Che cos'è la profilatura?
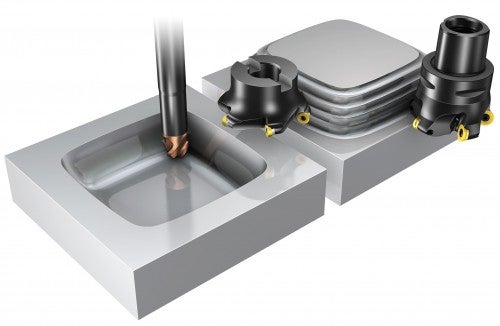
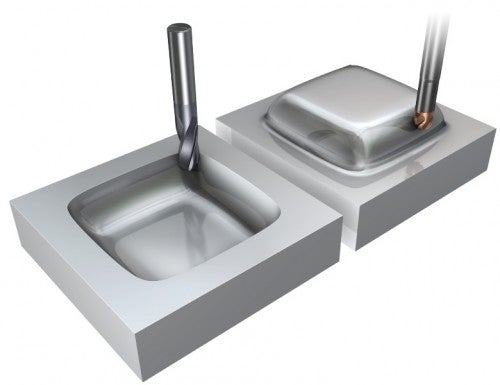
La profilatura è un'operazione di fresatura piuttosto comune. Le frese con inserti rotondi e raggiati vengono utilizzate per la sgrossatura e la semisgrossatura, mentre le frese a candela con testa sferica vengono utilizzate per la finitura e la superfinitura.
Processo di profilatura
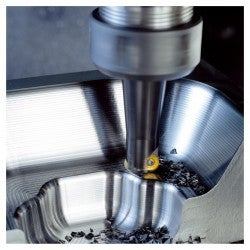
La profilatura comprende la fresatura multiasse di forme concave e convesse, bidimensionali e tridimensionali. Più grande è il componente e più è complicata la configurazione da lavorare, più diventa importante la pianificazione del processo.
Il processo di lavorazione dovrebbe essere suddiviso in almeno tre tipi di operazioni:
- Sgrossatura/semisgrossatura
- Semifinitura
- Finitura
Talvolta è richiesta la superfinitura, spesso eseguita usando metodi di lavorazione ad alta velocità. La fresatura del sovrametallo, la cosiddetta ripresa, è inclusa nelle operazioni di semifinitura e finitura. Per la massima precisione e produttività si consiglia di eseguire la sgrossatura e la finitura in macchine separate e di usare utensili da taglio specifici per ciascuna operazione.
L'operazione di finitura deve essere eseguita in una macchina utensile a 4/5 assi con software e tecniche di programmazione avanzati. Questo può ridurre sensibilmente o persino eliminare del tutto il lavoro di completamento manuale, che richiede molto tempo. Il risultato finale sarà un prodotto con miglior precisione geometrica e una miglior qualità della struttura superficiale.
Scelta degli utensili
Utensili da taglio ottimizzati per la sgrossatura e la semisgrossatura:
frese con inserti rotondi e raggiati.
Utensili da taglio ottimizzati per la finitura e la superfinitura:
frese a candela a testa sferica e con inserti raggiati.
