En grönare framtid för flygindustrin
Originaldelstillverkare måste se morgondagens flygplan ur ett helhetsperspektiv.
Eftersom flygindustrin står för en mycket stor del av de globala koldioxidutsläppen är den hårt pressad att tillhandahålla miljövänligare flygplan som är både lättare och kan flyga längre sträckor. Men för att lyckas med detta krävs det att man arbetar med svårbearbetad aluminium och varmhållfasta superlegeringar. Här förklarar Sébastien Jaeger, Industry Solution Manager – Aerospace hos Sandvik Coromant, hur tillverkare av originaldelar till flygindustrin kan använda sig av avancerade verktygslösningar för att bearbeta dessa krävande komponenter på ett hållbart sätt.
Enligt World Economic Forum (WEF), ”kommer man genom att uppnå nettonollutsläpp av koldioxid år 2050 inte bara hjälpa till att skapa en hållbar framtid, utan även säkerställa en finansiellt stabil och konkurrenskraftig flygindustri över lag.” Men även om e-mobilitet har blivit vardagsmat inom fordonsindustrin – och försäljningen av elfordon gick om försäljningen av dieselfordon i Storbritannien i augusti 2021 – kommer den här utvecklingen att ta längre tid inom flygindustrin.
Överlag förväntas inte elflyg användas i någon större utsträckning förrän framåt 2035. Lonely Planet rapporterar att – även om easyJet hoppas kunna använda elflyg på sträckor kortare än 500 km redan 2030 och Norge siktar på att alla kortdistansflygningar ska gå på el 2040 – ”kommer långdistansflygningar inte att göras med uppladdningsbara jumbojets än på ett tag: batterierna är helt enkelt för tunga.”
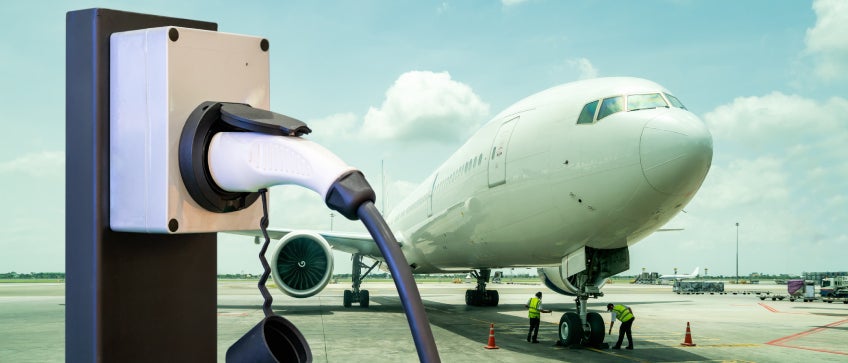
Elflyg förväntas användas i större utsträckning 2035.
Batterierna måste alltså bli lättare för att det ska vara rimligt att använda dem, men samtidigt har originaldelstillverkare ett allt större ansvar för att tillverka lättare komponenter som kan kompensera. Man kommer garanterat använda aluminium – mer specifikt nya typer av aluminium som är starkare och mer motståndskraftiga, och som har andra attribut – för att göra systemen lättare.
Vi ser också att användningen av nya varmhållfasta superlegeringar ökar. I själva verket används varmhållfasta superlegeringar redan idag i flygplanskomponenter som utsätts för stora påfrestningar, eftersom de behåller sin hårdhet även när de utsätts för extrem värme. Dessa materialegenskaper kommer att vara avgörande, eftersom ett sätt att ta sig an problemet med hållbarare flygresor är att pressa flygplansmotorerna hårdare och köra dem varmare.
Komponenter måste även tillverkas i snävare toleranser och i diverse utföranden. Precis som elbilar kommer morgondagens elflyg – inklusive flygplansskroven och motorerna – variera mer mellan tillverkarna än dagens flyg med förbränningsmotorer. När det gäller flygplansskroven experimenterar vissa originaldelstillverkare med deltaformer, integrerade vingsektioner och koncept med stagade vingstöttor. Andra originaldelstillverkare håller sig till en traditionell design med ”Stor rörformad flygkropp, vingar och motor”.
