Drehen von exotischen Werkstoffen
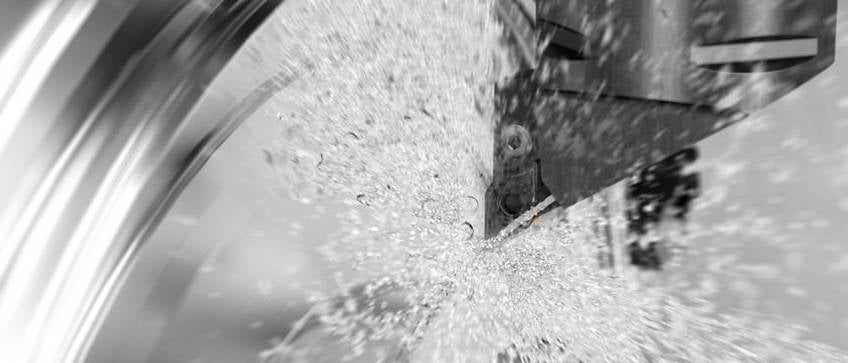
Hitzebeständige Superlegierungen und Titanlegierungen sind anspruchsvoll in der Bearbeitung. Es handelt sich um Metalle mit speziellen und damit eher exotischen Eigenschaften. Sie weisen hervorragende Merkmale auf, wie beispielsweise das Verhältnis von Festigkeit zu Gewicht, die Beibehaltung von Festigkeit und Härte bei hohen Temperaturen und eine ausgezeichnete Korrosionsbeständigkeit.
Da diese Werkstoffe aber auch schwer zerspanbar sind, benötigen sie „exotische“ Lösungen. Diese müssen mit speziellen Werkzeugen und sorgfältig ausgewählten Verfahren und Werkzeugwegen gut geplant werden, um Effizienz, Sicherheit und gute Ergebnisse zu erzielen.
Dieser Überblick befasst sich mit den Bearbeitungsanforderungen und Entwicklungen, die die Leistung und Prozesssicherheit beim Drehen erhöht haben.
Einzigartige Bauteileigenschaften, verbunden mit hohen Anforderungen bei der Bearbeitung
Die Zerspanbarkeit eines Bauteilwerkstoffs wird von mehreren Faktoren bestimmt, die die Anforderungen und Ergebnisse der Zerspanung beeinflussen. Im weitesten Sinne handelt es sich dabei um die Zerspanbarkeit des Bauteilwerkstoffs in Bezug auf die Neigung zum Werkzeugverschleiß und die Spanbildung. Mit dem Unterschied, dass sich diese exotischen Materialien in den meisten Fällen schlecht bearbeiten lassen. Sie gelten als anspruchsvoll, sind jedoch bei der richtigen Herangehensweise gut zerspanbar.
Die exotischeren, relativ häufig vorkommenden Werkstoffe werden in die Gruppe ISO S eingeordnet: hitzebeständige Superlegierungen (HRSA) und Titanlegierungen. Für die Bearbeitung können sie in mehrere Untergruppen unterteilt werden, je nach Zusammensetzung, Zustand und Eigenschaften. Die chemische Beschaffenheit und die metallurgische Zusammensetzung einer mit „S“ klassifizierten Legierung bestimmen die physikalischen Eigenschaften und damit die Zerspanbarkeit. Die Spankontrolle ist aufgrund der Segmentierung der Späne im Allgemeinen anspruchsvoll, und es ist nicht ungewöhnlich, dass die spezifische Schnittkraft doppelt so hoch ist wie die von Stahl - der Maßstab zur Beschreibung des Zerspanungsgrades eines Werkstoffs und Bestimmung der erforderlichen Schnittkraft und Leistung.
