Torneado de materiales exóticos
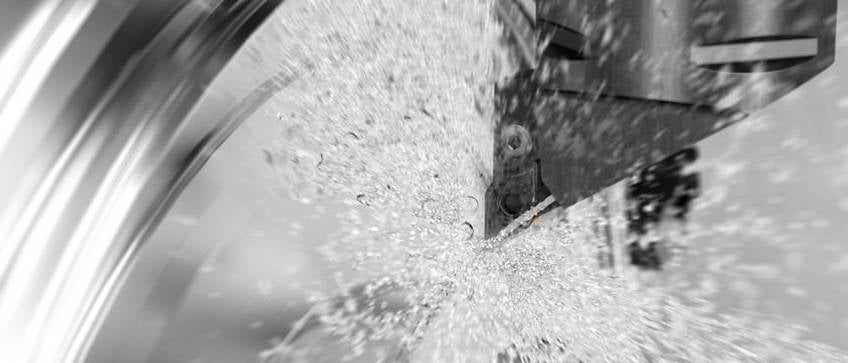
Las aleaciones de titanio y las superaleaciones termorresistentes (HRSA, por sus siglas en inglés) plantean dificultades de mecanizado. Son distintas de cualquier otro metal, por lo que se consideran exóticas. Presentan propiedades extraordinarias, como la relación resistencia-peso, la conservación de la fuerza y la dureza a altas temperaturas, así como una excelente resistencia a la corrosión.
Sin embargo, al ser unos materiales difíciles de mecanizar, requieren también soluciones "exóticas". Dichas soluciones deben ser planeadas minuciosamente, con herramientas específicas y métodos y recorridos de herramienta cuidadosamente escogidos, para poder conseguir eficiencia, seguridad y excelentes resultados.
Este documento de información general examina los requisitos de mecanizado y los avances que han mejorado el rendimiento y la seguridad de los procesos de torneado.
Unas propiedades de componentes extraordinarias, pero con dificultades de mecanizado
La capacidad de mecanizar el material de un componente está condicionada por diversos factores que determinan e influyen sobre los requisitos y los resultados en las operaciones de corte de metales. En un sentido muy amplio, se trata de la capacidad para cortar el material del componente en relación con la tendencia al desgaste de la herramienta y con la generación de virutas. La diferencia que plantean estos materiales exóticos en la gran mayoría de escalas radica en su escasa maquinabilidad. Su corte se considera complicado, pero no es tan difícil si se aborda con un enfoque apropiado.
Los materiales de componentes más exóticos de uso relativamente común se clasifican en el grupo ISO S: HRSA y aleaciones de titanio. Para su mecanizado, estos materiales se dividen en subgrupos en función de su composición, su estado y sus propiedades. La naturaleza química y la composición metalúrgica de una aleación de clasificación S determinan las propiedades físicas y, en consecuencia, la maquinabilidad. El control de virutas suele ser un factor exigente debido a la segmentación de las virutas y no es extraño que se requiera una fuerza de corte específica que duplique a la del acero; este parámetro expresa la dificultad de cortar un material, por lo que determina la fuerza y la potencia necesarias para efectuar el corte.
El principal motivo que explica la dificultad de cortar los materiales fabricados con HRSA es que estos mantienen una alta resistencia incluso a temperaturas elevadas; no se suavizan ni fluyen como lo hacen otros materiales y se endurecen fácilmente durante el trabajo. En el filo de corte se concentran altas temperaturas y una alta carga mecánica. Las aleaciones con base de níquel, hierro o cobalto son subgrupos de HRSA con capacidades únicas para su uso en componentes, principalmente en las industrias aeroespacial, energética y médica, ya que sus interesantes propiedades apenas se alteran hasta que se alcanza el punto de fusión. Además, son muy resistentes a la corrosión. Sin embargo, desde el punto de vista del mecanizado, requieren una máquina a la altura, condiciones de reglaje estrictas, calidades y geometrías específicas para las plaquitas y una aplicación optimizada de refrigerante, sin olvidar un enfoque apropiado respecto al método de mecanizado y las herramientas. Evidentemente, todo esto requiere una mayor planificación y, por consiguiente, más trabajo en las primeras líneas de fabricación.
