Un futuro più verde per il settore aerospaziale
Gli OEM devono adottare un approccio olistico per gli aerei di domani.
Essendo tra le principali responsabili delle emissioni globali di CO2, l'industria aerospaziale è spinta a fornire aerei sempre più ecologici, più leggeri e in grado di coprire distanze più lunghe. Tuttavia, per raggiungere questo risultato è necessario utilizzare materiali difficili da lavorare come l'alluminio e le superleghe resistenti al calore (HRSA). Qui, Sébastien Jaeger, Industry Solution Manager – Aerospace per Sandvik Coromant, spiega come gli OEM del settore aerospaziale possono adottare soluzioni di attrezzamento avanzate per lavorare in modo sostenibile questi componenti difficili.
Secondo il World Economic Forum (WEF), "Raggiungere l'obiettivo di zero emissioni nette di CO2 entro il 2050 non solo contribuirà a creare un futuro sostenibile dal punto di vista ambientale ma aiuterà l'industria aeronautica a diventare finanziariamente resiliente e competitiva nel suo complesso." Tuttavia, mentre la mobilità elettrica si afferma sempre maggiormente nel settore automobilistico - nel mese di agosto 2021, le vendite di veicoli elettrici nel Regno Unito hanno superato quelle dei diesel - nel settore aerospaziale questo percorso sarà più lento.
In generale, gli aerei elettrici non dovrebbero essere usati diffusamente fino al 2035. Lonely Planet riferisce che - anche se easyJet spera di utilizzare aerei elettrici sulle rotte inferiori a 311 miglia (500 km) entro il 2030 e la Norvegia mira a rendere elettrici tutti i voli a corto raggio entro il 2040 - "non voleremo molto presto a lungo raggio su jumbo ricaricabili: le batterie sono semplicemente troppo pesanti."
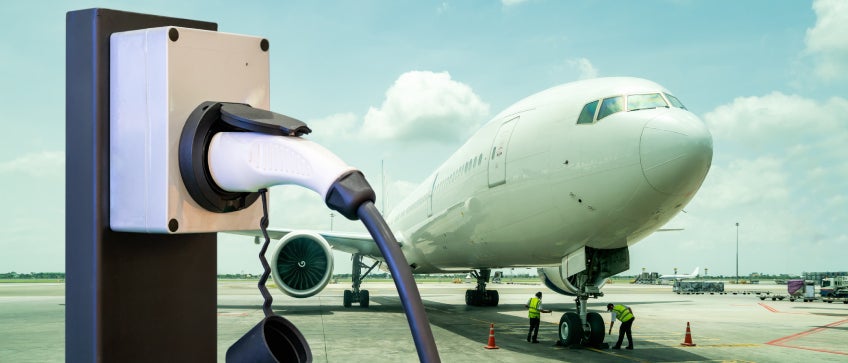
Gli aerei elettrici dovrebbero poter essere utilizzati diffusamente nel 2035.
Per essere utilizzabili, le batterie devono diventare più leggere ma, per controbilanciare il problema, anche i produttori OEM devono costruire componenti più leggeri. E l'alluminio - soprattutto quei nuovi tipi di alluminio caratterizzati da livelli superiori di robustezza e resistenza alla fatica - sarà certamente tra i materiali più utilizzati.
Stiamo assistendo anche a un aumento dell'uso di nuove superleghe resistenti al calore (HRSA). In effetti, le HRSA vengono già utilizzate per i componenti degli aerei che hanno requisiti prestazionali estremi perché mantengono la loro durezza anche in presenza di calore intenso. Le proprietà di questi materiali si riveleranno fondamentali dato che, per rendere più sostenibili i viaggi aerei, i motori saranno sottoposti a maggiori sforzi e a un maggiore riscaldamento.
I componenti, inoltre, devono essere prodotti con tolleranze più strette e design più differenziati. Come accade per le auto elettriche, il design degli aerei elettrici di domani - telai e motori inclusi - cambierà maggiormente da un costruttore all'altro rispetto agli attuali velivoli con motore a combustione interna. Per il telaio, alcuni OEM stanno sperimentando soluzioni con forma a triangolo, fusoliera integrata nelle ali (BWB) e ali controventate (SBW). Altri OEM si attengono a configurazioni tradizionali che prevedono "grande corpo tubolare, ali e motore".
