Wat is profielfrezen?
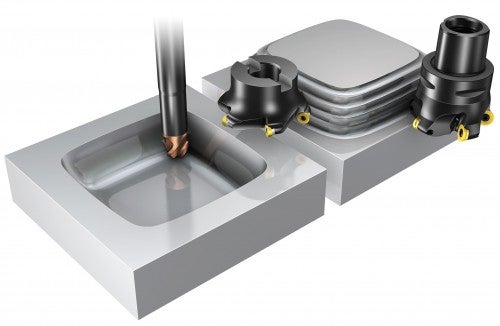
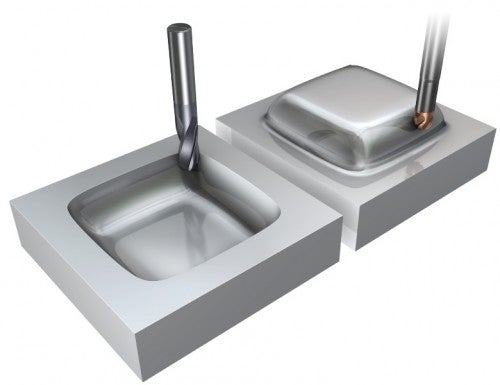
Profielfrezen is een gebruikelijke freesbewerking. Ronde wisselplaten en concepten met radius zijn frezen die worden gebruikt voor voorbewerken en semi-voorbewerken terwijl radiusfrezen worden gebruik voor nabewerking en super-nabewerken.
Profielfreesproces
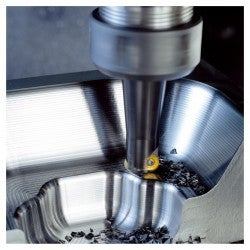
Profielfrezen beslaat multi-as frezen van convexe en concave vormen in twee- en drie dimensies. Hoe groter het werkstuk en hoe gecompliceerder de machine, des te belangrijker wordt de planning voor profielfrezen.
Het bewerkingsproces moet worden opgedeeld in tenminste drie bewerkingstypen:
- Voorbewerken/semi-voorbewerken
- Semi-nabewerken
- Nabewerken
Super-nabewerken, vaak uitgevoerd met hogesnelheid bewerkingstechnieken, is soms nodig. Frezen van resterende toegift, het zogenaamde restfrezen, is inbegrepen in semi-nabewerken en nabewerken. Voor de beste nauwkeurigheid en productiviteit wordt aanbevolen voorbewerken en nabewerken in afzonderlijke machines uit te voeren en om voor elke bewerking geoptimaliseerde snijgereedschappen te gebruiken.
De nabewerking moet worden uitgevoerd in een 4/5-assige machine met geavanceerde software en programmeringstechnieken. Dit kan het tijdrovende handmatige afwerken aanzienlijk reduceren of zelfs volledig elimineren. Het eindresultaat wordt een product met een betere geometrische nauwkeurigheid en een hogere kwaliteit van de oppervlaktestructuur.
Keuze van gereedschappen
Geoptimaliseerde snijgereedschappen voor voorbewerken en semi-voorbewerken:
ronde wisselplaten en concepten met radius.
Geoptimaliseerde snijgereedschappen voor nabewerking en super-nabewerken:
radiusfrees en concept met radius.
