Niezawodny sposób na mikrouszkodzenia
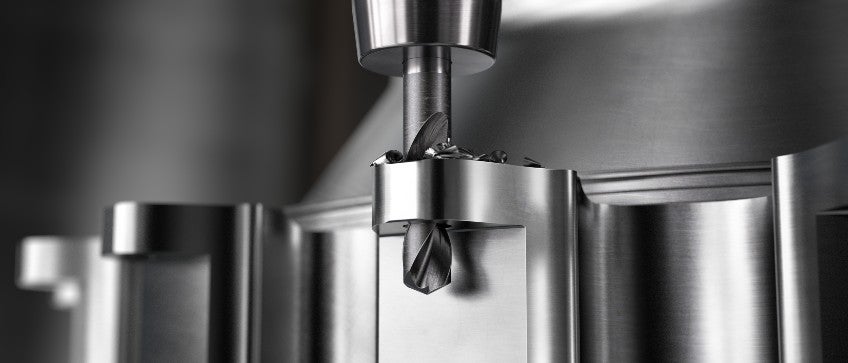
Testy wiertła węglikowego o ulepszonej konstrukcji potwierdzają nowe możliwości w zakresie jakości wykonywanych otworów.
„Mierz dwa razy, tnij raz” to znana dewiza w branży produkcyjnej, ale w przypadku obróbki trudno skrawalnych materiałów łatwiej to powiedzieć niż zrealizować. Dlatego gdy czołowy światowy producent z branży lotniczej szukał sposobu na wyeliminowanie powiercania, a jednocześnie poprawę jakości otworów wykonywanych w podzespołach lotniczych, zwrócił się do światowego lidera w dziedzinie obróbki skrawaniem. James Thorpe, globalny kierownik ds. produktu w firmie Sandvik Coromant, wyjaśnia w artykule, dlaczego konstrukcja wiertła ma zasadnicze znaczenie dla poprawy jakości otworu.
Wykonywanie otworów to najczęściej spotykany ze wszystkich procesów obróbki, ale także najczęściej uważany za oczywisty. Wiele zakładów obróbki skrawaniem nie widzi powodu, by zmieniać lub modernizować istniejącą konfigurację wykonywania otworów i od lat korzysta z tych samych narzędzi i parametrów skrawania. Ale, także z powodu trudnych do przewidzenia konsekwencji pandemii COVID-19, przyszedł czas na zmiany. Producenci napotkali nieprzewidziane lecz trwałe zmiany w potrzebach klientów i dostrzegli teraz konieczność dostosowania produkcji.
Przykładowo, większość producentów poszukuje obecnie nowych dostawców i produktów. Zakłady obróbki skrawaniem, które specjalizowały się w określonej dziedzinie produkcji, teraz przestawiają swoje tokarki i frezarki na większy zakres wytrzymałych i trudnych w obróbce materiałów. Jednocześnie producenci są zmuszeni do poszukiwania nowych sposobów zwiększenia zysków i skrócenia czasów realizacji, bez uszczerbku dla jakości produktu.
Innymi słowy, nadszedł czas, by producenci ponownie przemyśleli sposoby wykonywania otworów.
Biała warstwa
Stan warstwy wierzchniej w otworze to realne wyzwanie dla producentów z branży lotniczej lub firm z branży maszynowej, które chciałyby rozszerzyć działalność na podzespoły lotnicze. Wyższa jakość otworów jest istotna dla zapobiegania awariom podzespołów, a w znacznym stopniu decydują o niej procesy produkcyjne zastosowane do wykonywania lub obróbki wykończeniowej otworów.
Rozwiązania narzędziowe i zaawansowane geometrie wierteł stale ewoluują, aby sprostać najsurowszym normom w zakresie produkcji i jakości przedmiotu. Zastosowanie chłodziwa ogranicza przyrost temperatury w narzędziu. Testy wykazały, że każdy z tych czynników może sprzyjać opanowaniu tzw. efektu „białej warstwy” na powierzchniach obrobionych.
