Anwendungshinweise für das Gewindedrehen
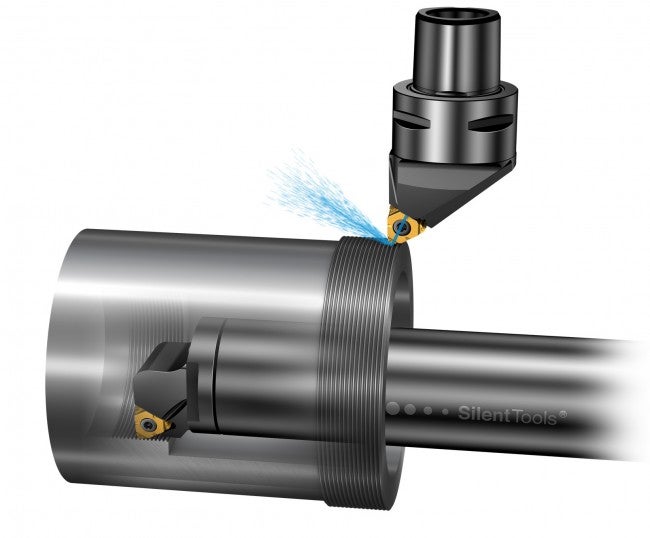
Ein häufiges Problem beim Gewindedrehen ist, dass sich Späne um Robotersysteme, Futter, Werkzeuge und Bauteile wickeln. Diese können sich außerdem in Späneförderern verfangen und zu Schäden sowie Verlust von produktiver Bearbeitungszeit führen. Erfolgreiche Spankontrolle ist der Schlüssel für eine gute Bauteilqualität beim Gewindedrehen. Folgen Sie unseren Anwendungshinweisen für gute Spankontrolle und lange Standzeit.
OptiThreading™
Verwendung der OptiThreading™ Methode für beste Spankontrolle. Diese Bearbeitungsmethode erlaubt kontrollierte oszillierende Bewegungen für Schnittunterbrechungen mit vollständigem Schnitteintritt und Schnittaustritt bei allen Durchgängen, außer beim letzten. Sie bietet höchste Prozessicherheit und Bauteilqualität.
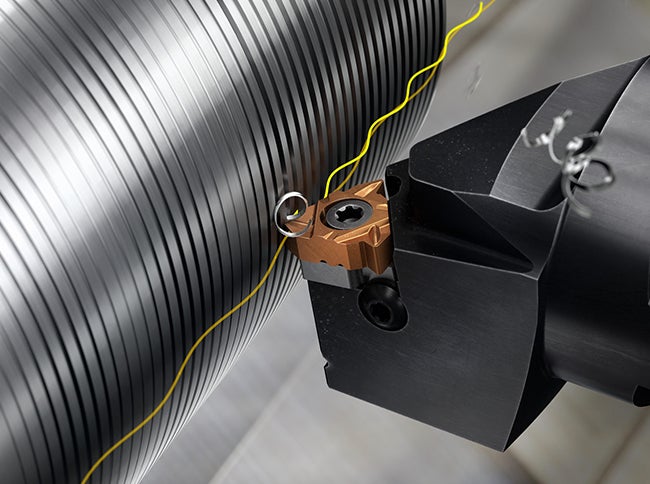
Modifizierte Flankenzustellung
Wählen Sie bei konventionellen Gewindedrehanwendungen modifizierte Flankenzustellung für beste Spankontrolle. Eine modifizierte Flankenzustellung erlaubt eine Gewindebearbeitung, die mit einer herkömmlichen Drehoperation vergleichbar ist. Diese Methode bietet kontrollierte Prozesse bei verbesserter Spankontrolle und somit vorhersagbare Standzeiten sowie eine hohe Gewindequalität.
Flankenzustellung in umgekehrter Richtung
Bei dieser Zustellungsart schneidet die Wendeschneidplatte unter Einsatz beider Flanken (gegenüberliegende Flanken), so dass die Späne in die richtige Richtung gelenkt werden können. Dies ist beim Gewindedrehen, insbesondere bei der Bearbeitung von Grundbohrungen ein wichtiger Faktor. Verwenden Sie diese Methode für eine reibungslose Gewindedrehbearbeitung ohne ungeplante Produktionsunterbrechungen.
