切断
切断主要在棒材进给机床中执行,通常在批量生产中使用。切断工序通常仅占零件总加工时间的一小部分,因此通常不被视为节省时间的目标。但是,切断工序完成后,一些零件仍有需要在副主轴中加工的附加特征。切屑缠绕在零件周围可能对在副主轴中夹紧下一个零件造成阻碍。如果出现这种情况,机床将加工出报废件或停止加工。切屑缠绕在已完工零件周围可能导致连续操作 (热处理、去毛刺、装配等) 出现问题,并影响表面质量。由于切断通常是对零件执行的最后几道工序之一,因此,安全非常重要。如果刀具在切断期间破裂,则正在加工的零件通常被报废。这可能导致机床长时间停机。
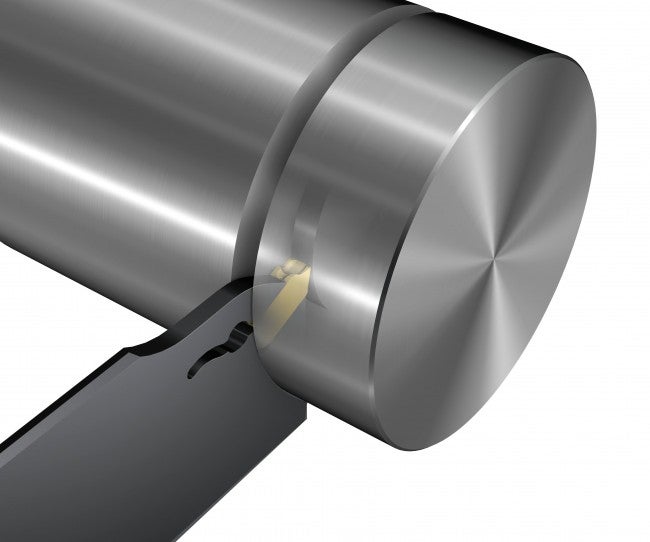
切断技巧:如何选择切断刀具
1. 浅切断
2. 中等切断
3. 深切断
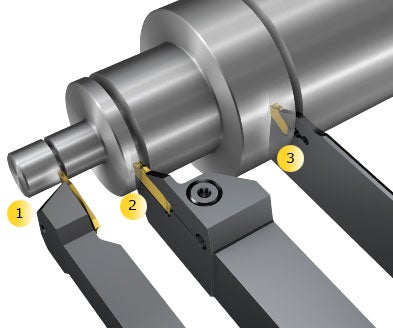
由于加工安全性非常重要,因此,最好选择采用高精度冷却液的刀具。这样可以排屑,降低温度,减轻刀片磨损并改进表面质量。使用悬伸尽可能短的刀具和安全的刀片夹紧系统可确保最佳稳定性。切断零件、棒材或管件时,节省材料并最大限度地减少切削力非常重要。窄刀片可产生更低的切削力并节省材料。选择为切断设计的刀片槽型。这些专门设计的刀片能够产生比槽更窄的切屑。这使切断工序能够实现良好的切屑控制和表面质量。
切断首选
单刃和双刃解决方案应被视作不同切断工序的首选。使用能够产生比槽更窄的切屑的刀片。
浅切断 对于浅切断 (直径 ≤ 12 mm (0.47英寸) ),使用三刃刀片可在批量生产中实现经济的切断。
中等切断
对于中等切断 (直径 ≤ 40 mm (1.57英寸)),使用螺钉夹紧和弹簧锁紧刀柄与双刃刀片。
深切断
对于深切断 (直径 ≤ 112 mm (4.41英寸)),刀片稳定性至关重要,因为这种类型的切削会在刀片上施加较高的力。因此,通过弹簧稳定夹紧的刀板和单刃刀片是最佳选择。
无飞边和无毛刺切断
为了实现无飞边和无毛刺切断,使用具有小刀尖圆角半径的锋利槽型。前角刀片还将减少飞边和毛刺。前角刀片将产生侧向切削力,仅推荐用于短悬伸 (< 13 mm (0.51英寸)) 工况。
小零件加工
对于小零件加工,使用宽度尽可能小且切削刃尽可能锋利的刀片。为了确保最佳加工安全性,使用采用高精度冷却液的刀具。如果不需要极高的刀具切削刃锋利程度,则选择三刃或双刃刀片可提供经济性更高的解决方案或实现更大的直径。
切断技巧:如何应用切断工序
切断棒材和管件
悬伸 (OH)
最大限度地减少悬伸。切断棒材时,更短的悬伸和更高的刀板都能显著减少弯曲 (δ)。
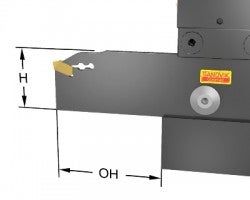
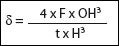