![]() | ![]() | ![]() | ![]() | |
Inserti rotondi | Testa sferica multitagliente | Testina intercambiabile a sfera | Testa sferica in metallo duro integrale | |
Dimensioni macchina/mandrino | ISO 40, 50 | ISO 40, 50 | ISO 30, 40 | ISO 30, 40 |
Requisiti di stabilità | Elevati | Medi | Medi | Ridotti |
Sgrossatura | Ottima | Buona | Accettabile | Accettabile |
Finitura | Accettabile | Accettabile | Ottima | Ottima |
Profondità di taglio ap | Media | Media | Piccola | Piccola |
Versatilità | Ottima | Ottima | Ottima | Ottima |
Produttività | Ottima | Buona | Buona | Buona |
Checklist applicativa per la profilatura
Il profilo del componente dovrebbe essere studiato attentamente per scegliere gli utensili giusti e trovare il metodo di lavorazione più adatto:
- Definire i raggi minimi e la profondità massima della cavità
- Stimare la quantità di materiale da rimuovere
- Considerare la configurazione dell'utensile e il bloccaggio del pezzo per evitare vibrazioni. L'intera lavorazione deve essere eseguita su macchine specifiche per ottenere una buona precisione geometrica sul profilo
- Usando macchine utensili separate e precise per le operazioni di finitura e superfinitura, la necessità di lucidatura manuale, che richiede molto tempo, può essere ridotta e in alcuni casi eliminata
- Può essere necessario adottare una parte di programmazione avanzata per ottenere risparmi significativi. Usare le frese a candela in metallo duro integrale con la tecnica ad alta velocità per lavorare il pezzo quasi alla forma finale e ottenere la miglior finitura possibile
- La sgrossatura e la semifinitura di componenti di grandi dimensioni sono, di norma, più produttive se vengono utilizzati i metodi e gli utensili tradizionali. Un'eccezione è l'alluminio, per cui sono usate anche elevate velocità di taglio per la sgrossatura
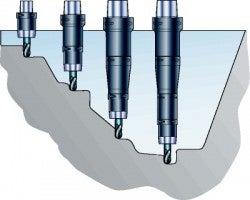
Come ridurre le vibrazioni
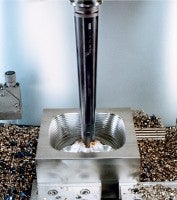
Le vibrazioni rappresentano un ostacolo alla fresatura di profili profondi usando sporgenze lunghe. I metodi comuni per superare questo problema consistono nel ridurre la profondità del taglio, la velocità o l'avanzamento.
- Utilizzare utensili modulari rigidi con buona precisione in termini di runout
- Utilizzando utensili modulari si ha una maggiore flessibilità e si ha a disposizione un maggior numero di combinazioni
- Usare utensili antivibranti o barre di estensione quando la lunghezza totale dell'utensile, dalla linea di riferimento al punto più basso del tagliente, supera di 4-5 volte il diametro
- Usare estensioni in metallo pesante se la rigidità alla flessione deve essere notevolmente aumentata
- Per velocità del mandrino superiori a 20,000 giri/minuto, usare utensili da taglio e portautensili bilanciati
- Scegliere il massimo diametro possibile sulle estensioni e sugli adattatori rispetto al diametro della fresa
- Una differenza radiale di 1 mm (0.039 poll.) tra il portautensile e l'utensile da taglio è sufficiente. Usare frese di grandi dimensioni
- La fresatura a tuffo è un metodo alternativo per fresare con utensili extra lunghi
Estensione graduale della lunghezza utensile
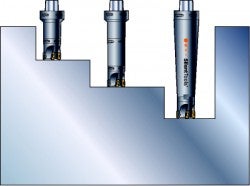

Per mantenere la massima produttività nelle operazioni di sgrossatura, dove la passata finale avviene in profondità nel componente, è importante lavorare con una serie di estensioni per la fresa.
- Iniziare con l'estensione più breve, poiché quelle più lunghe limitano la produttività e tendono a generare vibrazioni
- Passare agli utensili prolungati in posizioni predeterminate nel programma. La geometria della cavità determina il punto di sostituzione
- Adattare i dati di taglio a ciascuna lunghezza dell'utensile per mantenere la massima produttività
Velocità di taglio effettiva
Se si usa un valore di diametro nominale dell'utensile nel calcolo della velocità di taglio di una fresa con testa sferica o inserti rotondi, la velocità di taglio effettiva (vc) sarà molto inferiore se la profondità di taglio (ap) è ridotta. Avanzamento della tavola e produttività saranno gravemente ostacolati.
Basare i calcoli della velocità di taglio sul diametro effettivo nel taglio (Dcap).
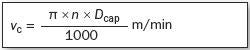
Fresa a candela per spallamenti
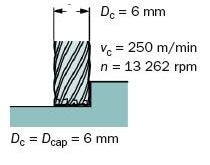
Fresa a testa sferica
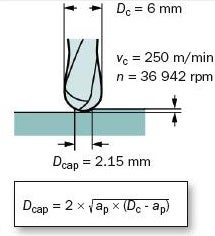
Fresa con inserti rotondi
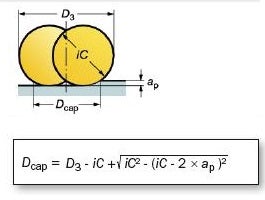
Fresatura a punti con fresa inclinata
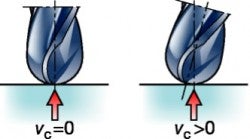
Quando si usa una fresa a candela con testa sferica, l'area più critica del tagliente è il centro dell'utensile, dove la velocità di taglio è vicina a zero, situazione sfavorevole per il processo di taglio. L'evacuazione truciolo al centro dell'utensile è di importanza critica, visto lo spazio ridotto nel tagliente trasversale.