HRSA-Werkstoffe sind insbesondere aufgrund ihrer hohen Festigkeit auch bei hohen Temperaturen schwer zerspanbar. Sie erweichen und fließen nicht wie die meisten anderen Werkstoffe, und sie lassen sich auch leicht aushärten. An der Schneidkante entsteht eine hohe mechanische Belastung und große Hitze. Legierungen auf Nickel-, Eisen- oder Kobaltbasis sind Untergruppen von HRSA-Werkstoffen, die sich insbesondere in der Luftfahrt, der Energiewirtschaft und der Medizintechnik gut für die Verwendung als Bauteile eignen, da sich ihre vorteilhaften Eigenschaften erst in der Nähe ihres Schmelzpunkts stark verändern. Sie sind auch sehr korrosionsbeständig. Unter dem Gesichtspunkt der Zerspanbarkeit benötigen sie jedoch eine leistungsfähige Maschine, präzise Einrichtbedingungen, spezielle Wendescheidplattensorten und -geometrien, einen optimierten Kühlschmierstoffeinsatz und nicht zuletzt das richtige Bearbeitungsverfahren und den richtigen Werkzeugansatz. Auf jeden Fall ist eine vertiefte Planung und Mehrarbeit im Vorfeld der Produktion erforderlich.
Titanlegierungen werden auch in Untergruppen mit unterschiedlicher Bearbeitbarkeit eingeteilt. Im Allgemeinen wird die Zerspanbarkeit eher schlecht eingestuft (Zähigkeit). Dies führt zu besonderen Anforderungen an Werkzeuge und Verfahren. Die Anforderungen entstehen durch die niedrige Wärmeleitfähigkeit, die hohe Festigkeit bei hohen Temperaturen, stark gescherte, dünne Späne mit Neigung zum Kaltverschweißen, die eine schmale Kontaktfläche auf der Spanfläche der Wendeschneidplatte erzeugen und hohe, nahe an der Schneidkante konzentrierte Schnittkräfte. Die Späne können sich zyklisch bilden. Dies führt zu unterschiedlichen Schnittkräften, und einige Legierungen weisen einen relativ hohen Karbidgehalt auf, der den Werkstoff besonders abrasiv macht. Bei zu hohen Schnittgeschwindigkeiten kann es zu einer chemischen Reaktion zwischen Span und Werkzeugmaterial kommen, die zu plötzlichen Abplatzungen/Brüchen an der Schneidkante und auch zu Materialadhäsion/Aufschweißungen an den Schneiden führt. Einige Legierungen lassen sich auch leicht kaltverfestigen. Dies führt zu diffusionsartigem Verschleiß und damit zu übermäßiger Gratbildung. Dies kann auch die folgenden Bearbeitungsvorgänge erschweren.
Es handelt sich bei vielen HRSA-Werkstoffen und Titanlegierungen um eher exotische Werkstoffe mit einem relativ kleinen Fenster, in dem eine erfolgreiche Bearbeitung möglich ist.
Beim Drehen dieser Werkstoffe ...
... hängt der Erfolg von der Ausgewogenheit der kombinierten Wirkung von Werkstoff und Anwendungsfaktoren ab. Es gibt einige grundlegende Faustregeln, die wesentlich zu guten Ergebnissen beitragen:
- Planen Sie eine solide, möglichst detaillierte Bearbeitungsstrategie im Voraus.
- Legen Sie den besten Werkzeugansatz fest.
- Legen Sie die besten Werkzeugwege fest und verwenden Sie eine sehr stabile Werkzeugaufnahme.
- Verwenden Sie neue, spezielle Werkzeugtechnologien.
- Verwenden Sie qualifizierte Schnittdaten zur Herstellung von Prozesssicherheit und Produktivität.
- Verwenden Sie die spiralförmige Schnittlängenberechnung zur Vorhersage von Schnitten.
- Setzen Sie Kühlschmiermittel als moderne Hochdrucklösung richtig ein.
- Holen Sie sich Empfehlungen und die Unterstützung von Spezialisten ein.
