Sådan vælger du tilspændingsmetode ved gevinddrejning
OptiThreading™
Hvad er OptiThreading™?
OptiThreading™ er en metode med oscillerende værktøjsbevægelser, der sikrer kontrolleret spånbrydning ved gevinddrejning. Denne unikke metode sikrer gentagen afbrudt spån i alle overløb, bortset fra det sidste.
Fordele ved OptiThreading™
- Mindre manuelt arbejde med at fjerne lange spåner, der blokerer værktøjet, emnet eller spåntransportøren
- Færre uplanlagte maskinstop og dermed højere produktivitet og bedre automatiseringsmuligheder
- Bedre overfladekvalitet på emnet, idet ingen lange spåner medfører skader
- Det giver et gevind med bedre overfladekvalitet og kontrollerede vibrationer
- Mulighed for at øge skærehastigheden, primært til større gevind/diametre, og det giver en højere produktivitet
- Færre vibrationer takket være metoden – mulighed for øget værktøjsudhæng
Det skal du overveje med OptiThreading™
- Til CNC-maskiner, der kan håndtere ISO-kode (G32/G33/G34)
- Ud- og indvendige applikationer
- Normale og kegleformede/koniske gevind
- Til alle standardgevind med en gevinddiameter større end 12 mm
- Det anbefales at anvende køling
OptiThreading™ – sådan gør du
Se videoen og lær, hvordan du udarbejder et NC-program med CoroPlus® Tool Path-softwaren.
Konventionelle gevinddrejningsmetoder
Der findes tre primære tilspændingsmetoder til gevinddrejning; modificeret flanketilspænding , radial tilspænding og trinvis tilspænding. Tilspændingsmetoden afgør, hvordan skæret indføres i emnet for at skabe den ønskede gevindform.
Modificeret flanketilspænding
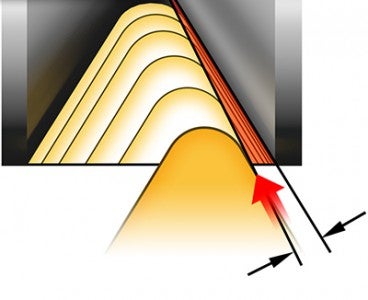
Radial tilspænding (lige tilspænding)
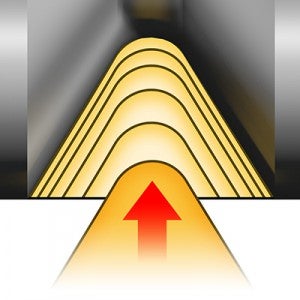
Trinvis tilspænding
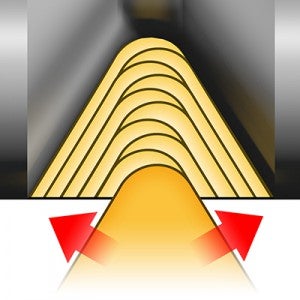
Valget af tilspændingsmetode bestemmes af maskine, skærgeometri, emnemateriale, gevindprofil og stigning og vil påvirke følgende direkte:
- Spånkontrol
- Gevindkvalitet
- Type skærslid
- Værktøjslevetid
Modificeret flanketilspænding
Den modificerede flanketilspænding er førstevalgsmetode, da den giver den længste værktøjslevetid og den bedste spånkontrol. De fleste CNC-maskiner er forprogrammerede til denne metode, der er modificeret lidt (vinklet) for at undgå at skærkanten gnider mod komponentens overflade.
- Anbefales til alle typer gevinddrejning og skærtyper
- Spånen er tykkere, men dannes kun på den ene side af skæret, hvilket gør bearbejdningen lettere
- Der er brug for færre overløb, da der overføres mindre varme til skæret
- Kan anvendes på begge flanker af gevindet (modstående flanke) til at styre spånen i den bedste retning
- Anvendes til store gevind og til eliminering af vibrationsproblemer
- Til skær med spånbrydningsgeometri er det den bedst egnede tilspændingsmetode med en tilspændingsvinkel på 1°
Eksempler på maskinkode:
G76, X48.0, Z-30.0, B57 (tilspændingsvinkel), D05 osv.
Til forskellige maskintyper kan parameteren for flanketilspændingen være: G92, G76, G71, G33 og G32
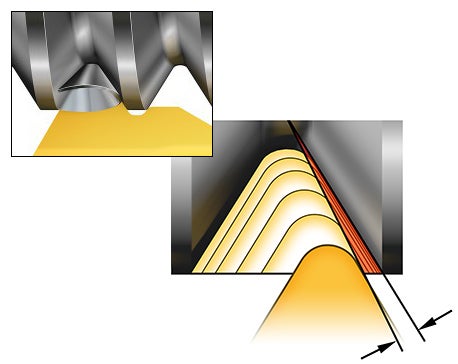
Radial tilspændingsbevægelse
Radial (lige) tilspænding er den hyppigst anvendte tilspændingsmetode og den eneste mulige på mange mekaniske drejebænke.
- Frembringer en stiv, V-formet spån, der er vanskelig at danne og styre
- Skærsliddet er jævnt på begge flanker
- Velegnet til små stigninger
- Skærspidsen udsættes for høje temperaturer, hvilket begrænser den mulige tilspændingsdybde
- Risiko for vibration og dårlig spånkontrol ved store stigninger
- Spånbrydningsgeometrier er ikke egnede til radial tilspænding.
