나사 밀링 가공 적용 팁
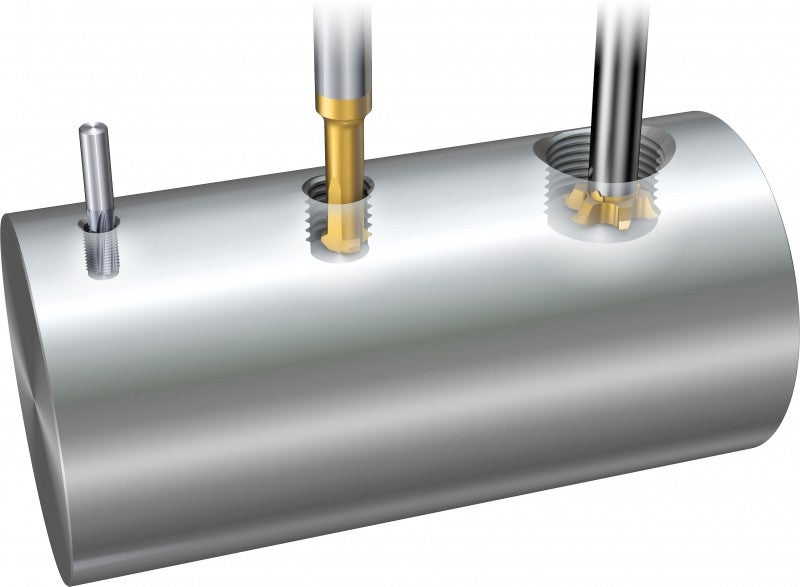
나사 밀링 가공에서 최상의 결과를 얻으려면 항상 다음 권장사항을 고려하십시오.
절삭 직경의 선택
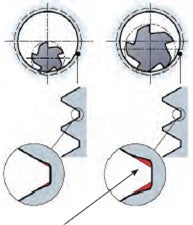
절삭 직경이 작을수록 더 높은 품질의 나사를 얻을 수 있습니다. 커터를 사용하면 나사 형상에서 나사골에 미세한 형태의 오류가 발생합니다. 내경 나사 밀링 가공에서는 나사 직경, 가공 직경 그리고 피치 간의 관계는 반경 방향의 실제 절입 깊이에 영향을 미칩니다.(ae eff)영향은 선택된 반경 절입 깊이 보다 휠씬 커집니다. 실제 ae가 커질수록 나사 골의 편차가 증가합니다. 나사 형상의 편차를 최소화하려면 커터 직경이 나사 가공 직경의 70%보다 커서는 안 됩니다.
예: M30x3
직경이 21.7 mm인 공구는 나사 형상의 편차가 0.07 mm (0.0027 inch)입니다.
직경이 11.7 mm인 공구는 나사 형상의 편차가 0.01 mm (0.0004 inch)입니다.
나사 밀링 공구 경로
나사 밀링 공구 경로는 하향 또는 상향 밀링을 사용해 우승수 또는 좌승수 나사를 제공합니다. 항상 부드러운 경로로 나사 밀링 커터를 진입 또는 진출시키십시오(롤 인/롤 아웃 가공). 나사 밀링 가공에는 X, Y 및 Z축에서 동시 이동이 가능한 가공 기계가 필요합니다. 나사 직경은 X와 Y축에 의해 결정되고 피치는 Z축에 의해 제어됩니다.
피치 | ![]() |
우승수 내경 나사
처음에 모든 커터는 홀 바닥에 가능한 한 가깝게 위치하고, 그런 다음 하향 밀링을 위해 위로 반시계 방향으로 이동합니다.
좌승수 내경 나사
좌승수 나사의 밀링 가공은 하향 밀링을 위해 반시계 방향 경로로 위에서 아래로 반대 방향으로 진행됩니다.
내경 | |
---|---|
우승수 나사 | 좌승수 나사 |
하향 밀링 | |
![]() |
![]() |
상향 밀링 | |
![]() | ![]() |
외경 | |
---|---|
우승수 나사 | 좌승수 나사 |
하향 밀링 | |
![]() |
![]() |
상향 밀링 | |
![]() |
![]() |
하향 밀링

- 하향 밀링은 공구가 공구 회전 방향으로 이송되는 경우입니다.
- 하향 밀링은 가공 기계, 지그 및 가공물이 허용하는 한 항상 권장되는 방법입니다.
- 칩 두께가 절삭 시작부터 끝까지 0에 도달할 때까지 감소하며, 날이 절삭으로 진입하기 전에 표면에 대한 날 러빙과 버닝을 멈춥니다.
상향 밀링
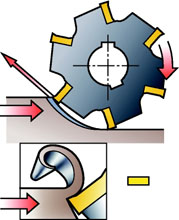
- 상향 밀링에서는 절삭 공구의 이송 방향이 회전 방향의 반대입니다.
- 절삭날은 절삭 부위로 강제로 진입해야 하기 때문에 마찰에 의한 마찰이나 버니싱 효과, 고온 및 종종 이전 절삭날에 의한 가공 경화된 표면을 접촉해야 합니다. 이 모든 것이 공구 수명을 단축시킵니다.
- 절삭 진출 부위에서 두꺼운 칩은 공구 수명을 단축시킵니다.