短悬伸可显著提高稳定性。在夹头附近切断。使用需要稳定工况和需求仔细装卸的薄刀片切断时,这一点尤为重要。
- 对于不可避免的长悬伸,使用轻快切削槽型
- 如果悬伸小于1.5 x H,则使用该槽型的推荐进给
- 如果悬伸超过1.5 x H,则将进给率降至该槽型推荐进给率的下限值
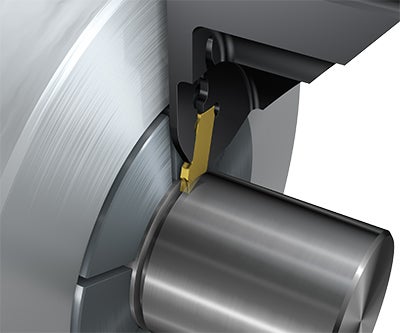
刀具中心高
确保偏差为±0.1 mm (±0.004英寸) 的正确中心高非常重要,特别是在沿径向切断时。对于长悬伸,使用高于中心的最大偏差+0.1 mm (+0.004英寸) 来补偿弯曲。
低于中心定位会导致:
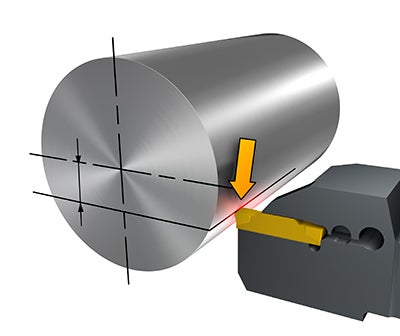
- 增加了飞边
- 破裂 (不利的切削力)
在中心定位会导致:
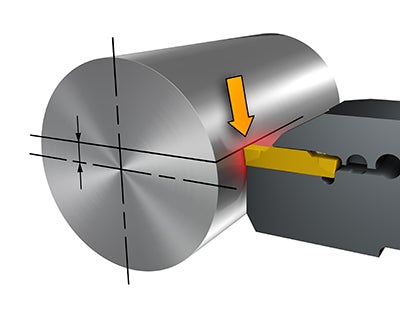
- 破裂 (穿过中心)
- 快速后刀面磨损 (间隙小)
进给率
切穿棒材中心会产生不必要的韧性要求,从而可能导致刀片破裂。在这种情况下,当工件开始沿切削方向的反方向运动时,刀片将受到剐蹭。这种作用会使刀片受到拉伸应力,从而导致破裂。
计算速度:

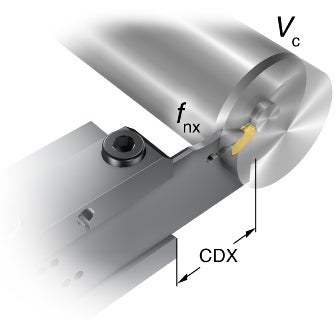
在到达中心之前约 2 mm (0.08英寸) 处将进给降低最多75%。在中心降低进给将减少切削力并显著延长刀具寿命,在周边提高进给将改进生产率并延长刀具寿命。为了避免破裂,在到达 棒材中心之前约0.5 mm (0.02英寸) 处停止进给,切断部分将在自身重量和长度的作用下落下。

通过中心进给将导致破裂
副主轴
切断棒材时,副主轴可用于拉断零件,同时显著降低韧性要求并延长刀具寿命。这样也允许使用耐磨性更高的材质,进而可进一步延长刀具寿命。执行切断工序,但在到达中心之前约 1 mm (0.04英寸) 处停止进给。然后使用副主轴拉断零件。
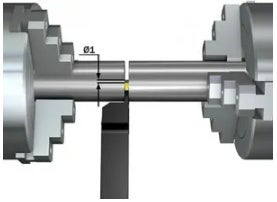
刀片宽度
使用尽可能窄的刀片可节省棒材并最大限度地减少切削力和环境污染。
使用表格来选择刀片宽度CW,具体取决于零件直径D:
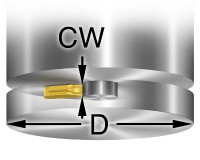
D mm (英寸) | CW mm |
---|---|
-10 (-0.4) | 1.0 |
10-25 (0.4-1.0) | 1.5 |
25-40 (1.0-1.6) | 2.0 |
40-50 (1.6-2.0) | 2.5 |
50-65 (2.0-2.6) | 3.0 |
无飞边和无毛刺切断
