Un modo affidabile per eliminare i microdifetti
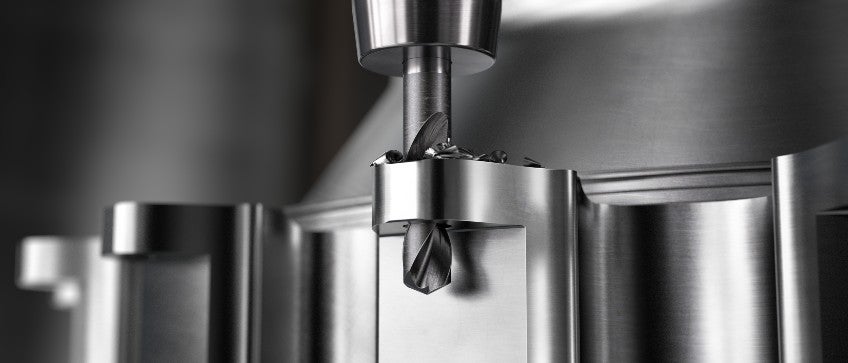
Test con punte in metallo duro dal design ottimizzato aprono nuove possibilità in termini di qualità del foro.
"Misurare due volte e tagliare una sola" è un'espressione diffusa nel settore manifatturiero ma, nella lavorazione di materiali difficili, è più facile a dirsi che a farsi. Ecco perché, quando un costruttore leader nel settore aerospaziale ha cercato di eliminare un'intera fase secondaria dai propri processi di foratura, migliorando nel contempo la qualità del foro, si è rivolto al leader globale nel taglio dei metalli. James Thorpe, Global Product Manager di Sandvik Coromant, spiega perché il design della punta sia fondamentale per realizzare fori di migliore qualità.
La realizzazione di fori è il processo di lavorazione più comune in assoluto, ma anche uno di quelli che viene più dato per scontato. Molte officine meccaniche non capiscono perché dovrebbero modificare o aggiornare il setup esistente per le operazioni di foratura e si limitano a utilizzare gli stessi utensili e parametri per anni e anni. Tuttavia, considerando anche gli effetti imprevedibili della pandemia COVID-19, tutto questo è destinato a cambiare. I costruttori si sono confrontati con cambiamenti imprevedibili e duraturi del mercato e ora vedono la necessità di adattare la loro produzione.
La maggior parte dei costruttori, ad esempio, sta esplorando nuovi fornitori e nuovi prodotti. Di conseguenza, le officine che una volta erano specializzate in una determinata area di produzione stanno aprendo i propri torni CNC e le proprie fresatrici a una più ampia varietà di materiali tenaci e difficili. Al tempo stesso, i costruttori si ritrovano a esplorare nuovi modi per aumentare i profitti e ridurre i tempi ciclo, senza sacrificare la qualità dei prodotti.
In altre parole, per i costruttori è arrivato il momento di ripensare ai propri metodi di realizzazione dei fori.
Lo "strato bianco"
L'integrità superficiale dei fori rappresenta una grande preoccupazione per i costruttori aerospaziali e le aziende di ingegneria generale che mirano a espandersi nell'aerospaziale. Una migliore qualità del foro è fondamentale per prevenire la rottura dei componenti ed è in gran parte determinata dai processi di produzione impiegati per la lavorazione o la finitura dei fori.
Le soluzioni di attrezzamento e le geometrie dei taglienti continuano a evolversi al fine di soddisfare i più elevati standard di lavorazione e qualità dei componenti. L'utilizzo di refrigerante, poi, riduce l'accumulo di calore nell'utensile. Una serie di test ha dimostrato che ciascuno di questi fattori può contribuire a controllare il cosiddetto "strato bianco" che si forma sui materiali da lavorare.
Il termine "strato bianco" è stato coniato da un costruttore leader globale nel settore aerospaziale, nonché cliente di Sandvik Coromant. Fa riferimento a una sottile struttura a grana ultrafine osservabile a seguito della foratura dei componenti, provocata dal calore della punta. Non soltanto lo strato bianco può modificare le proprietà superficiali del materiale ma è stato anche dichiarato inaccettabile nell'ambito dei processi di gestione della qualità del cliente.
Il costruttore applica un rigoroso processo di finitura ai fori praticati nei componenti aerospaziali, tra cui dischi turbina, compressori, rulli e alberi. Ecco perché ha scelto di collaborare con Sandvik Coromant per scoprire come si forma lo strato bianco e come controllarlo.
