Przyszłe trendy w branży lotniczej
Przez dziesięciolecia branża lotnicza nieprzerwanie rosła. W tym czasie zdarzały się kryzysy, ale żaden nie był tak poważny i nie dotknął branży tak bardzo, jak pandemia COVID-19. Obecnie, gdy rynki ponownie odnotowują poziom wzrostu nieznany od 2006 roku, co mogą zrobić producenci sprzętu lotniczego, aby wrócić na właściwy kurs? Odpowiedzią jest bardziej zrównoważona produkcja. W niniejszym artykule Sébastien Jaeger, Industry menedżer ds. rozwiązań przemysłowych dla branży lotniczej w firmie Sandvik Coromant, specjalizującej się w produkcji narzędzi skrawających, wyjaśnia, dlaczego współpraca odegra ważną rolę w regeneracji branży lotniczej.
Branża lotnicza rosła nieprzerwanie od 14 lat, zanim pandemia zadała jej cios. Nie ulega wątpliwości, że bezprecedensowa pandemia koronawirusa wywarła ogromny wpływ na trendy w przemyśle lotniczym i jego przyszłość. Nastąpił wykładniczy spadek liczby podróży w celach biznesowych lub rekreacyjnych, a linie lotnicze musiały przystosować się do znacznie obniżonych poziomów rentowności.
Nie był to koniec złych wieści. W branży lotniczej wystąpiła poprawa w pierwszej połowie 2021 roku; niemniej sukces ten wiązał się kilkoma czynnikami, takimi jak szczepienia oraz globalne perspektywy ekonomiczne, na co wpływ miała kondycja chińskiej gospodarki oraz powrót podróży biznesowych i wakacyjnych. Zgodnie z przewidywaniami branża wróci do wyników sprzed kryzysu w ciągu następnych dwóch lub trzech lat. Tempo tego odbicia będzie różne w zależności od kraju i regionu. Tak czy inaczej, w dłuższej perspektywie liczba nowych samolotów może spaść o 25% do 2040 roku.
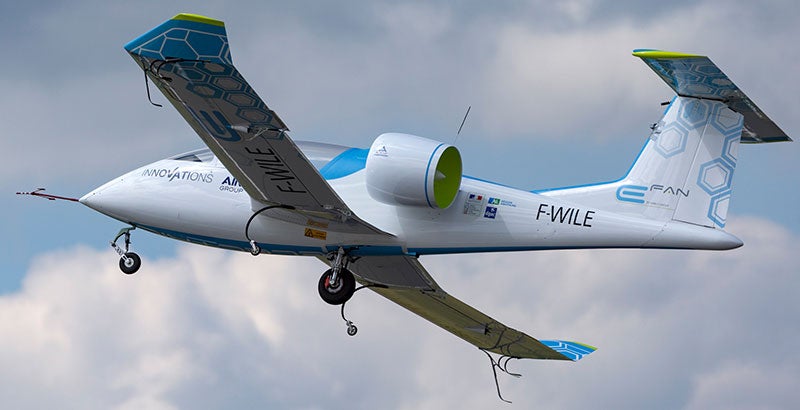
Producenci w różny sposób podchodzą do elektrycznych samolotów przyszłości, takich jak prototyp Airbus E-Fan stworzony przez Airbus Group.
Z inżynierskiego punktu widzenia kolejna wielka zmiana będzie polegała na tym, że samoloty będą mieć jedno przejście między fotelami, a nie dwa, i tym samym węższy kadłub. Będą także musiały mieć większy zasięg. Silnik i rama kadłuba są ze sobą ściśle powiązane: jedno nie może istnieć bez drugiego, ale w przypadku silnika można stwierdzić, że nacisk położony jest na zrównoważony rozwój. Oznacza to redukcję masy, hałasu i emisji oraz większą wydajność przy mniejszym zużyciu paliwa. Tego rodzaju maszyny z jednym przejściem między fotelami będą musiały zaspokajać szereg zastosowań bez zwiększania wymiarów samolotu i liczby jego silników.
Projektanci mogą podejść do tych wyzwań na różne sposoby. Jeden sposób polega na poszukiwaniu alternatywnych paliw do obecnie stosowanych silników, np. paliwa syntetycznego, biopaliwa lub wodoru. Inny sposób to stworzenie nowej architektury silnika; duzi producenci prezentują obecnie nowe typy silników, co jest bardziej długofalowym podejściem. Mamy wreszcie alternatywne kształty architektury silnika, np. elektryczny, z napędem akumulatorowym lub elektromagnetyczny, albo silniki hybrydowe, w których aktualnie używane silniki będą wspomagane przez silniki elektryczne.