Las aleaciones de titanio también se dividen en subgrupos con distintos grados de maquinabilidad. Por lo general, la maquinabilidad se clasifica en diferentes grados (tenacidad), lo que implica unos requisitos muy específicos en cuanto a herramientas y métodos. Los requisitos vienen determinados por la baja conductividad térmica, la alta resistencia a las temperaturas elevadas, las virutas finas y muy recortadas con tendencia a la corrosión por rozamiento, que crean una zona de contacto estrecha con la cara de desprendimiento de la plaquita, y las intensas fuerzas de corte que se concentran en las proximidades del filo de corte. Las virutas pueden ser de formación cíclica, lo que se traduce en unas fuerzas de corte variables, y algunas aleaciones constan de una gran cantidad de metal duro, por lo que el material es extremadamente abrasivo. Las velocidades de corte excesivas pueden causar una reacción química entre las virutas y el material de la herramienta, lo que, a su vez, puede provocar una rotura o un astillamiento repentino de los filos de corte, o el empastamiento o incluso la soldadura de materiales en ellos. Además, algunas aleaciones se endurecen rápidamente durante los trabajos, lo que provoca desgaste por difusión y, por consiguiente, una formación excesiva de rebabas que puede dificultar las operaciones subsiguientes.
No cabe duda de que son materiales exóticos; la ventana para mecanizar con éxito muchas HRSA y aleaciones de titanio es extremadamente reducida.
Al tornear estos materiales...
...el buen resultado depende del equilibrio del efecto combinado del material y los factores de aplicación. Existen algunas reglas de oro básicas que contribuyen en gran medida a la obtención de buenos resultados:
- planificación previa de una estrategia de mecanizado sólida y tan detallada como sea posible;
- definición del mejor enfoque para las herramientas;
- definición de los mejores recorridos de herramienta y uso de una sujeción de la herramienta muy estable;
- uso de las mejores tecnologías de vanguardia específicas para herramientas de corte;
- aplicación de datos de corte cualificados para determinar la seguridad del proceso y la productividad;
- uso del cálculo de longitud de corte en espiral para predecir los cortes;
- aplicación correcta del refrigerante con soluciones modernas de alta presión;
- uso de recomendaciones y apoyo de especialistas.
El proceso de mecanizado debe estar siempre cuidadosamente planificado, a causa de los factores críticos y decisivos implicados, como la consideración de las condiciones y el estado del material de la pieza. Fundición, forja, barra de material en bruto, tratamiento térmico, tratamiento en solución y envejecimiento son todos ellos métodos que afectan notablemente a la pieza, por lo que es necesario tenerlos en cuenta al seleccionar las herramientas y los métodos. Las condiciones superficiales de la pieza varían y afectan al mecanizado, como también lo hace la dureza. Además, la estrategia de torneado debe tener en cuenta los requisitos derivados de las características de diseño del componente que se desea mecanizar, así como las diversas etapas del mecanizado en términos de desbaste (primera etapa), semiacabado (etapa intermedia) y acabado (etapa final). Los problemas más comunes incluyen la complejidad de las características y la integridad superficial.
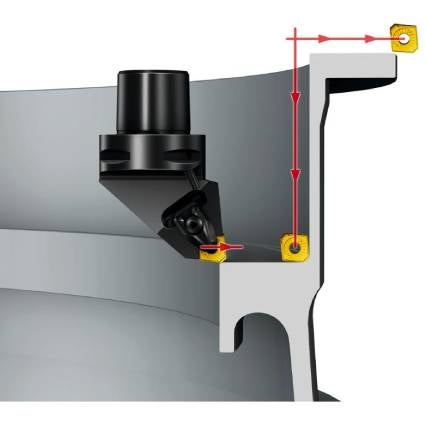
El diseño de los componentes, los materiales y su estado conforman la base de la planificación del torneado de materiales exóticos. Si procede, vale la pena definir cómo deben desarrollarse las etapas primera, intermedia y última del proceso de mecanizado, también en relación con el estado del material y los requisitos de calidad. La planificación de los recorridos de las herramientas y la reducción del avance en la programación pueden determinar el alcance del desgaste, el tipo de herramienta, los tiempos de ciclo y la seguridad.
La acción de corte en estos materiales...
...se ve afectada en gran medida por la aproximación del filo de corte a la pieza. El ángulo de posición del filo de corte, combinado con la geometría de la plaquita, resulta esencial de cara al rendimiento, la duración de la herramienta, la seguridad y los resultados. Las formas de las plaquitas deben elegirse en relación con el corte que se deba realizar. Sin embargo, en cada aplicación siempre se debe tener en cuenta que un ángulo de posición pequeño contribuye al rendimiento y a la vida útil de la herramienta.
