Eine grünere Zukunft für die Luftfahrt
Hersteller moderner Flugzeuge sehen sich zunehmend gezwungen, eine ganzheitliche Betrachtungsweise bei der Produktion ihrer Bauteile anzuwenden.
Als einer der größten Verursacher der weltweiten CO2-Emissionen steht die Luftfahrtindustrie unter großem Druck, umweltfreundlichere Flugzeuge zu entwickeln, die leichter sind und längere Strecken zurücklegen können. Um dies zu erreichen, müssen jedoch schwierig zu bearbeitendes Aluminium und hitzebeständige Superlegierungen (HRSA) eingesetzt werden. Nachfolgend erklärt Sébastien Jaeger, Industry Solution Manager für Luftfahrtkomponenten bei Sandvik Coromant, wie Hersteller in der Luftfahrtindustrie fortschrittliche Werkzeuglösungen einsetzen können, um anspruchsvolle Werkstücke nachhaltig zu bearbeiten.
Laut dem Weltwirtschaftsforum (WEF) wird das Erreichen einer vollständigen Vermeidung von CO2-Emissionen bis 2050 nicht nur dazu beitragen, eine ökologisch nachhaltige Zukunft zu gestalten, sondern auch eine finanziell widerstandsfähige und wettbewerbsfähige Luftfahrtindustrie als Ganzes zu gewährleisten. Während sich die E-Mobilität in der Automobilindustrie jedoch zunehmend durchsetzt, im August 2021 überholten in Großbritannien die Verkäufe von Elektrofahrzeugen die Verkäufe von Dieselfahrzeugen, wird es in der Luftfahrt länger dauern, bis diese Entwicklungen umgesetzt werden können.
Es wird erwartet, dass eine flächendeckende Elektrifzierung von Flugzeugen nicht vor 2035 umgesetzt wird. Lonely Planet berichtet, dass easyJet davon ausgeht, bis 2030 auf Strecken unter 500 km elektrisch betriebene Flugzeuge einsetzen zu können und Norwegen bis 2040 alle Kurzstreckenflüge elektrisch betreiben will. „Jedoch sind in absehbarer Zeit keine Langstreckenflüge mit wiederaufladbaren Großflugzeugen möglich: Die Batterien sind einfach zu schwer.“
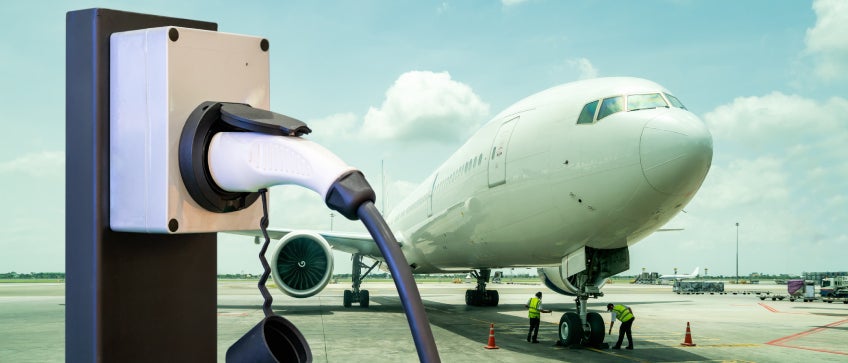
Elektrifizierte Flugzeuge werden voraussichtlich im Jahr 2035 weit verbreitet sein.
Während die Batterien also immer leichter werden müssen, um wirtschaftlich zu werden, sind die Hersteller zunehmend gefordert, leichtere Komponenten herzustellen, um das Problem auszugleichen. Wir können sicher sein, dass Aluminium, insbesondere neue Aluminiumsorten mit höherer Festigkeit, Ermüdungsbeständigkeit und weiteren Eigenschaften, verwendet werden, um diese Systeme leichter zu machen.
Wir beobachten auch einen verstärkten Einsatz neuer hitzebeständiger Superlegierungen (HRSA). HRSA wird bereits in Flugzeugteilen verwendet, die extremen Leistungsanforderungen ausgesetzt sind, da sie ihre Härte auch bei großer Hitze beibehalten. Diese Materialeigenschaften werden ein entscheidender Faktor, da ein Ansatz für einen nachhaltigeren Flugverkehr darin bestehen wird, die Triebwerke härter und heißer zu machen.
Darüber hinaus müssen die Bauteile mit engeren Toleranzen und in vielfältigeren Ausführungen hergestellt werden. Wie bei den Elektrofahrzeugen, werden sich auch die elektrifizierten Flugzeuge von morgen, einschließlich der Flugzeugzellen und der Triebwerke, von Hersteller zu Hersteller stärker unterscheiden als bei den jetzigen Flugzeugen mit Verbrennungstriebwerk. Bei Flugzeugzellen erforschen einige Hersteller Konzepte mit Deltaflügeln, übergangslosen Flügel-Rumpf-Verbindungen und verstrebten Flügeln. Andere Hersteller halten an der traditionellen Bauweise mit großen Flügeln und damit verbundenen Triebwerken fest.
