攻克微观缺陷的可靠方式
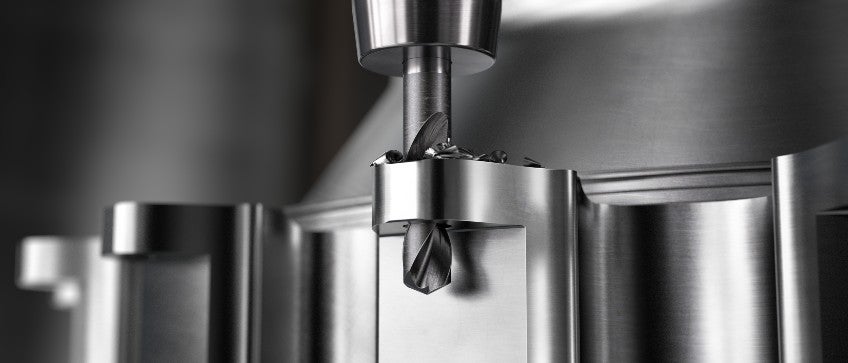
采用改进设计的硬质合金钻头进行的测试为提升孔的质量开启了全新的可能性。
“Measure twice and cut once” (两次测量,一次切削到位;三思而后行) 是制造业的常用表达,但是说起来容易,做起来难,尤其是对于难切削材料的加工。这也是为何当航空航天业的全球领先制造商试图将其钻孔加工流程的整个第二阶段完全移除同时又要提升航空航天零件的孔质量时,选择求助金属切削领域的全球领导者。在本文中,山特维克可乐满全球产品经理James Thorpe阐释了为何说钻头本身的设计是提升孔加工质量的必备要素。
钻孔加工是所有加工过程中最普遍的,但同时也最容易被视为“想当然”的加工过程。很多工厂几乎看不到更换或升级既有钻孔装备的必要性,同样的刀具和切削参数他们已经使用了多年。但是,从史无前例的新冠肺炎疫情袭来的那一刻起,这样的情况注定要改变。制造商们已经体验过了客户市场前所未有的持续变化,现在他们意识到了进行生产变革的必要性。
例如,大多数制造商都开始寻找新的供应商和产品。因此,曾经仅专注于某一个生产领域的工厂如今纷纷为了更广泛类型的难加工、挑战大的材质而开启更多数控车床和铣床。同时,制造商们也必须探索新的方式提升利润和缩短生产周期,同时不能牺牲产品质量。
换言之,现在制造商们必须重新思考钻孔加工方式。
白层
对于航空航天业制造商或是想要进入航空航天领域以进行多元化经营的机械工程企业,孔的表面质量是一大关注点。更优的孔质量对于预防部件故障至关重要,而质量在很大程度上取决于孔加工或表面工艺处理所采用的制造过程。
刀具解决方案以及钻头切削刃的槽型都在不断演进,以符合极其严苛的制造过程及工件质量标准。冷却液的应用也在改进,以减少刀具的热量积聚。且有测试发现这些因素中的每一个都可控制工件材质表面所形成的所谓“白层” (white layer)。
“white layer”这个术语本身由航空航天业的一家全球领先制造商创造,其也是山特维克可乐满的客户。“白层”指的是经过钻削加工的零件表面所形成的薄薄一层超细颗粒结构,由钻头的热量造成。白层不仅会改变材质的表面特性,也是客户质量管理流程所不接受的。
该制造商对于航空航天零件上的钻孔应用严苛的孔表面处理工艺,包括涡轮盘、压气机以及鼓和各种轴。也因此,该制造商最终选择与山特维克可乐满合作探寻白层形成的原因以及如何控制白层生成。
重要的一点是:测试不仅仅是由质量管理推动的。从高级管理层面而言,客户希望缩短整体运行时间、提升利润,而实现如此效果的方法是剔除加工过程的整个第二阶段。
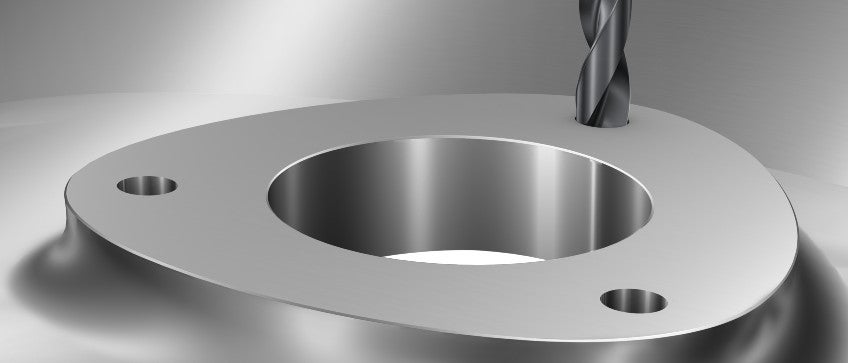
对于航空航天业制造商或是想要进入航空航天领域以进行多元化经营的机械工程企业,孔的表面质量是一大关注点。这里,使用-SM槽型的CoroDrill 860对HRSA高温合金机匣进行轴套钻孔
。
第二过程
第二个过程发生于硬质合金钻头钻孔之后,可能涉及铰削、插铣或铣削来完成零件加工。第二阶段的主要目的是满足表面完整性的要求——减少诸如白层这样的问题——而非为了满足尺寸精准性要求,公差要求严格的钻孔加工除外。
从总成本角度而言,第二过程甚至比维持低切削参数的成本更昂贵,后者是保持表面完整性的另一种方法。这正是山特维克可乐满的这位客户希望彻底去除这个阶段的原因。如果供应商的产品能在无需任何第二过程的前提下制造出尺寸合格的孔,则该供应商便具备了能够大幅降低单件成本的优势地位。
探寻白层形成原因及可能的预防措施的过程涉及四项测试:钻削高强度镍铬合金Inconel 718,一种使用广泛的航空航天材料。这是该客户第一次进行此类研究。
