Tłoczniki
![]() Tłoczniki to pierwsze, co przychodzi na myśl w przypadku produkcji podzespołów samochodowych. To z tego powodu w wykonanie każdego tłocznika inwestuje się znaczną ilość czasu, środków i wiedzy. Z tego samego powodu warto skorzystać z możliwości skrócenia czasu wykonania i obniżenia kosztów produkcji tłoczników, szczególnie w obliczu coraz szybszej rotacji modeli na rynku motoryzacyjnym. Wykonanie tłocznika wymaga sporych umiejętności w zakresie obróbki metalu, zarówno technologii prostych, jak i bardziej zaawansowanych metod skrawania żeliwa, żeliwa sferoidalnego, stali zwykłych i hartowanych. Przegląd zastosowań ![]() |
CoroMill® 745
Głowica frezarska na wieloostrzowe płytki przeznaczona do produkcji dużych partii, na elastycznych liniach obrabiarek zespołowych i w zastosowaniach, w których ważną rolę odgrywa maksymalne wykorzystanie narzędzi. Opatentowany system osadzenia płytek, zapewnia tak samo lekki przebieg skrawania i wysoką wydajność jak w przypadku frezów na jednostronne dodatnie płytki, ale w tym przypadku płytki są dwustronne i posiadają łącznie 14 krawędzi skrawających.
CoroMill® 345
CoroMill 345 to przedstawiciel nowej generacji frezów czołowych o kącie 45 stopni, zaprojektowany, aby uzyskać najlepszą efektywność pod względem kosztów na rynku. To nowoczesne narzędzie powstało dla zapewnienia dużej wydajności frezowania czołowego stali zwykłej, stali nierdzewnej i żeliwa przy małej i średniej głębokości skrawania. Dzięki wszechstronności i dużemu zasięgowi, frez znajduje zastosowanie zarówno w trudnej obróbce zgrubnej, jak i wykonywaniu wykończeń lustrzanych.
CoroMill® 390 z długą krawędzią
Wszechstronny frez do zróżnicowanej głębokiej i płytkiej obróbki walcowo-czołowej. Szeroki asortyment średnic do frezowania różnych przedmiotów.
CoroMill® 316
System frezarski z wymiennymi częściami roboczymi zapewniający większą elastyczność i poprawę produktywności, a także obniżenie kosztów narzędzi. Mocne połączenie między wymienną częścią roboczą, a częścią chwytową nadaje wytrzymałość przy obróbce zgrubnej i sztywność przy obróbce wykończeniowej. Nowy pełnowęglikowy trzonek jest dostępny ze złączami o wielkościach od 10 do 25 mm. Większa sztywność i mniejsze ugięcie pozwalają na stosowanie narzędzia do obróbki na długich wysięgach i obróbki głębokich kieszeni, zapewniają też precyzję podczas obróbki wykończeniowej.
CoroMill® z zakończeniem kulistym
Frez trzpieniowy CoroMill z zakończeniem kulistym jest obecnie dostępny w wersji ze zintegrowanym złączem Coromant Capto. Złącze Coromant Capto pozwala na stosowanie frezu w systemach modułowych i nadaje większą sztywność.
CoroDrill® 880
Zastosowanie konstrukcji Step Technology sprzyja poprawie produktywności nawet o 100% w porównaniu do konwencjonalnych wierteł na płytki wymienne. Cztery efektywne krawędzie skrawające z geometrią wiper generują powierzchnię o wysokiej jakości wykończenia. Zoptymalizowane rowki wiórowe usprawniają odprowadzanie wiórów i pozwalają uniknąć przerw w produkcji. Dostępne średnice od 12.00 do 63.5 mm.
5. Obróbka wykończeniowa twardych materiałów
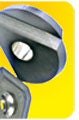
Gatunek GC1010
Nowy gatunek GC1010 do obróbki zgrubnej i wykończeniowej z pokryciem nakładanym metodą PVD doskonale uzupełnia dotychczasowy asortyment. Bardzo duża udarność krawędzi, większa odporność na zużycie i możliwość zwiększenia prędkości skrawania przy obróbce stali hartowanych mają bezpośredni wpływ na poprawę produktywności.
CoroMill® 300
Frez na płytki okrągłe do bezproblemowego frezowania czołowego, profilowania i wykonywania kieszeni. Obróbka zgrubna różnych materiałów: od żeliwa do stali hartowanej. Dodatni kąt skrawania nadaje się do obróbki lekkiej i pozwala na stosowanie dużych posuwów na obrabiarkach o mniejszej mocy i w niestabilnych warunkach. Nowe modele o średnicach 66 - 200 mm oraz na płytki wielkości IC20.
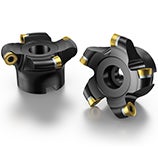
CoroMill® 200
Wytrzymały frez do obróbki czołowej i profilowej. Oferuje nadzwyczajną wydajność skrawania przy wysokim bezpieczeństwie obróbki i dużej niezawodności. Mocna krawędź skrawająca sprawia, że frez ten jest odporny na trudne warunki obróbki przerywanej (otwory, szczeliny itp.) i/lub obróbki powierzchni ściernych (naskórek).