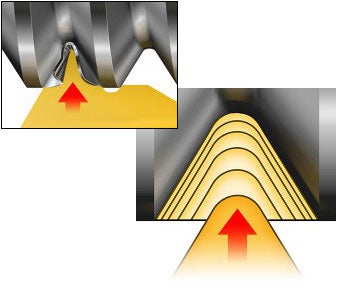
Trinvis tilspænding
Trinvis tilspænding er førstevalget til større gevindprofiler (anbefalet til gevindstigninger over 5 mm (5 t.p.i)).
- Spåner føres begge veje, og det gør spånkontrollen vanskelig
- Giver jævnt skærslid og den længste værktøjslevetid ved meget grove gevind
- Alle geometrier kan bruges til trinvis tilspænding
- Kræver et specielt CNC-maskinprogram
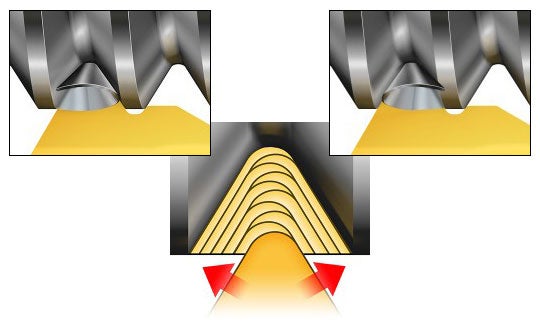
Dybde pr. overløb
Se anbefalingerne om tilspænding i kataloget eller ToolGuide. De anbefales som startværdier, og det mest velegnede antal overløb skal prøves af for den specifikke type gevinddrejning.
- Tilspænding på mindre end 0,05 mm (0,002 tommer) bør undgås
- For skær med spids af kubisk bornitrid bør tilspændingen ikke overstige 0,10 mm (0,004 tommer)
- For flerprofilskær er det afgørende, at der anvendes de rigtige tilspændingsanbefalinger
Aftagende spåndybde pr. overløb (konstant spånareal)
Aftagende tilspændingsdybde pr. overløb er den mest almindelige måde at forbedre bearbejdningsresultatet på og er førstevalget ved alle typer gevinddrejning.
- Lad det første overløb være det dybeste og det sidste overløb omkring 0,07 mm (0,003 tommer)
- Giver en jævn belastning af skæret og et mere "afbalanceret" spånområde
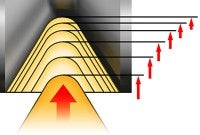
Konstant dybde pr. overløb
Med en konstant dybde pr. overløb, er hvert overløb (bortset fra det sidste overløb) af samme dybde, uanset antallet af overløb. Det er en mindre produktiv metode.
- Øger det nødvendige antal overløb
- Stiller større krav til skæret
- Kan give bedre spånkontrol
- Må ikke bruges til stigninger over 1,5 mm eller 16 t.p.i.
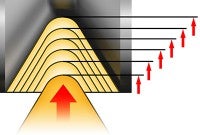
Gevinddrejningscyklusser på CNC-drejebænke
Normale CNC-drejebænke er udstyret med specielle gevinddrejningscyklusser, hvor stigning, gevinddybde og antal overløb kan indstilles på forskellige måder – inklusive første og sidste overløb.
Til det sidste overløb advarer vi kraftigt mod at bruge et overspringsoverløb (hvor spåndybden på det sidste overløb svarer til spåndybden på det foregående overløb). Det er bedre at anvende de anbefalede tilspændingscyklusser til at sikre bedre gevindkvalitet og lang skærlevetid.
Værktøjets tilspændingsretning
Et gevind kan fremstilles på flere forskellige måder. Spindlen kan rotere med uret eller mod uret, med værktøjstilspænding hen mod eller bort fra spændepatronen. Gevinddrejeværktøjet kan også anvendes i normal eller upside-down-position (sidstnævnte hjælper med at fjerne spåner).

De mest almindelige opsætninger er markeret med grønt i nedenstående figur.
Arbejde væk fra spændepatronen (kørsel indefra og ud)
Ved at bruge værktøjer i højreudførelse til venstregevind (og omvendt) kan du reducere omkostningerne ved hjælp af en reduktion af værktøjslageret.

Der skal anvendes en negativ underlagsplatte i opspændinger markeret med rødt i nedenstående figur.
Udvendig | |
Gevind i højreudførelse | Gevind i venstreudførelse |
![]() Værktøj/skær i højreudførelse | ![]() Værktøj/skær i venstreudførelse |
![]() Værktøj/skær i højreudførelse | ![]() Værktøj/skær i venstreudførelse |
![]() Værktøj/skær i venstreudførelse | ![]() Værktøj/skær i højreudførelse |
Indvendig | |
Gevind i højreudførelse | Gevind i venstreudførelse |
![]() Værktøj/skær i højreudførelse | ![]() Værktøj/skær i venstreudførelse |
![]() Værktøj/skær i højreudførelse | ![]() Værktøj/skær i venstreudførelse |
![]() Værktøj/skær i venstreudførelse | ![]() Værktøj/skær i højreudførelse |
![]() Værktøj/skær i venstreudførelse | ![]() Værktøj/skær i højreudførelse |