外圆切槽
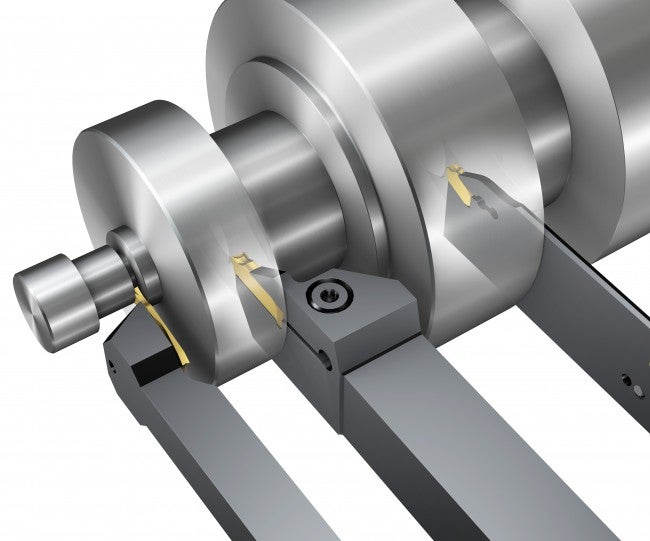
对于切槽而言,高生产率是目标。与切断相比,外圆切槽的要求通常更低,因此更易确保加工安全性。由此可将重点转移到提高生产率上,特别是在加工宽槽时,因为与窄槽相比,它们需要花费更长的时间,并且会对零件的总加工时间产生更大的影响。
外圆切槽方法
加工深槽时,由于需要长悬伸、排屑困难以及难以确保冷却液到达切削刃的原因,加工安全性可能成为一项挑战。单刀切槽是最经济的高生产率槽加工方法。但是,如果槽宽大于刀片宽度,则可通过多步切槽、横车、坡走或仿形切削来加工槽。外圆切槽的首选是带高精度冷却的刀具。
应用技巧:如何应用外圆切槽
单刀切槽

单刀切槽是一种经济的高生产率槽加工方法。采用单刀切槽时,需要考虑以下方面:
- 如果表面质量非常重要,则使用采用Wiper (修光刃) 技术的刀片槽型
- 确保使用具有严密公差以及正确刀尖圆角半径和宽度的刀片,推荐精磨刀片 (例如-GF)
- 如果进行批量生产,则使用具有正确轮廓和倒角的刀片。如果未包含在标准产品类别中,请订购Tailor Made定制刀片
粗加工宽槽
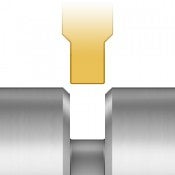
加工宽槽或在台肩之间进行车削的最常用方法是:
- 多步切槽
- 横车
- 坡走车槽
三种方法均为粗加工工序,随后必须执行一道单独的精加工工序。
经验法则是:如果槽的宽度小于深度,则使用多步切槽法;如果宽度大于深度,则使用插车法。加工细长零件时,可使用坡走车槽方法。
多步切槽

- 用于深而宽的凹槽 (深度大于宽度)
- 最后切削的剩余环 (4和5) 应小于刀片宽度 (CW - 2 x 刀尖圆角半径)
- 加工剩余环时将进给提高30-50%
- 首选槽型为-GM
横车
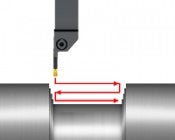
- 用于更宽并且更浅的凹槽 (宽度大于深度)
- 不要车削到肩部,要留台阶余量避让
- 首选槽形为-TF和-TM
坡走车削 (车削/仿形切削)
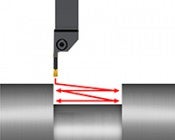
- 最佳切屑控制
- 将径向切削力和沟槽磨损降至最低
- 首选槽形为-RO和-RM
精加工车削一个凹槽
- 选择方案1:使用车削槽型
- 选择方案2:使用仿形切削槽型,例如加工大半径槽
- 推荐的轴向和径向切削深度为0.5-1.0 mm (0.02-0.04英寸)
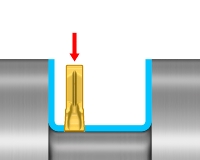
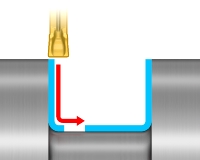
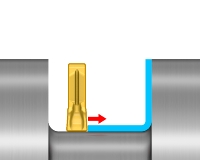
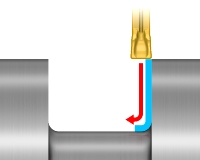
车削和外圆切槽
使用切断切槽刀片进行车削
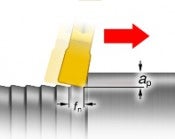
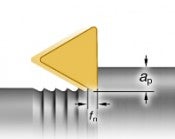
- 插车时,使用大于刀尖圆角半径的切深 (ap)
- Wiper (修光刃) 效应 - 单位切深的进给率 (fn/ap) 必须相对较高,以确保刀具和刀片略微偏斜。这可确保切削刃与加工面之间存在间隙
- fn/ap过低会导致刀具剐蹭、振动和表面质量差
- ap最大值 = 刀片宽度的75%
表面质量 | |||||
Ra µm | |||||
![]() | |||||
进给,fn mm/r 英寸/转 |
![]() | TNMG 160404 |
![]() | TNMG 160408 |
![]() | 切断切槽刀片 - 5 mm -RM |
![]() | 切断切槽刀片 - 4 mm -TF |
![]() | 切断切槽刀片 - 6 mm -TM |
下图所示为切断切槽刀片与TNMG刀片 (具有04或08刀尖圆角半径) 的表面质量的比较。
车槽
进行侧面车削时,刀具和刀片肯定会弯曲。但是,过度弯曲可能导致振动和破裂:
- 较厚的刀板会减少弯曲
- 较短的悬伸 (OH) 可减少弯曲 (δ)
- 避免在车削工序中使用长和/或薄的刀具
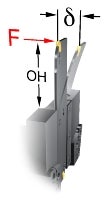
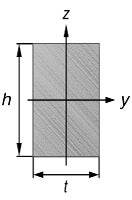
较短的悬伸会减少侧向弯曲
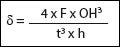
底切削和外圆切槽
许多零件都需要执行磨削或螺纹加工工序。当在轴肩位置进行磨削或螺纹加工时,需要有避让空间;因此,建议使用底切削工序专用刀片。例如:T-Max Q-Cut®和CoroCut® 1-2
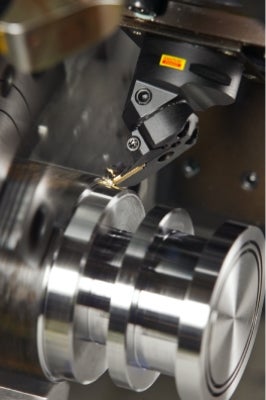
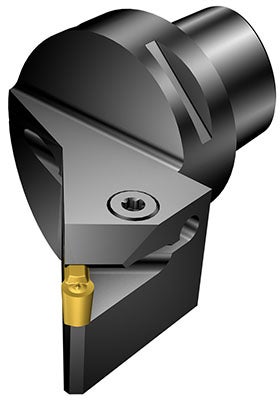