旋削加工でのクーラントおよび切削油の使用方法
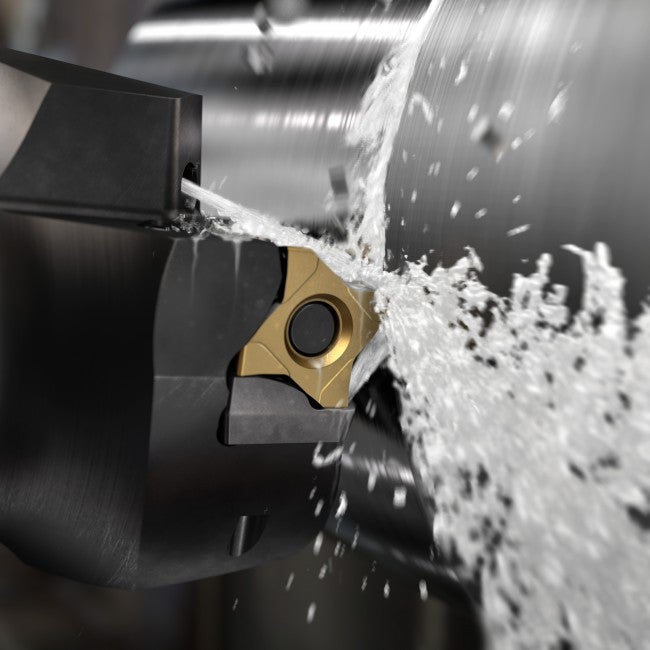
切削油の主な役割は、工具と被削材間の切りくず排出、冷却、潤滑です。正しく使用すると、生産量は最大になり、加工安定性が高まり、工具性能と加工部品の品質が向上します。
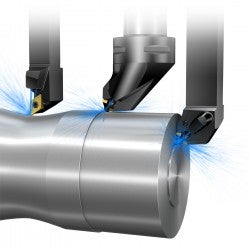
場合によっては、クーラントを使用せずに加工すること(ドライ加工)が環境やコストの面でのメリットになります。ドライ加工を行う場合は、最善の工具、形状および材種を選定するために、サンドビック・コロマントのスペシャリストにご連絡ください。
多くの加工では、公差、加工面品質、被削性の要素のためにクーラントが必要です。クーラントが必要な場合は、最適化を行って能力を最大限に発揮させる必要があります。
切削加工にとって重要なクーラントの特徴にはさまざまなものがあります:
- クーラント媒体
- クーラント出口
- クーラント圧
クーラント媒体
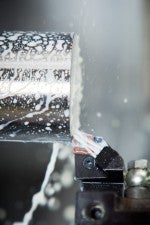
旋削時に使用されるクーラント媒体は多数あります:
- エマルジョン:水と油を混ぜたもの(水に5–10%の油)が最も一般的なクーラント媒体です
- 油:一部の機械では、油がエマルジョンの代わりに使用されます
- 圧縮空気:切りくず排出に使用されますが、良好には熱を取り除きません
- MQL - セミドライ加工 - 潤滑のための最低量の油と圧縮空気
- 極低温クーラント:冷却効果を最大にするために、液化ガスがクーラントとして使用されます
旋削工具のクーラントチャンネルを通して、エマルジョン、油および空気を使用することができます。クーラントを一般的な言葉で表現すれば、エマルジョンまたは油を含む冷却液です。MQLと極低温クーラントには特殊な装置が必要です。
クーラント出口
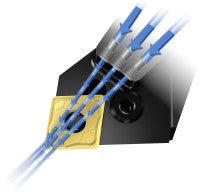
最新の旋削工具では、工具を通して内部クーラントが供給され、これらの多くは実際に、高精度のすくい面へのクーラントと逃げ面へのクーラントを提供します。工具内の出口には以下のタイプがあり、加工に対してさまざまなメリットをもたらします:
- 高精度クーラントまたは高精度のすくい面へのクーラント:ノズル(または同様のもの)がクーラントビームを直接すくい面側の切削領域の方へ向かわせます。温度を下げ、切りくず処理を改善します。切りくず処理を改善するために高圧で使用できます
- 逃げ面へのクーラント:逃げ面側のクーラントビームが効果的にチップから熱を取り除き、それによって工具寿命が長くなります
- 従来のクーラント出口:例えば、ほとんどの場合に高精度クーラントノズルよりも大きな出口径を持つ調整式ノズル。加工中にクーラントがチップと加工部品の上を流れるようになっています(フラッドクーラントと呼ばれることもあります)。これらの工具は高圧での使用向けには作られていません
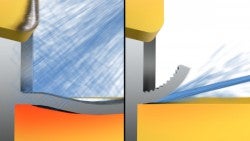
従来のクーラントと高精度クーラント
高精度クーラント
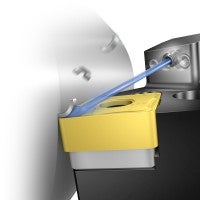
最近の旋削工具に装備されているノズルは、正確にすくい面側の切削領域の方へ向かう高精度クーラントを供給して、切りくず処理を制御し、安定した加工を提供します。機械の能力を最大限に活かし、さらに工具寿命と切りくず生成を向上させるために、ノズル径を変えてクーラント供給と流量を微調整することができます。