Även motorernas uppbyggnad kommer att skilja sig åt. Det kommer finnas elektrifierade, batteridrivna eller elektromagnetiska motorer, eller hybridmotorer där dagens motorer kombineras med elmotorer. Originaldelstillverkare kommer tvingas tillverka allt fler komponentvarianter i snäva toleranser och samtidigt hitta nya sätt att reducera buller, vikt och utsläpp – faktorer som alla påverkar elektriska systems prestanda. Men komponenter av aluminium och varmhållfasta superlegeringar är svåra att bearbeta, så det kommer bli en utmaning att lyckas med detta på ett hållbart och kostnadseffektivt sätt.
Snabba framsteg
Ett sätt att få fram lättare och bränsleeffektivare flygplan är att använda sig av additiva tillverkningstekniker (AM). Med AM kan man utveckla mycket avancerade, anpassade detaljer och funktionella produkter med snäva toleranser för att underlätta bearbetningen av svårbearbetade detaljer som t.ex. gitter. Enligt resultat från programvaruföretaget Dassault Systemes, ”kan en viktreducering genom AM-processer inom flygindustrin resultera i energibesparingar på upp till 25 %”, medan ”varje förlorat kilo under en flygning kan spara upp till 3 000 USD i bränslekostnader per år.”
Men är additiv tillverkning som sådan hållbar? En studie framtagen av avdelningen för produktionsteknik vid rumäniens tekniska universitet i Cluj-Napoca beskriver AM som ”ett utmärkt alternativ till traditionella tillverkningsmetoder (TM) som sprutformning, pressgjutning och bearbetning.” De skriver vidare att: ”AM har potentialen att sänka kostnaderna och vara energieffektivare än konventionella processer.”
AM kommer också avsevärt påverka inte bara hur produkterna tillverkas utan även antalet utföranden de tillverkas i. Bland fördelarna kan man se reducerade koldioxidutsläpp, mindre materialåtgång och färre transporter eftersom detaljerna kan tillverkas på plats istället för att importeras.
Tillverkare kan också producera mer avancerade, kompakta och innovativa flygplanskomponenter tack vare s.k. Rapid prototyping (snabb prototyputveckling). Rapid prototyping hänvisar till flera olika tekniker, men målet är att snabbt ta fram en konkret 3D-prototyp från en CAD-fil. Med hjälp av dessa prototyper kan man testa nya material i mindre volymer innan man påbörjar tillverkning i full skala, för att säkerställa att komponenterna håller högsta standard vad gäller innovation, kvalitet och precision.
Vi har tittat på hur originaldelstillverkare inom flygindustrin kan använda nya metoder för att tillverka mer avancerade komponenter. Men hur är det med att använda rätt verktyg för uppgiften – i synnerhet vid bearbetning av seg aluminium och varmhållfasta superlegeringar?
Dessa material kräver att man använder särskilt slitstarka verktyg med längre verktygslivslängd. Det är just därför som Sandvik Coromant tog fram sorten S205 för stålskär som används vid svarvning. S205 består bland annat av ett lager Inveio® med tätt packade kristaller i samma riktning. Detta skapar en stark, skyddande barriär runt skäret som stärker verktyget och förbättrar dess mekaniska egenskaper. Skäret har redan visat sig vara effektivt vid tillverkningen av en mängd olika flygplanskomponenter, som t.ex. turbinskivor till flygmotorer, ringar och axlar. Sandvik Coromants kunder har redan rapporterat en skärhastighetsökning med 30–50 % med S205 jämfört med konkurrenternas sorter för svarvning i varmhållfasta superlegeringar.