- 진출 부위에서 큰 칩 두께와 높은 온도로 인해 때때로 칩이 절삭날에 들러붙거나 융착되고, 다음 절삭의 시작 부위로 옮겨지거나 날 깨짐 현상을 유발합니다.
절삭으로 진입 – 롤인
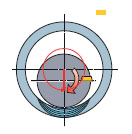
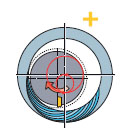
원호 밀링 가공이나 원호 램핑 가공에서는 부드럽게 진입하십시오. 이는 추가적인 반원 실행을 통해 가능하고, 그 결과 소재로 서서히 진입하게 됩니다. 절삭으로 진입하는 동안 1/4 회전(90°)할 때마다 피치를 4로 나누어야 합니다. 절삭으로의 부드러운 진입은 진동 방지와 공구 수명 연장에 필수적입니다.
날당 이송
최상의 품질을 얻고 가공물 표면에 이송 자국이 나타나지 않도록 하려면 항상 작은 날당 이송 값을 사용하십시오. 날당 이송이 0.15 mm/날(0.006 inch/날)를 초과하면 안 되기 때문에 작은 Hex 값이 필요합니다.
기계 소프트웨어에서 요구하는 이송
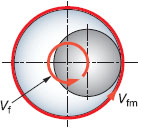
항상 기계 소프트웨어에서 요구하는 올바른 나사 밀링 이송률을 계산해 올바른 인서트 부하를 보장하십시오. 이송은 원주 이송률과 일치하는 Hex 값에 항상 의존합니다. 그러나 대부분의 기계는 공구 중심 이송(vf)을 요구합니다. 내경 나사 밀링 가공에서는 원주의 공구 경로가 공구 중심선의 이동보다 빠릅니다. 대부분의 밀링 기계에서 이송률 프로그래밍은 스핀들의 중심선을 기준으로 하고, 공구 수명을 극대화하고 진동/공구 파손을 방지할 수 있도록 나사 밀링 가공 계산에 이를 반드시 포함시켜야 합니다.
패스 수
나사 밀링 가공을 몇 번의 패스로 나누면 나사 피치가 더 커지고 난삭재에서 공구 파손에 대한 안정성이 향상됩니다. 나사 밀링 가공을 몇 번의 패스로 나누면 공구 휨이 감소해 나사 공차도 향상됩니다. 그 결과 긴 오버행과 불안정한 조건에서 안정성이 향상됩니다. 고경도 소재와 난삭재에서 나사 밀링 가공을 수행할 때는 항상 2회 이상의 패스를 사용하십시오.
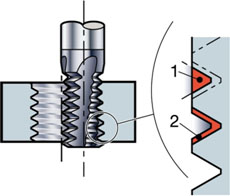
건식 또는 습식 가공
절삭유가 입구와 출구에서 온도 변화를 강화해 열 균열을 발생시키므로 건식 가공이 항상 권장됩니다. 스테인리스강/알루미늄의 정삭, HRSA 가공, 주철 가공 같은 일부 경우에서는 절삭유가 유리할 수 있습니다(독성 먼지 감소). 그러나 압축 공기를 사용해 칩을 배출하는 것이 가장 좋습니다.
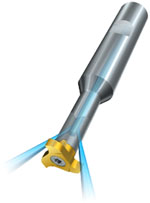
절삭 조건 고려사항
- 내경 나사 밀링 가공 적용에서 직선 절삭에 비해 ae가 증가하여 칩이 얇아지는 효과가 감소합니다.
- 외경 나사 밀링 가공에서는 반경 방향 깊이가 훨씬 작아지고 더 높은 절삭 속도를 사용할 수 있습니다.
- 노즈 반경의 절입각은 90°입니다. 이것이 인서트에서 가장 민감한 부분이기 때문에 90°의 절입각을 사용해 Hex 계산을 수행해야 합니다.
절삭 조건 및 값은 CoroPlus® ToolGuide를 참조하십시오.
나사 밀링 홀 크기
나사 밀링 커터는 태핑 가공과 같은 홀 크기를 사용합니다. 항상 공차를 벗어나지 않으면서 최대한 큰 홀을 선택하십시오. 그러면 더욱 안정적인 공정과 긴 공구 수명이 보장됩니다. 풀 프로파일 인서트를 사용할 때는 나사 상단의 가공을 위해 더 작은 홀이 필요합니다.
취급
스크류 클램프 방식 인서트가 있는 공구 홀더에서 최상의 성능에 도달하려면 항상 토크 렌치를 사용해 인서트를 단단히 고정해야 합니다.
- 토크를 너무 높게 설정하면 공구 성능에 부정적인 영향을 미치고 인서트와 스크류가 파손됩니다.
- 토크를 너무 낮게 설정하면 진동이 발생하고 절삭 결과가 부정확해집니다.
- 인서트 스크류를 정기적으로 교체하고, 팁 시트가 깨끗하고 인서트를 오프셋할 수 있는 방해물이 없는지 확인하십시오. 이러한 점검은 나사 밀링 공정의 신뢰성을 위해 필수적입니다.

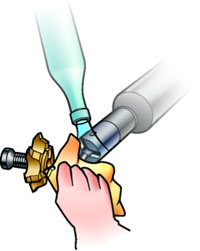