切断棒材或管件时,选择左手型或右手型前角刀片以控制飞边或毛刺。大前角刀片可减少飞边和毛刺,但可能无法进行直线切削,并且可能导致更不充分的切屑控制、更差的表面质量和更短的刀具寿命。使用尽可能小的前角刀片。对于更长的悬伸,使用中置型刀片 - 刀具越长,使用前角刀片的问题就越大。
| 前角 | 中置型 |
稳定性和刀具寿命 | 不良 | 良好 |
径向切削力 | 低 | 高 |
轴向切削力 | 高 | 低 |
飞边/毛刺 | 小型 | 大型 |
振动风险 | 高 | 低 |
表面质量和平整度 | 不良 | 良好 |
切屑流 | 不良 | 良好 |
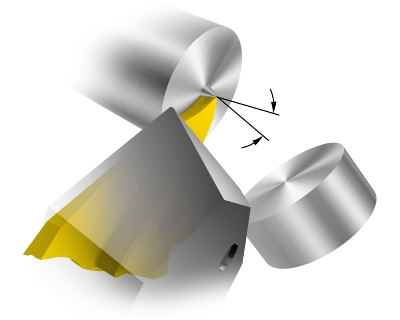
切断小直径棒材
确保产生尽可能最小的切削力。使用宽度尽可能小且切削刃尽可能锋利的刀片。
切勿将刀具用于止挡棒材!
这对任何刀具都不好,然而,对于小刀片宽度,还将损坏刀柄。
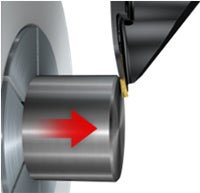
切断至钻孔
避免切断至锥形区域内,因为这将导致刀板偏斜并且可能导致刀具破裂。
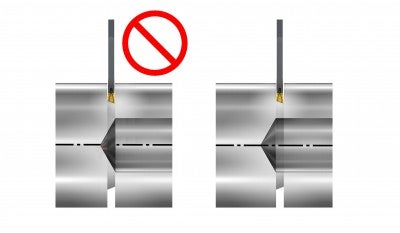
薄壁管件
当切断薄壁管件时,应确保产生尽可能低的切削力。使用宽度尽可能小且切削刃尽可能锋利的刀片。

冷却液
使用冷却液和润滑油会对切断切槽的加工安全性产生较大影响。在切削液和冷却液部分中,您将找到有关上方和下方冷却液、高精度冷却液和压力的更多信息和建议。
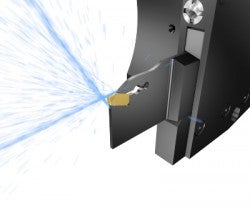
Y轴切断
Y轴切断是一种全新的切断方式。在传统切断中,大部分切削力由切削速度生成,其余部分则由切削进给生成。合成力以大约30°角导入刀具。因此,切断刀板的受力线刚好在第二弱方向。克服此弱点的最佳方法是缩短刀板悬伸和/或增加刀板高度。通过将刀座转动90°并利用多任务机床和车削中心的Y轴进给刀具,合成切削力将被引导至刀具的最强方向。对于60 mm (2.36英寸) 的刀板悬伸,抗弯刚度将提高6倍以上。这可确保更加稳定的无声无振动切削加工,从而实现更好的表面质量,并允许使用更高的进给率和更长的刀具悬伸。用于Y轴切断的CoroCut® QD是在有Y轴的车削中心、多任务机床和纵切机床上执行切断的首选。它能够加工最大180 mm (7英寸) 的大直径零件,特别适合长悬伸工况,能够到达主夹头与副夹头之间。在悬伸大于刀板高度时使用Y轴切断刀板始终是有利的。
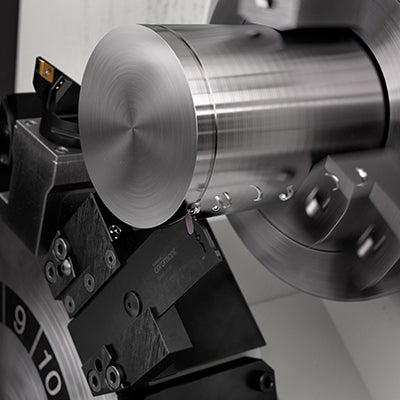
如何应用
在多任务机床上执行Y轴切断
刀具总成的长度通常足以到达主夹头与副夹头之间。这意味着与Y轴负载相比,总体装夹在X方向较弱 (切削力导入刀具装配以及机床主轴)。