低圧でも高精度クーラントの良好な効果を得ることができますが、圧力が高いほどより加工が困難な被削材でも優れた加工結果を出すことができます。
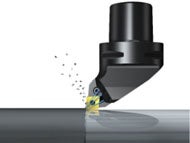
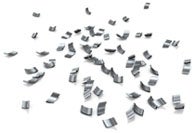
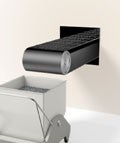
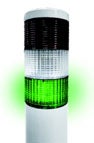
高精度クーラントにより、切りくず処理の向上、工具寿命の延長、加工安定性および生産性の向上が実現されます。
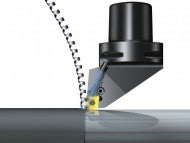
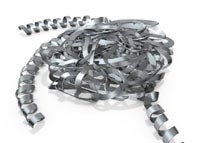
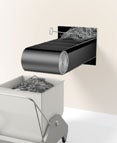
高精度クーラントなしでは、切りくず詰まりが問題となることがあり、機械の停止、サービススタッフの呼び出し、工具の摩耗増加、加工面品質の低下などが発生します。
逃げ面へのクーラント
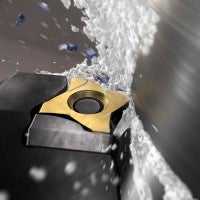
最新の旋削コンセプトは、逃げ面へのクーラントも特徴としています。逃げ面へのクーラントは切削領域の熱を制御し、工具寿命を延ばし、安定した加工をもたらします。
逃げ面へのクーラントは低圧ですでに非常に効率的ですが、圧力が高いほど工具寿命の延長の面でより大きな効果が見られます。生産量を向上させるために、切削速度または送りを上げることができます。
すくい面へのクーラントと逃げ面へのクーラントのどちらを使用するか?あるいは両方を使用するか?
すくい面へのクーラント(高精度クーラント)と逃げ面へのクーラントを特徴とする工具を使用する際、すくい面へのクーラントを止めた方が良い結果を得られる場合があります。これは、加工する被削材、材種および切削条件に大きく左右されます。
耐熱合金(ISO S)用の第一推奨のPVD材種のような薄膜コーティング材種の場合、チップを熱から保護して塑性変形を防ぐために、すくい面/逃げ面へのクーラントの両方を使用するのが最善です。
鋼材(ISO P)と鋳鉄(ISO K)用の第一推奨のCVD材種のような厚膜コーティング材種の場合は、コーティングの中に優れた熱保護作用があります。これらの材種は荒加工から中荒加工において、逃げ面へのクーラントのみを使用した場合に最高の工具寿命を得られる可能性があります。以下に示す鋼材(ISO P)に関する青色の図と説明をご覧ください。
ステンレス鋼(ISO M)用の第一推奨のCVD材種のような中膜厚コーティング材種の場合は、すくい面/逃げ面へのクーラントの両方を使用することをお勧めします。ただし、加工ですくい面摩耗が発生する場合は、逃げ面へのクーラントのみを使用するようにして、工具寿命を比べてください。
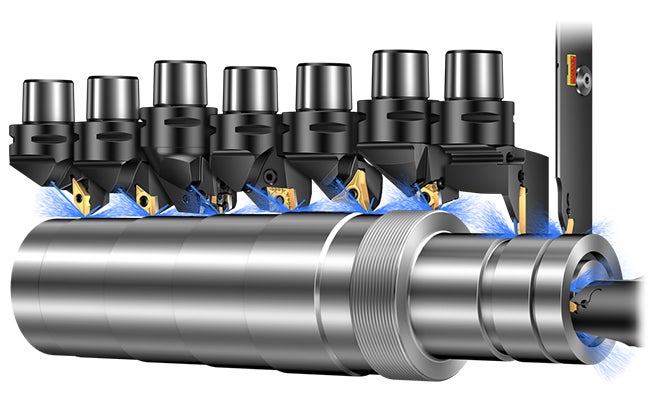
鋼旋削加工に推奨されるクーラント
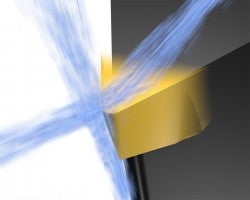
- 工具寿命を延ばすには逃げ面へのクーラントを使用します