Der Bearbeitungsprozess sollte immer sorgfältig geplant werden, da kritische, entscheidende Faktoren berücksichtigt werden müssen, wie beispielsweise die Einbeziehung des Zustands des Werkstückmaterials. Gegossenes, geschmiedetes, stangenförmiges Material, Wärmebehandlung, Lösungsbehandlung und Alterung beeinflussen das Bauteil in einer Weise, die bei der Auswahl der Werkzeuge und Verfahren berücksichtigt werden muss. Die Oberflächenbeschaffenheit der Werkstücke ist unterschiedlich und wirkt sich ebenso wie die Härte auf die Bearbeitung aus. Die Strategie für das Drehen sollte auch die Anforderungen berücksichtigen, die sich aus den Konstruktionsmerkmalen des zu bearbeitenden Werkstücks ergeben. Dies gilt auch für die verschiedenen Bearbeitungsstufen, d. h. Schruppen (erste Stufe), Vorschlichten (Zwischenstufe) und Schlichten (letzte Stufe). Komplexe Merkmale und die Oberflächengüte sind wichtige Aspekte.
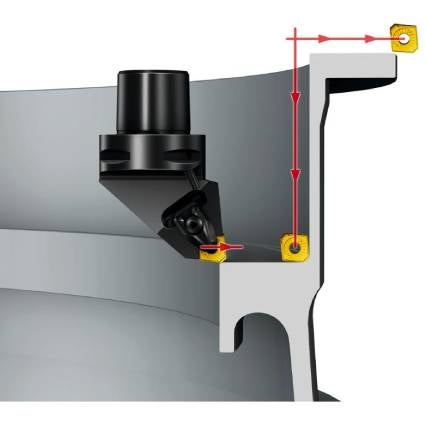
Bei der Planung der Drehbearbeitung von exotischen Werkstoffen sind die Bauteilkonstruktion, der Werkstoff und der Zustand die Grundlage. Legen Sie gegebenenfalls fest, wie die Vor-, Zwischen- und Fertigbearbeitung in Abhängigkeit von der Materialbeschaffenheit und den Qualitätsanforderungen durchgeführt werden soll. Die Planung der Werkzeugwege und Anwendung der Vorschubreduzierung bei der Programmierung bestimmen das Ausmaß des Verschleißes, die Art des Werkzeugs, die Zykluszeiten und die Sicherheit.
Der Zerspanungsvorgang bei diesen Werkstoffen ...
... wird in hohem Maße von der Annäherung der Schneidkante an das Werkstück beeinflusst. Der Eintrittswinkel der Schneidkante in Kombination mit der Wendeschneidplattengeometrie bestimmt die Leistung, die Standzeit, die Sicherheit und die Ergebnisse. Die Form der Wendeschneidplatte muss in vielen Fällen in Abhängigkeit von dem zu erstellenden Schnitt gewählt werden. Dass die Verwendung eines kleinen Eintrittswinkels zur Leistung und zur Standzeit des Werkzeugs beiträgt, sollte jedoch immer eine wichtige Überlegung für die Anwendung sein.
Die Wahl der Wendeplattensorte muss zum Teil in Abhängigkeit vom Eintrittswinkel getroffen werden. Dieser Winkel beeinflusst unter anderem die Art des Verschleißes, der eine Kerbe an der Schneide bildet, deren Größe das Ergebnis beeinflusst und zu einem vorzeitigen Werkzeugausfall führen kann. Die richtige Vorgehensweise bei der Anwendung umfasst auch, dass eine Wendeschneidplattensorte gewählt werden kann, die eine höhere Produktivität ermöglicht und gleichzeitig eine lange Standzeit und Prozessstabilität bietet.

Der Eintrittswinkel des Schneidwerkzeugs beeinflusst die Spandicke, die Vorschubgeschwindigkeit, die Schnittkräfte sowie die möglichen Schnittarten. Bei exotischen Werkstoffen hat die Wahl des Winkels direkte Auswirkungen auf die Produktivität und die Prozesssicherheit, da sie die Form der Wendeschneidplatte und den Schneidenradius sowie die Nutzung des Werkzeugmaterials beeinflusst. In der Regel sind runde Wendeschneidplatten und Xcel-Ausführungen die beste Wahl.