Pertanto, si consiglia di inclinare il mandrino o il pezzo di 10-15 gradi, in modo che l'area di taglio sia allontanata dal centro dell'utensile.
- Velocità di taglio minima superiore
- Durata utensile e formazione del truciolo migliorate
- Migliore finitura superficiale
Esempio di frese con tagliente centrale
Parte centrale, z = 2
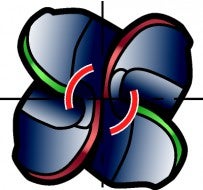
Parte periferica, z = 4
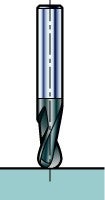
Z = 2
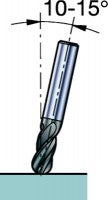
Z = 4
Taglio poco profondo
Quando si usa un inserto rotondo o una fresa con testa sferica ad una profondità di taglio inferiore, la velocità di taglio (vc) può essere aumentata, visto il breve tempo di contatto del tagliente. Il tempo per la propagazione del calore nell'area di taglio diventa più breve: la temperatura di tagliente e pezzo sono entrambe mantenute ad un valore basso. Inoltre, l'avanzamento/dente (fz) può essere aumentato grazie all'effetto di assottigliamento dei trucioli.
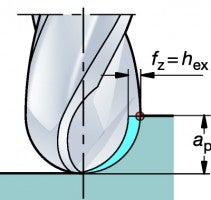
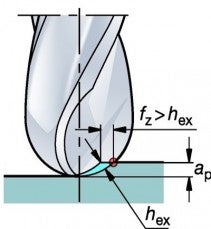
Taglio poco profondo
Esempio di taglio poco profondo, fresa non inclinata vs. fresa inclinata
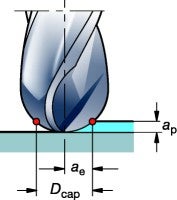
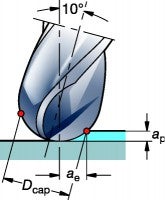
Questo esempio mostra le possibilità per aumentare la velocità di taglio quando il valore ae/ap è limitato, nonché i vantaggi di impiegare una fresa inclinata.
Testa sferica in metallo duro integrale
Dc = 10 mm, qualità GC 1610.
Materiale: acciaio, 400HB
Dati di taglio raccomandati per un taglio profondo ap - Dc/2:
vc = 170 m/min
fz = 0.08 mm/giro = hex
Operazione | Fresa non inclinata | Fresa inclinata (10°) |
Semifinitura ap - 2 mm (0.079 poll.)
vc - 300 m/min (984 piedi/min)
L'avanzamento per dente (fz) è lo stesso per entrambi i tipi | Dc = 10 mm (0.394 poll.)
vc = 300 m/min (984 piedi/min)
hex = 0.08 mm (0.003 poll.)
vf = 2 860 mm/min (113 poll./min) | Dc = 10 mm (0.394 poll.)
vc = 300 m/min (984 piedi/min)
hex = 0.08 mm (0.003 poll.)
vf =5 100 mm/min (201 poll./min) |
Superfinitura ae - 0.1 mm
vc - 5 * 170 - 850 m/min (557–2789 poll./min)
Nota: nella superfinitura, una fresa con due denti (zn = 2) può essere utile
fz - 0.12 mm/z (0.005 poll./dente) | Una fresa non inclinata non è consigliabile nella superfinitura | Dc = 10 mm (0.394 poll.)
vc = 850 m/min (2789 piedi/min)
hex = 0.02 mm (0.0008 poll.)
vf =14 600 mm/min (575 poll./min) |
Produttività nella profilatura: il sovrametallo costante
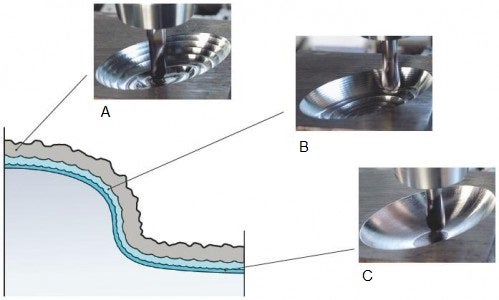
A: sgrossatura
B: semifinitura
C: finitura e superfinitura
Un sovrametallo costante è uno dei criteri più elementari alla base di una produttività regolare ed elevata delle operazioni di profilatura, soprattutto ad alta velocità.
