Künftige Trends in der Luftfahrt
Die Luftfahrt war jahrzehntelang eine von Wachstum geprägte Branche. Im Laufe der Jahre hat es immer wieder Krisen gegeben, aber nie eine so tiefgreifende und schwere wie die Coronapandemie. Wie können die Flugzeughersteller jetzt, da die Märkte sich einem Wachstumsniveau annähern, wie es zuletzt 2006 erreicht wurde, wieder auf Kurs kommen? Die Antwort liegt in einer nachhaltigeren Produktion. Im Folgenden erklärt Sébastien Jaeger, Industry Solution Manager – Aerospace bei Sandvik Coromant, Spezialist für Schneidwerkzeuge, wie Zusammenarbeit eine entscheidende Rolle bei der wirtschaftlichen Erholung der Luftfahrtbranche spielen wird.
Die Luftfahrtindustrie erlebte bis zum Ausbruch der Pandemie seit 14 Jahren ein kontinuierliches Wachstum. Es besteht kein Zweifel, dass die Trends und die Zukunft der Luftfahrtbranche durch die beispiellose Coronapandemie stark beeinflusst wurden. Der Geschäfts- und Urlaubsreiseverkehr ist exponentiell zurückgegangen und die Fluggesellschaften mussten sich auf ein wesentlich geringeres Rentabilitätsniveau einstellen.
Es gibt aber nicht nur schlechte Nachrichten. Der Luftfahrtsektor hat sich in der ersten Hälfte des Jahres 2021 etwas erholt, aber der Erfolg hängt von mehreren Faktoren ab, wie z. B. der Impfquote und den globalen Wirtschaftsaussichten, wobei auch der ökonomische Erfolg Chinas und die wieder etwas steigenden Zahlen bei Geschäfts- und Urlaubsreisen einen Einfluss haben. Prognosen zufolge wird die Branche in den nächsten zwei bis drei Jahren wieder das Vorkrisen-Niveau erreichen, wobei sich die verschiedenen Länder und Regionen unterschiedlich schnell erholen werden. Langfristig könnte die Zahl neuer Flugzeuge bis 2040 dennoch um 25 % geringer sein.
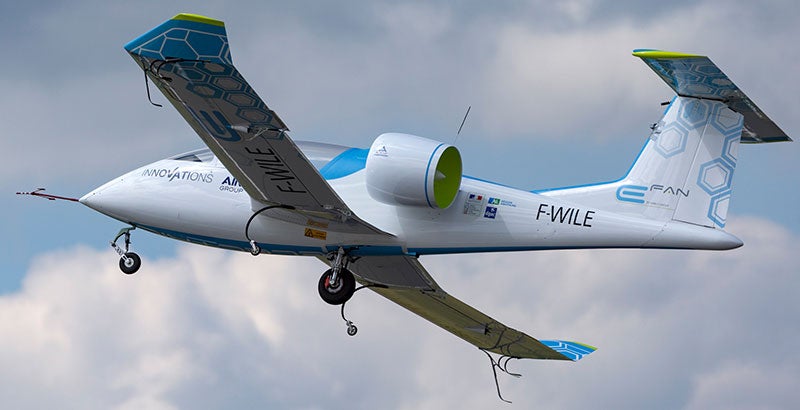
Hersteller verfolgen unterschiedliche konstruktive Ansätze für die elektrifizierten Flugzeuge der Zukunft, wie z. B. den Airbus E-Fan-Prototyp der Airbus Group.
Eine weitere große Veränderung aus technischer Sicht besteht darin, dass künftig schlankere Flugzeuge mit nur einem Mittelgang statt zweier Gänge gebaut werden, die zudem eine größere Reichweite haben müssen. Triebwerke und Flugzeugzellen können nicht unabhängig voneinander betrachtet werden. Bei Triebwerken liegt das Augenmerk jedoch unbedingt auf ihrer Umweltverträglichkeit. Dies bedeutet Geräusch-, Gewichts- und Emissionsreduzierungen sowie eine höhere Effizienz mit geringerem Verbrauch. Diese schlankeren Flugzeuge müssen ein breites Einsatzspektrum abdecken, ohne dass dabei die Größe oder die Anzahl der Triebwerke erhöht wird.
Diese konstruktiven Herausforderungen können auf unterschiedliche Weise bewältigt werden, beispielsweise durch alternative Treibstoffe wie synthetische Treibstoffe, Biotreibstoffe oder Wasserstoff für die bestehenden Treibstofftanks, aber auch durch neue Triebwerksarchitekturen großer Hersteller – ein längerfristiger Ansatz. Es gibt weiterhin auch alternative Typen von Triebwerken – elektrifiziert, batteriebetrieben oder elektromagnetisch – oder Hybridtriebwerke, bei denen die derzeitigen Triebwerke durch Elektromotoren unterstützt werden.