Bei der Wahl des Schneidstoffs (Wendeschneidplattensorte) sollte die Art der Drehbearbeitung (Schruppen, Vorschlichten oder Schlichten) sowie die Werkstückbeschaffenheit und die Art des Schnitts berücksichtigt werden. Aufgrund der Härte dieser Werkstoffe sollte die plastische Verformung der Schneidkante immer als primärer Risikofaktor bei der Auswahl der Wendeplattensorte berücksichtigt werden (der Kolkverschleiß wird, wie bereits erwähnt, hauptsächlich durch den Eintrittswinkel und die Schnitttiefe beeinflusst). Die Wahl der Wendeplattensorte sollte auch mit der Form der Wendeplatte kombiniert werden, da dies die Festigkeit mitbestimmt, die zusammen mit der Annäherung, der Spanbelastung und der Frage, ob der Schnitt kontinuierlich oder unterbrochen ist, bewertet werden muss. Spezielle Sorten sind daher für die HRSA-Bearbeitung unerlässlich.
Eine hohe Warmfestigkeit der Wendeschneidplatte, die richtige Zähigkeit und eine ausreichende Haftung der Beschichtung der Wendeschneidplatte sind die wichtigsten Anforderungen. Eine positive Schneidgeometrie, eine scharfe Schneidkante, eine starke Schneide und ein vergleichsweise offener Spanbrecher sollten die Wendeschneidplatte für diese Werkstoffe kennzeichnen.
Die Ermittlung der am besten geeigneten Schnittdaten ist für den Erfolg bei diesen Werkstoffen ebenso entscheidend. Die Schnittgeschwindigkeit wird durch die Kombination von Drehzahl, Vorschub und Schnitttiefe bestimmt und kann für ein hohes Maß an Produktivität, Sicherheit und Qualität optimiert werden. Die Schnittgeschwindigkeit hängt mit der Wärmeentwicklung und deren Auswirkungen auf die Wendeschneidplatte zusammen. Sie muss hoch genug sein, damit der Span eine ausreichende Plastizität aufweist, aber nicht zu hoch, um das Werkzeugmaterial nicht aus dem Gleichgewicht zu bringen. Die Geschwindigkeiten liegen in der Regel im Bereich von 40 bis 80 m/min bei speziellen Hartmetall-Wendeschneidplatten und 150 bis 400 m/min bei Keramik-Wendeschneidplatten.
Die Vorschubgeschwindigkeit ist der Hauptfaktor, der die Schnittzeit und die Spandicke beeinflusst. Bei exotischen Werkstoffen muss dies sorgfältiger abgewogen werden, da die Grenzen relativ eng gesetzt sind. Beim Schruppen muss der Span so groß wie möglich sein, darf aber die Schneidkante nicht überlasten, während beim Schlichten der Span dick genug sein muss, um übermäßige Hitze und Kaltverfestigung zu vermeiden.
Die Schnitttiefe wirkt sich oft auf die Annäherung an die Schneidkante aus und muss daher unter einem bestimmten Wert liegen. Bei der Verwendung von runden Wendeschneidplatten in HRSA sollte die Schnitttiefe beispielsweise 15 % des Wendeplattendurchmessers nicht überschreiten. Auch die Schnitttiefe muss beim Profilfräsen sorgfältig programmiert werden. Es entstehen Aussparungen oder Ecken, damit der geeignete Eingriffsbogen nicht überschritten wird.
Im Hinblick auf die Standzeit ist es wichtig, sich ausgiebig mit der Spiralschnittlänge (SCL) zu beschäftigen. Eine korrekte Festlegung bedeutet, dass Maschinenstopps für den Wendeschneidplattenwechsel vorhergesagt und programmiert und Durchgänge mit einem Werkzeug, das mit der richtigen Schnittgeschwindigkeit eingesetzt wird, durchgeführt werden, ohne die geforderte hohe Oberflächenqualität zu beeinträchtigen.