- Per raggiungere la massima produttività in queste operazioni, comuni nella realizzazione di stampi, è importante adattare la dimensione delle frese alle operazioni specifiche
- L'obiettivo fondamentale è generare un sovrametallo uniformemente distribuito, in modo da avere pochi cambiamenti nel carico e direzione di lavoro per ogni utensile usato
Spesso è più favorevole "scalare" le dimensioni su frese diverse, da più grandi a più piccole, soprattutto nelle operazioni di sgrossatura leggera e semifinitura, invece di usare un unico diametro per tutta la durata di ogni operazione.
- La qualità migliore di finitura si ottiene quando le operazioni precedenti lasciano la quantità di sovrametallo minore e più costante possibile
- L'obiettivo deve sempre essere avvicinarsi il più possibile ai requisiti specificati per la forma finale
- Processo di taglio sicuro
Vantaggi con un sovrametallo costante
- Alcune operazioni di semifinitura e praticamente tutte quelle di finitura possono essere eseguite con una presenza parziale dell'operatore e talvolta anche in sua assenza
- L'impatto su guide della macchina utensile, viti a ricircolo di sfere e cuscinetti del mandrino sarà meno negativo
Allargatura di un pezzo dal pieno
- Quando si apre una cavità, è importante scegliere un metodo che riduca al minimo il valore ap e che lasci un sovrametallo costante per l'operazione di profilatura successiva
- Le frese a candela/per spallamenti e spianatura o le frese per contornatura lasciano un sovrametallo a gradini che deve essere rimosso. Questo genera diverse forze di taglio e flessioni dell'utensile. Il risultato è un sovrametallo irregolare per la finitura, che inciderà sulla precisione geometrica della forma finale
- L'uso di frese con inserti rotondi genera raccordi lisci tra le passate e lascia meno sovrametallo in quantità più uniformi per l'operazione di profilatura, dando come risultato una miglior qualità del componente
- Una terza alternativa è l'uso di una fresa ad elevati avanzamenti per aprire la cavità. Anche questo genera un sovrametallo ridotto e costante, grazie alla limitata profondità di taglio e ai gradini molto piccoli
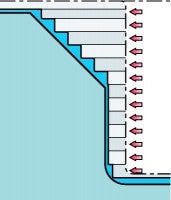
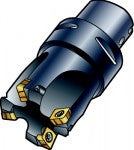
Fresa per spallamenti retti,
parecchio sovrametallo irregolare rimanente
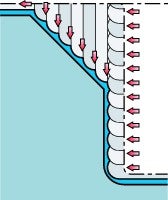
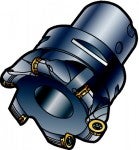
Fresa con inserti rotondi,
poco sovrametallo rimanente
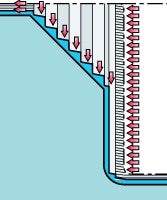
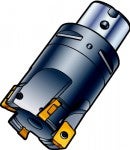
Fresa ad elevati avanzamenti,
poco sovrametallo rimanente
Copiatura
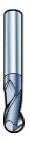
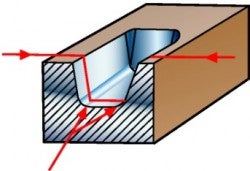
Il metodo tradizionale e più semplice per la programmazione dei percorsi utensile per una cavità consiste nell'uso dei normali sistemi di copiatura, con molte entrate e uscite dal materiale. Tuttavia, questo significa che software, macchine e utensili da taglio potenti sono usati in modo molto limitato. È preferibile usare una macchina con un software con funzioni "look ahead" per evitare le deviazioni dal percorso utensile.
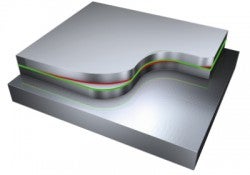
Un approccio aperto alla scelta di metodi, percorsi utensile e portautensili è essenziale.