La elección de la calidad de la plaquita se debe realizar en función del tamaño del ángulo de posición. Entre otras cosas, el ángulo de posición influye sobre el tipo de desgaste que genera entallas en el filo, cuyo tamaño afecta al resultado y causa un fallo prematuro de la herramienta. Si se consigue una aproximación correcta para la aplicación, es posible seleccionar una calidad de plaquita que ofrezca una mayor productividad, lo que contribuye también a una vida útil más larga y a una mayor seguridad.

El ángulo de posición de la herramienta de corte afecta al espesor de viruta, la velocidad de avance, las fuerzas de corte y el tipo de cortes que se pueden realizar. Al utilizar materiales exóticos, la elección del ángulo tiene consecuencias directas de cara a la productividad y la fiabilidad de los procesos, lo que influye en la forma de la plaquita y en el radio de punta, así como en la idoneidad de uso del material de la herramienta. Las plaquitas redondas y de tipo Xcel suelen ser las mejores opciones.
La elección del material de la herramienta (calidad de la plaquita) debe fundamentarse en el tipo de operación de torneado que se vaya a realizar (desbaste, semiacabado o acabado) y también en el estado de la pieza y el tipo de corte. Dada la dureza de estos materiales, la deformación plástica del filo de corte debe considerarse siempre como el principal factor de riesgo a la hora de seleccionar la calidad de la plaquita (como se ha mencionado, el desgaste en entalla está influido principalmente por el ángulo de posición y el ángulo de posición). La selección de la calidad de la plaquita debe ir siempre asociada a la forma de la plaquita, que constituye un factor de fuerza que debe valorarse en términos de aproximación, carga de virutas y de si el corte es continuo o intermitente. Así pues, los grados de calidad específicos son imprescindibles para el mecanizado de HRSA.
Los requisitos principales son un elevado grado de resistencia al calor de la plaquita, el nivel apropiado de dureza de esta y una adhesión suficiente de su revestimiento. Una geometría de corte positiva, un filo de corte agudo y resistente, y un rompevirutas relativamente abierto son las características que debe tener la plaquita intercambiable para estos materiales.
Igual de esencial para el éxito con estos materiales es la definición de los datos de corte más apropiados. La velocidad de corte depende de la combinación de velocidad, avance y profundidad de corte, y se puede optimizar para lograr unos altos niveles de productividad, seguridad y calidad. La velocidad de corte está vinculada a la generación de calor y a cómo esta afecta a la plaquita; debe ser lo bastante elevada como para que la viruta alcance una plasticidad suficiente, pero no en exceso, para que no se desequilibre el material de la herramienta. Por lo general, las velocidades están comprendidas en rangos de 130 a 260 pies por minuto (40-80 m/min) con plaquitas específicas de metal duro y de 490 a 1310 pies por minuto (150-400 m/min) con plaquitas de cerámica.
La velocidad de avance es el factor principal que afecta al tiempo de corte y al espesor de viruta. En los materiales exóticos, es preciso equilibrarla con más cuidado, porque los límites son relativamente estrictos: en la etapa de desbaste, la viruta debe maximizarse, pero sin llegar a sobrecargar el borde; en cambio, en el acabado, la viruta debe ser lo bastante gruesa como para evitar niveles excesivos de calor y templado de la pieza.
La profundidad de corte suele afectar a la aproximación del eje, por lo que debe mantenerse por debajo de un valor determinado. Por ejemplo, al utilizar plaquitas redondas en HRSA, la profundidad de corte no debe superar el 15 % del diámetro de la plaquita. La profundidad de corte también debe programarse minuciosamente durante el perfilado. Se emplean recesos o escuadras para no exceder el arco apropiado de empañamiento del filo de corte.
En lo que respecta a la vida útil de la herramienta, es importante trabajar de forma intensiva con la longitud de corte en espiral (SCL). La definición correcta de este parámetro permite predecir y programar las paradas de la máquina para el intercambio de plaquitas, y también que las pasadas con una herramienta utilizada a la velocidad correcta se puedan completar sin que el filo de corte pierda la capacidad de mantener la calidad superficial requerida.
