Axialeinstechen
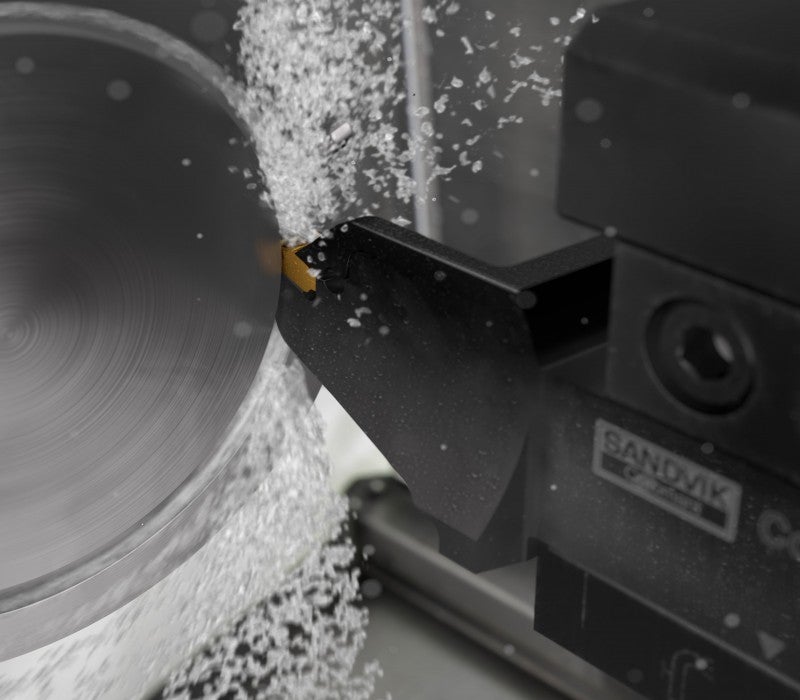
Beim Axialeinstechen ist die Wahl der richtigen Werkzeuge besonders wichtig. Die Werkzeughalterform muss dabei auf den Nutenradius abgestimmt und deshalb gebogen sein. Aufgrund der gebogenen Nut stellt die Spanabfuhr beim Axialeinstechen häufig ein Problem dar. In der Nut festgeklemmte Späne können zu Wendeplattenbruch führen und die Prozesssicherheit gefährden.
Auswahl des korrekten Werkzeugs zum Axialeinstechen
Durchmesserbereich (DAXIN und DAXX)
Wählen Sie den Durchmesserbereich des ersten Einstichs (DAXIN und DAXX) Nehmen Sie das Werkzeug für den größten Durchmesser, der zu Ihrer Nut passt. Ein Werkzeug für größere Durchmesser hat eine geringere Krümmung und verfügt daher über eine höhere Stabilität und Steifigkeit. Darüber hinaus bietet es eine verbesserte Spankontrolle.
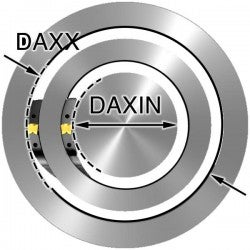
Einstechtiefe (CDX)
Immer ein Werkzeug mit der kleinstmöglichen Einstechtiefe einsetzen (CDX), um maximale Stabilität zu erzielen.
Wendeschneidplattenbreite [CW]
Nehmen Sie die Wendeschneidplatte und das Werkzeug für den größten Durchmesser, der zu Ihrer Nut passt. Ein breiterer Halter verfügt über höhere Steifigkeit und bietet mehr Stabilität.
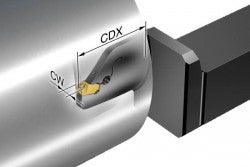
Werkzeugausführung und -form
Korrektes Werkzeug wählen – Form A oder B, Rechts- oder Linksausführung – je nach Maschinenaufspannung und Drehrichtung des Werkstücks.
- Form A = Für die Innenbearbeitung
- Form B = Zum Axialeinstechen an Zapfen/Wellenstümpfen (Störkonturen)
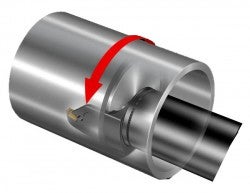
Form A
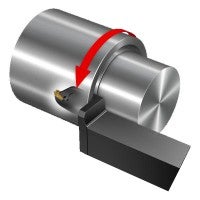
Form B
Suchen Sie Werkzeugempfehlungen?
Hier finden Sie unsere Zerspanungswerkzeuge chevron_right
Brauchen Sie Beratung?