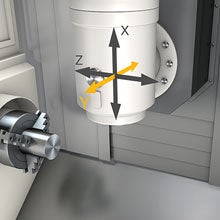
传统装夹
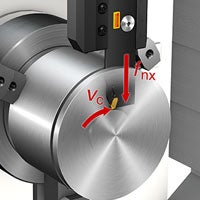
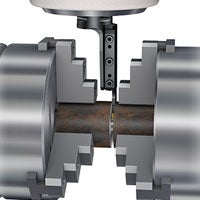
Y轴切断装夹
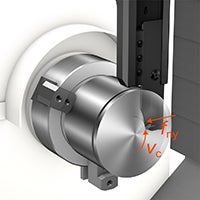
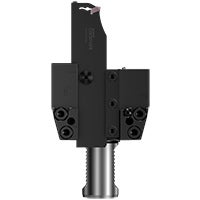
刀具长度通常可使用光学装置在机床外测量。切断时,刀具长度将成为刀具中心高,请务必确保中心高正确,特别是在向中心切断时。
在机床外进行光学测量
如果难以看见切削刃,刀具上还有一个基准面。该基准位于:
- E、F、G和H刀座 (2、2.5、3和4 mm (0.079、0.098、0.118和0.157英寸) ) 的切削刃上方5±0.05 mm (0.197±0.002英寸)
- J和K刀座 (5和6 mm (0.197和0.236 英寸) ) 的切削刃上方5.5±0.05 mm (0.236±0.002英寸)
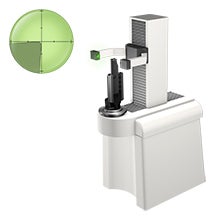
在车削中心中执行Y轴切断
刀具总成通常较为细长,因此能够到达主夹头与副夹头之间,并且允许在夹头附近执行切断。与Y轴负载相比,总体装夹在X方向上较弱 (切削力被引导至刀具总成和刀架中)。

传统装夹

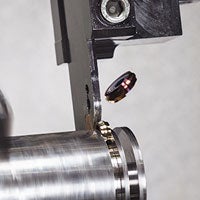
Y轴切断装夹
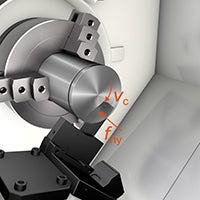
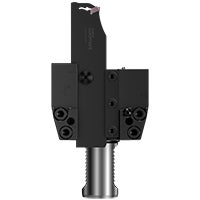
刀具长度通常可使用对刀仪在机床内测量。切断时,刀具长度将成为刀具中心高,请务必确保中心高正确,特别是在向中心切断时。
如果难以看见切削刃,刀具上还有一个基准面。该基准位于:
E、F、G和H刀座 (3 mm (0.118 英寸) ) 的切削刃上方5±0.05 mm (0.197±0.002英寸)
J和K刀座 (4 mm (0.157 英寸) ) 的切削刃上方5.5±0.05 mm (0.236±0.002英寸)
使用对刀仪在机床内测量
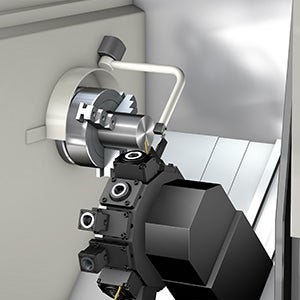
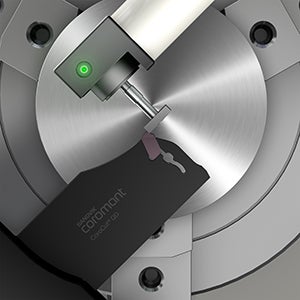
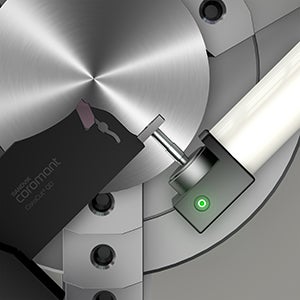
在纵切机床中的Y轴切断加工
如果切削刃难以触碰棒材,刀具上还有一个基准面。该基准位于:
E和F刀座 (3 mm (0.118 英寸) ) 的切削刃上方5±0.05 mm (0.197±0.002英寸)