− Carico pesante sul punto centrale dell'inserto
− Ridotte velocità di avanzamento
− Ridotta durata utensile
− Impatto meccanico
− Errori di forma
− Programmi e tempo di taglio più lunghi
Un percorso utensile per la copiatura spesso prevede una combinazione di fresatura discorde e concorde e richiede molti impegni e disimpegni sfavorevoli nel taglio. Ogni entrata e ogni uscita genera una flessione dell'utensile, lasciando così un segno in rilievo sulla superficie. Le forze di taglio e la flessione dell'utensile si riducono e vi sarà una leggera esecuzione di scarichi di materiale nell'area di uscita.
Conclusioni
- La copiatura su pareti ripide deve essere evitata il più possibile. In caso di lavorazione a tuffo, lo spessore del truciolo è notevole e la velocità di taglio deve essere bassa
- Esiste un rischio di sfaldamento del tagliente al centro dell'utensile, soprattutto quando la fresa tocca l'area del fondo
- Usare un controllo della velocità di avanzamento con funzione "look ahead". Diversamente, la decelerazione non sarà abbastanza rapida da evitare danni al centro dell'utensile
- Vi sarà una notevole lunghezza di contatto quando la fresa tocca la parete, con il rischio di flessioni, vibrazioni o rottura dell'utensile
- Quando si usano frese a candela con testa sferica, l'area più critica è il centro dell'utensile, poiché la velocità di taglio è pari a zero. Evitare di usare l'area al centro dell'utensile e attuare una fresatura a punti inclinando il mandrino o il pezzo per migliorare le condizioni
- Per il processo di taglio è meglio eseguire la copiatura discorde su pareti ripide, poiché lo spessore del truciolo è al valore massimo ad una velocità di taglio più favorevole
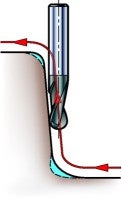
Rischio di "scavare"
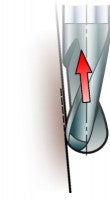
Copiatura discorde:
massimo spessore del truciolo al valore vc consigliato.
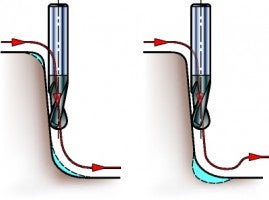
Al fondo della cavità:
rischio di sfaldamento al centro dell'utensile.
Gli errori di forma sono comuni, soprattutto quando si utilizza la tecnica di lavorazione ad alta velocità.
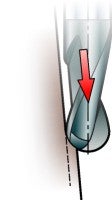
Copiatura concorde:
elevato spessore del truciolo con un valore vc molto ridotto.
Riduzione dell'avanzamento per evitare una durata utensile troppo breve
La fresatura discorde e concorde invertita espone l'utensile a flessione e forze di taglio alternate. Riducendo la velocità di avanzamento nelle sezioni critiche del percorso utensile, il rischio di sfaldamento del tagliente si riduce ed è possibile ottenere un processo di taglio più sicuro e una maggiore durata utensile.
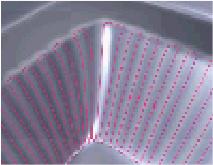
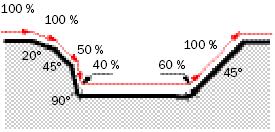
Contornatura
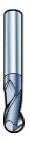
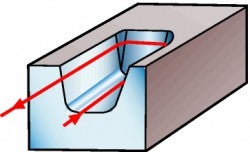
Invece di usare tecniche di programmazione che si limitano a "tranciare via" il materiale a un valore Z costante, è molto vantaggioso usare percorsi dell'utensile di contornatura in combinazione con la fresatura concorde. Il risultato garantisce:
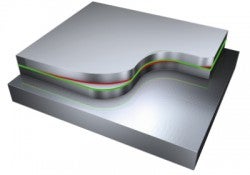
+ Tempi di lavorazione sensibilmente più brevi
+ Miglior utilizzo di macchina e utensile
+ Miglior qualità geometrica della forma lavorata
+ Finitura e operazioni di lucidatura manuali che richiedono meno tempo
+ Controllo della velocità di taglio - ve
+ Possibilità di HSM
+ Avanzamenti elevati
+ Lunga durata dell'inserto
+ Sicurezza
