外径旋削加工
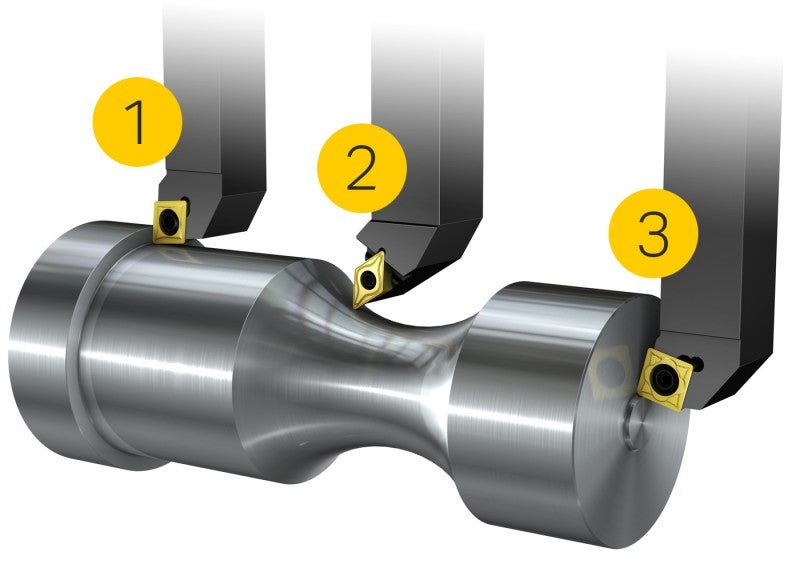
外径旋削加工ではワークの外径を加工します。外径旋削加工は最もよく知られていて、一般に使用されている加工方法の一つであるため、切りくず処理、加工安定性および加工部品の品質に対する要求は高くなっています。外径旋削加工の基本加工領域は、軸送り旋削 (1)、倣い旋削 (2)、そして端面旋削 (3) です。
PrimeTurning™ではあらゆる方向での旋削加工が可能なため、切りくず排出速度が高くなり、最高の生産性が得られます。
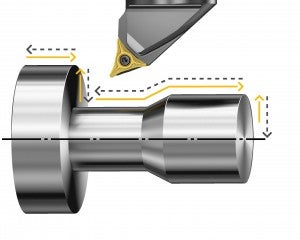
軸送り旋削加工
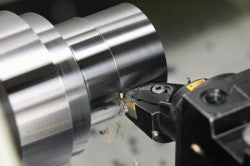
軸送り旋削加工の場合、工具の送り運動は被削材の軸方向となるため、被削材の径は旋削によって小さくなっていきます。これは最も一般的な旋削加工です。
軸送り旋削加工用の工具を選択するときは、チップをツールホルダに固定するシステムを最初に選ぶことをお勧めします。加工タイプと、また、ある程度は加工物の大きさによって選択肢が決まります。大型の加工物を荒加工する場合は、小型部品の仕上げ加工とはかなり要求項目が異なります。
チップ形状
強度と費用効率を求める場合は、刃先角度が最も大きくて適切なチップを選択する必要があります。
切込み角
工具の切込角は切りくず生成に影響を及ぼします。切込み角が90°(アプローチ角0°)の場合、切りくず厚さは送りfnと同じになります。切込み角が75–45°(アプローチ角15–45°)の範囲まで小さくなると、切りくず厚さが薄くなり、送りを上げることが可能です。
ツールホルダ
加工部品内に加工するショルダー部がある場合、切込み角91–95°(アプローチ角-1~-5°)で工具を使用します。第一の選択肢としてC型(80°)チップを使用します。
D型(55°)チップでは倣い加工とぬすみ加工が可能です。
加工するショルダー部がない場合は、正方形チップと切込み角75°(アプローチ角15°)を選択することで、生
産性を向上させることができます。
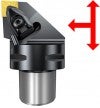

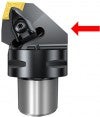
倣い旋削加工
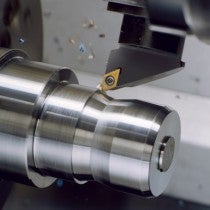
倣い旋削加工では、切込み深さ、送り、切削速度に応じて切削が変化することがあります。倣い旋削加工に使用する工具は、さまざまな加工方向と径変化があるため、応力および切込み深さが大きく変動します。倣い加工工具の最重要特性の一つが接近性です。
チップ形状
強度と費用効率を求める場合は、刃先角度が最も大きくて適切なチップを選択する必要があります。ただし、チップの刃先角度を接近性と関連して考慮する必要があります。最もよく使用される刃先角度は35°と55°です。
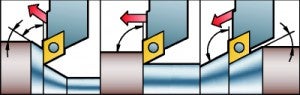
切込み角
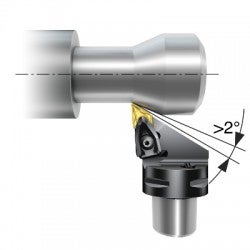
最も適切な切込み角を選択するために、加工物の形状を分析します。加工物からチップまで最低2°の円滑な切込角は維持する必要があります。ただし、加工面品質と工具寿命の観点から、最低7°の切込み角(83°のアプローチ角)をお勧めします。
ツールホルダ
第一推奨は切込み角93°(アプローチ角-3°)の工具とD型(55°)チップです。より大きなランピング角が必要な場合は、V型(35°)チップを使用します。
別の方向への倣い加工あるいはコーナーリリーフ加工を行えるようにするには、切込み角107–117°(アプローチ角-17~-27°)のホルダを選択します。倣い旋削用旋削工具
端面旋削加工
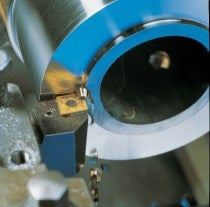
端面旋削加工では、工具が加工物の端で径に沿って中心に向かって送られます。径方向の切削抵抗が高いため、部品がたわむ可能性があり、びびりの原因となることが時々あります。
チップ形状
チップ形状は、必要な切込み角に応じて、加工物に必要な接近性あるいは汎用性に関連して選ぶ必要があります。強度と費用効率を求める場合は、刃先角度が最も大きくて適切なチップを選択する必要があります。
