Toczenie nietypowych materiałów
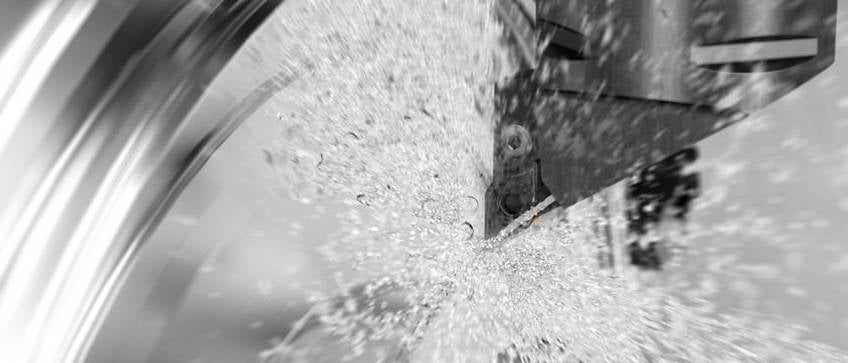
Superstopy żaroodporne i stopy tytanu to materiały wymagające w obróbce. Nie przypominają one innych metali i dlatego są nietypowe. Posiadają one doskonałe właściwości, takie jak stosunek wytrzymałości do masy, utrzymanie wytrzymałości i twardości w wysokich temperaturach oraz doskonała odporność na korozję.
Natomiast materiały te są także wymagające w obróbce, potrzebują „egzotycznych” rozwiązań. Takie rozwiązania należy dobrze zaplanować, korzystając z wyspecjalizowanych i starannie dobranych narzędzi oraz dróg przejść, by uzyskać wydajność, bezpieczeństwo i dobre wyniki obróbki.
Poniższy przegląd uwzględnia wymogi względem obróbki oraz innowacje, które zwiększyły wydajność i bezpieczeństwo procesu toczenia.
Komponent o wyjątkowych właściwościach, lecz wymagający w obróbce
O skrawalności materiału decyduje kilka czynników, które wpływają na wymogi względem skrawania metalu i jego rezultaty. W bardzo ogólnym sensie skrawalność to podatność danego materiału obrabianego na skrawanie, z uwzględnieniem tendencji narzędzia do zużywania się oraz sposobu formowania wiórów. Różnica polega na tym, że w większości klasyfikacji te egzotyczne materiały mają słabą skrawalność. Są one postrzegane jako wymagające w obróbce, aczkolwiek nie trudne, jeśli zastosuje się właściwe podejście do obróbki.
Bardziej egzotyczne spośród stosunkowo często stosowanych materiałów obrabianych są sklasyfikowane w grupie ISO S: superstopy żaroodporne (HRSA) i stopy tytanu. Pod kątem obróbki grupę tę można z kolei podzielić na kilka podgrup, w zależności od ich składu, stanu i właściwości. Natura chemiczna i skład metalurgiczny stopu zaliczanego do grupy S będzie decydować o właściwościach fizycznych i tym samym skrawalności. Kontrola spływu wiórów to przeważnie duże wyzwanie z powodu segmentacji wiórów i nierzadko zdarza się, że właściwy opór skrawania jest dwukrotnie większy niż w przypadku stali (co jest bezpośrednią miarą trudności, jaka towarzyszy skrawaniu materiału, określającą opory skrawania i zapotrzebowanie na moc).
Główną przyczyną, dla której superstopy żaroodporne są trudne do skrawania, jest fakt, że zachowują wytrzymałość w wysokich temperaturach. Nie miękną i nie zaczynają płynąć w odróżnieniu od większości innych materiałów oraz łatwo ulegają utwardzeniu w trakcie obróbki. Duże obciążenia mechaniczne oraz wysoka temperatura koncentrują się na krawędzi skrawającej. Stopy na bazie niklu, żelaza i kobaltu to podgrupy kategorii superstopów żaroodpornych, o wyjątkowej charakterystyce sprzyjającej zastosowaniu do produkcji określonych podzespołów, zwłaszcza w branży lotniczej, energetycznej i medycznej, gdyż ich właściwości pozostają niezmienne do momentu osiągnięcia temperatury bliskiej temperaturze topnienia. Mają one także silne właściwości antykorozyjne. Jednak co się tyczy skrawalności, materiały te wymagają odpowiedniej obrabiarki, sztywnej konfiguracji, specjalnych gatunków i geometrii płytek, zoptymalizowanego podawania chłodziwa oraz – co równie istotne – doboru właściwej metody obróbki i narzędzia. Z pewnością oznacza to konieczność dalej idącego planowania, co zwiększa nakład pracy podczas przygotowania produkcji.