Wymagające materiały
W przemyśle samochodowym widać już ogromny postęp w dziedzinie nowych układów elektrycznych i hydrydowych. Tymczasem w branży lotniczej producenci oryginalnego sprzętu (OEM) nadal pracują nad tymi systemami, a wiele konstrukcji nie wejdzie do powszechnego użytku przed rokiem 2035. W przypadku mniejszych samolotów, np. zabierających na pokład od dwóch do 10 osób, technologie te mogłyby pojawić się wcześniej.
Ograniczenia dotyczące hałasu, masy i emisji będą oczywiście wpływać na działanie tych systemów elektrycznych, ale wiążą się z tym pewne wyzwania. Jeśli w pojeździe elektrycznym (EV) dojdzie do awarii, można zatrzymać się na poboczu – na wysokości 10 kilometrów nie wchodzi to w grę. Ponadto jeśli projektanci i inżynierowie chcą, aby lżejsze samoloty pokonywały większe odległości, konieczne jest zastosowanie ciężkich baterii. Występują zatem przeszkody techniczne.
W kwestii takich podzespołów, jak kadłub samolotu, producenci idą w dwóch różnych kierunkach. Z jednej strony widzimy coraz większą popularność aluminium, choć w podzespołach do samolotów należy stosować nowe typy aluminium, odznaczające się m.in. większą wytrzymałością i odpornością na zużycie zmęczeniowe. Podejście to zakłada pozostanie przy tradycyjnej konstrukcji samolotu, która składa się – w uproszczeniu – z wielkiej rury ze skrzydłami i silnikiem.
Odmienną strategią jest poszukiwanie innych kształtów samolotu, takich jak delta, skrzydła połączone z kadłubem i podparte rozpórkami, lub dalej idące wbudowanie silników w kadłub. W tym przypadku inżynierowie będą zapewne częściej korzystać z materiałów kompozytowych, połączeń kompozytów z ceramiką i materiałów mieszanych. Przyszłość pokaże, czy konstrukcje te zdobędą popularność. Obecnie można mieć pewność, że częściej wykorzystywanymi materiałami będą aluminium i superstopy żaroodporne (HRSA). Superstopy żaroodporne (nadstopy) to grupa materiałów często wykorzystywanych w konstrukcji części samolotów, które muszą sprostać ekstremalnym wymogom w zakresie wytrzymałości. Ich znaczna wytrzymałość na wysokie temperatury oznacza, że materiały te utrzymują swoją twardość także w skrajnie wysokiej temperaturze.
Jednak nawet najlepsi producenci podzespołów lotniczych mogą nie mieć doświadczenia w produkcji tych udarnych materiałów. Właśnie na tym polu specjalistyczna wiedza Sandvik Coromant okazała się przydatna.
Pakiety rozwiązań
Firma Sandvik Coromant oferuje pakiety rozwiązań w odpowiedzi na rosnący nacisk na wielozadaniowość obrabiarek. Zamiast skupiać się na jednej obrabiarce, dzisiejsi inżynierowie obsługują cztery lub pięć maszyn na raz, przez co mają mniej czasu i okazji, by koncentrować się na poszczególnych procesach. Co jednak rozumiemy pod pojęciem pakietu rozwiązań? W takim przypadku przyjmujemy bardziej całościową perspektywę, co oznacza, że chodzi nie tylko o dostarczane przez Sandvik Coromant narzędzia, lecz także o pomoc w realizacji całego procesu.
Tak stało się w przypadku klienta Sandvik Coromant z branży lotniczej, który borykał się z trudnościami podczas obróbki superstopów żaroodpornych (HRSA). Stosowana przez klienta strategia wymagała zastosowania wielu obrabiarek przy słabej kontroli spływu wiórów i długich czasach realizacji. Występowały problemy ze zmienną trwałością narzędzi i niezawodnością procesów, a obróbka często wymagała monitorowania przez cały czas przez operatora.
W przypadku tego rodzaju kosztownych projektów pakiet rozwiązań Sandvik Coromant składa się z kilku etapów. Są to: analiza wymogów obróbki, badania czasowe w celu ustalenia kosztu jednostkowego przedmiotu oraz analiza metod produkcji przy rozruchu, obejmująca pomiar czasu metody (MTM) i procesy końcowe u użytkownika końcowego. Pakiet rozwiązań obejmuje także programowanie za pomocą narzędzi do komputerowego wspomagania produkcji (CAM) oraz zarządzanie projektami lokalnymi lub transgranicznymi.
Analizy te wykazały, że aby rozwiązać problemy klienty z odłamywaniem wiórów, należało zmienić jego strategię programowania. Jako uzupełnienie narzędzia specjaliści z Sandvik Coromant zaprojektowali nową strategię wykorzystującą dynamiczne krzywe napędu, co umożliwiło kontrolę odłamywania wiórów w dowolnym momencie. Nazwaliśmy to nowe podejście scoop turning i obecnie dysponujemy prawami patentowymi do tego rozwiązania.