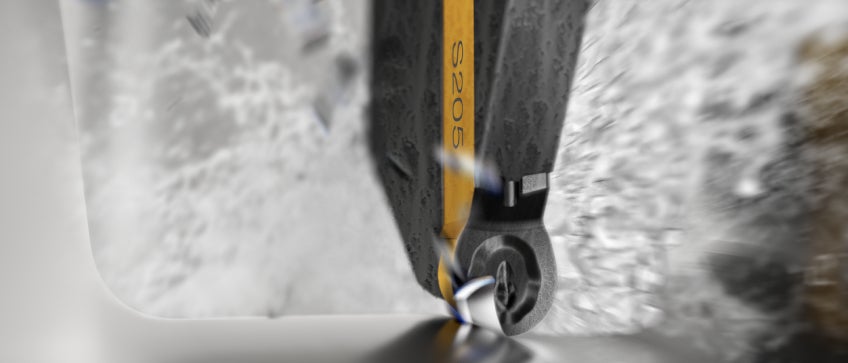
Ett helhetsperspektiv
Vi har tänkt på tillverkningsprocesserna och verktygen, men hur kombinerar vi dem på bästa sätt? När allt kommer omkring kan tid gå förlorad om man sätter ihop en helintegrerad lösning utan att systemen är kompatibla med varandra.
Här hjälper Sandvik Coromant sina kunder i flygindustrin med något som vi kallar en komponentlösning. Lösningen är indelad i flera steg. Man tittar bland annat på maskinkraven och utför tidsstudier för att undersöka kostnaden per komponent. Dessutom analyseras produktionsmetoderna vid uppstart, med hänsyn till både MTM-tidsstudier och slutanvändarprocesser. Komponentlösningen innefattar även programmering av datorstödd tillverkning (CAM) och projekthantering för både lokala och globala projekt.
Hos en av Sandvik Coromants kunder med spånbrytningsproblem i produktionen gav denna komponentlösning oss chansen att hitta orsaken till problemet och sedan ta fram en lösning. Sandvik Coromants specialister tog fram en ny strategi åt kunden med dynamic drive curves som gjorde det möjligt att hela tiden kontrollera spånbrytningen. Vi kallade denna nya metod ”Scoop turning” och har nu patent på den. Med Scoop turning lyckades kunden reducera cykeltiden med 80 %, bibehålla utmärkt spånkontroll och fördubbla verktygslivslängden.
Som om det inte var nog behövde kunden därefter bara använda en maskin istället för fyra, så att personalen slapp göra flera saker samtidigt och bearbetningsprocesserna blev säkrare – utan onödiga driftstopp. Några av nycklarna till hållbarare flygplanstillverkning kommer vara användningen av färre maskiner samt förmågan att fullborda produktionscykler med färre omriggningar, tack vare segare bearbetningssorter som S205.
Även programvaror kommer spela en viktig roll, som t.ex. CoroPlus® Tool Guide som är en del av Sandvik Coromants digitala sortiment. Kunder kan fatta viktiga beslut om valet av verktyg och skärparametrar innan de ens har påbörjat produktionen.
Cirkeln sluts
Utöver nya strategier för verktyg och nya tillverkningsmetoder kan flygindustrins originaldelstillverkare även utnyttja gammalt material. Enligt en rapport från Air Transport Action Group (ATAG) har Kaiser, det företag som förser Boeing med aluminium, implementerat ett slutet kretslopp för återvinning – ett av de största programmen av sitt slag inom industrin. Kaiser uppskattar att omkring tio miljoner kilo restmaterial och metallskrot kommer återanvändas inom industrin per år via programmet.
Sandvik Coromant har implementerat ett eget cirkulärt system för återvinning av hårdmetallverktyg där vi köper tillbaka kundernas utslitna hårdmetallverktyg och återanvänder dem vid tillverkningen av nya verktyg. Det betyder att det mesta av råmaterialet som används i Sandvik Coromants hårdmetallverktyg kommer från skrot. Vi ägnar oss åt hållbara affärer i en miljö med begränsade resurser och minskar onödigt svinn. Genom att göra detta har vi märkt att det går åt 70 % mindre energi och man släpper ut 40 % mindre koldioxid när man tillverkar verktyg av återvunna material.
Flygindustrin har allt större press på sig att tillverka miljövänligare flyg som är både lättare och kan flyga längre sträckor. Men med rätt processer och rätt verktyg – för att inte tala om att se tillverkningen ur ett helhetsperspektiv – kan flygindustrins originaldelstillverkare dra sitt strå till stacken för att ge flyget en grönare framtid.