Ett säkert sätt att bli kvitt mikrodefekter
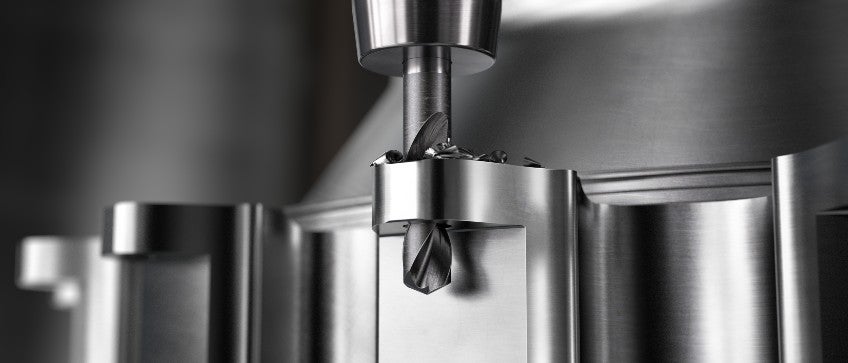
Tester med hårdmetallborr i förbättrad konstruktion öppnar nya möjligheter när det gäller hålkvalitet.
”Mät två gånger, skär en gång”, är ett vanligt uttryck inom tillverkningsbranschen, men det är lättare sagt än gjort vid bearbetning av besvärliga material. Det är därför som en ledande, global tillverkare inom flygindustrin vände sig till den globala ledaren inom skärande bearbetning när de ville göra sig kvitt hela det andra momentet i borrningsprocessen och samtidigt förbättra hålkvaliteten hos sina flygindustrikomponenter. Här berättar James Thorpe, som är Global Product Manager på Sandvik Coromant, hur konstruktionen hos ett borr ingår i helheten vid tillverkning av hål med högre kvalitet
Håltillverkning är den vanligaste av alla bearbetningsprocesser, men den är också den som oftast tas för given. Många verkstäder har haft liten anledning att ändra eller uppgradera sin befintliga riggning för håltillverkning och har använt samma verktyg och skärparametrar i åratal. Men med de oförutsägbara följderna av COVID-19 har allt detta kommit att ändras. Tillverkare har ställts inför oförutsedda och varaktiga förändringar på sina kundmarknader och behöver nu anpassa produktionen.
De flesta tillverkare undersöker till exempel nya baser och produkter att bygga försäljningen på. Verkstäder som en gång i tiden specialiserade sig på ett visst produktionsområde öppnar nu upp sina CNC-svarvar och -fräsar för en mängd sega och krävande material. Samtidigt måste tillverkare hitta nya sätt att öka vinsterna och korta ner cykeltiderna, utan att tumma på produktkvaliteten.
Det är med andra ord dags för tillverkarna att tänka nytt kring hur de gör hål.
Det vita skiktet (white layers)
Ytintegriteten hos hål är ett verkligt problem för tillverkare inom flygindustrin, eller för företag inom allmän verkstadsindustri som vill utöka verksamheten till flygindustrin. Bättre hålkvalitet är avgörande för att förhindra komponentfel, och den bestäms i stor utsträckning av vilka tillverkningsprocesser som används för att bearbeta eller finbearbeta hålen.
Verktygslösningarna och skäreggsgeometrin hos borren utvecklas oavbrutet för att uppfylla de högst ställda kvalitetskraven på tillverkning och detaljer. Användningen av skärvätska optimeras också för att minska värmeuppbyggnaden i verktyget. Vid tester har det visat sig att var och en av dessa faktorer kan styra den så kallade ”vitskiktseffekten” på materialet i arbetsstyckena.
Termen vitskikt myntades av en ledande, global tillverkare inom flygindustrin som även är kund hos Sandvik Coromant. Den avser en tunn, ultrafinkornig struktur som man kan se när man borrat i en komponent, och som orsakas av värmeutvecklingen från borret. Det vita skiktet riskerar inte bara att förändra materialets ytegenskaper, det har också bedömts som ej godtagbart inom ramarna för kundens kvalitetsstyrningsarbete.
Tillverkaren tillämpar en strikt finbearbetningsprocess för genomgående hål i flygplanskomponenter, där sådant som turbinskivor, turbinkompressorer, turbintrummor och turbinaxlar ingår. Det är därför man valt att samarbeta med Sandvik Coromant för att undersöka varför det vita skiktet bildas och hur det kan kontrolleras.