Zakres średnic: 25–160 mm (1–10 cala)
CoroMilll® MH20
Frez do frezowania z wysokim posuwem zoptymalizowany pod kątem frezowania kieszeni w zagłębieniach form HRC 48, frezowania głębokich wybrań w podstawie form, obróbki naroży matrycy i frezowania występów przy niewielkim zagłębieniu w materiał.
Zakres średnic: 16–50 mm (5/8–2 cale)
CoroMilll® 415
Frez czołowy o niewielkiej średnicy do obróbki z wysokim posuwem. Jest to wszechstronne rozwiązanie do szerokiej gamy zastosowań. Oferuje mniejszy koszt jednostkowy i zwiększona produktywność dzięki wysokiej wydajności skrawania i czteroostrzowej płytce.
Zakres średnic: 13–32 mm (0.5–1.25 cala)
CoroMilll® 210
Frez do frezowania czołowego i do frezowania wgłębnego z dużym posuwem. Jest to niezwykle produktywne narzędzie do frezowania zgrubnego w zastosowaniach, w których priorytetem jest duża objętościowa wydajność skrawania. Duże prędkości posuwu jest możliwe dzięki cienkim wiórom, czego skutkiem jest wysoka produktywność.
Zakres średnic: 25–160 mm (1–6 cali)
CoroMilll® 210
Historia z happy endem z branży motoryzacyjnej
Początek: rok 1956; zakończenie: wtorek, godz. 10:15 czasu lokalnego. To właśnie wtedy wieloletni pracownik branży motoryzacyjnej Kenneth Rooth ujrzał, jak następują zmiany w branży od drewnianych modeli i gipsowych form do wydajnej produkcji z użyciem CAD - na miarę XXI wieku.
Ale kiedy Kennethowi wydawało się, że osiągnął już szczyt zaawansowania technologicznego, we współpracy z Sandvik Coromant uzyskał skrócenie czasu produkcji tłoczników o 30%.
Historyczne wydarzenie? Czas pokaże. Oszczędności? Bez wątpienia.
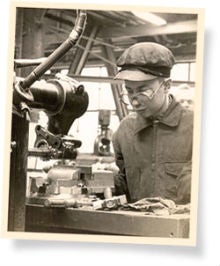
Producenci samochodów wykonują we własnym zakresie ponad jedną trzecią tłoczników. Jako że do wyprodukowania samochodu potrzeba około 750 różnych tłoczników, jest to czynność czasochłonna i spowalniająca cały proces produkcji. W obliczu tendencji do skracania czasu obróbki, zwiększania liczby modeli samochodów i obniżania kosztów warto przyjrzeć się bliżej temu zagadnieniu.
Kenneth Rooth miał świadomość, że liczne operacje skrawania i frezowania wykończeniowego są dużym nakładem czasu wykonywane ręcznie przez specjalnie przeszkolonych operatorów. Taki system był kosztowny i uniemożliwiał utrzymanie stałych norm jakości wyrobów. Jakość i precyzja wykonania prawych i lewych drzwiczek samochodu mogła być różna jeśli obrabiarki programowało dwóch operatorów.
Opracowanie sposobu obniżenia kosztów i skrócenia czasu obróbki przy jednoczesnej poprawie jakości zlecono firmie Sandvik Coromant. W ramach nowej technologii zastosowane zostały nowe narzędzia i metody obróbki. Oto wyniki: skrócenie czasu maszynowego o ponad 30%, całkowite wyeliminowanie etapu ręcznego polerowania podzespołów, znaczne ograniczenie innych procesów sterowanych ręcznie.
Jak oni tego dokonali?
Po pierwsze, wiertła ze stali szybkotnącej zastąpiono wiertłami na węglikowe płytki wymienne, co doprowadziło do istotnego zwiększenia wydajności produkcji. Aby poprawić wydajność obróbki podzespołów na długich wysięgach, w miejsce narzędzi konwencjonalnych wprowadzono narzędzia z tłumieniem drgań, przygotowano też szereg wzorników do wykorzystania w przyszłości.
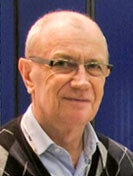
Kenneth Rooth
Nowa koncepcja produkcji tłoczników
Największe oszczędności związane z produkcją tłoczników można uzyskać przez wdrożenie nowych technik skrawania. Oto kilka sposobów, dzięki którym Kenneth Rooth zyskał sławę eksperta od obniżania kosztów.
Frez na płytki okrągłe zamiast frezu z zakończeniem kulistym: skrócenie czasu obróbki zgrubnej 3D
Do obróbki zgrubnej powierzchni 3D zazwyczaj stosuje się frezy z zakończeniem kulistym; popularna technika obróbki to frezowanie kopiowe z różną głębokością. Jeśli mamy przy tym do czynienia z długimi wysięgami końcówki wrzeciona, w czasie obróbki narzędzie i wrzeciono są poddawane dużym naprężeniom.