Modifizierte Flankenzustellung (Standard) | Vorschubrichtung | Flankenzustellung in umgekehrter Richtung |
![]() | ||
Spanablauf | Spanablauf |
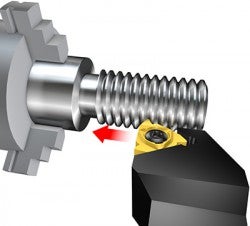
Schneidflüssigkeit und Kühlschmierstoff
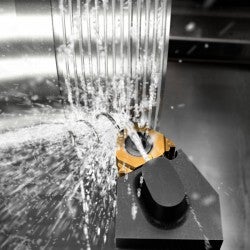
Für optimierte Spankontrolle und -abfuhr werden Werkzeuge mit Präzisions-Kühlschmierstoffzufuhr empfohlen. Präzisionskühlung bietet folgende Vorteile in Gewindedrehanwendungen:
- Kontrollierte Temperatur an der Schneidkante
- Gute Spanabfuhr
- Verbesserte Spankontrolle
Bei Verwendung von äußerer Kühlschmierstoffzufuhr gelangt oft nur eine geringfügige Kühlmittelmenge in das Gewinde und hat deshalb auch nur einen geringen Effekt.
Mit innerer Kühlmittelzufuhr erreicht der Kühlschmierstoffstrahl die Schneidkante sogar in tiefen Gewinden. Der Kühlschmierstoff reduziert effektiv die Temperatur, mit folgenden Vorteilen:
- Einsatz höherer Schnittdaten oder einer zäheren Sorte
- Verbesserte Spankontrolle und Oberflächengüte
Eine niedrige Temperatur kann den Wendeschneidplattenverschleiß z. B. Freiflächenverschleiß und plastische Verformung reduzieren und dadurch die Standzeit verlängern. Zu geringe Temperaturen bewirken allerdings kürzere Standzeiten, da eine zu hohe Temperatursenkung in adhäsiven Werkstoffen wie beispielsweise rostfreier Stahl zu Aufbauschneidenbildung (BUE) führt.
Suchen Sie Werkzeugempfehlungen?
Hier finden Sie unsere Zerspanungswerkzeuge chevron_right
Brauchen Sie Beratung?
Stellen Sie uns eine Frage chevron_right
Was es sonst noch über die Grundlagen unserer Metallzerspanung zu lernen gibt?
Registrieren Sie sich für unser kostenloses E-Learning Programm chevron_right
Überprüfung des Durchmessers
Stellen Sie vor Beginn des Gewindedrehens sicher, dass der Werkstückdurchmesser gemäß den Spezifikationen eingestellt ist.
- Wenn beim Außengewindedrehen der Durchmesser zu groß oder beim Innengewindedrehen zu klein ist, ist der erste Schnitt sehr groß und kann zu Wendeschneidplattenbruch führen.
- Ein zu kleiner Durchmesser beim Außengewindedrehen oder ein zu großer Durchmesser beim Innengewindedrehen könnte zu einem falschen Gewindedurchmesser führen.
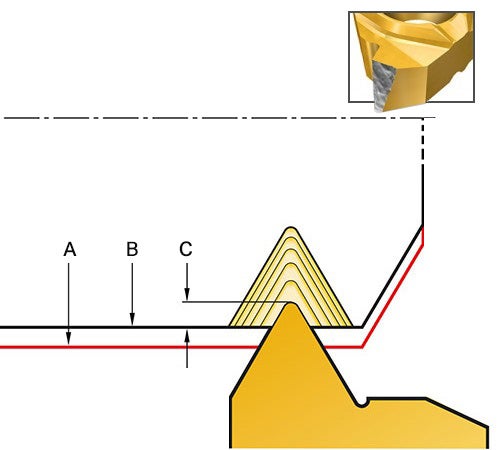
A: Zu groß gedrehter Durchmesser beim Außengewindedrehen
B: Korrekter Außengewindedurchmesser
C: Erster Durchgang, vom Gewindedrehzyklus
Standzeit
Die sorgfältige Betrachtung der Wendeschneidplatte/Schneidkante nach einer Gewindedrehbearbeitung gibt Aufschluss darüber, wie bestmögliche Standzeit und Gewindequalität erreicht werden können.
Die zwei Hauptbearbeitungsparameter, die jeweils Auswirkungen auf die Standzeit haben, sind Schnittgeschwindigkeit und Zustellung. Die Erhöhung einer dieser Parameter verkürzt die Standzeit und erhöht außerdem die Temperatur. Eine zu hohe Temperatur führt zu einer reduzierten Standzeit.
Um eine längere Standzeit zu erzielen, ist es vorteilhafter, zunächst die Zustellung/Spandicke zu optimierten. Bei Erhöhung der Zustelltiefe/Spandicke ist der Temperaturanstieg niedriger als bei der Erhöhung der Schnittgeschwindigkeit. Andererseits kann eine zu große Spandicke zur Überlastung der Wendeschneidplatte führen.
Verwenden Sie Kühlschmierstoff, um die Temperatur zu senken. Untere Präzisionskühlung hat die größte Wirkung.