Stopy tytanu także dzielą się na podgrupy, różniące się pod względem klasy skrawalności. Ogólnie rzecz biorąc, klasyfikacja pod kątem skrawalności opiera się na różnych stopniach słabej udarności, co z kolei oznacza specjalne wymogi wobec narzędzi i metod. Wymogi te wyznaczają niska przewodność cieplna, znaczna wytrzymałość w wysokich temperaturach, wysoko ścinane, cienkie wióry, mające tendencję do przywierania, tworzące wąską strefę kontaktu na powierzchni natarcia płytki, oraz duże opory skrawania skupione w pobliżu krawędzi skrawającej. Wióry mogą formować się w sposób cykliczny, co powoduje zmienność oporów skrawania, natomiast niektóre stopy charakteryzują się stosunkowo dużym udziałem węglika, co nadaje materiałowi dodatkowe właściwości abrazyjne. Nadmierne prędkości skrawania mogą spowodować reakcję chemiczną między wiórem i materiałem narzędzia, co przekłada się na nagłe wykruszenia / rozłamywanie krawędzi skrawającej oraz rozsmarowywanie lub przywieranie materiału na krawędzi skrawającej. Do tego niektóre stopy szybko utwardzają się podczas obróbki, co jest przyczyną zużycia typu dyfuzyjnego i w efekcie nadmiernego tworzenia się zadziorów. To także utrudnia kolejne czynności obróbkowe.
Dotyczy to materiałów egzotycznych, ale także okno parametrów do obróbki wielu superstopów żaroodpornych i stopów tytanu jest stosunkowo małe.
Podczas toczenia tych materiałów…
sukces zależy od znalezienia równowagi między skumulowanymi skutkami oddziaływania czynników związanych z materiałem i zastosowaniem. Istnieje kilka podstawowych praktycznych zasad, których przestrzeganie znacząco przyczynia się do osiągnięcia dobrych wyników:
- wstępne zaplanowanie dobrej, możliwie najbardziej szczegółowej strategii obróbki,
- dobór najlepszego podejścia do kwestii narzędzi,
- dobór najlepszych dróg narzędzia i zastosowanie bardzo stabilnego mocowania,
- zastosowanie najlepszej spośród nowych, specjalnych technologii narzędzi skrawających,
- zastosowanie odpowiednich parametrów skrawania w celu uzyskania bezpieczeństwa i produktywności obróbki,
- zastosowanie obliczeń długości przejścia spiralnego do przewidywania przejść,
- właściwe zastosowanie chłodziwa, z użyciem nowoczesnych rozwiązań wysokociśnieniowych,
- korzystanie z zaleceń i wsparcia specjalistów.
Proces obróbki należy zawsze starannie zaplanować, ze względu na krytyczne czynniki o decydującym znaczeniu, takie jak uwzględnienie stanu materiału przedmiotu obrabianego. Odlewanie, kucie, kształt pręta, obróbka cieplna, zastosowanie roztworów oraz starzenie znacząco wpływają na podzespół w sposób, który wymaga uwzględnienia przy doborze narzędzi i metod. Stan powierzchni przedmiotu obrabianego może być różny i wpływać na obróbkę, podobnie jak twardość przedmiotu. Strategia toczenia powinna również uwzględniać wymogi wynikające z cech konstrukcyjnych przedmiotu, które wymagają obrobienia, a także różne etapy obróbki, czyli etap zgrubny (pierwszy), pół wykończeniowy (pośredni) oraz wykończeniowy (ostatni). Skomplikowane kształty i chropowatość powierzchni to częste źródła problemów.