Zastosowanie frezu na płytki okrągłe i techniki frezowania kształtowego pozwala poprawić wydajność skrawania ze względu na większą liczbę efektywnych ostrzy. Stała osiowa głębokość skrawania przekłada się na mniejsze i równomierne obciążenie wrzeciona oraz możliwość optymalizacji procesu.
Szybsze wykonywanie otworów w podstawach tłoczników
Otwory w żeliwnych podstawach tłoczników są zwykle wykonywane za pomocą wierteł ze stali szybkotnącej. Jest to zazwyczaj operacja czasochłonna z uwagi na dużą liczbę otworów na śruby i otworów oczkowych.
Wprowadzenie wierteł na płytki wymienne, na przykład wiertła CoroDrill 880, pozwala na znaczną poprawę produktywności, nawet przy obróbce na sucho.
Wydajne wiercenie wgłębień w stali nieuspokojonej
Owalne otwory tego typu są zazwyczaj wykonywane za pomocą wierteł ze stali szybkotnącej, a następnie powiększane frezem.
CoroDrill 880 umożliwia zastosowanie techniki przerywanego wiercenia wgłębień do powiększenia otworu początkowego.
Wydajność skrawania wynosi w tym przypadku 85% i jest osiągania w znacznie krótszym czasie, pozostałą zaś część wykończenia otworu wykonuje się frezem na płytki okrągłe.
Element lancetu
Metoda konwencjonalna polega na wykonaniu otworu za pomocą wiertła ze stali szybkotnącej i poszerzeniu go monolitycznym frezem węglikowym, aż do otwarcia elementu.
Metoda alternatywna to wykonanie prostego otworu wiertłem na płytki wymienne (CoroDrill 880) i poszerzenie go frezem do wgłębień na płytki wymienne (CoroMill 210).
Metoda frezowania trochoidalnego pozwala na szybkie usuwanie materiału w wąskiej części rowka z dużą głębokością skrawania.
Gniazda tulei ustalającej
Wydajna i elastyczna metoda obróbki gniazd tulei ustalającej wymaga zastosowania frezu na płytki okrągłe CoroMill 300, frezu o długich krawędziach skrawających CoroMill 390 i wytaczaka CoroBore 825 do wykończenia przedmiotu.
CoroMill 300 jest wykorzystywany do frezowania czołowego oraz otwarcia otworu metodą interpolacji śrubowej w trzech osiach.
CoroMill 390LE zapewnia wydajność procesu dzięki dużej głębokości skrawania i lekkiemu przebiegowi czynności skrawania.
Ostateczne tolerancje przedmiotu są uzyskiwane za pomocą precyzyjnego wytaczadła CoroBore 825. Metoda ta pozwala skrócić czas obróbki przy zastosowaniu mniejszej liczby narzędzi.
Do obróbki elementów tego rodzaju stosowane są zwykle mniej produktywne narzędzia wiertarskie we współpracy z monolitycznymi frezami węglikowymi.
Obróbka powierzchni pod śruby zabezpieczające
Przy obróbce elementów o ograniczonej dostępności, wymagających długiego wysięgu, dobrą alternatywą dla frezu o długich krawędziach skrawających może być frez CoroMill 210 do wgłębień. Standardowo stosowane narzędzia to frezy o długich krawędziach skrawających ze stali szybkotnącej.
Przy frezowaniu wgłębień, siły działają w kierunku osiowym, co jest wskazane przy obróbce elementów na długich wysięgach z uwagi na drgania.
Właściwości zespołu narzędziowego poprawi użycie wyjątkowo stabilnego systemu modułowego Coromant Capto.
CoroMill 300 w obróbce zgrubnej powierzchni 3D.
CoroDrill 880 do wykonywania otworów w tłocznikach.
Wiercenie wgłębień za pomocą CoroDrill 880.
Frezowanie trochoidalne za pomocą CoroMill Plura.
CoroMill 390LE (o długich krawędziach) do obróbki tulei prowadzącej.
CoroMill 210 do frezowania wgłębnego.
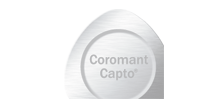
Coromant Capto®
Oszczędność czasu i pieniędzy przy wymianie narzędzi tokarskich, wiertarskich i frezarskich.
Niezrównana elastyczność przy produkcji tłoczników. Coromant Capto stało się jednym ze złącz opisywanych normą ISO.
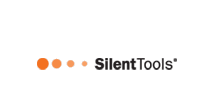
Silent Tools
W układach wykazujących tendencje do drgań, zastosowanie narzędzi z tłumieniem drgań Silent Tools może przyczynić się do znacznej poprawy produktywności.
Energia drgań jest pochłaniana przez trzonek z elementem tłumiącym, co umożliwia zwiększenie parametrów skrawania przy zminimalizowaniu drgań.
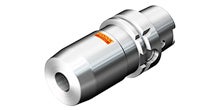
CoroChuck™ 930
Oprawka tego typu najlepiej na rynku zabezpiecza przed wysunięciem narzędzia, a także zapobiega drganiom i zapewnia najwyższą stabilność i dostępność w obróbce frezarskiej i wiertarskiej