Bohrungsherstellung
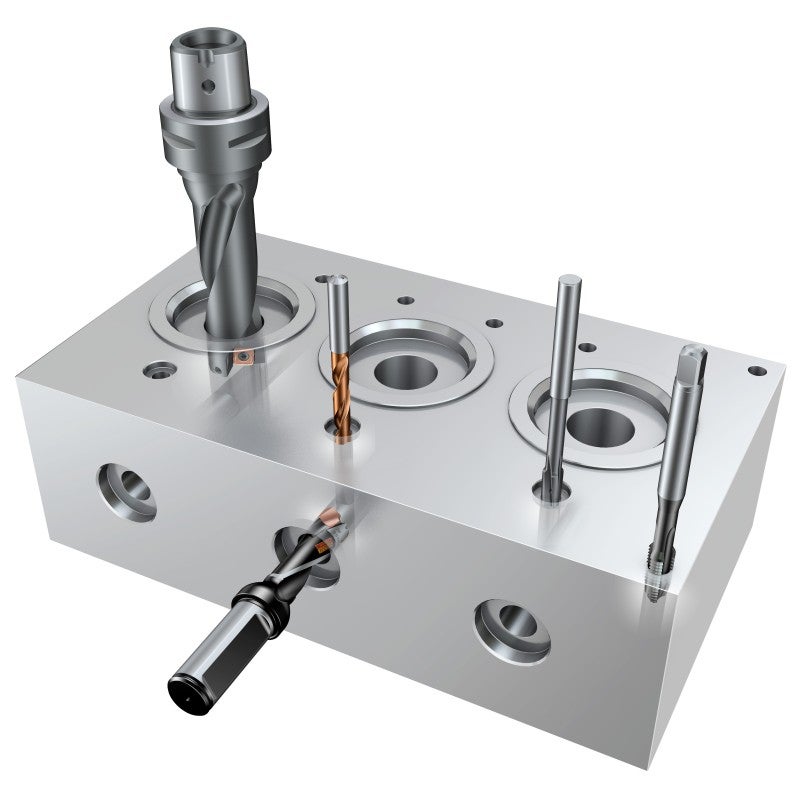
Bohren und Gewindebohren sind Anwendungen, die am Ende des Produktionszyklus durchgeführt werden, wenn der Wert des Bauteils schon relativ hoch ist. Die Anwendung, obwohl sie scheinbar einfach aussieht, ist eine komplexe Bearbeitung, die gravierende Auswirkungen haben können, wenn Ihr Werkzeug nicht richtig funktioniert oder über seine Kapazität eingesetzt wird.
Erste Überlegungen bei der Bohrungsherstellung
1. Die Bohrung
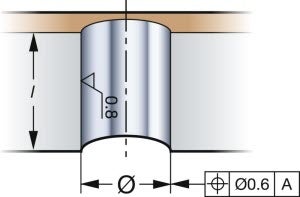
Die wichtigsten drei Hauptparameter für die Bohrung sind:
- Bohrungsdurchmesser
- Bohrungstiefe
- Bohrungsqualität
Der Bohrungstyp und die gewünschte Präzision haben Einfluss auf die Werkzeugwahl. Der Bohrprozess kann durch unregelmäßige oder gewinkelte Ein- und Austrittsflächen sowie durch Kreuzbohrungen beeinflusst werden.
Bohrungstypen
Durchgangsbohrung
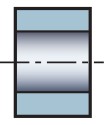
Grundbohrung
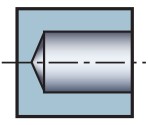
Fasbohrung
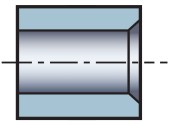
Stufenbohrung
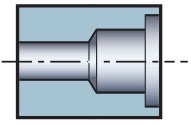
Entrittsbohrung
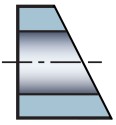
Austrittsbohrung
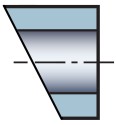
Kreuzbohrung
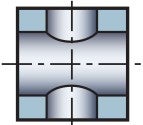
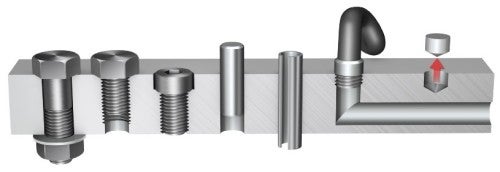
- Bohrung mit Freiraum für Schrauben
- Bohrung mit Schraubgewinde
- Senkbohrung
- Passgenaue Bohrung
- Bohrung für Rohre (Wärmeaustauscher)
- Bohrung, die Kanäle bildet
- Bohrung zum Gewichtsausgleich
- Tiefe Bohrung/Kühlschmierstoffbohrung
2. Das Bauteil
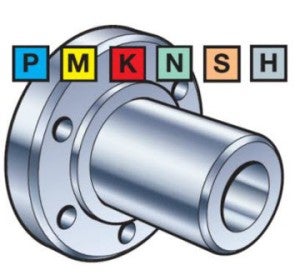
Ist die Bohrung analysiert, werden Werkstoff, Form des Bauteils und Menge näher betrachtet.