Metoda „scoop turning” przyniosła klientowi znaczne oszczędności. Oprócz doskonałej kontroli spływu wiórów, klient odnotował skrócenie czasu cyklu o 80% przy podwojonej trwałości narzędzia. Klientowi udało się ograniczyć liczbę wykorzystywanych obrabiarek z czterech do jednej, co zmniejszyło zapotrzebowanie na wielozadaniowość, podniosło poziom bezpieczeństwa obróbki i umożliwiło „zielone światło” dla produkcji.
Pokazuje to, w jaki sposób bardziej holistyczna strategia może wpłynąć korzystnie na końcowy bilans producenta. Dużą rolę odgrywa także oprogramowanie, takie jak CoroPlus® Tool Guide, będące częścią cyfrowego asortymentu firmy Sandvik Coromant. Klienci mogą podejmować kluczowe decyzje dotyczące doboru narzędzi i parametrów skrawania przed przystąpieniem do produkcji.
Bardziej zrównoważone toczenie
Producenci z branży lotniczej mają zróżnicowane podejście do kwestii zrównoważonego rozwoju. Mimo to firmie Sandvik Coromant udało się stworzyć spersonalizowane rozwiązanie dla jednego klienta, które później przyniosło korzyści całym segmentom przemysłu.
Aby pomóc klientowi poprawić parametry toczenia superstopów żaroodpornych, firma Sandvik Coromant opracowała gatunek tokarski S205. Płytka posiada pokrycie wykonane w technologii Inveio® drugiej generacji, zapewniając dużą odporność na zużycie i wysoką trwałość. Wynika z tego odporność ostrzy w gatunku S205, która jest większa również dzięki obróbce wykończeniowej płytki polegającej na zmianie jej właściwości mechanicznych. Warstwę materiału wykonaną w technologii Inveio® charakteryzują gęsto obsadzone, uporządkowane w jednym kierunku ziarna, które tworzą mocną barierę ochronną wokół płytki. Daje to maksymalną ochronę termiczną i zapewnia większą odporność na zużycie kraterowe i starcie powierzchni przyłożenia.
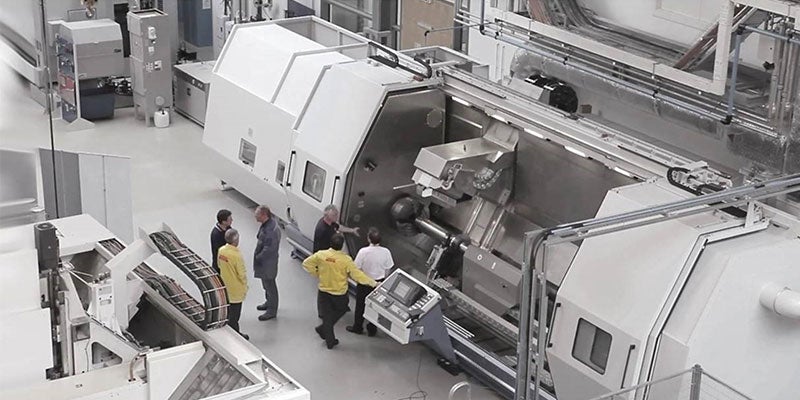
Gatunek nadaje się do obróbki takich podzespołów, jak tarcze turbin silników lotniczych, pierścienie i wały. Nasi klienci poinformowali o wzroście prędkości skrawania o 30 do 50% po zastosowaniu gatunku S205 w porównaniu do konkurencyjnych gatunków do toczenia superstopów żaroodpornych. Zmiana ta nie miała negatywnego wpływu na trwałość narzędzia. Od czasu wprowadzenia na rynek gatunek S205 przyniósł korzyści kilku producentom w przemyśle lotniczym i kilku innych branżach. Wyniki te osiągnięto stosującpodejście holistyczne, a konkretnie stworzoną przez Sandvik Coromant filozofię PrimeTurning™ umożliwiającą toczenie we wszystkich kierunkach w celu uzyskania maksymalnej produktywności.
U podstaw metody PrimeTurningTM leży zagłębianie ostrza w materiał przy uchwycie i toczenie przejściem od uchwytu. W rezultacie najwyższy priorytet ma wydajność skrawania metalu, co oznacza szybszą, wysokiej jakości produkcję i szybsze zmiany wyposażenia. W niektórych przypadkach naszym kllientom udało się zrealizować przebiego produkcyjne z zaledwie jedną zmianą narzędzia, natomiast stosując produkt konkurencji musieliby je zmieniać pięć razy.
Być może branża lotnicza stoi przed największym kryzysem w swojej historii, ale widać już światełko w tunelu. Firma Sandvik Coromant nadal wspiera wszystkich czołowych producentów sprzętu lotniczego i wspomaga ich postpandemiczny powrót na ścieżkę wzrostu, łącząc zrównoważony rozwój z lepszymi narzędziami, zoptymalizowanymi parametrami skrawania i całościowym podejściem do kwestii narzędzi.