Ci saranno anche motori di diversa architettura come, ad esempio, motori elettrici, a batteria, elettromagnetici o ibridi ovvero motori convenzionali assistiti da motori elettrici. Agli OEM sarà richiesto di produrre una crescente varietà di componenti con tolleranze strette, oltre che di trovare nuovi modi per ridurre il rumore, il peso e le emissioni - tutti fattori che influiscono sulle prestazioni dei sistemi elettrici. Tuttavia, considerato che i componenti in alluminio ed HRSA sono difficili da lavorare, raggiungere questo obiettivo in modo sostenibile ed economicamente conveniente sarà una sfida.
Progressi rapidi
Un modo di costruire aerei più leggeri e più efficienti in termini di consumo di carburante è quello di utilizzare tecniche di produzione additiva (AM). La produzione additiva consente di sviluppare componenti personalizzati di forma molto complessa ed elementi funzionali con tolleranze strette; in questo modo, anche le parti difficili da lavorare come le strutture a traliccio possono essere realizzate più facilmente. Secondo i risultati di una ricerca della società di software Dassault Systemes, "nel settore aerospaziale, la riduzione del peso derivante dai processi AM può comportare un risparmio energetico anche del 25 %" mentre "ogni chilogrammo (2.2 lb) di minor peso su un volo può far risparmiare fino a 3.000 dollari all'anno di carburante."
Ma la produzione additiva è a sua volta sostenibile? Uno studio, realizzato con il contributo del Dipartimento di Ingegneria della Produzione presso l'Università Tecnica di Cluj-Napoca in Romania, descrive la produzione additiva come "una grande alternativa ai metodi di produzione tradizionali (TM) come lo stampaggio a iniezione, la pressofusione o la lavorazione." E continua: "La produzione additiva consente di abbassare i costi e di aumentare l'efficienza energetica rispetto ai processi convenzionali."
La produzione additiva avrà un effetto importante anche sulla diversità dei modi in cui i prodotti verranno fabbricati. I vantaggi possono includere la riduzione delle emissioni di carbonio, un minor consumo di materiali e minori esigenze di trasporto, dato che i componenti possono essere realizzati all'interno anziché fatti arrivare dall'esterno.
Inoltre, grazie alla prototipazione rapida, i costruttori potranno realizzare componenti più complessi, compatti e innovativi. La prototipazione rapida implica l'uso di diverse tecniche ma l'obiettivo è quello di produrre rapidamente un prototipo 3D tangibile da un file CAD (Computer Aided Design). Con questi prototipi, è possibile eseguire prove su piccoli volumi di nuovi materiali prima della produzione su larga scala, in modo da garantire che i componenti vengano effettivamente realizzati secondo i criteri previsti di innovazione, qualità e precisione.
Abbiamo visto che gli OEM del settore aerospaziale possono adottare nuovi metodi per produrre componenti più complessi. Ma dispongono anche degli utensili necessari - soprattutto quando si parla di alluminio duro ed HRSA?
Questi materiali richiedono l'uso di utensili con livelli superiori di resistenza all'usura e durata utensile. Questo è il motivo per cui Sandvik Coromant ha sviluppato la qualità S205 per gli inserti in acciaio utilizzati nelle operazioni di tornitura. La metallurgia di S205 prevede uno strato Inveio® di cristalli unidirezionali molto ravvicinati. Ciò crea una robusta barriera protettiva intorno all'inserto che rafforza l'utensile e ne migliora le proprietà meccaniche. L'inserto si è già rivelato utile nella produzione di una serie di componenti per aerei, tra cui dischi turbina, anelli e alberi. I clienti di Sandvik Coromant hanno già dichiarato che, con S205, riescono a lavorare a velocità di taglio del 30-50% superiori rispetto a quelle ottenibili con qualità concorrenti per la tornitura di HRSA.