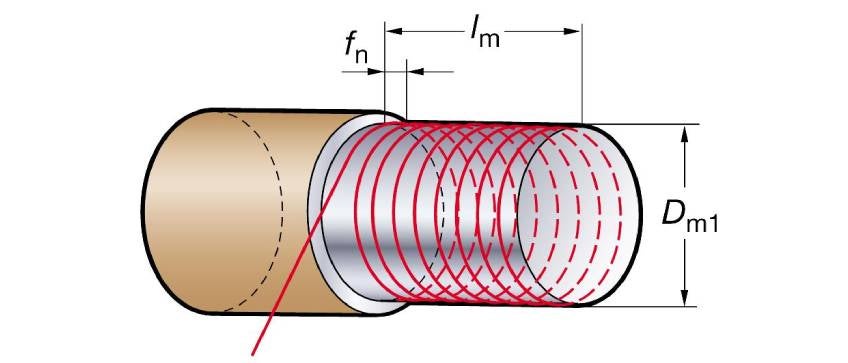
Die Berechnung der Spiral-Schnittlänge hilft bei der Vorhersage der Zeit oder der Schnittlänge, um die Bearbeitungszeit zu reduzieren und die Oberflächengüte bei anspruchsvollen exotischen Materialien zu verbessern. Die Maschinenstopps für den Wendeschneidplattenwechsel werden dann mit einem Spiral-Längsschnitt geplant, um den Arbeitsgang und die Schnittdaten besser zu berücksichtigen und die Standzeit und Maschinenauslastung zu optimieren.
Der Werkzeugverschleiß wird stark beeinflusst ...
... durch die hohen Zerspanungskräfte in Verbindung mit höheren Schneidkantentemperaturen, wobei sich bestimmte Arten von Schneidkantenverschleiß entwickeln können. Die wichtigsten Verschleißarten sind der erwähnte Kerbverschleiß (die mechanische Verschleißart, bei der die konstante Schnitttiefe eine Markierung/Kerbe an der Hauptschneide hinterlässt); ferner die plastische Verformung der Schneidkante als Folge der hohen Temperatur und des hohen Drucks und drittens der abrasive Verschleiß, der hauptsächlich durch die härteren Werkstoffe inklusive ihrer Legierungselemente verursacht wird. Ein weiterer Verschleißtyp sind Abplatzungen auf der Spanfläche, die bei der Bearbeitung mit Keramik-Wendeplattenauftreten, wenn die Schnittgeschwindigkeit bzw. der Wärmeeintrag nicht groß genug ist.Der Schneidkantenansatz spielt eine große Rolle.
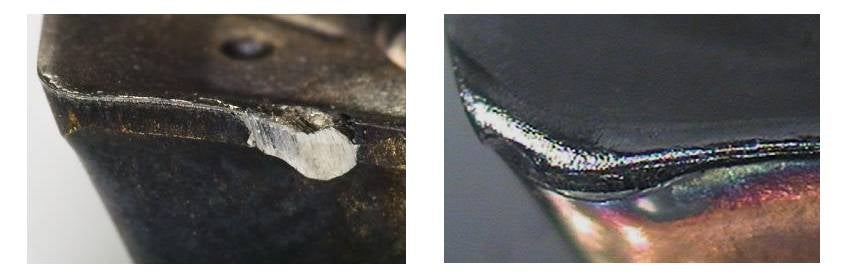
Die Wahl der Wendeschneidplattensorte ist bei exotischen Werkstoffen nicht auf die gleiche Weise direkt mit dem Schruppen und Schlichten verbunden wie bei anderen Materialien. Stattdessen ist die Wahl der Sorte eher ein Optimierungsfaktor. Sie ist etwas komplexer und abhängig von der Form der Wendeschneidplatte, dem Schneidkantenansatz und der Art der Bearbeitung. Destruktive Verschleißmuster, wie der dargestellte Kerbverschleiß und die plastische Verformung, müssen insbesondere durch eine Kombination von geeigneten Werkzeugen, Schnittdaten und Verfahren eingedämmt werden. Hartmetall-Wendeschneidplatten sowie mit moderner Sialon-Keramik und bis zu einem gewissen Grad auch Whisker-Keramik sind oft die am besten geeignete Wahl.