Il lavoro di programmazione iniziale è più complesso e richiede un po' di tempo in più; tuttavia, questo viene rapidamente compensato, poiché il costo orario della macchina è normalmente il triplo di quello di una stazione di lavoro. È preferibile usare una macchina con un software con funzioni "look ahead" per evitare le deviazioni dal percorso utensile.Conclusioni
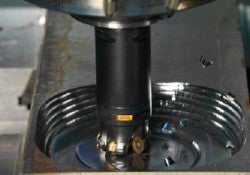
- Usare un tipo di percorso utensile per contornatura, ad esempio "Fresatura waterline": è il metodo migliore per garantire la fresatura concorde
- La contornatura, eseguita con la periferia della fresa, spesso fornisce una maggiore produttività, poiché un numero maggiore di denti si trova effettivamente impegnato nel taglio su un diametro utensile più grande
- Se la velocità del mandrino è limitata nella macchina, la contornatura aiuta a mantenere e controllare la velocità di taglio
- La contornatura crea anche meno cambi rapidi nel carico e nella direzione di lavoro. Nella fresatura ad avanzamento e velocità elevati e sui materiali temprati, questo è di particolare importanza poiché il tagliente e il processo sono più vulnerabili a qualsiasi cambiamento che crei differenze nella flessione o crei vibrazioni
- Per una buona durata utensile, rimanere nel taglio il più a lungo possibile
Nota: evitare di asportare con il centro dell'utensile quando la velocità di taglio è pari a zero.
Strategia del percorso utensile
Z – contornatura costante, due assi. Da sgrossatura a finitura
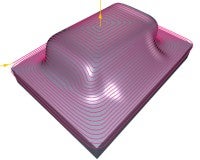
Fresatura Z Waterline - contornatura costante
- Comune quando è disponibile la funzione di rilevamento dell'altezza massima dello smerlo con controllo CAM
- Impegno e ritrazione senza problemi
- Programmazione semplice
- Ampia scelta di utensili
Contornatura elicoidale, tre-cinque assi. Finitura
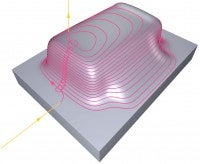
Contornatura con un percorso utensile in rampa
- Cambiamenti di direzione fluidi
- Buona precisione della forma e finitura superficiale
- Altezza dello smerlo controllata
- Impegno costante
- Programmi brevi
- Utensile corto
Generazione di superfici sculturate
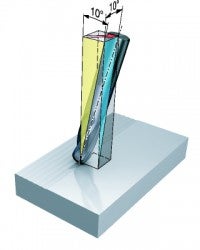
La fresatura concorde con fresa inclinata di circa 10° in due direzioni garantisce una buona finitura superficiale e prestazioni affidabili. Una fresa con testa sferica su un tagliente raggiato forma una superficie con una certa altezza della cuspide (h) a seconda di:
- Larghezza di taglio, ae
- Avanzamento per dente, fz
Altri fattori importanti sono la profondità di taglio (ap), che influisce sulle forze di taglio e la lettura del valore di runout sull'indicatore – TIR. Per ottenere risultati ottimali:
- Usare mandrini idraulici ad alta precisione con Coromant Capto®
- Minimizzare la sporgenza dell'utensile
Sgrossatura/semisgrossatura
Se l'avanzamento per dente è molto inferiore alla larghezza e profondità del taglio, la superficie generata avrà un'altezza della cuspide molto inferiore nella direzione di avanzamento.
Finitura e superfinitura
È vantaggioso ottenere una struttura superficiale uniforme e simmetrica in tutte le direzioni, che possa essere facilmente lucidata in seguito, a prescindere dal metodo di lucidatura selezionato.
Ciò si ottiene quando fz ≈ ae.
Nella superfinitura, usare sempre una fresa a due denti inclinata per ottenere la miglior struttura superficiale possibile.
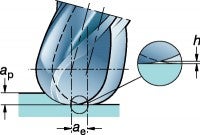
Semisgrossatura con fz molto inferiore a ae
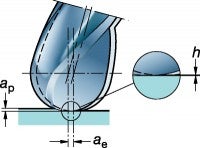
Superfinitura con fresa inclinata e fz equivalente a ae
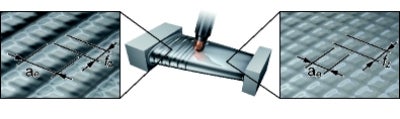