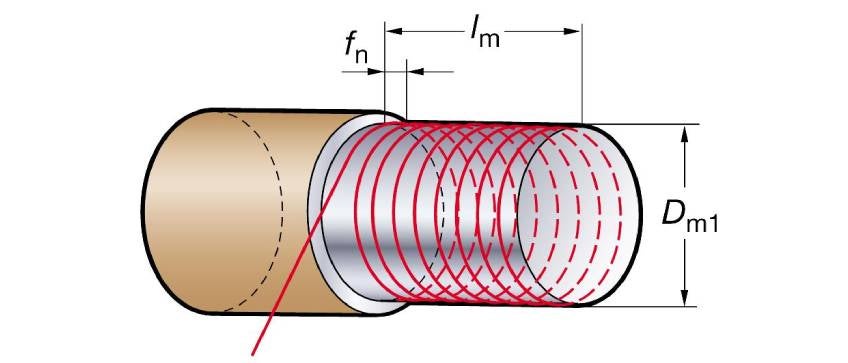
El uso de cálculos de longitud de corte en espiral puede ayudar a predecir el tiempo o la longitud del corte para reducir el tiempo de mecanizado y mejorar el acabado superficial en materiales exóticos de difícil mecanizado. Las paradas de la máquina para el cambio de plaquitas se planifican con la longitud de corte en espiral para adaptarse mejor a la operación y a los datos de corte y, así, optimizar la vida útil de la herramienta y la utilización de la máquina.
El desgaste de la herramienta se ve afectado en gran medida…
…por las elevadas fuerzas de corte en combinación con las altas temperaturas del filo de corte, lo que implica una tendencia al desarrollo de ciertos tipos de desgaste del filo de corte. Los más importantes son el ya mencionado desgaste en entalla (el tipo de desgaste mecánico en el punto en que la profundidad de corte incide en la línea del material de la pieza), la deformación plástica del filo de corte (como consecuencia de la combinación de temperaturas y presiones elevadas) y, finalmente, el desgaste abrasivo provocado principalmente por los materiales de mayor dureza. Otro tipo de desgaste es el de corte superior, que se desarrolla en las plaquitas cerámicas al desprenderse capas de la parte superior del filo de corte. La aproximación del filo de corte desempeña un papel fundamental.
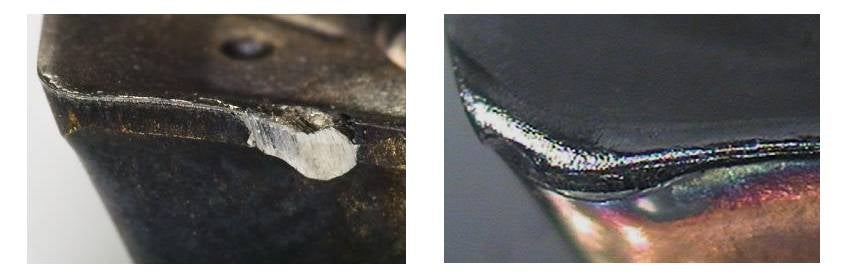
Al trabajar con materiales exóticos, la selección de la calidad de la plaquita no tiene un efecto tan directo en el desbaste y el acabado como con otros materiales. En este caso, la selección de la calidad es más bien un factor de optimización, con una complejidad ligeramente mayor, que depende de la forma de la plaquita, de la aproximación del filo de corte y del tipo de operación. Es preciso contener los patrones de desgaste destructivo, como el desgaste en entalla y la deformación plástica que se explicaron anteriormente, por medio de una combinación de herramientas, datos de corte y métodos apropiados. Las plaquitas de metal duro, junto con la cerámica de SiAlON y, hasta cierto punto, la cerámica con filamentos, suelen ser la opción más apropiada y de aplicación más generalizada.
El ángulo de posición más apropiado para el torneado de materiales exóticos es un ángulo reducido, de no más de 45 grados. La condición más desfavorable se produce cuando el estado es de 90/0 grados, o cuando la profundidad de corte es más larga que el radio de punta de la plaquita. Un ángulo grande/pequeño se traduce en virutas finas y un mayor avance.