Es werden auch verschiedene Triebwerksarchitekturen entstehen, wie beispielsweise elektrifizierte, batteriebetriebene, elektromagnetische Motoren oder Hybridmotoren, bei denen die derzeitigen Triebwerke von Elektromotoren unterstützt werden. Die Hersteller müssen eine zunehmende Vielfalt von Komponenten mit engen Toleranzen fertigen und gleichzeitig neue Wege finden, um Betriebsgeräusche, Gewicht und Emissionen zu reduzieren. Dies sind alles Faktoren, die die Leistung elektrischer Systeme beeinflussen. Aluminium- und HRSA-Bauteile sind jedoch schwer zu bearbeiten, sodass es eine Herausforderung sein wird, dies nachhaltig und kostengünstig umzusetzen.
Schnelle Fortschritte
Ein Weg zur Herstellung leichterer und treibstoffeffizienterer Flugzeuge führt über additive Fertigungsverfahren. Die additive Fertigung ermöglicht die Entwicklung sehr komplex geformter, kundenspezifischer Teile und funktionaler Produkte mit engen Toleranzen, sodass schwer zu bearbeitende Teile wie Gitter einfacher bearbeitet werden können. Nach Erkenntnissen des Softwareunternehmens Dassault Systèmes ( ) kann „in der Luftfahrt eine Gewichtsreduzierung durch additive Fertigung zu Energieeinsparungen von bis zu 25 Prozent führen“, und „jedes Kilogramm weniger Fluggewicht kann jährlich bis zu 3.000 US-Dollar an Treibstoffkosten einsparen.“
Ist additive Fertigung auch nachhaltig? In einer Studie, die von der Abteilung für Fertigungstechnik an der Technischen Universität Cluj-Napoca in Rumänien mitverfasst wurde, wird additive Fertigung als „eine hervorragende Alternative zu traditionellen Fertigungsverfahren wie Spritzguss, Druckguss oder maschinelle Bearbeitung“ beschrieben. In der Studie wird festgestellt: „Additive Fertigung hat das Potenzial, Kosten zu senken und energieeffizienter zu sein als herkömmliche Verfahren.“
Die additive Fertigung hat ferner einen entscheidenden Einfluss auf die Art und Weise und die Vielfalt der Produktherstellung. Zu den Vorteilen gehören geringere Kohlendioxidemissionen, weniger Materialverbrauch und reduzierter Transportaufwand, da die Teile nicht mehr importiert werden müssen, sondern selbst hergestellt werden können.
Zudem können Hersteller durch „Rapid Prototyping“ (schneller Prototypenbau) auch komplexere, kompaktere und innovativere Teile für die Luftfahrt herstellen. Rapid Prototyping bezieht sich auf verschiedene Verfahren. Das Ziel ist jeweils die schnelle Herstellung eines physischen 3D-Prototyps aus einer CAD-Datei. Mit diesen Prototypen können Versuche mit neuen Werkstoffen in kleinen Stückzahlen durchgeführt werden, bevor sie in Serie gefertigt werden. Damit wird sichergestellt, dass die Bauteile mit einem Höchstmaß an Innovation, Qualität und Präzision hergestellt werden.
Wir haben uns angesehen, wie Hersteller in der Luftfahrtindustrie neue Verfahren zur Herstellung komplexerer Bauteile einsetzen können. Aber stehen auch die richtigen Werkzeuge für diese Aufgaben zur Verfügung - insbesondere bei der Bearbeitung von anspruchsvollen Materialien wie Aluminium und HRSA?
Diese Werkstoffe erfordern den Einsatz von Werkzeugen mit höherer Verschleißfestigkeit und längerer Standzeit. Aus diesem Grund hat Sandvik Coromant die Sorte S205 für Wendeschneidplatten zum Drehen entwickelt. Die Metallurgie von S205 umfasst eine Inveio®-Schicht aus dicht gepackten, unidirektionalen Kristallen. Dadurch entsteht eine starke Schutzbarriere um die Wendeschneidplatte, die das Werkzeug verstärkt und seine mechanischen Eigenschaften verbessert. Die Wendeschneidplatte hat sich bereits bei der Herstellung einer Reihe von Flugzeugkomponenten bewährt, darunter Scheiben, Ringe und Wellen von Triebwerksturbinen. Kunden von Sandvik Coromant haben bereits von 30 bis 50 % höheren Schnittgeschwindigkeiten mit S205 im Vergleich zu konkurrierenden HRSA-Drehsorten berichtet.