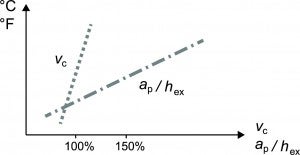
Auswirkung auf die Temperatur bei der Erhöhung von Schnittgeschwindigkeit und Vorschub
Zustellung ap |
|
|
Schnittgeschwindigkeit,vc |
|
|
Spandicke
Bei der Bearbeitung von Werkstoffen die zur Kaltverfestigung neigen, sind niedrige Schnitttiefen und damit Schnitte in die kaltverfestigte Randzone zu vermeiden.
Bei einem Radialschnitt von 0.2 mm (0.008 Zoll) beträgt die Spandicke an den Flanken:
- 0.05 mm (0.002 Zoll) mit 30° Profil
- 0.1 mm (0.004 Zoll) mit 60° Profil
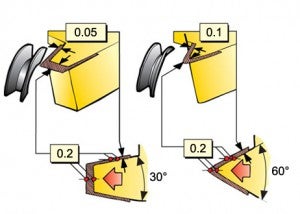
Suchen Sie Werkzeugempfehlungen?
Hier finden Sie unsere Zerspanungswerkzeuge chevron_right
Brauchen Sie Beratung?
Stellen Sie uns eine Frage chevron_right
Was es sonst noch über die Grundlagen unserer Metallzerspanung zu lernen gibt?
Registrieren Sie sich für unser kostenloses E-Learning Programm chevron_right
Wendeplatteneckenradius und Standzeit
Der Eckenradius ist der kleinste Punkt auf der Wendeschneidplatte und kann unter dem extremen Schnittdruck einer Gewindedrehbearbeitung leicht brechen.
Die Eckenradien der verschiedenen Wendeschneidplattentypen sind sehr unterschiedlich. Daher sollte für optimierte Performance und Prozesssicherheit die Schnittgeschwindigkeit und die Anzahl der Durchgänge berücksichtigt werden.
Wendeschneidplatten für NPT- und NPTF-Gewindeprofile verfügen über den kleinsten Eckenradius im Standardbereich. Für optimale Leistung ist die Anzahl der Durchgänge zu erhöhen und die Schnittgeschwindigkeit zu reduzieren.
Die Wendeschneidplatte für Innengewinde hat einen wesentlich kleineren Eckenradius als die Wendeschneidplatte für Außengewinde.
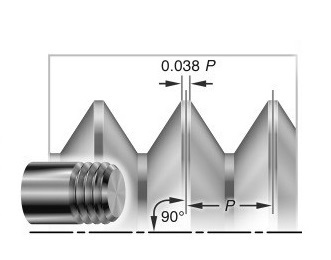
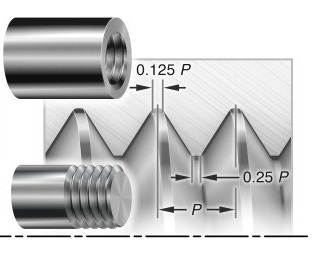
Vorbearbeitung mit einem Drehwerkzeug
Sowohl Produktivität als auch Standzeit können durch die Vorbearbeitung des Gewindes mit einem Drehwerkzeug mit einer 55° oder 60° Wendeschneidplatte vor dem abschließenden Schlichtschnitt mit einem Gewindewerkzeug verbessert werden.
Bei der Bearbeitung von Gewindespitze und -kern mit kleinen Radien kann eine vergleichbare Vorbearbeitung auch durch eine Schruppbearbeitung mit einer Wendeschneidplatte mit gleichem Winkel, jedoch größerem Eckenradius verwendet werden. Es verbleibt dann ein Aufmaß für die restlichen Schlichtschnitte, die mit der Wendeschneidplatte zum Gewindedrehen durchgeführt werden.
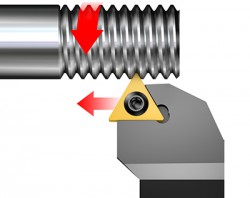
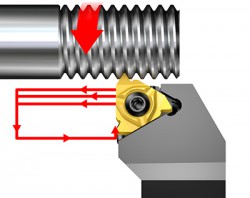
Entgraten
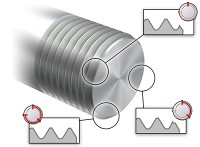
Entgraten am Gewindeanfang
Gratbildung tritt häufig am Gewindeanfang auf, bevor die Wendeschneidplatte das vollständige Profil erstellt. Dies gilt insbesondere im Bereich der Hydraulik- und Lebensmittelindustrie, wo die Anforderungen bezüglich Toleranz und Qualität besonders hoch sind.
Am häufigsten tritt Gratbildung bei rostfreien Stählen und Duplex-Werkstoffen auf.
Das Entgraten von Gewinden lässt sich mit Standarddrehwerkzeugen durchführen. Hier ist insbesondere auf die richtige Position der Wendeschneidplatte zum Entgraten im Verhältnis zum Gewinde, zur Steigung und m Gewindezyklus zu achten.