Werkstoff
- Verfügt der Werkstoff über gute Spanbruchqualitäten? Lang- oder kurz spanender Werkstoff?
- Zerspanbarkeit?
- Werkstoffhärte?
- Legierungselemente?
Bauteilform
- Verläuft die Werkstückrotation symmetrisch um die Bohrung, d. h. kann die Bohrung mit einem nicht rotierenden Bohrer bearbeitet werden?
- Ist das Werkstück stabil, oder gibt es dünne Abschnitte, die Vibrationen hervorrufen können?
- Kann es sicher aufgespannt werden? Welche Stabilitätsprobleme müssen in Betracht gezogen werden?
- Wird eine Werkzeugverlängerung benötigt? Müssen lange Werkzeugüberhänge eingesetzt werden?
Menge
Die Losgröße beeinflusst die Wahl des Bohrers.
- Großserien - optimierten Bohrer, TM/Spezialbohrer einsetzen
- Kleinserien - für Vielseitigkeit optimierten Bohrer einsetzen
3. Die Maschine
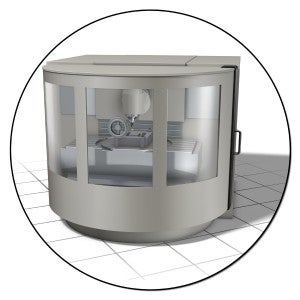
Es ist wichtig zu wissen, wie man einen sicheren und produktiven Bohrprozess in der Maschine erzielt. Die Maschine hat Einfluss auf die:
- Bearbeitungsart
- Wahl von Werkzeughalter- bzw. Spannzangentyp
Folgendes muss immer berücksichtigt werden:
- Maschinenstabilität im Allgemeinen und Stabilität der Spindel im Besonderen
- Ist die Spindeldrehzahl (U/min) ausreichend für kleine Durchmesser?
- Kühlschmierstoffzufuhr. Ist die Kühlschmierstoffmenge ausreichend für Bohrer mit großem Durchmesser?
- Ist der Kühlschmierstoffdruck ausreichend für Bohrer mit kleinem Durchmesser?
- Aufspannung des Werkstücks. Ist die Aufspannung stabil genug?
- Horizontal- oder Vertikalspindel? Eine horizontale Spindel ermöglicht eine bessere Spanabfuhr
- Leistung und Drehmoment. Ist die Leistung für große Durchmesser ausreichend? Falls nicht, kann stattdessen ein Kernbohrer eingesetzt oder Zirkularinterpolation mit einem Fräswerkzeug angewendet werden?
- Ist der Platz im Werkzeugmagazin begrenzt? In diesem Fall kann ein Stufen- und Fasbohrer die beste Lösung sein
Werkzeughalter
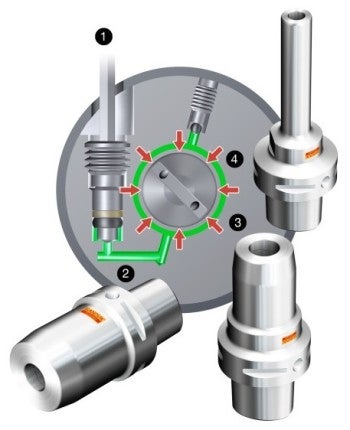
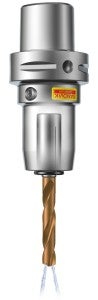
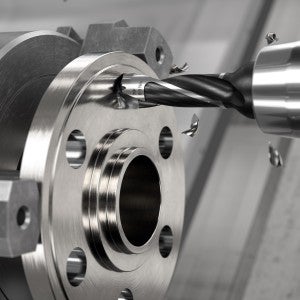
Die Produktivität wird nicht nur durch Sorte und Geometrie beeinflusst, sondern auch durch den Werkzeughalter und einer sicheren und präzisen Aufspannung. Stets den kürzesten Bohrer und die kürzeste Auskraglänge wählen.