Für die Drehbearbeitung von exotischen Werkstoffen ist ein kleiner Eintrittswinkel von 45 Grad oder weniger am besten geeignet. Am ungünstigsten ist es, wenn der Eintrittswinkel 90/0 Grad beträgt oder wenn die Schnitttiefe größer ist als der Schneidenradius der Wendeschneidplatte. Ein großer/kleiner Winkel führt zu einem dünnen Span und höheren Vorschüben.
Beim HRSA-Drehen bestimmt der Eintrittswinkel des Werkzeugs, ob eine PVD- oder CVD-beschichtete Wendeschneidplatte am besten geeignet ist. Dies dient dem Schutz vor thermischen Einflüssen. PVD ist für einen Eintrittswinkel von 90/0 Grad und CVD für 45 Grad geeignet. Beim Drehen von Titan hingegen wirkt sich die Beschichtung der Wendeplatte nicht aus. In diesem Fall kommt es insbesondere darauf an, dass die Schneidkantenbeschaffenheit optimal ist, beispielsweise eine runde Wendeschneidplatte beim Schlichten. Neue Familien von PVD-Wendeschneidplatten bieten eine hohe Härte und eine gute Beständigkeit gegen Schneidkantenverformung und Thermoschocks. In Kombination mit scharfen Schneidkanten eignen sie sich auch hervorragend für Schrupp- bis Schlichtbearbeitungen von adhäsiven Werkstoffen.
Die richtige Form der Wendeschneidplatte ...
... ist ein wichtiger Anwendungsfaktor bei der Bearbeitung dieser Werkstoffe. Die runde Form (Typ-R) ist zu einer der wichtigsten Empfehlungen für diese Materialien geworden. Die runde Wendeschneidplatte sorgt für Stabilität und eine scharfe, positive Schneidkante, eine Spandicke, die entlang einer langen Schneidkante variiert und hohe Vorschubgeschwindigkeiten ermöglicht, und einen großen Wendeschneidplattenradius, der die Vorschubgeschwindigkeit aufgrund der erzeugten Oberflächengüte nicht einschränkt. Runde Wendeschneidplatten ermöglichen auch Flexibilität bei der Programmierung für das Profil- und Taschenfräsen – Bearbeitungsschritte, die für viele Bauteilformen erforderlich sind.
Eine quadratische Wendeschneidplatte (Typ-S) eignet sich in manchen Fällen am besten für die erste Bearbeitungsstufe, da sie Schruppschnitte in verschiedenen Richtungen mit einem Winkel von 45 Grad ausführen kann. Die rautenförmige (Typ-C) Wendeschneidplatte bietet eine hohe Flexibilität in Bezug auf die Werkzeugwege und, wenn sie zu einer Xcel-Wendeschneidplatte erweitert wird, eine noch bessere Zugänglichkeit der Werkzeuge in Ecken und Taschen. Diese Kombination aus Wendeschneidplattenform und 45-Grad-Eintrittswinkel reduziert auch die radialen Schnittkräfte, sorgt für eine konstante Spandicke und verringert den Ausfräsungsverschleiß. Das Ergebnis sind bessere Produktivität, hohe Standzeit und mehr Sicherheit.
Die Programmoptimierung ...
... ist wichtig, und im Folgenden werden einige Empfehlungen zur Verbesserung der Leistung gegeben, insbesondere bei der Verwendung von runden Wendeschneidplatten, die grundsätzlich für exotische Werkstoffe geeignet sind:
- Vermeiden Sie das Eintauchen in Schnitte und mildern Sie Stöße ab. Wenn diese Schnitte erforderlich sind, halbieren Sie den Vorschub.