Pojęcie białej warstwy wprowadził czołowy światowy producent z branży lotniczej, który jest także klientem Sandvik Coromant. Oznacza ono cienkowarstwową, bardzo drobnoziarnistą mikrostrukturę pojawiającą się na powierzchni obrobionej m.in. po wierceniu, której przyczyną jest wysoka temperatura narzędzia (wiertła). Biała warstwa może nie tylko zmienić właściwości warstwy wierzchniej, lecz także jest nieakceptowalna z punktu widzenia procesów zarządzania jakością stosowanych przez klienta.
Producent stosuje rygorystyczny proces wykończania otworów w komponentach lotniczych, do których należą tarcze turbin, sprężarki, bębny i wały. Dlatego zdecydował się na partnerstwo z firmą Sandvik Coromant, aby dowiedzieć się, dlaczego tworzy się biała warstwa i jak przeciwdziałać jej powstawaniu.
Warto zauważyć, że zarządzanie jakością nie było wyłączną motywacją do przeprowadzenia testów. Na wyższym poziomie zarządzania klient dążył do zmniejszenia czasochłonności operacji i zwiększenia rentowności poprzez eliminację całego wtórnego procesu obróbkowego.
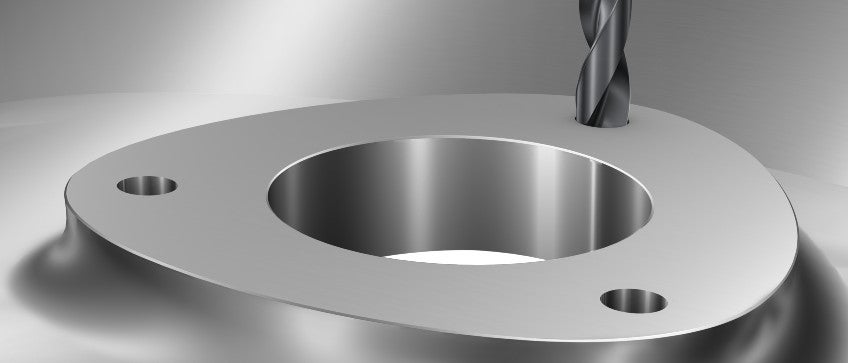
Stan warstwy wierzchniej w otworze to realne wyzwanie dla producentów z branży lotniczej lub firm z branży maszynowej, które rozszerzają działalność na podzespoły lotnicze. W tym przypadku chodzi o wiercenie występów obudowy z superstopu żaroodpornego za pomocą wiertła CoroDrill 860 o geometrii -SM
.
Akt drugi
Wtórny proces następuje po wykonaniu otworu wiertłem węglikowym i może polegać na rozwiercaniu, obróbce wgłębnej lub frezowaniu w celu wykończenia przedmiotu. Proces ten ma na celu głównie sprostanie wymogom otrzymania odpowiedniego stanu warstwy wierzchniej – ograniczając występowanie takich zjawisk, jak biała warstwa – a nie osiągnięciu precyzji wymiarowej, za wyjątkiem obróbki wąsko tolerowanych otworów.
Z punktu widzenia łącznych kosztów, wtórny proces jest droższy niż wiercenie z użyciem niskich parametrów skrawania, czyli alternatywny sposób uzyskania akceptowalnego stanu warstwy wierzchniej. Dlatego klient Sandvik Coromant chciał zbadać możliwość całkowitej rezygnacji z tego procesu. Dostawca oferujący produkt, za pomocą którego można wykonać otwór o odpowiednich wymiarach bez zastosowania wtórnego procesu obróbkowego, ma dobrą pozycję wyjściową, by znacznie zmniejszyć koszt jednostkowy wykonania przedmiotu.