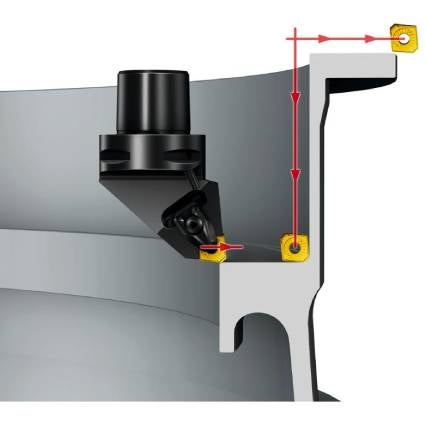
Podstawą podczas planowania toczenia nietypowych materiałów jest uwzględnienie planowanego kształtu, materiału i stanu przedmiotu. Jeśli to konieczne, należy określić sposób wykonania pierwszego, pośredniego i ostatniego etapu obróbki, z uwzględnieniem stanu materiału i wymogów jakościowych. Planowanie drogi narzędzi i zastosowanie redukcji posuwu podczas programowania pomoże określić zakres zużycia, typ narzędzia, czasy realizacji i poziom bezpieczeństwa obróbki.
Przebieg skrawania tego rodzaju materiałów…
zależy w znacznym stopniu od sposobu przyłożenia krawędzi skrawającej do przedmiotu obrabianego. Kąt przystawienia krawędzi skrawającej, w połączeniu z geometrią płytki, decyduje o wydajności, trwałości narzędzia, bezpieczeństwie i wynikach obróbki. Kształty płytek trzeba często dobrać w zależności od przejścia skrawającego, jakie należy wykonać. Jednak fakt, że zastosowanie małego kąta przystawienia wpływa na wydajność i trwałość narzędzia, powinien być zawsze kluczową kwestią.
Doboru gatunku płytki należy dokonać częściowo w odniesieniu do kąta przystawienia. Kąt ten wpływa między innymi na rodzaj zużycia powodującego powstawanie karbu na krawędzi skrawającej, którego rozmiar wpływa na wyniki obróbki i może spowodować przedwczesną awarię narzędzia. Dobór właściwego sposobu przystawienia krawędzi oznacza również, że można wybrać bardziej produktywny gatunek płytki, zapewniając przy tym większą trwałość narzędzia i bezpieczeństwo obróbki.

Kąt przystawienia narzędzia skrawającego wpływa na grubość wiórów, posuw, siły skrawania i możliwe do zastosowania techniki obróbki. W przypadku materiałów nietypowych dobór kąta ma bezpośrednie konsekwencje dla produktywności i niezawodności obróbki, wpływając na kształt płytki i promień naroża oraz możliwości wykorzystania materiału narzędziowego. Zazwyczaj najlepszym wyborem są płytki okrągłe oraz płytki w wersji Xcel.
Dobór materiału narzędziowego (gatunku płytki) powinien uwzględniać rodzaj planowanej obróbki tokarskiej – zgrubnej, pół wykończeniowej lub wykończeniowej – a także stan przedmiotu obrabianego i typ skrawania. Twardość tych materiałów oznacza, że należy zawsze uwzględnić odkształcenie plastyczne krawędzi skrawającej jako najważniejszy czynnik ryzyka przy wyborze gatunku płytki (jak już wspomniano powyżej, na powstawanie karbu wpływają głównie kąt przystawienia i głębokość skrawania). Dobór gatunku płytki należy również połączyć z dobraniem odpowiedniego kształtu, gdyż jest do kwestia związana z wytrzymałością, którą należy uwzględnić obok sposobu przystawienia, obciążenia wiórami oraz czy skrawanie ma mieć charakter ciągły, czy przerywany. Co za tym idzie, ważną rolę w obróbce superstopów żaroodpornych odgrywają specjalne gatunki.
Duża zdolność płytki do zachowania twardości w wysokich temperaturach, wysoki poziom jej udarności oraz odpowiedni stopień przywierania pokrycia płytki to najważniejsze wymogi. Dodatnia geometria skrawania, ostra krawędź skrawająca, wytrzymałe ostrze oraz stosunkowo otwarta konstrukcja łamacza wiórów to pożądane cechy płytki wymiennej do obróbki tych materiałów.