![]() | ![]() | ![]() | ![]() | |
Ronde wisselplaten | Wisselplaat radiusfrees | Radiusfrees verwisselbare - kop | Radiusfrees volhardmetaal | |
Machine / spindelgrootte | ISO 40, 50 | ISO 40, 50 | ISO 30, 40 | ISO 30, 40 |
Stabiliteitsvereiste | Hoog | Middelzwaar | Middelzwaar | Laag |
Voorbewerken | Zeer goed | Goed | Acceptabel | Acceptabel |
Nabewerken | Acceptabel | Acceptabel | Zeer goed | Zeer goed |
Snedediepte ap | Middelzwaar | Middelzwaar | Klein | Klein |
Veelzijdigheid | Zeer goed | Zeer goed | Zeer goed | Zeer goed |
Productiviteit | Zeer goed | Goed | Goed | Goed |
Toepassing checklist voor profielfrezen
Het profiel van het werkstuk moet zorgvuldig worden bestudeerd om de juiste gereedschappen te selecteren en om de meest geschikte bewerkingsmethode te vinden:
- Definieer de minimum radii en maximum uitsparingsdiepte
- Schat de hoeveelheid materiaal dat moet verwijderd worden
- Houd rekening met de gereedschapsopstelling en opspanning van het werkstuk om trillingen te voorkomen. Alle bewerkingen moeten worden uitgevoerd op geoptimaliseerde machines om een goede geometrische nauwkeurigheid op het profiel te realiseren
- Door gebruik te maken van afzonderlijke, nauwkeurige bewerkingsgmachines voor nabewerken en super-nabewerken, kan de noodzaak voor tijdrovende handmatige polijstbewerkingen worden gereduceerd en in sommige gevallen geëlimineerd
- Er kan geavanceerde programmering nodig zijn om grote besparingen te realiseren. Gebruik een volhardmetalen vingerfrees met hoge snelheidstechniek voor het bewerken van minimale toeslag vormen en het behalen van de best mogelijke afwerking
- Voorbewerken en semi-nabewerken van grote componenten worden doorgaans het meest productief uitgevoerd met conventionele methoden en gereedschappen. Een uitzondering vormt aluminium, waarvoor hoge snijsnelheden ook worden gebruikt voor voorbewerken
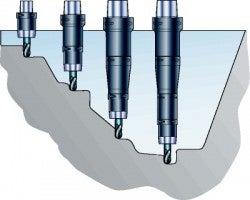
Hoe trillingen te reduceren
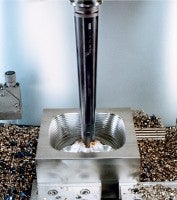
Trillingen vormen een obstakel bij het frezen van diepe profielen bij het gebruik van lange uitsteeklengten. Gangbare methoden om dit probleem te verhelpen zijn een verlaging van de snedediepte, snelheid of voeding.
- Gebruik stijve modulaire gereedschappen met een goede rondloopnauwkeurigheid
- Modulaire gereedschappen verhogen de flexibiliteit en het mogelijke aantal combinaties
- Gebruik gedempte gereedschappen of verlengbaren wanneer de totale gereedschapslengte, van de referentielijn tot het laagste punt van de snijkant, groter is dan 4−5 maal de diameter bij de referentielijn
- Gebruik verlengingen gemaakt van zwaar metaal, wanneer de buigstijfheid radicaal verhoogd moet worden
- Gebruik gebalanceerde snijgereedschappen en houders voor spiltoerentallen hoger dan 20.000 tpm
- Kies de grootst mogelijke diameter op de verlengstukken en adapters iten opzichte van de freesdiameter
- 1 mm (0.039 inch) in radiaal verschil tussen de houder en het snijgereedschap is voldoende. Gebruik overgedimensioneerde frezen
- Plungefrezen is een alternatieve methode voor het frezen met extra lange gereedschappen
Verleng de gereedschapslengte geleidelijk
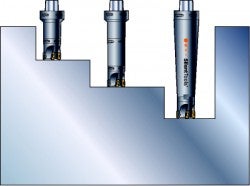

Om een maximale productiviteit bij voorbewerkingen te handhaven, waar zich de laatste gang diep in het component bevindt, is het belangrijk te werken met een serie verlengingen voor de frees.
- Beging met de kortste verlenging, omdat langere verlengingen de productiviteit beperken en de neiging hebben om trillingen te veroorzaken
- Wissel de verlengde gereedschappen op vooraf bepaalde posities in het programma. De geometrie van de uitsparing bepaalt het wisselpunt
- Pas de snijgegevens aan elke gereedschapslengte aan om de maximale productiviteit te handhaven
Werkelijke freessnelheid
Bij het gebruik van een nominale diameterwaarde van het gereedschap bij het berekenen van de snijsnelheid van een radiusfrees of frees met ronde wisselplaten, zal de werkelijke freessnelheid, vc, veel lager zijn, wanneer de snedediepte, ap, ondiep is. Tafelvoeding en productiviteit worden ernstig gehinderd.
Basisberekeningen van snijsnelheid van de werkelijke of effectieve diameter in snede, Dcap.