Anspruchsvolle Materialien
Beim Automobilbau gibt es bereits große Fortschritte mit neuen elektrifizierten und hybriden Systemen. Die Originalhersteller der Luftfahrtbranche arbeiten indes noch an solchen Systemen. Viele dieser Entwicklungen werden voraussichtlich frühestens ab 2035 auf breiter Front zum Einsatz kommen, bei kleineren Flugzeugen für zwei bis zehn Passagiere möglicherweise auch früher.
Geräusch-, Gewichts- und Emissionsreduzierungen werden natürlich die Leistung dieser elektrischen Systeme verbessern. Es sind dennoch große Herausforderungen zu bewältigen. Wenn es in einem Elektrofahrzeug Probleme gibt, kann dieses am Straßenrand anhalten – das ist in 10.000 Fuß Höhe nicht möglich. Hinzu kommt, dass Batterien schwer sind. Designer und Ingenieure wollen aber leichtere Flugzeuge mit größeren Reichweiten bauen. Es sind also noch technische Hürden zu nehmen.
Bei einem Bauteil wie dem Flugzeugrumpf verfolgen die Hersteller zwei unterschiedliche Ansätze. Einerseits wird immer mehr Aluminium eingesetzt, obwohl Flugzeugkomponenten neue Aluminiumsorten mit höherer Festigkeit, höherer Ermüdungsbeständigkeit und anderen Eigenschaften erfordern. Dieser Ansatz orientiert sich an traditionellen Flugzeugkonstruktionen, bei denen man vereinfacht ausgedrückt einen Rumpf mit Flügeln und einem Triebwerk hat.
Ein anderer Ansatz ist die Erprobung anderer Flugzeugformen, wie z. B. Deltaform, Blended Wing Body mit übergangsloser Flügel-Rumpf-Verbindung oder abgestrebte Flügel sowie eine stärkere Einbindung des Triebwerks in den Rumpf. Hier werden die Ingenieure eher zu (keramischen) Verbundwerkstoffen und Mischwerkstoffen greifen. Ob sich diese Entwürfe durchsetzen werden, bleibt abzuwarten. Im Moment können wir sicher davon ausgehen, dass mehr Aluminium und auch warmfeste Superlegierungen (HRSAs) zum Einsatz kommen werden. HRSAs werden in der Regel für Flugzeugkomponenten verwendet, an die extreme Leistungsanforderungen gestellt werden. Durch ihre hohe Festigkeit bei hohen Temperaturen können die Materialien ihre Härte auch bei großer Hitze beibehalten.
Doch selbst die besten Flugzeughersteller haben oft keine Erfahrung mit der Bearbeitung dieser widerstandsfähigeren Materialien. Hier hat sich das Know-how von Sandvik Coromant als nützlich erwiesen.
Bauteilspezifische lösungen
Als Antwort auf den zunehmenden Trend hin zu Multitasking bei Anlagenbedienern bietet Sandvik Coromant bauteilspezifische Lösungen an. Bediener können heute nicht nur eine einzige Maschine, sondern vier oder fünf Maschinen gleichzeitig bedienen, was ihnen weniger Zeit oder Gelegenheit gibt, sich auf bestimmte Prozesse zu konzentrieren. Aber was verstehen wir unter einer bauteilspezifischen Lösung? Es geht hier nicht nur um die von Sandvik Coromant bereitgestellten Werkzeuge, sondern auch um die Unterstützung des gesamten Prozesses.
Dies war der Fall, als ein Kunde von Sandvik Coromant aus der Luftfahrtindustrie bei der Bearbeitung von HRSA-Materialien auf Schwierigkeiten stieß. Der bisherige Ansatz des Kunden erforderte mehrere Maschinenwerkzeuge mit schlechter Spanlenkung und langen Zykluszeiten. Es gab Probleme mit uneinheitlichen Standzeiten und unzuverlässigen Prozessen und die Bearbeitung erforderte oft die ständige Überwachung durch einen Anlagenbediener.
Bei wertvollen Projekten wie diesen besteht die bauteilspezifische Lösung von Sandvik Coromant aus mehreren Stufen. Dies umfasst die Ermittlung der Maschinenanforderungen, Zeitstudien zur Untersuchung der Bauteilkosten und die Analyse der Produktionsmethoden, sowohl in Bezug auf die Methoden der Arbeitsablauf-Zeitanalyse (AAZ) als auch auf die Endbenutzerprozesse. Dazu gehören auch computergestützte Fertigungsprogrammierung (CAM) und Projektmanagement für lokale oder grenzüberschreitende Projekte.
Diese Analysen ergaben, dass wir die Programmierstrategie des Kunden ändern mussten, um seine Spanbruchprobleme zu lösen. In Kombination mit dem Werkzeug entwickelten die Spezialisten von Sandvik Coromant eine neue Strategie mit dynamischen Antriebskurven, die es uns ermöglichte, den Spanbruch in jedem Moment zu kontrollieren. Wir bezeichneten diesen neuen Ansatz als „Scoop Turning“ und haben jetzt ein Patent darauf.