通过测试对山特维克可乐满整体硬质合金钻头CoroDrill® R840和CoroDrill® R846的钻孔加工表现进行评估。两款钻头分别应用两套不同的切削参数:切削速度分别为58 mm/min和98 mm/min,而转速分别为829 rev/min和757 rev/min。测试中还测量了切削力和扭矩数据以及白层厚度。
自从进行了这些测试之后,CoroDrill R840就被CoroDrill® 860-GM槽型取代了,而CoroDrill R846被CoroDrill® 860-GM槽型取代。这两款新一代刀具均以延长刀具寿命同时不影响钻孔质量。
测试结果对于白层厚度的成因提供了一些有价值的发现。尤其值得注意的是CoroDrill R846生成的白层少一些,而这要得益于其弯曲的径向切削刃。同时认为:CoroDrill R840的直型切削刃以及切削刃的倒角与切削力、扭矩和白层厚度的增加直接相关。所以说,钻头的设计决定了是否能够在不降低切削参数的前提下实现出色的钻孔质量以及白层厚度的缩减。
不仅是这家航空航天业全球领先制造商与山特维克可乐满合作开展的测试对白层的形成揭示了一二,该公司还得以成功去除了一些“第二工序”,例如铰削和插铣,由此减少了加工时间获得了成本效益。此外,测试结果也证明了山特维克可乐满CoroDrill 860系列硬质合金钻头的设计优势。
专注钻头设计,全面提升钻孔加工
该系列包括前面提到的CoroDrill 860-GM槽型,设计用意是成为能够钻削ISO P、M、K和H这些难切削材料的“全能”刀具,覆盖所有行业领域。CoroDrill 860-GM槽型专为ISO S材质的加工经过优化,如高温合金 (HRSA)、钛合金和Inconel。事实证明,后一款钻头在航空航天业的应用尤其普及。
通过CoroDrill 860-GM槽型和CoroDrill 860-SM槽型钻头,山特维克可乐满的工程师们得以贯彻“刀具寿命的延长和钻孔质量的提升取决于钻头设计”这一理念。CoroDrill 860-GM槽型钻头采用创新的抛光容屑槽设计,提升了排屑效果和钻芯强度,同时降低了钻削加工时的切削力。
同时,CoroDrill 860-SM槽型钻头采用全新材质且钻尖结构设计经过优化,这进一步延长了加工难加工材料HRSA时的刀具寿命。其结果是钻孔质量的提升。
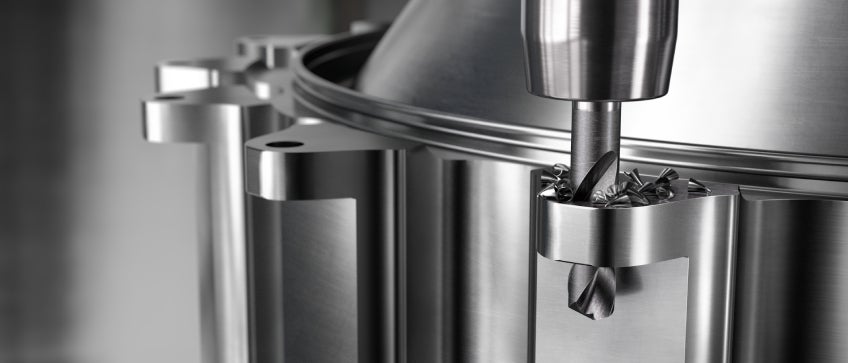
CoroDrill® 860-SM槽型钻头证明:更长的刀具寿命和更优的钻孔质量取决于钻头的设计。
CoroDrill 860在上市前经过了各种行业的测试。法国一家机械工程公司曾将CoroDrill 860-GM槽型钻头用于加工AISI 4140高强度建筑用钢。可以针对凹面、凸面进行高质量钻孔,孔的直线度及公差都很好。自此,该公司便与山特维克可乐满建立起全新的业务合作关系。
山特维克可乐满的另一个客户——意大利的一家机械工程制造企业使用CoroDrill 860-GM槽型钻头加工合金钢34CrNiMo6的生产率提升了45%以上 (相比竞争对手的钻头)。刀具寿命也延长了100%。而采用CoroDrill 860-SM槽型在加工Inconel 718表现突出。尤其值得一提的是在波兰卡托维兹 (Katowice) 进行的测试中,相比CoroDrill R840,采用CoroDrill 860-SM槽型钻头实现了刀具寿命180%的大幅度提升。
无论对于航空航天、机械工程还是其他行业,如果钻头是专为特定用途而专门设计的,则能够实现出色的加工效果。同时,诸如山特维克可乐满的CoroPlus® Tool Guide这类在线工具能够提供进一步支持。用户通过网页浏览器即可访问该工具,输入所希望加工的工件材质以及孔直径和深度即可找到符合自身需求的最佳整体式圆柄刀具和切削参数。
尽管还未实现“两次测量,一次切削到位”,但是采用CoroDrill 860-GM槽型和采用CoroDrill 860-SM槽型钻头的优异表现已经使制造商们开始重新思考钻孔加工方式。