été mesurés dans chacun des essais, tout comme l'épaisseur de la couche blanche.
Depuis ces essais, des forets de conception plus récente, CoroDrill® 860 -GM et CoroDrill® 860 -SM, sont venus remplacer les forets CoroDrill R840 et CoroDrill R846. Ces outils de nouvelle génération sont conçus pour offrir une plus longue durée de vie sans compromettre la qualité des trous.
Les résultats ont apporté un éclairage intéressant sur l'épaisseur de la couche blanche. Il est notamment apparu qu'elle était moins épaisse avec le foret CoroDrill R846 qui possède des arêtes courbes avec une préparation spécifique. À l'opposé, les arêtes de coupe rectilignes et les chanfreins du foret CoroDrill R840 génèrent une force de coupe et un couple plus élevés, ainsi qu'une couche blanche plus épaisse. La conception du foret détermine donc la qualité des trous et l'épaisseur de la couche blanche, indépendamment des conditions de coupe.
Grâce aux essais menés avec Sandvik Coromant, le fabricant de pièces aéronautiques a pu mieux comprendre la formation de la couche blanche, et, surtout, il lui a été possible d'éliminer certaines opérations secondaires comme le réalésage des trous, ce qui s'est traduit par un gain de temps et une réduction des coûts. En outre, les résultats ont permis de valider la conception de la gamme de forets carbure monobloc CoroDrill 860 de Sandvik Coromant.
Une conception améliorée
Cette gamme inclut le foret mentionné plus haut CoroDrill 860 dans la géométrie -GM, un foret polyvalent qui convient aux matières ISO P, M, K et H dans tous les secteurs industriels. La gamme inclut CoroDrill 860 dans la géométrie -SM pour les matières ISO S comme les superalliages réfractaires, le titane et l'Inconel. Ce dernier outil est très utilisé dans l'aéronautique.
Dans le développement des forets CoroDrill 860 dans la géométrie -GM et CoroDrill 860 dans la géométrie -SM, les ingénieurs de Sandvik Coromant ont suivi l'idée que la durée de vie des outils et la qualité des trous étaient avant tout une question de conception. CoroDrill 860 dans la géométrie -GM possède des goujures polies novatrices qui facilitent l'évacuation des copeaux, renforcent l'âme du foret et réduisent les forces de coupe.
CoroDrill 860 dans la géométrie -SM possède une géométrie de pointe optimisée et une nouvelle nuance de coupe qui contribuent à prolonger sa durée de vie dans le perçage des matières difficiles que sont les superalliages réfractaires. La qualité de trou obtenue est nettement meilleure.
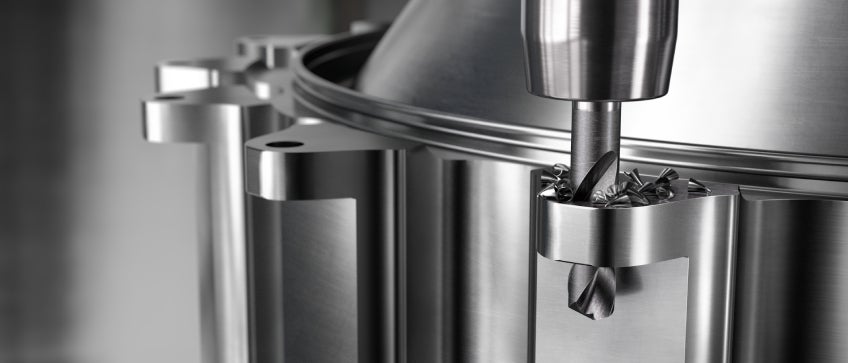
Avec le foret CoroDrill ® 860 dans la géométrie -SM, durée de vie d'outil plus longue et meilleure qualité des trous est due à la conception du foret.
CoroDrill 860 a déjà fait ses preuves dans des essais avant mise sur le marché dans plusieurs secteurs d'activité. CoroDrill 860 dans la géométrie -GM a été mis à l'épreuve par une entreprise de mécanique générale en France pour le perçage d'un acier structurel AISI 860 4140. Les trous étaient percés dans des surfaces concaves et convexes ; la qualité obtenue était très bonne, la rectitude et les tolérances étaient satisfaisantes. Suite à ces essais, l'entreprise a développé une relation commerciale privilégiée avec Sandvik Coromant.
Un autre client de Sandvik Coromant, un fabricant de pièces de mécanique générale italien, a pu obtenir un gain de productivité de plus de 45 % dans un alliage d'acier résistant 34CrNiMo6 avec le foret CoroDrill 860 dans la géométrie -GM. De plus, la durée de vie de l'outil s'est avérée 100% plus longue que celle de l'outil concurrent utilisé auparavant. Dans d'autres essais menés par des clients de Sandvik Coromant, CoroDrill 860 dans la géométrie -SM a donné des résultats impressionnants dans l'Inconel 718. Un atelier de Katowice en Pologne a obtenu un gain de durée de vie de 180 % avec CoroDrill dans la géométrie -SM par rapport au foret CoroDrill R840.
Quel que soit le secteur, qu'il s'agisse de l'aéronautique, de la mécanique générale ou d'autres secteurs, les performances des forets dépendent de leur conception. D'autres outils en ligne de Sandvik Coromant comme CoroPlus® Tool Guide apportent des avantages supplémentaires. Ce service est accessible à l'aide d'un navigateur Internet ordinaire ; il permet de spécifier la matière à percer et les dimensions des trous et indique quel foret et quelles conditions de coupe utiliser.
Même si l'adage qui préconise de « mesurer deux fois, couper une fois » reste un vœu pieux, les performances des forets CoroDrill 860 dans la géométrie -GM et CoroDrill 860 dans la géométrie -SM représentent un atout réel pour repenser les process de perçage.