Badanie przyczyn i ewentualnych sposobów zapobiegania powstawaniu białej warstwy polegało na przeprowadzeniu czterech testów wiercenia, popularnego w branży lotniczej, bardzo wytrzymałego niklowo-chromowego stopu Inconel 718. Pierwszy raz zdarzyło się, by tego rodzaju badanie zostało przeprowadzone przez klienta.
Testy obejmowały wiercenie przy użyciu dwóch monolitycznych wierteł węglikowych Sandvik Coromant: CoroDrill® R840 i CoroDrill® R846. W przypadku każdego z wierteł zastosowano dwa różne zestawy parametrów skrawania: odpowiednio 58 mm/min i 98 mm/min dla prędkości posuwu oraz prędkość obrotową 829 obr./min i 757 obr./min. Podczas testów mierzono dane dotyczące oporów skrawania i momentu obrotowego, a także grubość białej warstwy.
W okresie po przeprowadzeniu testów wiertło CoroDrill R840 zostało zastąpione przez CoroDrill® 860 o geometrii -GM, a wiertło CoroDrill R846 – przez CoroDrill® 860 o geometrii -SM. Każde z tych narzędzi kolejnej generacji miało na celu dalsze zwiększenie trwałości bez pogorszenia jakości otworu.
Na podstawie wyników testów wyciągnięto cenne wnioski dotyczące przyczyn powstawania białej warstwy. Warto zauważyć, że wiertło CoroDrill R846 pozostawiało mniejszą białą warstwę, dzięki przygotowaniu zakrzywionych krawędzi skrawających. Jednocześnie proste krawędzie skrawające i faza krawędzi skrawającej wiertła CoroDrill R840 okazały się powiązane ze wzrostem oporów skrawania, momentu obrotowego i grubości białej warstwy. Zatem konstrukcja wiertła decyduje o tym, czy można osiągnąć wysoką jakość otworu poprzez redukcję białej warstwy bez pogorszenia parametrów skrawania.
Testy przeprowadzone przez wiodącego na świecie producenta z branży lotniczej z udziałem firmy Sandvik Coromant nie tylko pozwoliły dowiedzieć się kilku rzeczy o zjawisku białej warstwy: firmie udało się również wyeliminować niektóre wtórne procesy obróbkowe, np. rozwiercanie i frezowanie wgłębne, co zaowocowało oszczędnością czasu i kosztów. Ponadto wyniki te potwierdziły trafność konstrukcji stworzonego przez Sandvik Coromant asortymentu wierteł węglikowych CoroDrill 860.
Wyższość konstrukcji
Asortyment obejmuje wspomniane wiertło CoroDrill 860 o geometrii -GM, które ma pełnić rolę uniwersalnego wykonawcy zadań wiercenia wymagających materiałów z grup ISO P, M, K i H we wszystkich branżach przemysłu. Wiertło CoroDrill 860 o geometrii -SM jest zoptymalizowane pod kątem obróbki materiałów z grupy ISO S, takich jak superstopy żaroodporne (HRSA), stopy tytanu i Inconel. To drugie wiertło sprawdziło się zwłaszcza w branży lotniczej.
Tworząc wiertła CoroDrill 860 o geometrii -GM i CoroDrill 860 o geometrii -SM, inżynierowie firmy Sandvik Coromant wcielili w życie przekonanie, że większa trwałość narzędzia i wyższa jakość otworu zależą od konstrukcji wiertła. W wiertle CoroDrill 860 o geometrii -GM zastosowano konstrukcję, której polerowane rowki wiórowe o innowacyjnej konstrukcji usprawniają odprowadzanie wiórów, rdzeń jest bardziej wytrzymały, a opory skrawania podczas wiercenia – mniejsze.