Dobór najbardziej odpowiednich parametrów skrawania jest nie mniej ważny dla powodzenia obróbki. Prędkość skrawania ogranicza się do połączenia prędkości, posuwu i głębokości skrawania i można ją optymalizować w celu osiągnięcia wysokiego poziomu produktywności, bezpieczeństwa i jakości. Prędkość skrawania wiąże się z powstawaniem wysokiej temperatury i jej wpływem na płytkę; prędkość musi być na tyle duża, aby wióry były odpowiednio plastyczne, ale nie za duża, aby nie dopuścić do utraty równowagi przez materiał narzędziowy. Prędkości zazwyczaj mieszczą się w zakresie od 130 do 260 sfm (od 40 do 80 m/min) w przypadku specjalnych płytek z węglika spiekanego oraz od 490 do 1310 sfm (od 150 do 400 m/min) w przypadku płytek ceramicznych.
Posuw stanowi główny czynnik wpływający na czas skrawania i grubość wiórów. Przy obróbce materiałów nietypowych posuw należy dobierać z większą starannością, gdyż wartości graniczne są stosunkowo wymagające: podczas obróbki zgrubnej wiór powinien być jak największy, ale nie powinien przeciążać krawędzi, natomiast podczas obróbki wykończeniowej wiór powinien być na tyle gruby, by zapobiegać powstawaniu zbyt wysokiej temperatury i utwardzaniu się podczas obróbki.
Głębokość skrawania często wpływa na sposób przystawienia krawędzi i tym samym nie może przekraczać określonej wartości. Na przykład przy zastosowaniu płytek okrągłych do obróbki superstopów żaroodpornych głębokość skrawania nie powinna przekraczać 15% długości średnicy płytki. Głębokość skrawania należy również starannie zaprogramować podczas profilowania. W grę wchodzi zastosowanie wnęk lub występów, aby nie przekroczyć odpowiedniego łuku zagłębiania krawędzi skrawającej.
Co się tyczy trwałości narzędzia, ważne jest częste uwzględnianie długości drogi spiralnej (SCL). Właściwe wdrożenie tej techniki oznacza, że można przewidzieć i zaprogramować postoje obrabiarki w celu wymiany płytek oraz że przejścia narzędziem pracującym z odpowiednią prędkością można wykonywać bez utraty przez krawędź skrawającą zdolności do utrzymania wymaganej chropowatości powierzchni.
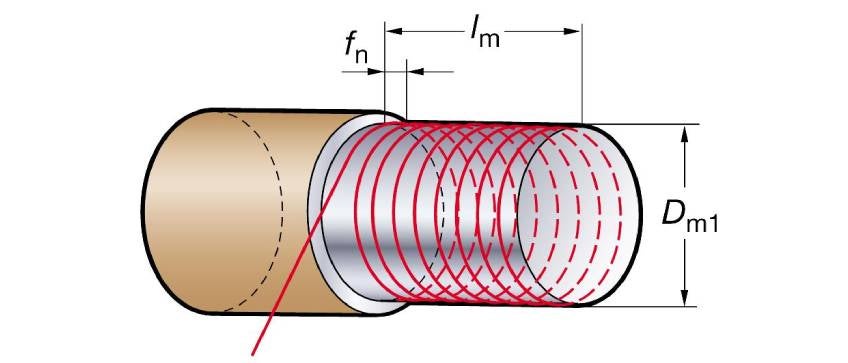
Zastosowanie obliczeń długości drogi spiralnej pomoże przewidywać czas lub długość drogi skrawania, aby skrócić czas obróbki i zmniejszyć chropowatość powierzchni podczas obróbki nietypowych materiałów. Przestoje obrabiarki w celu wymiany płytki są wówczas planowane z wykorzystaniem spiralnej długości drogi skrawania, dzięki czemu można lepiej dobrać typ obróbki i parametry skrawania w celu optymalizacji trwałości ostrza narzędzia i stopnia wykorzystania obrabiarek.
Na zużywanie się narzędzia ogromny wpływ mają…
… wysokie opory skrawania w połączeniu z wysokimi temperaturami krawędzi skrawającej, połączone z tendencją do powstawania określonych rodzajów zużycia krawędzi skrawającej. Główne objawy zużycia to wspomniany wrąb/karb (typ zużycia mechanicznego, przy którym głębokość skrawania wyznacza linię oddziaływania na krawędź skrawającą); odkształcenie plastyczne krawędzi skrawającej – skutek połączenia wysokiej temperatury i ciśnienia, oraz zużycie ścierne, którego przyczyną są przeważnie materiały o większej twardości. Innym typem zużycia jest górne zużycie sieczne, powstające na płytkach ceramicznych i polegające na odcięciu górnych warstw krawędzi skrawającej. Sposób przystawienia krawędzi skrawającej odgrywa ważną rolę.