È importante ricordare che lo svolgimento dei test non è stato motivato esclusivamente da finalità legate alla gestione della qualità. A livello dirigenziale, il cliente mirava a ridurre i tempi operativi complessivi e aumentare i profitti, eliminando un intero processo di lavorazione secondario.
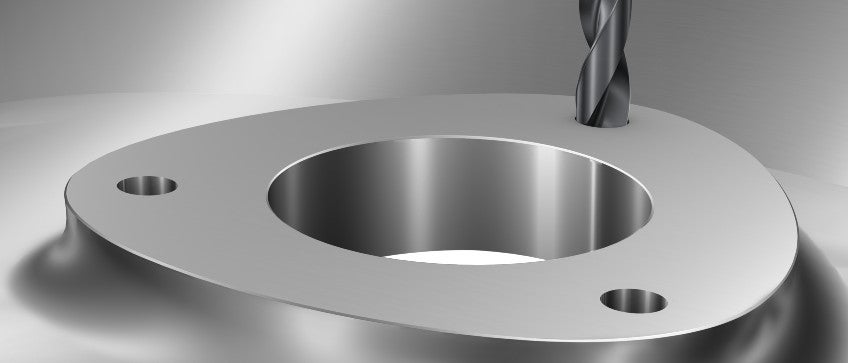
L'integrità superficiale dei fori rappresenta una grande preoccupazione per i costruttori aerospaziali e le aziende di ingegneria generale che mirano a espandersi nell'aerospaziale. Qui, la foratura di un mozzo su una cassa in HRSA con CoroDrill 860 con geometria -SM
.
Secondo atto
Il processo secondario in questione avviene dopo la realizzazione del foro mediante la punta in metallo duro e può implicare operazioni di alesatura o fresatura a tuffo per finire il componente. Tale fase secondaria mira soprattutto a soddisfare requisiti di integrità superficiale - limitando problematiche come quella dello strato bianco - anziché di precisione dimensionale, fatta eccezione per la lavorazione di fori con tolleranze strette.
In termini di spese generali, questo processo secondario risulta ancora più costoso del mantenimento di dati di taglio ridotti, ossia l'altro metodo per preservare l'integrità superficiale. Ecco perché il cliente di Sandvik Coromant ha voluto esplorare la potenziale eliminazione dell'intero processo. Un fornitore in grado di produrre un foro già perfettamente dimensionato, senza alcun processo secondario, si trova in una posizione commerciale sufficientemente solida da ridurre notevolmente il costo per componente.
L'indagine sulle cause e i possibili mezzi di prevenzione dello strato bianco prevedeva quattro test di foratura su Inconel 718, una lega di nichel-cromo ad alta resistenza molto diffusa nelle applicazioni aerospaziali. Si trattava del primo test di questo tipo per il cliente.
I test hanno valutato le prestazioni di foratura di due punte in metallo duro integrale di Sandvik Coromant, CoroDrill® R840 e CoroDrill® R846. Ciascun test è stato eseguito con due diversi set di parametri di taglio: una velocità di avanzamento di 58 mm/min e 98 mm/min e una velocità di rotazione di 829 giri/min e 757 giri/min rispettivamente. La forza di taglio e il momento torcente sono stati misurati per tutta la durata dei test, come anche lo spessore dello strato bianco.
In seguito ai test, CoroDrill R840 è stata sostituita da CoroDrill® 860 con geometria -GM e CoroDrill R846 è stata sostituita da CoroDrill® 860 con geometria -SM. Ognuno di questi utensili di nuova generazione è progettato per ottimizzare ulteriormente la durata utensile, senza compromettere la qualità del foro.
I risultati hanno fornito preziose informazioni sulle cause dello spessore dello strato bianco. Particolarmente degno di nota è stato il fatto che CoroDrill R846 ha generato una minor quantità di strato bianco, per via della preparazione dei suoi taglienti ricurvi e radiali. Invece, si ritiene che i taglienti diritti e lo smusso sul tagliente di CoroDrill R840 siano associati all'aumento della forza di taglio, del momento torcente e dello spessore dello strato bianco. Se ne deduce che il design della punta determina se è possibile ottenere un'elevata qualità del foro e uno strato bianco ridotto senza sacrificare i dati di taglio.
Non soltanto i test svolti dal costruttore aerospaziale insieme a Sandvik Coromant rivelano nuovi aspetti relativi allo strato bianco, ma l'azienda è anche riuscita a eliminare alcuni processi secondari, tra cui operazioni di alesatura e fresatura a tuffo, il che ha comportato notevoli vantaggi in termini di tempi e costi. Inoltre, i risultati hanno convalidato il design della gamma di punte in metallo duro CoroDrill 860 di Sandvik Coromant.