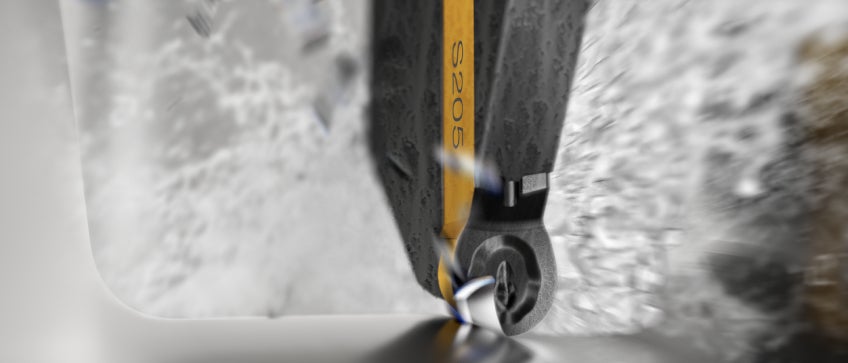
Approccio olistico
Ora che abbiamo considerato processi di produzione e utensili, dobbiamo chiederci com'è possibile combinarli al meglio. Se i sistemi non sono concepiti per lavorare bene insieme, può volerci tempo per creare una soluzione pienamente integrata.
A tal fine, Sandvik Coromant supporta i clienti del settore aerospaziale con ciò che chiamiamo soluzioni per componenti. La soluzione è frutto di un processo che comporta diverse fasi, tra cui l'analisi dei requisiti della macchina e l'esame dei costi per componente. È previsto anche uno studio dei metodi di produzione al collaudo, considerando sia il tempo di lavoro in base al metodo applicato (MTM) che i processi degli utenti finali. La soluzione per componenti include anche la programmazione CAM (Computer Aided Manufacturing) e la gestione di progetti locali o internazionali.
Per un cliente di Sandvik Coromant che aveva problemi di truciolabilità, la soluzione per componenti ha permesso di individuare la causa e trovare una soluzione. Per questo cliente, gli specialisti di Sandvik Coromant hanno sviluppato una nuova strategia con curve dinamiche che ci ha permesso di controllare costantemente la truciolabilità. Abbiamo chiamato questo nuovo approccio "scoop turning" e lo abbiamo brevettato. Con lo "scoop turning", il cliente ha ottenuto una riduzione dell'80% del tempo ciclo, con un ottimo controllo truciolo e una durata utensile raddoppiata.
Inoltre, il cliente è riuscito a passare da quattro macchine a una, riducendo la necessità del multi-tasking, con processi di lavorazione più sicuri e una produzione "green light". L'uso di meno macchine e la possibilità di completare la produzione con meno cambi utensile, grazie a qualità più tenaci come la S205, saranno elementi chiave per rendere più sostenibile la produzione nel settore aerospaziale.
Anche il software assumerà un ruolo fondamentale, come CoroPlus® Tool Guide che fa parte del portfolio digitale di Sandvik Coromant. I clienti possono prendere decisioni cruciali sulla scelta degli utensili e dei parametri di taglio prima ancora di aver iniziato la produzione.
Un sistema circolare
Oltre che considerare i nuovi approcci agli utensili e alla produzione, gli OEM del settore aerospaziale possono agire anche sulla produzione. Secondo un report di Air Transport Action Group (ATAG), Kaiser - l'azienda che fornisce alluminio alla Boeing - ora adotta un sistema di riciclo ad anello chiuso che è diventato uno dei più grandi programmi del suo genere nel settore. Kaiser stima che, grazie a questo programma, sarà possibile riutilizzare ogni anno circa dieci milioni di chilogrammi di scarti e rottami metallici.
In Sandvik Coromant, abbiamo avviato il nostro sistema circolare per riciclare gli utensili in metallo duro che prevede il riacquisto degli utensili usurati dai clienti e il riutilizzo del materiale per produrne di nuovi. Il risultato è che la maggior parte delle materie prime utilizzate negli utensili in metallo duro di Sandvik Coromant provengono da scarti. In tal modo, cerchiamo di perseguire un business sostenibile in un ambiente in cui le risorse sono limitate e minimizziamo il volume di scarti. E facendolo, ci siamo accorti che produrre utensili con materiale riciclato richiede il 70% di energia in meno, mentre le emissioni di anidride carbonica si riducono del 40%.
All'industria aerospaziale si chiede di produrre aerei sempre più ecologici, più leggeri e in grado di viaggiare per distanze più lunghe. E disponendo dei giusti processi e degli utensili adeguati - per non parlare di un approccio più olistico alla produzione - gli OEM del settore possono fare la loro parte per creare un futuro più "verde".