Para el torneado de HRSA, el ángulo de posición de la herramienta determina si es más apropiada una plaquita con recubrimiento de PVD o de CVD. El objetivo es proteger contra los efectos térmicos. El recubrimiento de PVD (por deposición física en fase de vapor) es apropiado para un ángulo de posición de 90/0 grados, mientras que el recubrimiento de CVD (por deposición química en fase de vapor) es apropiado para un ángulo de 45 grados. En cambio, las plaquitas con recubrimiento no son especialmente ventajosas para el torneado de titanio; en este caso, es más importante garantizar la condición del filo de corte más apropiada, como puede ser el uso de plaquitas redondas en la etapa de acabado. Las nuevas familias de recubrimientos de PVD ofrecen elevados niveles de dureza y una excelente resistencia ante la deformación del filo y los choques térmicos. En combinación con bordes afilados, destacan también en las operaciones con materiales propensos al empastamiento, desde el desbaste hasta el acabado.
Una forma de plaquita correcta...
…es un importante factor de aplicación al mecanizar estos materiales. La forma redonda (R) es una de las más recomendadas para estos materiales. La plaquita redonda ofrece fuerza para un filo de corte positivo y agudo, un espesor de viruta que varía a lo largo de un filo de corte largo, lo que permite alcanzar altas velocidades de avance, y un gran radio de plaquita que no restringe la velocidad de avance gracias al acabado superficial que se genera. Además, la plaquita redonda aporta flexibilidad a la programación para realizar las operaciones de perfilado y formación de cavidades necesarias para muchas formas de componentes.
En algunos casos, una plaquita cuadrada (en forma de S) puede ser la más apropiada para el mecanizado en primera etapa, gracias a su capacidad de realizar cortes de desbaste en varias direcciones con un ángulo de 45 grados. La plaquita romboide (en forma de C) destaca por su flexibilidad en cuanto a los recorridos de herramienta; al ampliarse para su transformación en plaquita de tipo Xcel, ofrece una accesibilidad a las herramientas aún mayor para penetrar en esquinas, recesos y escuadras. Esta combinación de forma de plaquita y ángulo de posición de 45 grados también reduce las fuerzas de corte radial, lo que propicia un espesor de viruta constante y reduce el desgaste en entalla. El resultado es una mayor productividad, una vida útil de la herramienta más duradera y una seguridad mejorada.
La optimización del programa...
...es de gran importancia, por lo que, a continuación, se indican algunas recomendaciones encaminadas a mejorar el rendimiento, especialmente al utilizar plaquitas redondas, que son, en principio, las apropiadas para los materiales exóticos:
- evitar el avance axial en los cortes y suavizar los impactos; si es necesario realizar este tipo de cortes, reducir la velocidad de avance a la mitad;
- al tornear en escuadra, el avance debe también reducirse a la mitad, o deberá llevarse la herramienta a la escuadra en la que el radio programado sea idéntico al diámetro de la plaquita. (Se recomienda que el radio mínimo programado sea de aproximadamente el 25 % del diámetro de la plaquita, y el radio del componente, un 75 % del diámetro de la plaquita. El avance centrado en la herramienta es para el radio programado);
- para tareas de desbaste con plaquitas redondas, permitir que el radio programado equivalga al diámetro de la plaquita, y en tareas de acabado, asegurarse de que el radio programado sea mayor que el diámetro de la plaquita;
- plantear recorridos de herramienta alternativos, múltiples pasadas y un mecanizado en ambas direcciones para utilizar las plaquitas completamente;
- proteger las plaquitas de cerámica con un achaflanado previo de la pieza y avanzar por el chaflán;
- mantener un equilibrio adecuado del ángulo de posición con respecto al arco de empañamiento de la plaquita durante el mecanizado. La limitación del ángulo es esencial para un buen rendimiento, y el uso de las plaquitas redondas constituye un importante elemento adicional para desplegar todo el potencial disponible con las calidades de plaquitas actuales;
- evitar los efectos envolventes al perfilar o ranurar para no sobrecargar la plaquita, utilizar recorridos de herramienta alternativos o diámetros de plaquitas más pequeños;
- plantear un torneado trocoidal, la rotura del corte en cortes más pequeños y adecuados, especialmente en trabajos de formación de cavidades.
¿Qué se debe tener en cuenta en relación con los tipos de herramientas y los métodos de mecanizado de aleaciones de titanio y HRSA? A continuación, se explican algunas nociones básicas.