- Bei einer Ecke sollte der Vorschub ebenfalls um die Hälfte reduziert werden oder das Werkzeug sollte in die Ecke einrollen, wobei der programmierte Radius dem Durchmesser der Wendeschneidplatte entspricht. (Als Richtwert gilt, dass der programmierte Radius mindestens 25 % des Durchmessers der Wendescheidplatte und der Werkstückradius 75 % des Durchmessers der Wendescheidplatte betragen sollte. Der Vorschub der Werkzeugmitte gilt für den programmierten Radius.)
- Beim Schruppen mit runden Wendeschneidplatten muss der programmierte Radius dem Durchmesser der Wendeschneidplatte entsprechen, beim Schlichten muss der programmierte Radius größer als der Durchmesser der Wendeschneidplatte sein.
- Ziehen Sie alternative Werkzeugwege, mehrere Durchgänge und die Bearbeitung in beide Richtungen in Betracht, um die Wendeschneidplatten vollständig zu nutzen.
- Schützen Sie Keramik-Wendeschneidplatten, indem Sie das Werkstück vorfasen und in die Anfasung einführen.
- Halten Sie während der gesamten Bearbeitung ein zufriedenstellendes Gleichgewicht zwischen Eintrittswinkel und Wendeplatten-Eingriffsbogen aufrecht. Die Begrenzung des Winkels ist für eine gute Leistung von entscheidender Bedeutung, und die Verwendung runder Wendeschneidplatten ist eine wichtige Voraussetzung für die Ausschöpfung des vorhandenen Potenzials mit modernen Wendeschneidplattensorten.
- Vermeiden Sie beim Profil- und Tauchfräsen Umschlingungseffekte, um die Wendeschneidplatte nicht zu überlasten. Verwenden Sie alternative Werkzeugwege oder kleinere Plattendurchmesser.
- Erwägen Sie das trochoidale Drehen, bei dem der Schnitt in geeignete kleinere Teile, insbesondere beim Taschenfräsen aufgeteilt wird.
Worauf sollten Sie bei Werkzeugtypen und Verfahren für die HRSA- und Titanbearbeitung achten? Nachfolgend einige wichtige Aspekte:
- Präzisionskühlschmierstoff sollte immer in die Überlegungen miteinbezogen werden. Mit Präzisionsdüsen, die hinter und an der Schneidkante wirken und von durchströmten Werkzeugen gespeist werden, lassen sich viele Vorteile bei Dreh-, Fräs- und Bohrbearbeitungen erzielen. Modernste Düsentechnologie, die als Standard- und Sonderlösungen mit verschiedenen Druckbereichen erhältlich ist, kann bei allen Maschinentypen mit ausreichender Kühlmittelzufuhr eingesetzt werden. Der Kühlmitteldruck sollte bei neuen Maschinen immer einen möglichen Kühlmitteldruck von 70 bar für das Titandrehen beinhalten, um einen besseren Spanbruch zu ermöglichen. Ein Druck von bis zu 200 bar empfiehlt sich für das HRSA-Drehen aufgrund der härteren Späne.