Migliore fin dalla progettazione
La gamma include la già menzionata CoroDrill 860 con geometria -GM, progettata per garantire una buona versatilità nella foratura dei difficili materiali ISO P, M, K e H in tutti i settori industriali. CoroDrill 860 con geometria -SM è ottimizzata per la lavorazione di materiali ISO S come le superleghe resistenti al calore (HRSA), il titanio e l'Inconel. Quest'ultima punta si è dimostrata particolarmente utile nel settore aerospaziale.
Con CoroDrill 860 con geometria -GM e CoroDrill 860 con geometria -SM, i tecnici di Sandvik Coromant hanno dimostrato che una maggiore durata utensile e una migliore qualità del foro dipendono dal design stesso della punta. CoroDrill 860 con geometria -GM presenta un innovativo design con scanalatura levigata, che migliora l'evacuazione truciolo e implica un'elevata robustezza e forze di taglio ridotte durante la foratura.
CoroDrill 860 con geometria -SM, d'altra parte, presenta una nuova qualità e una geometria ottimizzata e rifinita, che aumenta ulteriormente la durata utensile nella lavorazione di materiali HRSA difficili. Il risultato è una migliore qualità del foro.
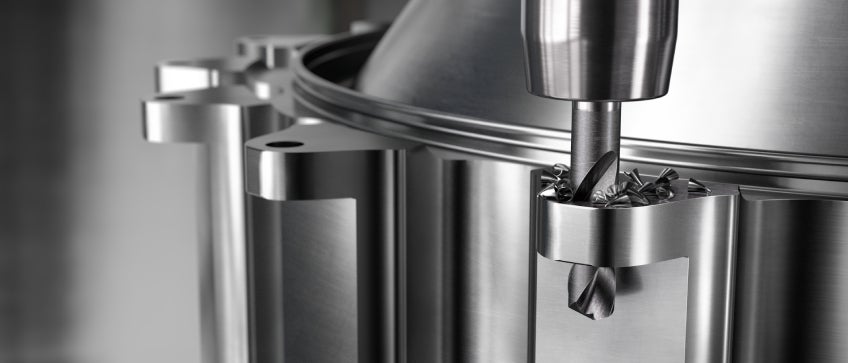
CoroDrill® 860 con geometria -SM dimostra che l'aumento di durata utensile e qualità del foro dipendono dal design stesso della punta.
CoroDrill 860 ha già dimostrato il suo valore nei test preliminari alla commercializzazione in vari settori. Un'azienda di ingegneria meccanica in Francia ha messo CoroDrill 860 con geometria -GM all'opera su componenti in acciaio strutturale AISI 4140, riuscendo a ottenere fori di elevata qualità con entrate concave e convesse della punta e buoni risultati in termini di rettilineità e tolleranza. Da allora, l'azienda ha stabilito un nuovo rapporto commerciale con Sandvik Coromant.
Un altro cliente di Sandvik Coromant, un costruttore di ingegneria generale italiano, utilizzando CoroDrill 860 con geometria -GM nella lavorazione della resistente lega di acciaio 34CrNiMo6, è riuscito a ottenere un aumento della produttività del 45% superiore rispetto a una punta concorrente. Il tutto in aggiunta a un aumento della durata utensile del 100%. D'altra parte, CoroDrill 860 con geometria -SM ha fornito risultati straordinari nella lavorazione di Inconel 718. In particolare, i test svolti a Katowice, in Polonia, hanno rivelato un miglioramento della durata utensile del 180% con CoroDrill 860 con geometria -SM rispetto a CoroDrill R840.
Indipendentemente dal settore - che sia quello aerospaziale, dell'ingegneria generale o altro - è possibile ottenere elevate prestazioni degli utensili quando la punta è progettata appositamente per tale fine. Nel mentre, altri strumenti online come CoroPlus® Tool Guide di Sandvik Coromant possono fornire un ulteriore supporto. Accedendo all'applicazione tramite browser web e inserendo materiale da lavorare, diametro del foro e profondità, l'utente può trovare il miglior utensile integrale rotante e i dati di taglio più adatti ai propri requisiti.
Se la regola di "misurare due volte e tagliare una sola" non è ancora stata messa completamente in pratica, le prestazioni di CoroDrill 860 con geometria -GM e CoroDrill 860 con geometria -SM possono aiutare i costruttori a ripensare i propri metodi di foratura.