Entgraten von Gewinden
- Wählen Sie einen Standardgewindezyklus mit den empfohlenen Zustellwerten. Das Werkzeug sollte in das Gewinde bei einem Winkel von 45° eintreten.
- Wählen Sie das gleiche Gewindedrehprogramm mit der gleichen Schnittgeschwindigkeit, einer Wendeschneidplatte zum Gewindedrehen und halb so vielen Durchgängen. Programmieren Sie die Entgratlänge vor dem 45° Austritt auf 1 x Steigung und vermessen Sie die Nullpunkte entsprechend der Abbildung unten.
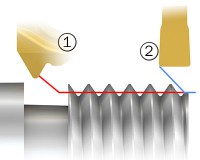
Einstellhinweise
- Nullpunkt der Wendeschneidplatte zum Gewindedrehen einstellen
- Nullpunkt der Wendeschneidplatte messen
- Wendeschneidplatte zum Ein- und Abstechen um 'z' versetzen
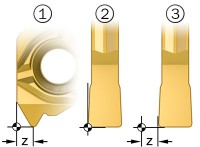
Entgraten des Gewindedurchmessers
Beim Drehen eines Gewindes mit einer Teilprofil-Wendeschneidplatte wird oft ein Grat an der Gewindespitze gebildet. Dieser Grat muss entfernt werden, um ein hochwertiges Gewinde zu erhalten.
Mehrgängiges Gewinde
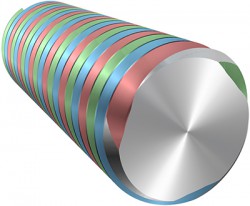
Gewinde mit zwei oder mehreren parallelen Gewindenuten erfordern zwei oder mehrere Gewindeanfänge. Der Steigungswinkel bei einem solchen Gewinde ist mindestens zweimal so groß wie bei einem eingängigen Gewinde.
Der Steigungswinkel nimmt relativ zur Steigung zu, und zwar um einen Faktor, der der Anzahl der Gewindegänge entspricht:
- Eingängiges Gewinde - Steigungswinkel entspricht der Steigung
- Zweigängiges Gewinde - Steigungswinkel entspricht dem 2-fachen der Steigung
- Dreigängiges Gewinde - Steigungswinkel entspricht dem 3-fachen der Steigung usw.
Zur Herstellung eines mehrgängigen Gewindes ist zunächst eine einzelne Gewindenut in einer bestimmten Anzahl von Durchgängen herzustellen, gefolgt von einer zweiten Gewindenut in einer bestimmten Anzahl von Durchgängen, dann eine dritte Gewindenut in einer bestimmten Anzahl von Durchgängen.
Die Wahl der richtigen Zwischenlage ist entscheidend. Nehmen Sie den Vorhaltewert zur Berechnung des korrekten Neigungswinkels (Steigungswinkel) und wählen Sie die entsprechende Zwischenlage. Siehe Abschnitt: Wahl der Wendeschneidplatte und Zwischenlage in Gewindedrehanwendungen.
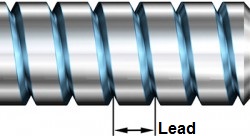
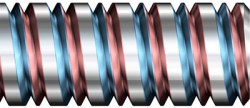
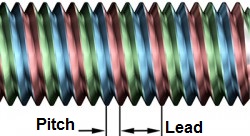
Einstellung des Halters zur Außenbearbeitung
Bei einer doppelt oder dreimal so hohen Steigung wird der Eintrittswinkelt (Steigungswinkel) drastisch geändert und im Extremfall nicht durch die verfügbaren Zwischenlagen abgedeckt. Für diese extremen Fälle kann der Halter für die Außengewindebearbeitung in Richtung des Steigungswinkels gefräst/geschliffen werden.
- Die Zwischenlagen dürfen nicht geschliffen werden. Dies beeinträchtigt die Stabilität des kompletten Systems.
- Berechnen Sie den Eintrittswinkel φ (Steigungswinkel) und bestellen Sie einen Sonderwerkzeughalter
- Eine große Steigung bei kleinem Durchmesser führt zu einem großen Steigungswinkel
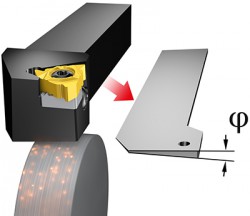
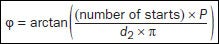
Suchen Sie Werkzeugempfehlungen?
Hier finden Sie unsere Zerspanungswerkzeuge chevron_right
Brauchen Sie Beratung?
Stellen Sie uns eine Frage chevron_right
Was es sonst noch über die Grundlagen unserer Metallzerspanung zu lernen gibt?
Registrieren Sie sich für unser kostenloses E-Learning Programm chevron_right