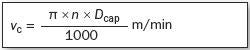
Hoek vingerfrees
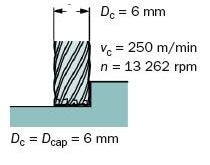
Radiusfrees
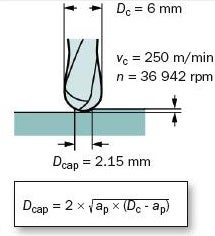
Frees met ronde wisselplaten
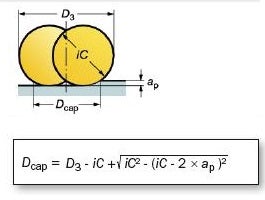
Puntfrezen – gekantelde frees
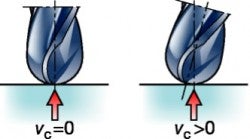
Bij gebruik van een radiusfrees, is het meest kritische gebied van de snijkant het gereedschapscentrum, waar de snijsnelheid dicht bij nul is, hetgeen ongunstig is voor het snijproces. Spaanafvoer bij het gereedschapscentrum is van kritisch belang, vanwege de nauwe ruimte bij de beitelrand.
Daarom wordt het kantelen van de spil of het werkstuk met 10 tot 15 graden aanbevolen, waardoor de snijzone weg van het gereedschapscentrum wordt bewogen.
- De minimale snijsnelheid wordt hoger
- Verbeterde gereedschapslevensduur en spaanvorming
- Betere oppervlakte-afwerking
Voorbeeld van centrum snijdende frezen
Centraal deel, z = 2
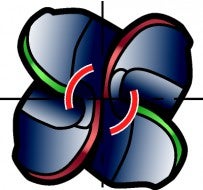
Perifeer deel, z = 4
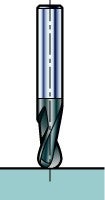
Z = 2
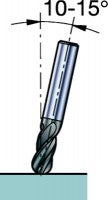
Z = 4
Ondiepe snede
Bij het gebruik van een ronde wisselplaat of een radiusfrees bij een geringere snedediepte, kan de snijsnelheid, vc worden verhoogd, dankzij de korte aangrijptijd voor de snijkant. De tijd voor hitteverspreiding in de snijzone wordt korter, d.w.z. de snijkant en de temperatuur van het werkstuk worden beide laag gehouden. Tevens kan de voeding/tand, fz worden verhoogd, vanwege het spaanverdunnend effect.
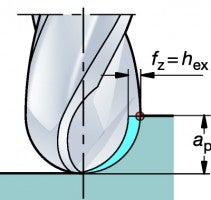
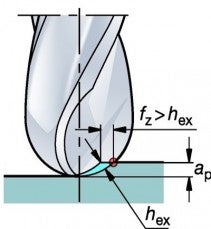
Ondiepe snede
Voorbeeld ondiepe snede, niet gekantelde versus gekantelde frees
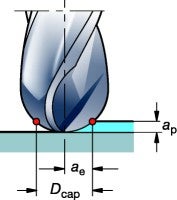
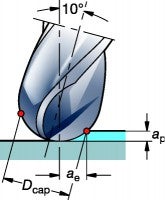
Dit voorbeeld toont de mogelijkheden voor het verhogen van de snijsnelheid wanneer de ae/ap klein is, alsmede de voordelen van het gebruik van een gekantelde frees.
Radiusfrees volhardmetaal
Dc = 10 mm, soort GC 1610.
Materiaal: Staal, 400HB
Snijgegevens aanbeveling voor een diepe snedeap - Dc/2:
vc = 170 m/min
fz = 0.08 mm/omw = hex
apSemi-nabewerken - 2 mm (0.079 inch) vc - 300 m/min (984 ft/min) De snelheid kan verder worden verhoogd met ca. 75% dankzij de | vc hex vf Dc = 10 mm (0.394 inch) | vc hex vf Dc = 10 mm (0.394 inch) |
vc - 5 * 170 - 850 m/min (557–2789 ft/min) Opmerking: fz aeSuper-nabewerken - 0.1 mm | Een niet gekantelde frees wordt niet aanbevolen voor supernabewerken | vc hex vf Dc = 10 mm (0.394 inch) |
Productiviteit in profielfrezen: constante toegift
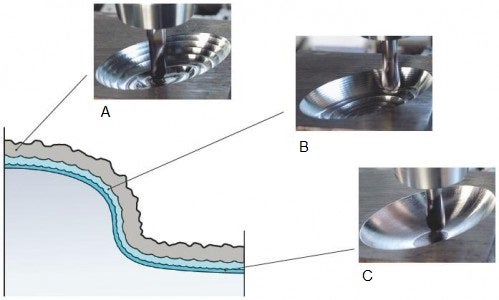
A: Voorbewerken
B: Semi-nabewerken
C: Nabewerking en super-nabewerken
Een constante toegift is een van de belangrijkste basiscriteria voor een hoge en constante productiviteit bij profielfrezen, met name bij het gebruik van hoge snelheden.