Stellen Sie uns eine Frage chevron_right
Was es sonst noch über die Grundlagen unserer Metallzerspanung zu lernen gibt?
Registrieren Sie sich für unser kostenloses E-Learning Programm chevron_right
Empfohlene Werkzeughalter
Bei der Wahl des korrekten Halters ist je nach Axialeinstechoperation Folgendes zu beachten:
- Wahl der Maschinenschnittstelle. Auswahl zwischen modularer oder einteiliger Lösung, wie QS-Schaft
- 0°oder 90° Halter
- Werkzeug in Rechts- oder Linksausführung. Dies ist abhängig von Ihrer bisherigen Wahl
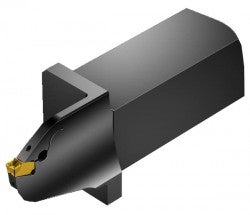
0° Halter
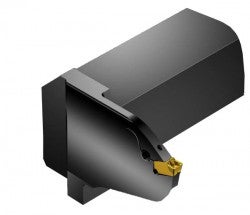
90° Halter
Rechts- oder Linksausführung?
Überlegen Sie ob Sie, abhängig von Ihrer bisherigen Wahl, ein Werkzeug in Rechts- oder Linksausführung benötigen.
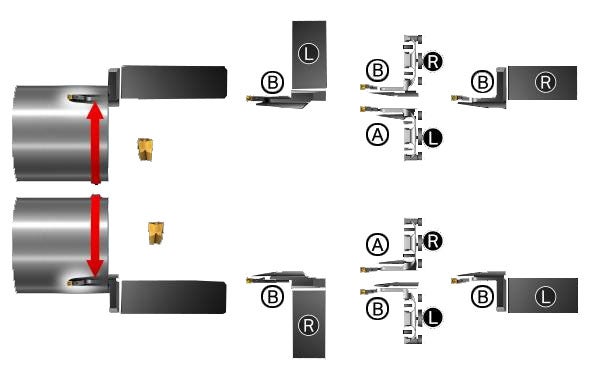
Zur Erzielung bester Ergebnisse beim Axialeinstechen wird ein speziell für diese Operation entwickeltes System empfohlen, z. B. CoroCut QF. Für weitere Unterstützung bei der Wahl des richtigen Werkzeugs zum Axialeinstechen, besuchen Sie die spezielle Produktseite oder nutzen Sie den CoroPlus® ToolGuide
Tailor-Made-Werkzeuge
Alle Standardwerkzeuge zum Axialeinstechen decken einen Durchmesserbereich für den ersten Einstich ab. Um ein für die zu bearbeitende Nut optimiertes Werkzeug zu erhalten, besteht die Option, in einen Werkzeughalter aus dem Tailor-Made-Programm zu investieren. Alle Standardwerkzeuge zum Axialeinstechen decken einen Durchmesserbereich für den ersten Einstich ab. (siehe Abbildung). Tailor-Made-Werkzeuge lassen sich auf die Stechtiefe und den Durchmesserbereich für den ersten Einstich exakt abgestimmt und sind daher die optimale Lösung zum Axialeinstechen.
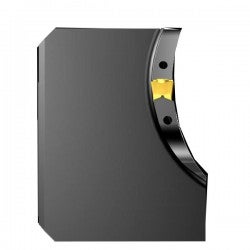
Standard-Werkzeughalter
Höhere Werkzeugstabilität
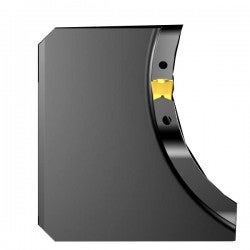
Tailor-Made-Halter
Suchen Sie Werkzeugempfehlungen?
Hier finden Sie unsere Zerspanungswerkzeuge chevron_right
Brauchen Sie Beratung?
Stellen Sie uns eine Frage chevron_right
Was es sonst noch über die Grundlagen unserer Metallzerspanung zu lernen gibt?
Registrieren Sie sich für unser kostenloses E-Learning Programm chevron_right
Auswahl des korrekten Werkzeugs zum Axialeinstechen beim Aufbohren
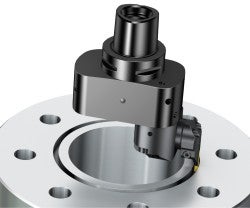
Um eine axiale Nut in einem Werkstück herzustellen, muss der richtige Werkzeughalter für die Wendeschneidplatte gewählt werden. Das Axialstechwerkzeug wird immer von größten Stechdurchmesser des Bauteils festgelegt, um eine maximale Stabilität im Werkzeug zu haben. Die Spankontrolle ist beim Axialeinstechen wichtig; der Span sollte lang genug sein, um nicht in der Nut stecken zu bleiben, aber kurz genug, um sich nicht um das Werkzeug oder Werkstück zu wickeln.
