Fehlerbehebung beim Drehen
Spankontrolle
Lange, ungebrochene Späne wickeln sich um das Werkzeug oder Werkstück. Ursache ist normalerweise niedriger Vorschub sowie niedrige und/oder flache Schnitte.
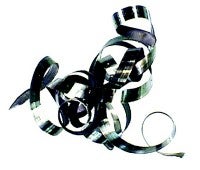
Ursache | Lösung |
|
|
|
|
|
|
|
|
Spankontrolle
Sehr kurze, oft aneinander haftende Späne durch einen zu harten Spanbruch.
Harter Spanbruch führt häufig zu verminderter Standzeit oder sogar Wendeplattenbruch aufgrundzu hoher Spanlast an der Schneidkante.
Ursache | Lösung |
|
|
|
|
|
|
Oberflächengüte
Die Oberfläche sieht „faserig" aus und fühlt sich auch so an. Die geforderte Maßgenauigkeit wird nicht erfüllt.
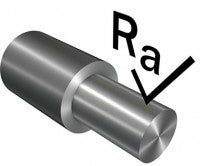
Ursache | Lösung |
|
|
|
|
|
|
Gratbildung
Gratbildung am Werkstück beim Ein-/Austritt aus dem Werkstück
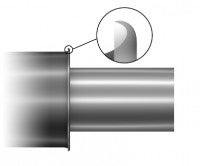
Ursache | Lösung |
|
|
|
|
|
|
Vibration
Hohe radiale Schnittkräfte aufgrund von Vibrationen oder Rattermarken, die durch Werkzeug oder Werkzeugspannung verursacht werden. Typisch für die Innenbearbeitung mit Bohrstangen.
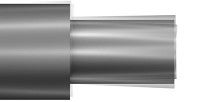
Ursache | Lösung |
|
|
|
|
|
|
|
|
Vibrationen
Hohe tangentiale Schnittkräfte
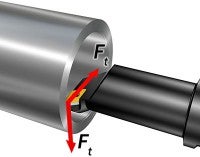
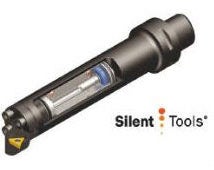
Ursache | Lösung |
|
|
|
|
|
|
|
|
|
|
Suchen Sie Werkzeugempfehlungen?
Hier finden Sie unsere Zerspanungswerkzeuge chevron_right
Brauchen Sie Beratung?
Stellen Sie uns eine Frage chevron_right
Was es sonst noch über die Grundlagen unserer Metallzerspanung zu lernen gibt?
Registrieren Sie sich für unser kostenloses E-Learning Programm chevron_right
Wendeplattenverschleiß
Zur Erzielung optimierter Schnittdaten, bester Werkstückqualität und Standzeit sollte stets die Schneidkante/Wendeschneidplatte überprüft werden. Die nachfolgende Auflistung unterschiedlicher Verschleißformen, deren Ursachen und mögliche Abhilfen dient als Referenz für eine erfolgreiche Drehbearbeitung.
![]() Freiflächenverschleiß |
|
|
Kerbverschleiß ![]() |
|
|
Kolkverschleiß ![]() |
|
|
![]() ![]() Plastische Deformation |
|
|
Aufbauschneidenbildung (B.U.E.) ![]() |
|
|
Abplatzungen ![]() |
|
|
Schneidenausbrüche ![]() |
|
|
Kammrisse ![]() |
|
|
Bruch ![]() |
|
|
Verschleiß der Umfangsfase - Keramik ![]() |
|
|
Schneidenausbrüche außerhalb der Schnittzone ![]() |
|
|
Suchen Sie Werkzeugempfehlungen?
Hier finden Sie unsere Zerspanungswerkzeuge chevron_right
Brauchen Sie Beratung?
Stellen Sie uns eine Frage chevron_right
Was es sonst noch über die Grundlagen unserer Metallzerspanung zu lernen gibt?
Registrieren Sie sich für unser kostenloses E-Learning Programm chevron_right