切込み角
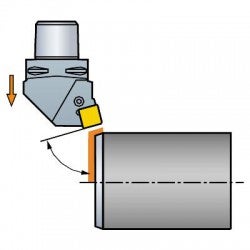
切込み角75°(アプローチ角15°)
切込み角を小さくすることで(アプローチ角を大きくすることで)、径方向の切削抵抗の一部を軸に沿ってチャックに向かわせて、安定性の向上とびびり傾向の軽減を実現することができます。
ツールホルダ
最適化の場合は、正方形チップ、切込み角75°(アプローチ角15°)のホルダを選びます。
汎用性の場合は、菱型チップ80°あるいは六角形チップ、切込み角95°(アプローチ角-5°)のホルダを選びます。端面旋削用旋削工具
PrimeTurning™
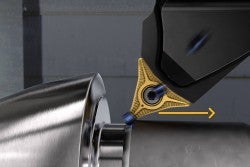
PrimeTurning™は、加工物の終端からチャックに向かう従来の方法とは違って、チャック付近で加工物に切込み、加工物の終端に向かって移動しながら被削材を切削する加工方法です。この旋削方法は、従来の旋削加工に比べてはるかに効率と生産性が高い方法です。
この加工方法は、あらゆる方向への旋削を可能にする柔軟性を提供します。つまり、単一の工具で軸送り加工、端面加工および倣い加工を行うことができます。さらに、同じ工具で従来の旋削加工を行うこともできます。ただし、その場合は生産性も従来と同じです。
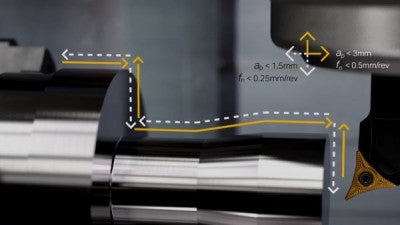
小さい切込み角
PrimeTurning™ではショルダー部に完璧に届き、25–30°の切込み角(65–60°のアプローチ角)が可能です。小さい切込み角によって薄く幅広い切りくずが生成されることで、負荷と熱をノーズRから分散します。その結果、工具寿命が長くなり、より高い切削条件が可能になります。これが生産性を大幅に向上させます。
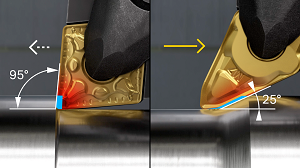
従来の旋削加工対PrimeTurning™
卓越した切りくず排出
切りくず詰まりは、従来の軸送り旋削を利用する際によく発生する問題です。PrimeTurning™では、ショルダー部から離れる方向に切削が行われるため、切りくず詰まりのリスクがありません。
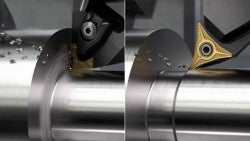
PrimeTurning™の利用時
径方向の切削抵抗が高くなるため、この加工方法には安定性の高い加工部品とセットアップが必要です。短い小物部品およびテールストックを使用する細長い部品の加工に最適です。PrimeTurning™は、大量生産あるいは頻繁なセットアップや工具交換が必要な部品加工に非常に適した選択肢です。CoroTurn® Prime工具に関する詳細はこちら
重旋削加工
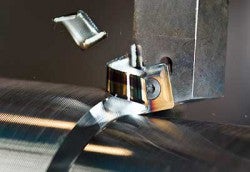
代表的な重旋削加工は大きな加工物の均一でない表面の旋削加工で、切込み深さが非常に大きく、また切込み深さが変化します。
通常切削時間も長いため、切削温度が高くなります。切削速度や回転数はしばしば加工物のサイズやクランプ状態により制限されます。機械はオープンタイプで湿式加工には適していないため、加工はしばしばドライ加工となります。
部品例としては動力エネルギー用の大きなシャフト、プロペラシャフト、大きな原子力容器用のシールドです。
バーピーリング
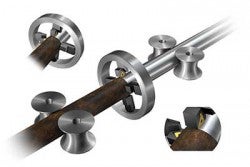
バーピーリングは、酸化物スケール、ミルスケール、表面クラック等を熱間圧延ブランクや鍛ブランクから除去する方法です。また、バーピーリングは肉厚チューブにも適用されます。
ピーリング加工の最も一般的な被削材は、炭素鋼、ばね鋼およびステンレス鋼です。
用途領域はいろいろありますが、バーピーリング済みブランクは、製品の製造における中間ステージとしてよく使用され、その後さらに加工されます。そのような例として、管材製造のための押出しブランクや自動車産業のアクスルコンポーネントを挙げることができます。
従来の旋削と比較してバーピーリングはスループットタイムが短いので、高い生産性と低い生産コストをもたらします。加工面品質と寸法公差も良好で、その結果後続工程での加工の必要も低減されます。重旋削用旋削工具
再旋削および新しい車輪の旋削についてもっと知りたいですか?鉄道車輪の旋削加工ガイドをお読みください。