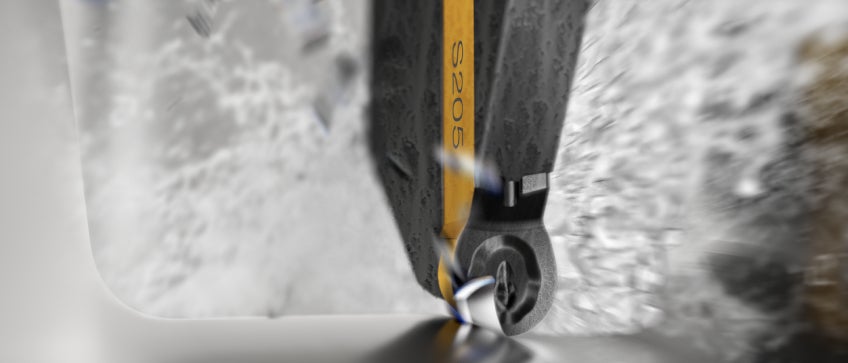
Ganzheitlicher Ansatz
Wir haben uns Gedanken über Herstellungsverfahren und Werkzeuge gemacht, aber wie können wir beides kombinieren? Bei der Zusammenstellung einer vollständig integrierten Lösung kann viel Zeit vergeudet werden, wenn die Systeme nicht optimal aufeinander abgestimmt sind.
Aus diesem Grund unterstützt Sandvik Coromant seine Kunden in der Luftfahrt mit einer Bauteillösung. Die Lösung umfasst mehrere Stufen, darunter die Prüfung des Maschinenbedarfs und Zeitstudien zur Ermittlung der Kosten pro Bauteil. Desweiteren die Analyse von Fertigungsverfahren bei der Auftragsabwicklung sowohl im Zusammenhang mit der Arbeitsablauf-Zeitanalyse (AAZ) als auch mit den Endbenutzerprozessen. Die Bauteillösung umfasst auch die Programmierung der computergestützten Fertigung (CAM) und das Projektmanagement für lokale oder grenzüberschreitende Projekte.
Bei einem Kunden von Sandvik Coromant, der in seiner Fertigung Probleme mit dem Spanbruch hatte, konnten wir mit der Bauteillösung die Ursache erkennen und das Problem beheben. Für den Kunden entwickelten die Spezialisten von Sandvik Coromant eine neue Strategie mit dynamischen Antriebskurven, die es uns ermöglichten, den Spanbruch permanent zu kontrollieren. Wir nannten diesen neuen Ansatz „Scoop Turning“ und besitzen nun ein Patent für dieses Verfahren. Mit dem Scoop Turning erreichte der Kunde eine Reduzierung der Zykluszeit um 80 % bei hervorragender Spankontrolle und verdoppelter Standzeit.
Darüber hinaus konnte der Kunde den Einsatz von vier Maschinen auf eine reduzieren. Damit konnte der Bedarf an Multitasking verringert werden, die Bearbeitungsprozesse wurden sicherer und eine „Green Light Production“ wurde ermöglicht. Ein geringerer Maschinenbedarf und die Möglichkeit, Fertigungsverfahren mit weniger Werkzeugwechseln abzuschließen, sind, dank härterer Bearbeitungsqualitäten wie S205, der Schlüssel zu einer nachhaltigeren Herstellung von Luftfahrzeugen.
Auch die Software wird eine wichtige Rolle spielen, wie zum Beispiel der CoroPlus® Tool Guide, der Bestandteil des digitalen Portfolios von Sandvik Coromant ist. Kunden können bereits vor Beginn der Fertigung wichtige Entscheidungen über die Wahl des Werkzeugs und der Schnittparameter treffen.
Kreislaufwirtschaft
Neben neuen Ansätzen für Werkzeuge und Fertigungsverfahren, können Hersteller in der Luftfahrtindustrie auch die Kreislaufwirtschaft nutzen. Laut einem Bericht der Air Transport Action Group (ATAG) setzt Kaiser Aluminium, das Unternehmen, das Boeing mit Aluminium beliefert, jetzt ein geschlossenes Recyclingsystem ein. Es handelt sich um eines der größten Programme dieser Art in der Branche. Kaiser schätzt, dass durch das System jährlich rund zehn Millionen Kilogramm Verschnitt und Schrott wiederverwendet werden können.
Bei Sandvik Coromant haben wir ein eigenes Kreislaufsystem für das Recycling von Hartmetallwerkzeugen eingeführt, bei dem wir die gebrauchten Hartmetallwerkzeuge unserer Kunden aufkaufen und für die Herstellung neuer Werkzeuge wiederverwenden. Daher stammen die meisten Rohstoffe, die für die Hartmetallwerkzeuge von Sandvik Coromant verwendet werden, aus Schrott. Wir praktizieren nachhaltiges Wirtschaften in einem Umfeld begrenzter Ressourcen und minimieren übermäßigen Ausschuss. Wir haben festgestellt, dass für die Herstellung von Werkzeugen aus Recyclingmaterial 70 % weniger Energie benötigt wird und 40 % weniger Kohlendioxid ausgestoßen wird.
Der Druck auf die Luftfahrtindustrie wächst, umweltfreundlichere Flugzeuge herzustellen, die leichter sind und längere Strecken zurücklegen können. Mit den richtigen Prozessen und Werkzeugen und einem ganzheitlichen Ansatz in der Fertigung, können die Hersteller ihren Beitrag zu einer grüneren Zukunft in der Luftfahrt leisten.