Axialeinstechanwendungen
Strategien
Schruppen
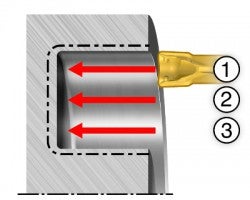
Beginnen Sie stets mit dem größten Durchmesser und arbeiten Sie nach innen. Bei diesem Schritt ist ein kontinuierlicher Span erforderlich, um ein Festklemmen des Spans in der Nut zu vermeiden. Wählen Sie Vorschubunterbrechung oder Mikro-Stopps, wenn Sie kürzere Späne benötigen. Die weiteren Schnitte (2, 3) sollten das 0,5- 0.8-fache der Wendeschneidplattenbreite betragen. Da die Späne bei dieser Bearbeitung leichter abzuführen sind, kann der Vorschub um 30‒50% erhöht werden. Bei diesen Schritten erhalten Sie in der Regel kürzere Späne.
Tiefe Nuten
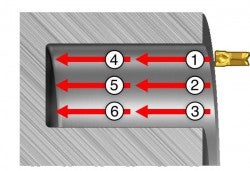
Bei tiefen Nuten (>25 mm (0.984 Zoll)) wird die Bearbeitung in zwei Schritten empfohlen:
- Bearbeiten Sie die Nut mit 50% der erforderlichen Einstechtiefe und Breite (1, 2, 3)
- Bearbeiten Sie bis zu der erforderlichen Einstechtiefe (4, 5, 6)
Schruppen mit Längsdrehen
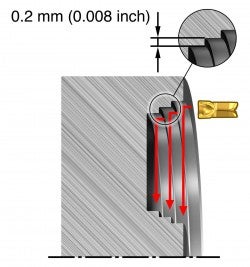
p
Längsdrehen bietet bessere Spankontrolle und Spanbruch. Beginnen Sie mit dem größten Durchmesser und bearbeiten Sie zum Zentrum hin. Stellen Sie nicht zur und gegen die Schulter zu, lassen Sie Stufen von 0.2 mm (0.008 Zoll) zwischen den Durchgängen. Längsdrehen bietet einen stabileren Prozess als der Schnitt mit axialem Vorschub. Setzen Sie Längsdrehen ein, um Vibrationen zu vermeiden. Denken Sie daran, dass das Längsdrehen wegen der geringeren Schnitttiefe (a) weniger produktiv ist als axiale Schnitte
Schlichten
Der Erhalt guter Spankontrolle beim Schlichten ist stets schwierig, insbesondere bei der Bearbeitung von Auskehlungen. Es ist wichtig, dass die Zerspanung des abzutragenden Materials in drei Durchgängen erfolgt.
- Führen Sie den ersten axialen Schnitt nah am Eckenradius am größten Durchmesser durch
- Beginnen Sie den zweiten Schnitt am größten Durchmesser und arbeiten Sie bis zum Eckenradius am Innendurchmesser
- Beim dritten Schnitt werden der Innendurchmesser und der Eckenradius geschlichtet
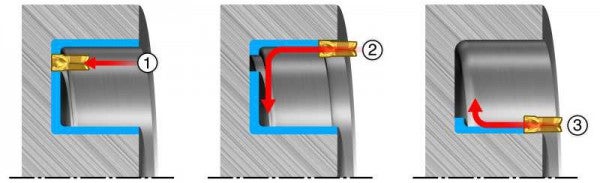
Zielgerichtete Kühlschmierstoffzufuhr
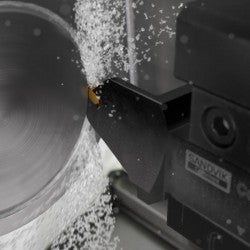
Verwenden Sie Werkzeuge zum Axialeinstechen mit Präzisions-Kühlschmierstoffzufuhr, auch wenn der max. Kühlschmierstoffdruck Ihrer Maschine niedrig ist (7‒10 102-145 bar)). Zielgerichtete Kühlschmierstoffzufuhr verbessert die Spanabfuhr und verringert das Risiko von Spanklemmen in der Nut, insbesondere bei tiefen Nuten. Stets höchstmöglichen Kühlschmierstoffdruck bis zu 80 bar (1160 PSI) zur Verbesserung der Spankontrolle und -abfuhr verwenden.