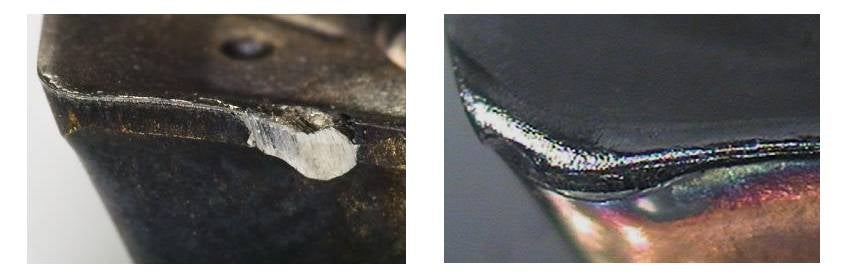
Wybór gatunku płytki nie jest tak bezpośrednio związany z obróbką zgrubną i wykończeniową materiałów nietypowych jak w przypadku innych materiałów. Dobór gatunku jest raczej czynnikiem optymalizacji – nieco bardziej złożonym, zależnym od kształtu płytki, sposobu przystawienia krawędzi skrawającej oraz typu obróbki. Destrukcyjnemu przebiegowi zużywania się, takiemu jak wspomniany wcześniej karb i odkształcenie plastyczne, należy zapobiegać głównie poprzez połączenie odpowiednich narzędzi, parametrów skrawania i metody obróbki. Płytki z węglika spiekanego, nowoczesne gatunki ceramiczne wykonane z SiAlON oraz do pewnego stopnia płytki wzmacniane wiskerami stanowią często najbardziej odpowiedni i najszerzej stosowany wybór.
Najbardziej odpowiedni kąt przystawienia podczas toczenia materiałów nietypowych to kąt mały, nieprzekraczający 45 stopni. Najgorsza sytuacja to taka, w której kąt przystawienia wynosi 90/0 stopni lub głębokość skrawania jest większa od promienia naroża płytki skrawającej. Duży lub mały kąt przystawienia to cienkie wióry i możliwość stosowania większego posuwu.
Podczas toczenia superstopów żaroodpornych kąt przystawienia narzędzia decyduje o tym, czy najbardziej odpowiednia jest płytka z pokryciem z PVD czy CVD. Ma to zapewniać ochronę przed skutkami wysokich temperatur. Płytki z pokryciem z PVD są odpowiednie przy kącie przystawienia 90/0 stopni, natomiast płytki z pokryciem z CVD – przy kącie przystawienia 45 stopni. Z kolei podczas toczenia tytanu pokrycie płytki nie przynosi żadnych korzyści. W takim przypadku ważniejszym czynnikiem jest zapewnienie najbardziej odpowiedniego kształtu krawędzi skrawającej, np. płytek okrągłych do obróbki wykończeniowej. Nowe rodziny płytek z pokryciem z PVD zapewniają dużą twardość i dobrą odporność na odkształcenie krawędzi i pęknięcia cieplne. W połączeniu z ostrymi krawędziami, mogą również doskonale sprawdzać się w obróbce zgrubnej i wykończeniowej materiałów przywierających.
Właściwy kształt płytki…
to ważny czynnik podczas obróbki omawianych materiałów. Płytki okrągłe (o kształcie R) stały się jednym z najczęściej zalecanych rozwiązań do obróbki tych materiałów. Płytka okrągła zapewnia wytrzymałość ostrej krawędzi skrawającej o dodatniej geometrii; grubość wiórów zmienia się wzdłuż długiej krawędzi skrawającej, co umożliwia wysokie posuwy; duży promień płytki nie ogranicza wartości stosowanego posuwu z uwagi na chropowatość powierzchni. Zaletą płytek okrągłych jest również elastyczność programowania operacji profilowania i przebijania podzespołów o różnych kształtach.