- Voor het behalen van de maximale productiviteit in deze bewerkingen, gangbaar bij de productie van mallen en matrijzen, is het belangrijk de grootte van de frezen aan te passen aan de specifieke bewerkingen
- Het primaire doel is het creëren van een gelijkmatig verdeelde werktoeslag, of toegift, om te zorgen voor weinig wisselingen in de werkbelasting en richting van elk gereedschap dat wordt gebruikt
Het is vaak gunstiger om de maten van de verschillende frezen te laten verlopen, van groter naar kleiner, vooral bij licht voorbewerken en semi-nabewerken, in plaats van het gebruiken van slechts één diameter bij elke bewerking.
- De beste nabewerkingskwaliteit wordt gerealiseerd wanneer voorgaande bewerkingen zo weinig mogelijk en een zo constant mogelijke hoeveelheid toegift als mogelijk over laten
- Het doel moet altijd zijn om zo dicht mogelijk bij de opgegeven vereisten te komen voor de uiteindelijke vorm
- Veilig snijproces
Voordelen met een constante toegift
- Sommige semi-nabewerkingen en vrijwel alle nabewerkingen kunnen deels bemand of soms zelfs onbemand worden uitgevoerd
- De invloed op de geleidingen van de bewerkingsmachine, kogelspindels en spillagers zal minder ongunstig zijn
Openen van een massief werkstuk
- Bij het openen van een uitsparing, is het belangrijk een methode te kiezen die ap minimaliseert en ook een constante toegift achterlaat voor de volgende profielfreesbewerking
- Schouder vlak/vingerfrezen of lange snijkantsfrezen zullen een getrapte toegift achterlaten die verwijderd moet worden. Dit genereert variabele snijkrachten en gereedshapsafbuigingen. Het resultaat is een ongelijke toegift voor nabewerking, hetgeen invloed heeft op de geometrische nauwkeurigheid van de uiteindelijke vorm
- Het gebruik van frezen met ronde wisselplaten zal soepele overgangen tussen de passen genereren en minder toegift in gelijkmatigere hoeveelheden over laten voor de profielfreesbewerking, hetgeen resulteert in een betere componentkwaliteit
- Een derde alternatief is het gebruik van een frees met hoge voeding om de uitsparing te openen. Dit resulteert ook in een kleine en zelfs constante toegift, vanwege de geringe snedediepte, d.w.z. kleine getrapte overgangen
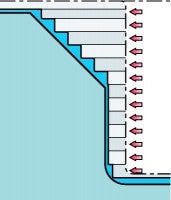
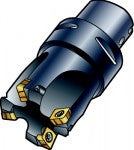
Schouderfrees,
grotere en ongelijkmatigere toegift blijft achter
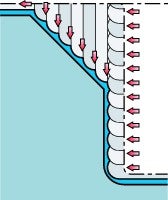
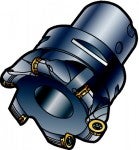
Frees met ronde wisselplate,
geringe toegift blijft achter
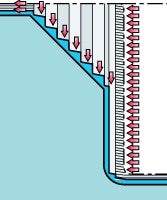
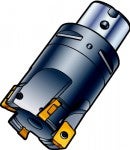
Frees met hoge voeding,
geringe hoeveelheid toegift blijft achter
Kopieerfrezen
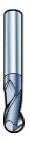
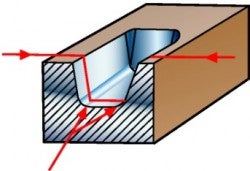
De traditionele en gemakkelijkste methode voor het programmeren van gereedschapspaden voor een uitsparing is het gebruik van de normale kopieerfreestechniek, met vele malen intreden en uittreden in het materiaal. Echter, dit betekent dat krachtige softwareprogramma's, machines en snijgereedschappen op een zeer beperkte manier worden ingezet. Het geniet de voorkeur een machine te gebruiken met software die vooruitziende functionaliteit heeft om gereedschapspadafwijkingen te voorkomen.
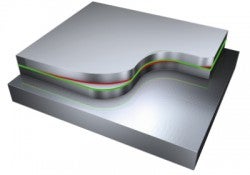
Een open benadering ten aanzien van de keuze van methoden, gereedschapspaden, freesgereedschappen en houders is essentieel.