Det är viktigt att notera att testerna inte enbart motiverades av kvalitetsstyrningsskäl. På högre ledningsnivå ville man hos kunden minska den totala driftstiden och öka vinsten genom att avskaffa en hel sekundär bearbetningsprocess.
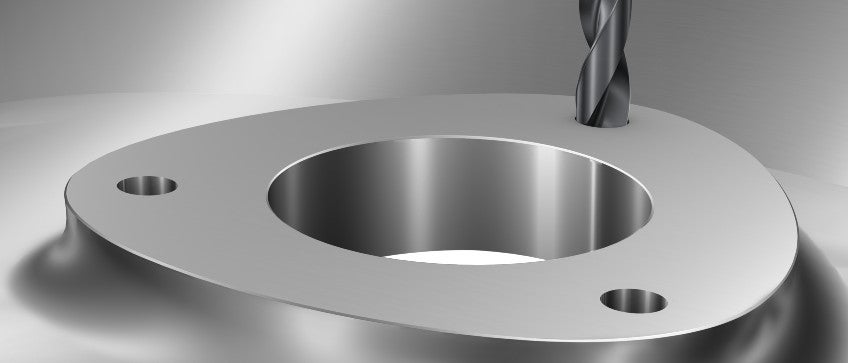
Ytintegriteten hos hål är ett verkligt problem för tillverkare inom flygindustrin, eller för företag inom allmän verkstadsindustri som utökar verksamheten till flygindustrin. Här ser vi borrning av ett hölje i varmhållfast superlegering med CoroDrill 860 med -SM-geometri
.
Andra akten
Den sekundära processen sker efter att ett hål har skapats med hårdmetallborret. Den kan innebära brotschning, dyk- eller pinnfräsning för att finbearbeta komponenten. Det sekundära processteget syftar huvudsakligen till att uppfylla kraven på ytintegritet – som att minska problem som det vita skiktet – snarare än måttnoggrannhet, med undantag för bearbetning av hål med snäv tolerans.
Ur ett övergripande kostnadsperspektiv är den sekundära processen rentav mer kostsam än att upprätthålla låga skärdata, vilket är det andra sättet att bevara ytintegriteten. Det är anledningen till att Sandvik Coromants kund ville undersöka om det gick att avskaffa processen helt och hållet. En leverantör med en produkt som tillverkar måttnoggranna hål utan någon sekundär process är i ett bra läge för att kunna sänka kostnaden per detalj avsevärt.
Undersökningen av orsakerna till, och möjliga åtgärderna mot, det vita skiktet omfattade fyra tester av borrning i det höghållfasta kromnickelmaterialet Inconel 718, ett vanligt förekommande material inom flygindustrin. Det var första gången som någon sådan undersökning hade utförts av kunden.
Vid testerna bedömdes borrning med två borr i solid hårdmetall från Sandvik Coromant, nämligen CoroDrill® R840 och CoroDrill® R846. Vart och ett av dem kördes med två olika uppsättningar skärparametrar: 58 mm/min respektive 98 mm/min, samt med varvtalet 829 varv/min respektive 757 varv/min. Skärkrafterna och vridmomentsdata mättes under hela testet, liksom tjockleken hos det vita skiktet.
Sedan dessa tester har CoroDrill R840 ersatts med CoroDrill® 860 med -GM-geometri och CoroDrill R846 har ersatts med CoroDrill® 860 med -SM-geometri. Båda dessa verktyg ur nästa generation har konstruerats för att ytterligare förbättra verktygslivslängden, utan att hålkvaliteten försämras.
Resultaten gav några värdefulla insikter i vad som orsakar tjockleken hos det vita skiktet. Värt att notera var att prepareringen av de krökta och radiellt skärande eggarna hos CoroDrill R846 gjorde att det skapades mindre vitskikt. Samtidigt verkade det som att de raka skäreggarna och fasningen av skäreggen på CoroDrill R840 hängde ihop med ökningen av skärkraften, vridmomentet och tjockleken hos vitskiktet. Borrets konstruktion avgör alltså om det går att uppnå hög hålkvalitet och mindre vitskiktsbildning utan att ge avkall på skärdata.
Testerna som den globala tillverkaren inom flygindustrin utförde tillsammans med Sandvik Coromant avslöjade inte bara några saker om det vita skiktet, utan företaget har också lyckats avskaffa en del sekundära processer, som brotschning och dykfräsning, vilket har gett tids- och kostnadsvinster. Resultaten blev också ett godkännande av konstruktionen hos Sandvik Coromants CoroDrill 860-serie med hårdmetallborr.