- 通常は青色の切込み深さ (ap) と送り (fn) の領域内で必要とされ、切りくず処理の改善が必要な場所では、すくい面へのクーラント(と逃げ面へのクーラント)を使用します
- 青色の領域外ですくい面へのクーラントを使用すると、副切刃に摩耗が発生し、すくい面摩耗が進行する原因となります。すくい面摩耗は判断が難しい場合が多いため、工具寿命がより短く、予測しにくくなります。これが、逃げ面へのクーラントが推奨される理由です。(逃げ面へのクーラントが使用できない場合は、従来のクーラント出口を備えた工具を使用してください)
ap (mm) | |
![]() | fn (mm/r) |
さまざまな被削材におけるすくい面/逃げ面へのクーラントによるメリット
被削材 | |||
P | CVD | ||
PVD | 切りくず処理/工具寿命 | ||
M | CVD | 切りくず処理 | |
PVD | 切りくず処理/工具寿命 | ||
K | CVD | 工具寿命 | |
セラミック | 工具寿命 | ||
N | ノンコート | 切りくず処理/工具寿命 | |
PVD | 切りくず処理/工具寿命 | ||
PCD(ダイヤモンド) | 切りくず処理/工具寿命 | ||
S | PVD | 切りくず処理/工具寿命 | |
セラミック | 切りくず処理 |
被削材 | 材種 | すくい面へのクーラント | 逃げ面へのクーラント |
![]() | CVD PVD | 切りくず処理 切りくず処理 / 工具寿命 | |
![]() | CVD PVD | 切りくず処理 切りくず処理 / 工具寿命 | |
![]() | CVD セラミック | 工具寿命 工具寿命 | 工具寿命 |
![]() | ノンコート PVD PCD (ダイヤモンド) | 切りくず処理 / 工具寿命 切りくず処理 / 工具寿命 切りくず処理 / 工具寿命 | |
![]() | PVD セラミック | 切りくず処理 / 工具寿命 切りくず処理 |
クーラント圧
高圧クーラントはエネルギー消費を増加させるため、持続可能性とコストの観点から考える必要があります。ただし、高圧はさまざまな方法で生産性を高めることもできます。
高圧の高精度クーラント
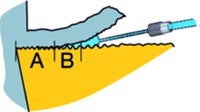
機械内の高圧とノズルの組み合わせによって高速クーラントジェットが実現され、そのクーラント噴射によって油圧ウェッジが生成されます。クーラントジェットには3つの主な効果があります:
- 接触ゾーン (A) 内のチップをより効率的に冷却する
- 切りくずをチップすくい面から素早く強制的に引き離し、チップ (B) の摩耗を低減する
- 切りくずを小さく破砕して、切りくずを切削領域から排出する
適切なクーラント圧の使用
7-10 bar (100-150 psi)
高精度クーラントは、鋼やその他の一般的な被削材で高い切りくず処理と優れた加工安定性を実現します。その高い精度により、加工安定性を維持しながら切削できます。
70-80 bar (1000-1200 psi)
より高い圧力で、切りくず処理も行えます。高精度クーラント用に設計されたブレーカを使用すれば、さらに良い結果が得られます。
150–200 bar (2200–2900 psi)
二相ステンレス鋼や耐熱合金 (HRSA) などの加工が困難な被削材の場合、高いクーラント圧が必要になります。高精度クーラント供給用ノズル付きツールホルダと高精度クーラント専用のブレーカを使用してください。