Ein modulares Werkzeugsystem in Betracht ziehen, das für alle Zerspanvorgänge ausgelegt ist, sogar für alle Methoden der Bohrungsherstellung. Mit dem System lassen sich dieselben Werkzeuge und Adapter für unterschiedliche Anwendungen und Maschinen einsetzen. So kann standardisiert werden, und lediglich ein Werkzeugsystem ist für die gesamte Werkstatt erforderlich.
Rundlaufgenauigkeit des Werkzeugs
Eine hohe Rundlaufgenauigkeit ist für erfolgreiches Bohren unerlässlich. Die Rundlaufgenauigkeit sollte max. 20 Mikrometer betragen. Die Ausrichtung muss parallel sein für:
- Enge Bohrungstoleranz und -geradheit
- Hohe Oberflächengüte
- Hohe und verlässliche Standzeit
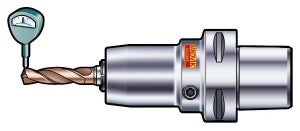
Wahl der Methode
Senken – Strategien
Lösung mit einem Werkzeug
- Stufenbohren/Senken
- Bohrertyp 4/5
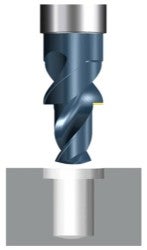
Vorteile
+ Kundenspezifische Werkzeuge
+ Schnellste Methode
Nachteile
- Weniger flexibel
Lösung mit zwei Werkzeugen
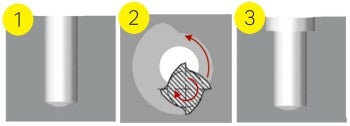
Vorteile
+ Standardwerkzeuge
+ Relativ flexibel
Nachteile
- Zwei Werkzeuge
- Zwei Werkzeugpositionen erforderlich
- Längere Taktzeiten
Stufen- und Fasbohren – Strategie mit einem Bohrertyp
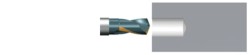
Bohrertyp 1
Standard
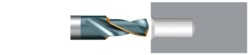
Bohrertyp 2
Bohrer mit 2 Durchmessern (Pilot + Körperdurchmesser)
Mit Pilot und Fase. Ohne Bohren des Körperdurchmessers
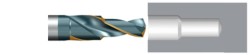
Bohrertyp 4
2 mit 2 Durchmessern (Pilot + Körperdurchmesser)
Mit Bohren von Pilot, Fase und Körperdurchmesser
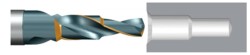
Bohrertyp 5
3 Bohrerdurchmesser (Pilot + Stufe + Körperdurchmesser)
Mit Pilot, Stufe und Fase. Ohne Bohren des Körperdurchmessers
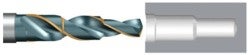
Bohrertyp 6
3 mit 2 Durchmessern (Pilot + Körperdurchmesser)
Mit Bohren von Pilot, Fase und Körperdurchmesser
Suchen Sie Werkzeugempfehlungen?
Hier finden Sie unsere Zerspanungswerkzeuge chevron_right
Brauchen Sie Beratung?
Stellen Sie uns eine Frage chevron_right
Was es sonst noch über die Grundlagen unserer Metallzerspanung zu lernen gibt?
Registrieren Sie sich für unser kostenloses E-Learning Programm chevron_right
Bohrbearbeitungen
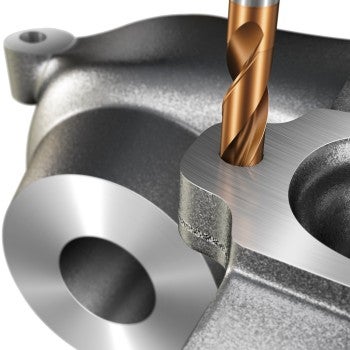
Die richtige Werkzeugwahl zu treffen heißt, dass die gewünschte Bohrungsqualität mit guter Funktionsfähigkeit bei niedrigsten Kosten pro erstellter Bohrung erreicht werden kann. Für die folgenden Bohrungstypen sind unterschiedliche Faktoren zu berücksichtigen:
- Bohrungen mit kleinen bis mittleren Durchmessern
- Bohrungen mit großem Durchmesser
- Tiefe Bohrungen
- Mikrobohrungen
Herstellung von Bohrungen mit kleinen bis mittleren Durchmessern
Für das Bohren kleiner bis mittlerer Durchmesser stehen drei unterschiedliche Bohrlösungen zur Auswahl: Vollhartmetallbohrer, Wechselkopfbohrer und Wendeschneidplattenbohrer. Bohrungstoleranz, Länge und Durchmesser sind drei wichtige Parameter, die bei der Auswahl des Bohrers zu berücksichtigen sind. Jede Lösung hat, je nach Anwendung, ihre eigenen Vorteile.