− Zware belasting op het centrumpunt van de wisselplaat
− Gereduceerde voedingen
− Gereduceerde standtijd
− Mechanische impact
− Vormfouten
− Langere programma's en snijtijd
Een kopieerfrees gereedschapspad is vaak een combinatie van tegenlopend- en meelopend frezen en vereist veel ongunstige in- en uittredingen in de snede. Elke intrede en uittrede betekent dat het gereedschap afbuigt, hetgeen een verhoogde markering op het oppervlakte achterlaat. De snijkrachten en de afbuiging van het gereedschap zullen afnemen en er zal sprake zijn van een geringe mate van ondersnijden van het materiaal in de uittreedzone.
Conclusies
- Kopieerfrezen langs steile wanden moet zoveel mogelijk worden vermeden. Bij plunge-frezen, is de spaandikte groot en moet de snijsnelheid laag zijn
- Er bestaat een risico van snijkantuitbrokkeling bij het gereedschapscentrum, vooral wanneer de frees het bodemgebied raakt
- Gebruik een voedingssnelheidsregeling met een vooruitkijkfunctie. Anders zal de vertraging niet snel genoeg zijn om beschadiging van het gereedschapscentrum te voorkomen
- Er zal sprake zijn van een grote contactlengte wanneer de frees de wand raakt, met risico van afbuiging, trilling of gereedschapsbreuk
- Bij het gebruik van radiusfrezen, is het meest kritische gedeelte het gereedschapscentrum, omdat de snijsnelheid nul is. Voorkom het gebruik van het gereedschapcentrumgebied en gebruik puntfrezen door de spil of het werkstuk te kantelen om de condities te verbeteren
- Het is iets beter voor het snijproces om tegenlopend kopiëren te gebruiken langs steile wanden, omdat de spaandikte haar maximum heeft bij een gunstigere snijsnelheid
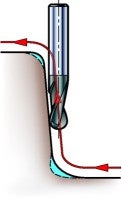
Risico op kerven
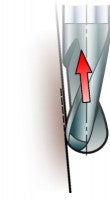
Tegenlopend kopiëren:
Maximum spaandikte bij aanbevolen vc.
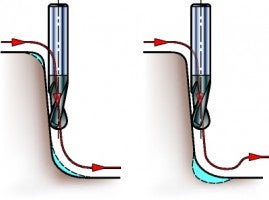
Onderin de uitsparing:
Risico van uitbrokkeling bij gereedschapscentrum.
Vormfouten zijn gangbaar, vooral bij het gebruik van de hogesnelheid bewerkingstechniek.
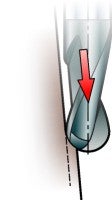
Meelopend kopiëren:
Grote spaandikte bij zeer lage vc.
Voedingsreductie om verkorting van de standtijd te voorkomen
Omgekeerd tegenlopend- en meelopend frezen zal het gereedschap blootstellen aan wisselende afbuigings- en snijkrachten. Door de voedingssnelheid in de kritische secties van het gereedschapspad te reduceren, wordt het risico op snijkantuitbrokkeling gereduceerd, en een veiliger snijproces met langere standtijd wordt bereikt.
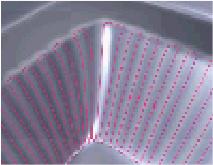
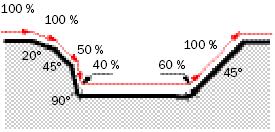
Contourfrezen
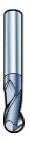
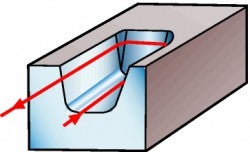
In plaats van het gebruiken van programmeertechnieken die zijn beperkt tot het "afschaven" van materiaal bij een constante Z-waarde, is het uiterst gunstig om contouring gereedschapspaden te gebruiken in combinatie met meelopend frezen. De resultaten zijn onder andere:
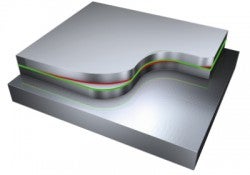
+ Een aanzienlijk kortere bewerkingstijd
+ Betere machine- en gereedschapsgebruik
+ Verbeterde geometrische kwaliteit van de bewerkte vorm
+ Minder tijdrovende bewerking en handmatig polijstwerk
+ Snijsnelheidsregeling - ve
+ Maakt HSM mogelijk
+ Hoge voedingswaarden
+ Lange levensduur van de wisselplaat
+ Zekerheid
Het initiële programmeerwerk is moeilijker en zal iets langer duren; echter, deze wordt snel terugverdiend, omdat de bewerkingskosten per uur normaal gesproken drie keer zo hoog is als die van een werkstation. Het geniet de voorkeur een machine te gebruiken met software die vooruitziende functionaliteit heeft om gereedschapspadafwijkingen te voorkomen.Conclusies
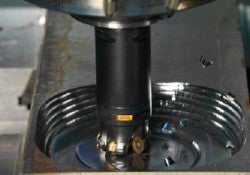
- Gebruik een contouring type gereedschapspad, zoals “waterlijnfrezen”, als de beste methode om meelopend frezen te waarborgen
- Contouring met de periferie van de frees resulteert vaak in een hogere productiviteit, omdat er meer tanden effectief in snede zijn op een grotere gereedschapsdiameter
- Wanneer het spiltoerental in de machine is beperkt, dan zal contouring helpen de snijsnelheid te handhaven en te besturen
- Contouring genereert tevens minder snelle wisselingen in de werkbelasting en -richting. Bij het hoge snelheid en voedingsfrezen in geharde materialen, is dit van speciaal belang, omdat de snijkant en het proces kwetsbaarder zijn voor eventuele wijzigingen die grote verschillen kunnen creëren in afbuiging of die trillingen kunnen creëren
- Blijf voor een goede standtijd continu in snede, en zo lang mogelijk
Opm.! Vermijd snijden met het centrum van het gereedschap (snijsnelheid nul).