- Siempre se debe contar con refrigerante de precisión. Los chorros de precisión que inciden en el filo de corte y por detrás del mismo, generados por herramientas con canalización interna de refrigerante, aportan muchas posibles ventajas para las operaciones de torneado, fresado y taladrado. Se puede aplicar una tecnología de boquillas de última generación, disponible como elemento estándar y como solución de ingeniería con diversos rangos de presión, a todos los tipos de máquinas que cuenten con un suministro de refrigerante adecuado. Las inversiones en nuevas máquinas deben procurar siempre que exista la posibilidad de aplicar una presión de refrigerante de 70 bar en operaciones de torneado de titanio para facilitar una mejor rotura de viruta; sin embargo, la posibilidad de aplicar presiones de hasta 200 bar plantea ventajas para el torneado de HRSA, en los que los procesos de rotura de viruta son de mayor dureza.
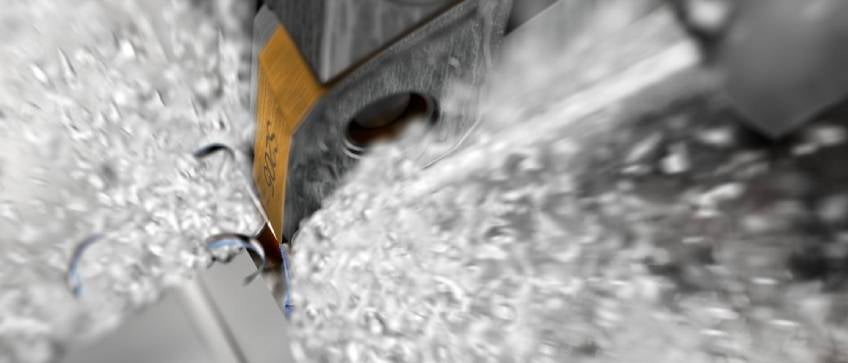
El uso de refrigerante es un factor decisivo de aplicación al mecanizar materiales exóticos. La aplicación de refrigerante de precisión es, en la actualidad, una tecnología de vanguardia disponible como opción estándar o solución técnica, y es lo suficientemente eficaz como para marcar una diferencia notable en términos de corte, formación de viruta, vida útil de las herramientas y productividad. Por lo general, las altas temperaturas generadas en estos materiales imponen la necesidad de un efecto de refrigeración; sin embargo, si el refrigerante se aplica en gran cantidad, a altas presiones y dirigido con precisión, en combinación con plaquitas específicas y un suministro canalizado a través de las herramientas, es posible optimizar notablemente el rendimiento y los resultados.
- La accesibilidad suele plantear dificultades a la hora de tornear materiales exóticos. Las características complejas y los voladizos de las herramientas obligan a acertar con las herramientas y los métodos adecuados. Es recomendable apostar por sistemas modulares, con un concepto fiable de aproximación de los filos de corte de las herramientas ante distintos ángulos y voladizos. La gama de opciones de adaptadores y de lamas debería ofrecer suficiente flexibilidad para, a partir de un inventario de herramientas estándar y limitado, construir prácticamente cualquier herramienta adecuada para las distintas configuraciones y que garantice la accesibilidad a espacios confinados interiores o exteriores. Las lamas deben respetar las distancias radiales y axiales requeridas para adentrarse en surcos en ángulo y suministrar además refrigerante de precisión al filo de corte a través de la herramienta.
- El material de la herramienta es el corazón de cualquier operación de mecanizado; en el caso de los materiales exóticos, constituye un factor decisivo. Este ámbito requiere calidades de plaquitas específicas, combinadas con una geometría de plaquita apropiada, por lo general fabricada con metal duro o cerámica de última generación. Los grados de metal duro sin recubrimiento siguen ocupando una posición destacada, pero los últimos avances en tecnología de recubrimiento de plaquitas han propiciado la aparición de plaquitas de metal duro con revestimiento, que han supuesto un revulsivo desde el punto de vista de las capacidades de los filos de corte, con una reducción del tiempo de corte y una prolongación de la vida útil.
- Deben también incluirse funciones de amortiguación integradas en las barras de mandrinado, lamas e incluso cuchillas de fresado para minimizar la tendencia a la vibración. La tecnología antivibración ha avanzado considerablemente y debe convertirse en una opción por defecto en aquellos casos en que los voladizos de las herramientas tiendan especialmente a generar un efecto de inestabilidad. La productividad, la seguridad de los procesos y la calidad de los componentes son factores directamente vinculados a la calidad y a la disponibilidad de las herramientas antivibratorias. Sin esta característica, son varias las operaciones que no se pueden realizar: en la actualidad, es posible efectuar con gran eficiencia y un acabado excelente operaciones de torneado interno con voladizos de diámetros hasta catorce veces mayores (hasta 250 mm).