Płytki kwadratowe (o kształcie S) to niekiedy najlepsze rozwiązanie do pierwszego etapu obróbki ze względu na możliwość wykonywania cięć zgrubnych w różnych kierunkach z kątem przystawienia 45 stopni. Płytki romboidalne (o kształcie C) gwarantują elastyczność doboru drogi narzędzia; w udoskonalonej wersji Xcel zapewnia lepszą dostępność do narożników, odsadzeń i wgłębień. To połączenie kształtu płytki i kąta przystawienia wynoszącego 45 stopni zmniejsza również promieniowe siły skrawania, generuje wióry o stałej grubości i jest bardziej odporna na powstawanie karbu. Wynik: poprawa produktywności, większa trwałość narzędzia i bezpieczeństwo obróbki.
Optymalizacja programu…
… odgrywa ważną rolę, dlatego poniżej zamieszczamy kilka zaleceń sprzyjających poprawie wydajności, zwłaszcza podczas stosowania płytek okrągłych, które zasadniczo nadają się do obróbki nietypowych materiałów:
- unikać zagłębiania w cięcia i osłabiania kontaktu; jeśli cięcia te są konieczne, zmniejszyć posuw o połowę,
- przy toczeniu odsadzeń, zmniejszyć posuw o połowę lub zbliżać się do odsadzenia po łuku jeśli zaprogramowany promień jest równy średnicy płytki. (Zgodnie z wytycznymi minimalny zaprogramowany promień powinien wynosić mniej więcej 25% średnicy płytki, a promień przedmiotu – 75% średnicy płytki. Posuw środka narzędzia dotyczy zaprogramowanego promienia.),
- przy obróbce zgrubnej za pomocą płytek okrągłych zaprogramowany promień powinien być równy średnicy płytki, natomiast przy obróbce wykończeniowej należy pamiętać, aby zaprogramowany promień był większy niż średnica płytki,
- należy rozważyć kilka alternatywnych dróg narzędzia, np. zastosowanie kilku przejść lub obróbkę w obu kierunkach dla lepszego wykorzystania płytek,
- płytki ceramiczne należy chronić poprzez fazowanie wstępne przedmiotu obrabianego i zagłębianie w fazkę,
- należy utrzymywać wystarczającą równowagę między kątem przystawienia i łukiem zagłębiania płytki przez cały czas trwania obróbki. Zmniejszenie kąta ma zasadnicze znaczenie dla osiągnięcia dobrej wydajności, natomiast zastosowanie płytek okrągłych jest ważnym czynnikiem stymulującym wykorzystanie dostępnego potencjału za pomocą nowoczesnych gatunków płytek,
- unikać „efektu dookolnego” przy profilowaniu lub obróbce wgłębnej aby nie przeciążyć płytki – zastosować alternatywną drogę narzędzia lub płytkę o mniejszej średnicy,
- rozważyć możliwość zastosowania toczenia trochoidalnego, umożliwiającego podzielenie przejścia na mniejsze odcinki, zwłaszcza przy przebijaniu.
Co należy uwzględnić przy doborze typów narzędzi i metod do obróbki superstopów żaroodpornych i tytanu? Oto kilka najważniejszych aspektów:
- Oferta musi zawsze obejmować precyzyjne podawanie chłodziwa. Dzięki precyzyjnym dyszom umieszczonym za krawędzią skrawającą i przy niej i narzędziom, do których chłodziwo jest doprowadzane wewnętrznie, można zyskać wiele korzyści podczas toczenia, frezowania i wiercenia. Najnowsza technologia dysz, dostępna w ramach oferty standardowej lub rozwiązań specjalnych oraz dla różnych zakresów ciśnienia, może być stosowana dla wszystkich typów obrabiarek z odpowiednim doprowadzaniem chłodziwa. Podczas inwestycji w nowe obrabiarki oferta powinna zawsze obejmować opcję zwiększenia ciśnienia chłodziwa do 70 bar na czas toczenia tytanu, aby ułatwić poprawę odłamywania wiórów, niemniej podczas toczenia supestopów żaroodpornych ciśnienie do 200 bar jest korzystne ze względu na trudniejsze do odłamania wióry.