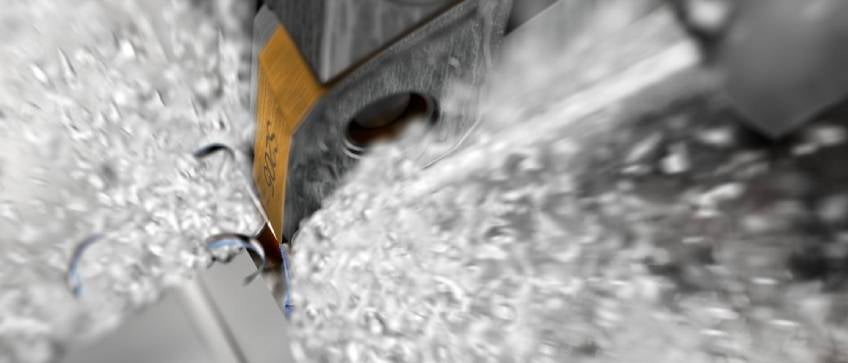
Bei der Bearbeitung von exotischen Werkstoffen ist der Einsatz von Kühlschmierstoffen ein entscheidender Anwendungsfaktor. Präzisions-Kühlschmierstoff ist heute als Hightech-Anwendung bereits Standard und so effizient, dass er einen deutlichen Unterschied in Bezug auf den Schnitt, die Spanbildung, die Standzeit und die Produktivität ausmacht. Die hohen Temperaturen, die in diesen Werkstoffen entstehen, machen im Allgemeinen eine Kühlung erforderlich. Wenn das Kühlmittel jedoch reichlich, mit hohem Druck und präzise dosiert in Kombination mit speziellen Wendeschneidplatten und einer Kühlmittelzufuhr durch das Werkzeug eingesetzt wird, werden Leistung und Ergebnisse optimiert.
- Die Zugänglichkeit ist oft ein Problem beim Drehen von exotischen Werkstoffen. Komplexe Merkmale und große Werkzeugüberhänge erfordern den richtigen Einsatz von Werkzeugen und Bearbeitungsmethoden. Schauen Sie sich die modularen Werkzeugsysteme aus Adaptern und Schneidköpfen/Schneideinsätzen mit zahlreichen unterschiedlichen Geometrien und Sorten für die Bearbeitung mit unterschiedlichen Überhängen an. Das Angebot an Adaptern und auswechselbaren Schneidköpfen/Schneideinsätzen erlaubt den Aufbau beliebiger Werkzeuge aus einem Minimalbestand an Standardwerkzeugen. Der zusätzliche Freiraum steht sowohl für die Außen- auch für die Innenbearbeitung zur Verfügung, sodass jeder Schneidkopf in beiden Konfigurationen genutzt werden kann. Die Schneideinsätze erlauben die erforderlichen radialen und axialen Freiräume, um mit Präzisions-Kühlschmierstoff, der durch das Werkzeug zur Schneidkante geleitet wird, tief in gewinkelte Nuten zu gelangen.
- Das Werkzeugmaterial ist das Herzstück des Bearbeitungsvorgangs, und bei exotischen Werkstoffen ist es ein entscheidender Faktor. In diesem Bereich sind spezielle Wendeschneidplattensorten in Kombination mit der richtigen Geometrie erforderlich, hauptsächlich durch Einsatz neuester Hartmetalle und Keramiken. Unbeschichtete Hartmetallsorten nehmen nach wie vor eine wichtige Stellung ein, aber die neuesten Entwicklungen in der Beschichtungstechnologie für Wendeschneidplatten haben speziell beschichtete Hartmetall-Wendeschneidplatten hervorgebracht, die durch eine Verkürzung der Schnittzeit und eine Verlängerung der Standzeit die Leistungsfähigkeit der Zerspanung erhöht haben.
- Bohrstangen, Einsätze und Fräser sollten über integrierte Schwingungsdämpfung verfüge, um die Vibrationsneigung zu minimieren. Die Anti-Vibrations-Technologie hat große Entwicklungsfortschritte gemacht und sollte immer in Betracht gezogen werden, wenn Werkzeugüberhänge Instabilitätseffekte hervorrufen. Produktivität, Prozesssicherheit und Bauteilqualität sind Faktoren, die direkt mit der Qualität und Verfügbarkeit von schwingungsgedämpften Werkzeugen zusammenhängen. Zahlreiche Bearbeitungsvorgänge sind ohne diese Funktion nicht durchführbar: Heute kann das Innendrehen mit Überhängen von bis zu 14xD und bis zu 250 mm sehr effizient und mit hoher Oberflächengüte durchgeführt werden.