Gereedschapspadstrategie
Z – constante contouring, twee assen. Voorbewerken tot nabewerken
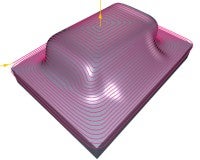
Waterlijnfrezen Z - constante contouring
- Algemeen gangbaar wanneer CAM- bestuurde maximale schulprandfunctie beschikbaar is
- Soepele aangrijping en terugtrekking
- Eenvoudige programmering
- Brede gereedschapskeuze
Spiraalvormige contouring, drie – vijf assen. Nabewerken
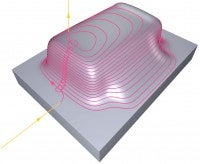
Contouring in een hellend gereedschapspad
- Soepele richtingsveranderingen
- Goede vormnauwkeurigheid en oppervlakte-afwerking
- Gecontroleerde schulprandhoogte
- Constante aangrijping
- Korte programma's
- Kort gereedschap
Genereren van gesculpteerde oppervlakken
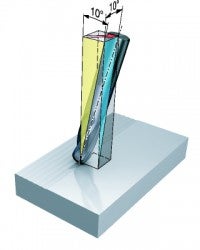
Meelopend frezen met een frees die ca. 10° is gekanteld .in twee richtingen, waarborgt een goede oppervlakte-afwerking en een betrouwbare prestatie. Een radiusfrees of een radiusvormige snijkant zal een oppervlakte vormen met een bepaalde ribbelhoogte, h, afhankelijk van:
- Breedte, ae, van de snede
- Voeding per tand, fz
Andere belangrijke factoren zijn de snedediepte, ap, welke invloed heeft op de snijkrachten en de gereedschapsindicator uitlezing van de rondloop – TIR. Voor de beste resultaten:
- Gebruik de hoge precisie Coromant Capto® hydraulische spantanghouder
- Minimaliseer gereedschapuitsteeklengte
Voorbewerken/semi-voorbewerken
Wanneer de voeding per tand veel kleiner is dan de breedte en snedediepte, dan zal het gegenereerde oppervlakte een veel kleinere ribbelhoogte in de voedingsrichting hebben.
Nabewerken en superfijn nafrezen
Het is gunstig om een gladde, symmetrische oppervlaktestructuur in alle richtingen te realiseren, welke naderhand heel gemakkelijk kan worden gepolijst, ongeacht de gekozen polijstmethode.
Dit wordt verkregen wanneer fz ≈ ae.
Gebruik altijd een gekantelde tweetands frees bij super-nabewerken om de beste oppervlaktetextuur te behalen.
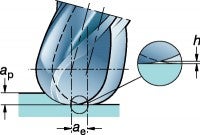
Semi-voorbewerken met fz veel kleiner dan ae
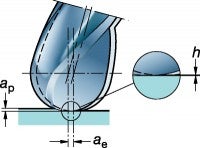
Super-nabewerken met een gekantelde frees en fz gelijk aan ae
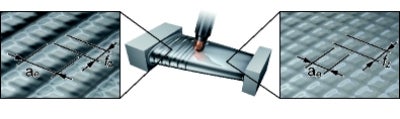