Z kolei wiertło CoroDrill 860 o geometrii -SM charakteryzuje się nowym gatunkiem materiału narzędziowego oraz zoptymalizowaną i udoskonaloną geometrią wierzchołka, co dodatkowo zwiększa trwałość narzędzia podczas obróbki trudno skrawalnych materiałów z grupy superstopów żaroodpornych. W efekcie uzyskuje się wyższą jakość otworu.
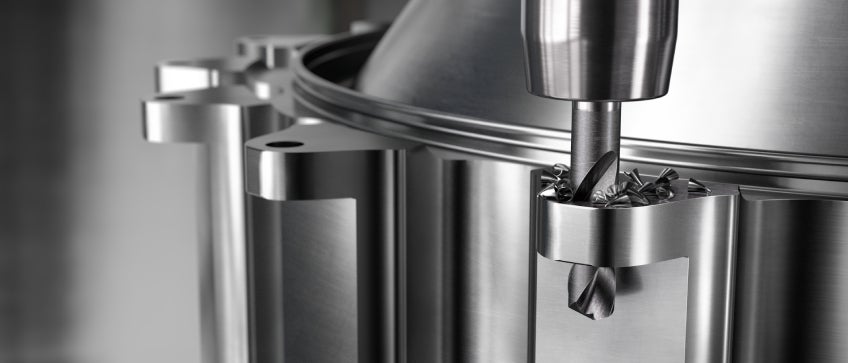
Wiertło CoroDrill 860 o geometrii -SM udowadnia, że większa trwałość narzędzia i wyższa jakość otworu zależą od konstrukcji wiertła.
Wiertło CoroDrill 860 zostało wcześniej sprawdzone w ramach testów poprzedzających wprowadzenie na rynek w szeregu branż. Francuska firma z branży maszynowej zastosowała wiertło CoroDrill 860 o geometrii -GM do obróbki stali konstrukcyjnej AISI 4140. Firmie udało się wykonać wysokiej jakości otwory, wywiercone za pomocą wiertła zagłębiającego się w powierzchnię wklęsłą i wypukłą, przy dobrej prostoliniowości i klasie tolerancji. Od tego czasu producent ten nawiązał nową relację biznesową z firmą Sandvik Coromant.
Inny klient Sandvik Coromant, włoski producent z branży maszynowej, osiągnął wzrost produktywności o ponad 45% w porównaniu z produktem konkurencji dzięki zastosowaniu wiertła CoroDrill 860 o geometrii -GM do obróbki wytrzymałego stopu stali 34CrNiMo6. Ponadto trwałość narzędzia wzrosła o 100%. W innych przypadkach wiertło CoroDrill 860 o geometrii -SM umożliwiło osiągnięcie imponujących wyników obróbki Inconelu 718. Zwłaszcza testy przeprowadzone w Katowicach, porównujące wiertło CoroDrill 860 o geometrii -SM z wiertłem CoroDrill R840, umożliwiły zwiększenie trwałości narzędzia o 180%.
Bez względu na branżę – lotniczą, maszynową lub inne obszary – zastosowanie wiertła o odpowiedniej konstrukcji umożliwia osiągnięcie wysokiej jakości. Zarazem wspomagające wytwarzanie narzędzia cyfrowe, takie jak stworzona przez Sandvik Coromant aplikacja internetowa CoroPlus® Tool Guide mogą oferować większe wsparcie. Za pośrednictwem przeglądarki internetowej i po wprowadzeniu zmiennych takich jak: gatunek materiału obrabianego, średnica i głębokość otworu, użytkownicy mogą dobrać najlepsze narzędzie (w tym wiertło monolityczne) i parametry skrawania, zgodne ze swoimi wymogami.
Choć w przypadku wiercenia nie udało się jeszcze wprowadzić w życie maksymy „Mierz dwa razy, tnij raz”, wydajność wierteł CoroDrill 860 o geometrii -GM oraz CoroDrill 860 o geometrii -SM sprzyja ponownemu przemyśleniu przez producentów stosowanych przez nich metod wykonywania otworów.