Lösungen für die produktive Aluminiumbearbeitung in der Automobilindustrie
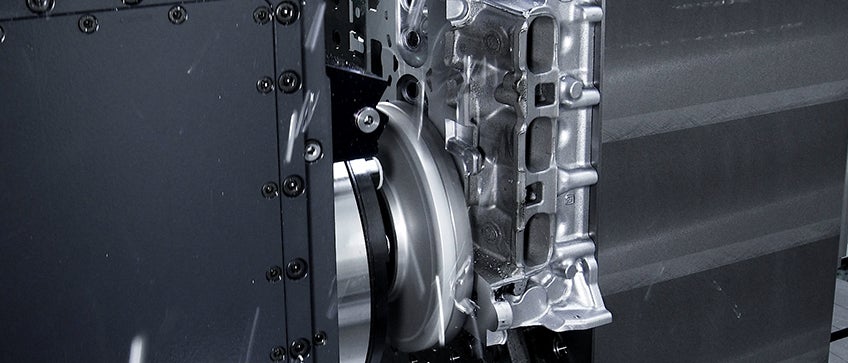
In der Automobilbranche werden zunehmend Motor-, Antriebsstrang-, Wasserpumpen- und Bremssystemteile aus Aluminium verwendet. Die Herausforderung für Erstausrüster (OEMs) und ihre Partner in der Lieferkette besteht darin, produktivere Fräsbearbeitungen umzusetzen. Da der richtige Einsatz von optimierten Fräsern für die gesamte Bandbreite der Bearbeitung von Motorkomponenten erhebliche Vorteile bringen kann, ist die Auswahl der Werkzeuge in diesem Segment der Schlüssel zu einer echten Marktdifferenzierung. Dies erläutert Emmanuel David, Global Product Manager Engineered Solutions Automotive Aluminium bei Sandvik Coromant.
Der Trend zu leichten Werkstoffen hat dazu geführt, dass Aluminium in der Automobilindustrie immer beliebter wird. Der Aluminiumanteil in einem durchschnittlichen Pkw ist von 50 kg im Jahr 1990 auf 151 kg im Jahr 2019 gestiegen. Prognosen der European Aluminium für das Jahr 2025 gehen davon aus, dass der Aluminiumanteil auf 196 kg steigen könnte.
Um die steigende Nachfrage zu befriedigen, verfügt Sandvik Coromant über ein komplettes Angebot für die Bearbeitung von Aluminium in der Automobilindustrie, von der ersten Stufe, dem Cubing, über das Schruppen, Vorschlichten und Schlichten. Jedes der insgesamt fünf Fräswerkzeuge ist darauf ausgelegt, die Qualität und die Kosten pro Teil zu optimieren. Um letzteres zu erreichen, erfüllen bestimmte Werkzeuge der Reihe eine Aufgabenkombination, wie beispielsweise das Schruppen und Schlichten in einem Arbeitsgang, um die Zykluszeiten zu reduzieren.
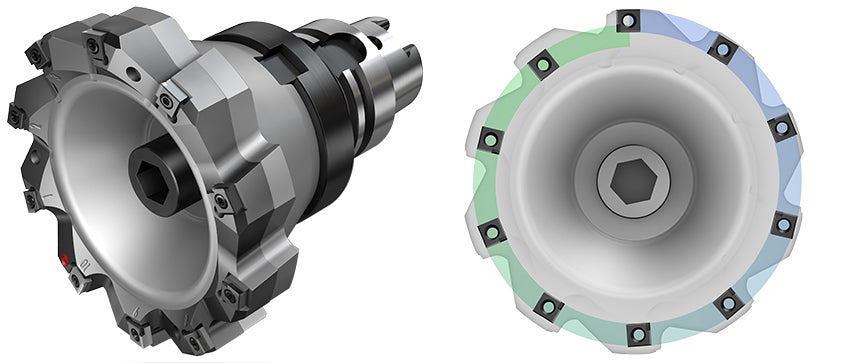
Ein Beispiel dafür ist der Planfräser M5B90 für die Feinstbearbeitung mit seiner einzigartigen axialen und radialen Positionierung der Schneidplatten. Diese Konfiguration gewährleistet zusammen mit der Wiper-Wendeschneidplatte einen gratfreien Schnitt mit hervorragender Oberflächenqualität. Dies liegt daran, dass das Modell mit einer zusätzlichen Reihe von tangential am Außendurchmesser angeordneten Wendeplatten ausgestattet ist. Damit werden höhere Vorschubgeschwindigkeiten möglich und die Bearbeitungszeit wird verkürzt.
Eine der wichtigsten Anwendungen, bei denen der M5B90 zum Einsatz kommt, ist die Herstellung von Zylinderköpfen für Pkw. Diese Bauteile sind von zentraler Bedeutung, da sie den oberen Teil des Zylinders abdichten und den Brennraum bilden. Außerdem befinden sich im Zylinderkopf der Ventiltrieb und die Zündkerzen.
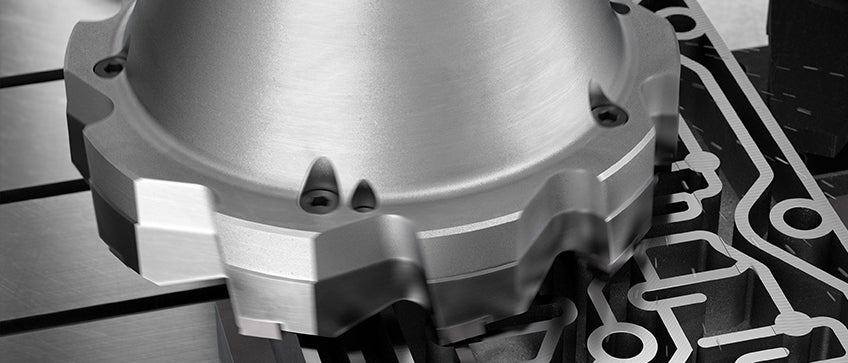
Aufgrund der Präzision des Verfahrens leiden viele Hersteller unter instabilen Prozessen, Gratbildung und einer unvorhersehbaren Standzeit der Wendeschneidplatten. Die meisten Fräser für dieses Verfahren erfordern eine laufende Einstellung der Kassette, die von Einrichtung zu Einrichtung unterschiedlich ist. Der Wechsel zum M5B90-Fräser sorgt für einen reibungslosen Schlichtvorgang mit vorhersehbarem Verschleiß ohne Gratbildung. Das Werkzeug erzeugt nur sehr dünne Späne, die während des Schneidprozesses zur Vermeidung einer Beschädigung der Bauteiloberfläche leicht entfernt werden können. Darüber hinaus kann der Wechsel zum M5B90 die Standzeit von durchschnittlich 30.000 auf 45.000 Teile verlängern.
Das Potenzial zur Verringerung der Zykluszeiten und der Kosten pro Teil bei gleichzeitiger Verbesserung der Werkzeugstandzeit und der Qualität ist beachtlich. In der Automobilindustrie, in der hohe Stückzahlen produziert werden, kann selbst eine kleine Einsparung bei der Zykluszeit zu erheblichen finanziellen Vorteilen führen. Vor diesem Hintergrund kommt jeder Technologie, die nachweislich zu größeren Einsparungen führen kann, ein hoher Stellenwert zu.