Scoop Turning führte zu erheblichen Einsparungen für den Kunden. Neben einer hervorragenden Spanlenkung erreichte der Kunde auch eine Reduzierung der Zykluszeit um 80 % und eine Verdopplung der Standzeit. Er war in der Lage, den Einsatz von vier Maschinen auf eine zu reduzieren, wodurch weniger Multitasking erforderlich war, was zu sichereren Bearbeitungsprozessen und Green-Light-Produktion führte.
Dies zeigt, wie ein ganzheitlicherer Ansatz dem Geschäftsergebnis eines Herstellers zugutekommen kann. Auch Software spielt eine wichtige Rolle, wie z. B. der CoroPlus® Tool Guide, aus dem digitalen Portfolio von Sandvik Coromant. Kunden können bereits vor Beginn der Fertigung wichtige Entscheidungen über die Wahl des Werkzeugs und der Schnittparameter treffen.
Nachhaltigeres Drehen
Flugzeughersteller verfolgen beim Thema Nachhaltigkeit unterschiedliche Ansätze. Sandvik Coromant hat jedoch festgestellt, dass es möglich ist, eine maßgeschneiderte Lösung für einen Kunden zu entwickeln, von der inzwischen ganze Branchen profitieren.
Um Kunden bessere Drehvorgänge bei HRSAs zu ermöglichen, entwickelte Sandvik Coromant die Drehsorte S205. Die Schneidplatte ist mit einer Inveio®-Beschichtung der zweiten Generation beschichtet, um eine hohe Verschleißfestigkeit und eine lange Standzeit zu gewährleisten. Durch die Nachbehandlungstechnologie werden die mechanischen Eigenschaften der S205-Schneidplatte verändert, so dass diese verstärkt wird. Das Material hat eine Inveio®-Schicht mit dicht gepackten, unidirektionalen Kristallen, die eine starke Schutzbarriere um die Schneidplatte bilden. Dies maximiert den Wärmeschutz, verbessert den Kolkverschleiß und bietet eine bessere Flankenverschleißfestigkeit.
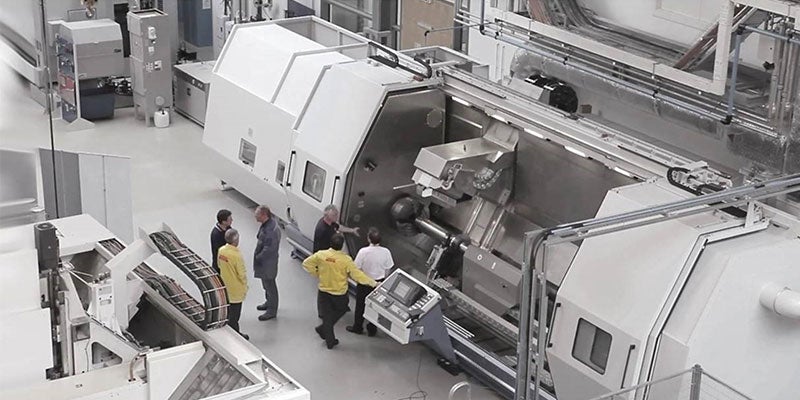
Die Sorte eignet sich gut für die Bearbeitung von Bauteilen wie Turbinenscheiben, Ringe und Wellen von Triebwerken. Unsere Kunden berichten von 30 bis 50 % höheren Schnittgeschwindigkeiten mit S205 im Vergleich zu konkurrierenden HRSA-Drehsorten, ohne Beeinträchtigung der Standzeit. Mehrere Hersteller in der Luftfahrtindustrie sowie in anderen Branchen haben schon von der S205 profitiert. Diese Ergebnisse wurden mit einem ganzheitlichen Ansatz erreicht, insbesondere mit Sandvik Coromants PrimeTurning™ für das Drehen in alle Richtungen, was maximale Produktivität ermöglicht.
Die PrimeTurningTM-Methode basiert darauf, dass das Werkzeug am Futter in das Bauteil eintritt und dann bis zum Ende des Bauteils Material abträgt. Die entscheidende Metallabtragsleistung wird so priorisiert, was eine schnellere, hochwertige Produktion und Umrüstung ermöglicht. In einigen Fällen haben unsere Kunden Produktionsläufe mit nur einem Werkzeugwechsel abgeschlossen, während bei einem Konkurrenzwerkzeug fünf Wechsel nötig gewesen wären.
Die Luftfahrtbranche mag in einer ihrer bisher größten Krisen stecken, aber es gibt einen Hoffnungsstreifen am Horizont. Sandvik Coromant unterstützt weiterhin alle führenden Flugzeughersteller bei ihrer postpandemischen wirtschaftlichen Erholung und verbindet dabei Umweltverträglichkeit mit besseren Werkzeugen und optimierte Schneidparameter mit einem ganzheitlichen Ansatz für die Werkzeugbereitstellung.