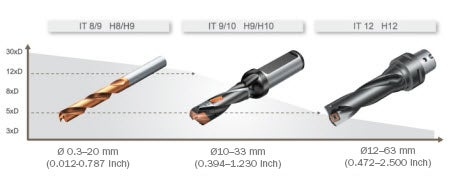
Herstellung von Bohrungen mit großen Durchmessern
Für das Bohren großer Durchmesser bei beschränkter Maschinenleistung gibt es drei Möglichkeiten:
- Einsatz eines Kermbohrers
- Vergrößern der Bohrung mit einem Aufbohrwerkzeug
- Zirkularinterpolation mit Fräswerkzeugen
Beim Erstellen großer Bohrungen steht die Stabilität von Werkstück und Maschine im Vordergrund. Darüber hinaus können auch Maschinenleistung und Drehmoment einschränkende Faktoren darstellen. Aus Sicht der Produktivität sind Bohrwerkzeuge die beste Wahl - 5-mal schneller als das Fräsen einer Bohrung mit Spiralinterpolation. Kernbohrer können allerdings nur für Durchgangsbohrungen verwendet werden. Fräswerkzeuge haben bei weitem die niedrigsten Anforderungen an Leistung und Drehmoment.
Herstellung tiefer Bohrungen
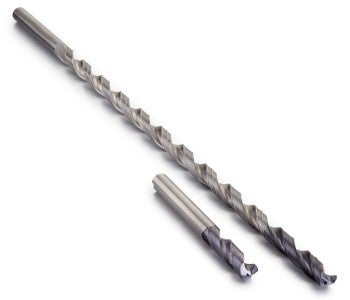
Führungsbohrungen
Pilotbohrer wurden zum Einsatz mit Tieflochbohrern für maximale Präzision und höchste Rundlaufgenauigkeit am Bohrort entwickelt.
Schnittgeschwindigkeiten und Vorschübe
Die für Tiefbohrer empfohlenen Schnittgeschwindigkeiten und Vorschübe gewährleisten eine gute Standzeit gepaart mit maximaler Produktivität. Die angegebenen Schnittgeschwindigkeits- und Vorschubwerte sind ein guter Ausgangspunkt; für optimale Ergebnisse müssen jedoch für jede Anwendung u.U. Anpassungen bei diesen beiden Parametern vorgenommen werden.
Herstellung von Mikrobohrungen
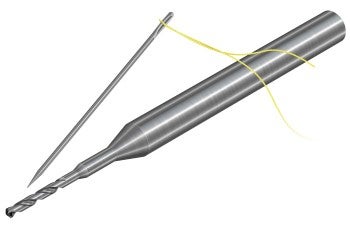
Schnittgeschwindigkeiten und Vorschübe
Die für Mikrobohrer empfohlenen Schnittgeschwindigkeiten und Vorschübe gewährleisten eine gute Standzeit gepaart mit maximaler Produktivität. Die angegebenen Schnittgeschwindigkeits- und Vorschubwerte sind ein guter Ausgangspunkt; für optimale Ergebnisse müssen jedoch für jede Anwendung u.U. Anpassungen bei diesen beiden Parametern vorgenommen werden.
Kühlschmierstoff
Der Kühlschmierstoffdruck ist ein Schlüsselfaktor beim Mikrobohren. Ungeeigneter Kühlschmierstoffdruck oder eine unzureichende Menge kann zu einem vorzeitigen Ausfall des Werkzeugs führen. Wir empfehlen unbedingt hohe Drücke. Normalerweise sollten diese zwischen 40 und 70 bar liegen.
Suchen Sie Werkzeugempfehlungen?
Hier finden Sie unsere Zerspanungswerkzeuge chevron_right
Brauchen Sie Beratung?
Stellen Sie uns eine Frage chevron_right
Was es sonst noch über die Grundlagen unserer Metallzerspanung zu lernen gibt?
Registrieren Sie sich für unser kostenloses E-Learning Programm chevron_right