En bättre konstruktion
I serien ingår ovannämnda CoroDrill 860 med -GM-geometri, konstruerat för att vara ett bra allroundverktyg vid borrning i utmanande material i klasserna ISO P, M, K och H inom alla sektorer i branschen. CoroDrill 860 med -SM-geometri har optimerats för bearbetning av ISO S-sorter som varmhållfasta superlegeringar, titan och Inconel. Det senare borret har visat sig särskilt uppskattat inom flygindustrin.
Med CoroDrill 860 med -GM-geometri och CoroDrill 860 med -SM-geometri har Sandvik Coromants ingenjörer tillämpat tanken att ökad verktygslivslängd och bättre hålkvalitet i grunden beror på borrets konstruktion. CoroDrill 860 med -GM-geometri har en innovativ konstruktion med polerade spånkanaler som förbättrar spånavgången och ger en stark kärna, samtidigt som skärkrafterna vid borrning minskas.
CoroDrill 860 med -SM-geometri, å sin sida, utnyttjar en ny sort och en optimerad och förfinad spetsgeometri som ytterligare förbättrar verktygslivslängden vid arbete med svårbearbetade varmhållfasta superlegeringar. Resultatet är bättre hålkvalitet.
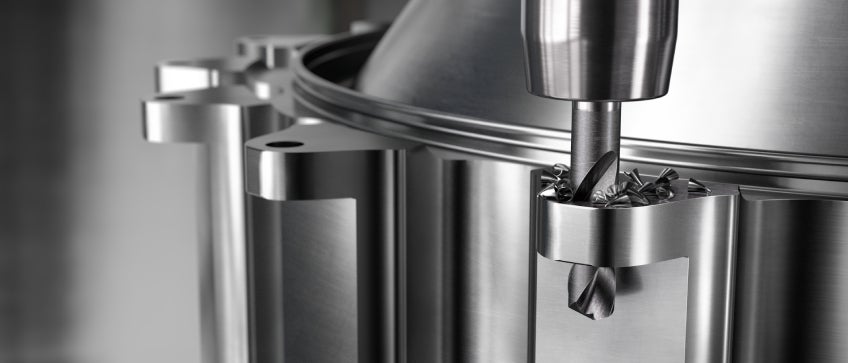
Med CoroDrill 860 med -SM-geometri beror ökad verktygslivslängd och bättre hålkvalitet i grunden på borrets konstruktion.
CoroDrill 860 har redan visat vad det går för i tester inom en rad olika sektorer före marknadslanseringen. Ett verkstadsföretag i Frankrike använde CoroDrill 860 med -GM-geometri på konstruktionsstål AISI 4140. Det lyckades producera hål med hög kvalitet vid både konkav och konvex ingång av borret, med bra rakhet och tolerans. Företaget har sedan dess etablerat en ny affärsrelation med Sandvik Coromant.
En annan av Sandvik Coromants kunder, en italiensk tillverkare inom allmän verkstadsindustri, lyckade uppnå en produktivitetsökning med mer än 45 % jämfört med borret från en konkurrent när man använde CoroDrill 860 med -GM-geometri för att bearbeta den starka stållegeringen 34CrNiMo6. Det uppnådde dessutom 100 % högre verktygslivslängd. På annat håll har CoroDrill 860 med -SM-geometri gett imponerande resultat vid bearbetning av Inconel 718. Särskilt lyckades man vid en testning i Katowice i Polen förbättra verktygslivslängden med 180 % med CoroDrill 860 med -SM-geometri jämfört med CoroDrill R840.
Oavsett sektor – flygindustri, allmän verkstadsindustri eller andra områden – går det att uppnå höga verktygsprestanda om borret har konstruerats på rätt sätt för uppgiften. Samtidigt kan onlineverktyg som Sandvik Coromants CoroPlus® Tool Guide ge ytterligare stöd. Genom att öppna verktyget via en webbläsare och ange önskat material i arbetsstycket, håldiameter och djup kan användaren hitta lämpligaste solida hårdmetallverktyg och skärdata för sina behov.
Även om man ännu inte fullt ut kan borra enligt devisen ”mät två gånger och skär en gång”, så kan funktionen hos CoroDrill 860 med -GM-geometri och CoroDrill 860 med -SM-geometri hjälpa tillverkare att tänka på nya sätt kring att göra hål.