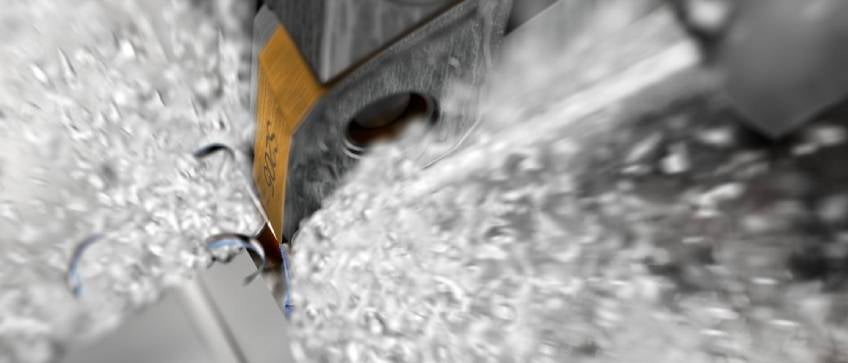
Zastosowanie chłodziwa to czynnik o znaczeniu decydującym dla obróbki materiałów egzotycznych. Precyzyjne doprowadzanie chłodziwa to obecnie zaawansowana technologicznie opcja dostępna w ofercie standardowej lub narzędzi specjalnych i na tyle wydajna, by w sposób decydujący wpływać na wyniki skrawania oraz formowanie wiórów, trwałość narzędzia i produktywność. Zasadniczo wysokie temperatury powstające podczas obróbki tych materiałów sprawiają, że chłodzenie jest niezbędne, ale podawanie chłodziwa w dużych ilościach, pod wysokim ciśnieniem i z dużą precyzją, a także w połączeniu ze specjalnymi płytkami i doprowadzaniem chłodziwa przez narzędzie, sprzyja optymalizacji wydajności i wyników obróbki.
- Podczas toczenia materiałów egzotycznych problemem jest często dostępność. Złożone kształty i wysięgi narzędzi sprawiają, że dobór narzędzi i metod ma krytyczne znaczenie dla powodzenia obróbki. Przyjrzyjmy się systemom modułowym, w ramach których dostępna jest niezawodna koncepcja z listwami narzędziowymi, na których umieszczone są krawędzie skrawające – pod różnymi kątami i na różnych wysięgach. Asortyment alternatywnych adapterów i listew ma zapewniać elastyczność, która umożliwia skonstruowanie przy użyciu ograniczonego zasobu niemal każdego narzędzia, pasującego do konfiguracji i umożliwiającego dostęp do ograniczonych przestrzeni zewnętrznych i wewnętrznych. Listwy powinny posiadać luzy promieniowe i osiowe wymagane przy obróbce głębokich rowków kątowych z precyzyjnym podawaniem chłodziwa przez narzędzie na krawędź skrawającą.
- Materiał narzędziowy ma zasadnicze znaczenie podczas każdego rodzaju obróbki, a w przypadku materiałów nietypowych jest czynnikiem o znaczeniu krytycznym. Obszar ten wymaga stosowania specjalnych gatunków płytek w połączeniu z właściwą geometrią płytki, głównie w postaci najnowszego asortymentu węglikowego i ceramicznego. Niepowlekane gatunki węglikowe nadal zajmują ważne miejsce, ale ostatnie postępy technologii pokrycia płytek doprowadziły do powstania płytek węglikowych ze specjalnym pokryciem, zwiększającym możliwości krawędzi skrawającej poprzez skrócenie czasu skrawania i wydłużenie okresu przydatności narzędzia.
- Należy korzystać z funkcji tłumienia drgań zintegrowanych w wytaczakach, listwach, a nawet frezach, aby ograniczać tendencję do wibracji. Technologia tłumienia drgań dokonała ogromnych postępów i powinna być naturalną opcją, zwłaszcza w sytuacji, gdy wysięgi narzędzi sprzyjają zmniejszeniu stabilności. Produktywność, bezpieczeństwo obróbki i jakość przedmiotu to czynniki mające bezpośredni związek z jakością i dostępnością narzędzi tłumiących drgania. Bez tych funkcji wielu czynności nie sposób wykonać: obecnie toczenie wewnętrzne z wysięgami sięgającymi nawet 14-krotności średnicy do 250 mm można wykonywać bardzo wydajnie, przy doskonałej jakości wykończenia powierzchni.