Tornitura dei materiali esotici
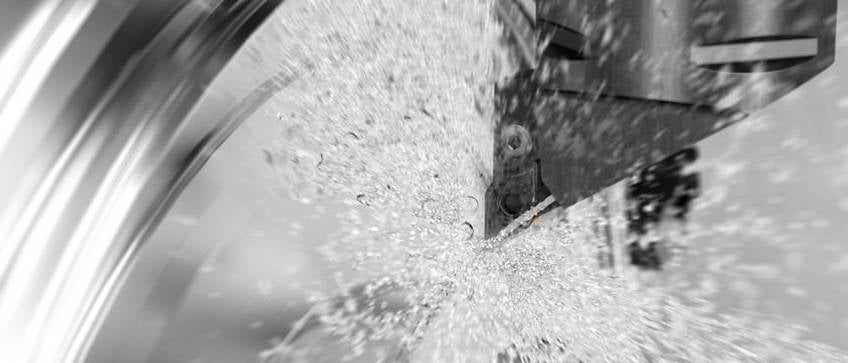
Le superleghe resistenti al calore e le leghe di titanio sono difficili da lavorare. Non somigliando ad altri metalli, questi materiali vengono chiamati "esotici". Hanno proprietà straordinarie come, ad esempio, il rapporto resistenza-peso, il mantenimento della resistenza e della durezza ad alte temperature e un'eccellente resistenza alla corrosione.
Tuttavia, essendo anche impegnativi da lavorare, hanno a loro volta bisogno di soluzioni "esotiche" che devono essere accuratamente pianificate con la scelta attenta di utensili, metodi e percorsi che garantiscano efficienza, sicurezza e buoni risultati.
Questa presentazione esamina i requisiti di lavorazione e gli sviluppi che hanno ottimizzato prestazioni e sicurezza del processo nella tornitura.
Componenti dalle proprietà uniche ma difficili da lavorare
La capacità di lavorare un materiale è definita da diversi fattori che influiscono sui requisiti e determinano i risultati delle operazioni di taglio. In senso lato, si tratta della facilità di taglio del materiale di un componente in relazione alla tendenza all'usura dell'utensile e al modo in cui si possono formare i trucioli. Con la differenza che, nella maggior parte dei casi, questi materiali esotici hanno una scarsa lavorabilità. Sono considerati impegnativi da tagliare - ma non difficili, se affrontati nel modo giusto.
I più esotici tra i materiali relativamente comuni sono classificati sotto il gruppo ISO S: superleghe resistenti al calore (HRSA) e leghe di titanio. Per la lavorazione, tutti questi materiali possono essere suddivisi in diversi sottogruppi, a seconda della composizione, delle condizioni e delle proprietà. La natura chimica e la composizione metallurgica di una lega classificata S ne determinano le proprietà fisiche e di conseguenza la lavorabilità. Il controllo truciolo è generalmente impegnativo a causa della segmentazione dei trucioli e non è raro che la forza di taglio specifica (misura diretta di quanto un materiale sia duro da tagliare che determina la forza di taglio e la potenza necessarie) sia doppia rispetto a quella dell'acciaio.
La ragione principale per cui le HRSA sono difficili da tagliare è la loro elevata resistenza alle alte temperature. Non si ammorbidiscono, non scorrono come la maggior parte degli altri materiali e si incrudiscono immediatamente. L'elevato carico meccanico e il notevole calore si concentrano sul tagliente. Le leghe a base di nichel, ferro o cobalto sono sottogruppi di HRSA che vantano capacità uniche, particolarmente adatte ai componenti per il settore aerospaziale, la produzione di energia e l'industria medicale, dato che le loro proprietà non cambiano molto fino al punto di fusione. Sono anche molto resistenti alla corrosione. Dal punto di vista della lavorabilità, tuttavia, hanno bisogno di una macchina potente, un setup rigido, inserti con qualità e geometrie specifiche, applicazione ottimizzata del refrigerante e, infine, del giusto metodo di lavorazione e del giusto avvicinamento degli utensili. Certamente occorre una maggiore pianificazione e quindi più lavoro a livello di front-end della produzione.
Anche le leghe di titanio sono divise in sottogruppi con diversi gradi di lavorabilità. Generalmente, la lavorabilità viene valutata in base alla tenacità, rendendo molto impegnativi i requisiti che devono avere utensili e metodi. I vincoli sono dovuti alla bassa conducibilità termica, all'elevata resistenza all'alta temperatura e a trucioli sottili, molto spezzettati e con tendenza a escoriare la superficie lavorata che creano una stretta area di contatto sul petto dell'inserto, concentrando elevate forze di taglio vicino al tagliente. La formazione dei trucioli può essere ciclica, comportando forze di taglio variabili, e alcune leghe hanno un livello relativamente alto di carburi che rendono il materiale ultra-abrasivo. Velocità di taglio eccessive possono provocare una reazione chimica tra il truciolo e il materiale dell'utensile, con i conseguenti rischi di scheggiatura/frattura del tagliente e incollamento/saldatura del materiale sui taglienti. Alcune leghe si incrudiscono facilmente, dando luogo a un'usura per diffusione che provoca un'eccessiva formazione di bave. Ciò può rendere difficili anche le operazioni successive.
Materiali esotici, sì, ma la finestra per una lavorazione di successo di molte HRSA e leghe di titanio è relativamente piccola.
Quando si procede alla tornitura di questi materiali …
… il successo dipende dal bilanciamento dell'effetto combinato del materiale e dei fattori applicativi. Il rispetto di alcune regole base contribuisce enormemente a ottenere buoni risultati:
- pianificare una buona strategia di lavorazione, quanto più dettagliata possibile,
- stabilire il miglior avvicinamento degli utensili,
- definire i migliori percorsi utensile e utilizzare un portautensili molto stabile,
- utilizzare le migliori tra le tecnologie nuove e specifiche per gli utensili da taglio,
- usare i corretti dati di taglio per ottenere sicurezza del processo e produttività,
- utilizzare il calcolo della lunghezza di taglio a spirale per una lavorazione prevedibile,
- applicare correttamente il refrigerante - moderne soluzioni ad alta pressione,
- avvalersi delle raccomandazioni e del supporto che possono fornire gli specialisti.
Considerata la presenza di fattori critici e decisivi come, ad esempio, la determinazione dello stato/condizione del materiale da lavorare, il processo di lavorazione dovrebbe essere pianificato sempre con attenzione. La scelta degli utensili e dei metodi dovrebbe dipendere dalle condizioni dei pezzi da lavorare e dai processi a cui sono stati sottoposti, che si tratti di fusione, forgiatura, formazione in barre, trattamento termico, trattamento in soluzione o invecchiamento. Le condizioni della superficie del pezzo variano e influiscono sulla lavorazione, così come la durezza. La strategia di tornitura dovrebbe considerare anche i vincoli imposti dalle caratteristiche di design del componente che deve essere lavorato, oltre che le varie fasi di lavorazione ovvero la sgrossatura (prima fase), la semifinitura (fase intermedia) e la finitura (ultima fase). Caratteristiche complesse e integrità superficiale sono problematiche comuni.
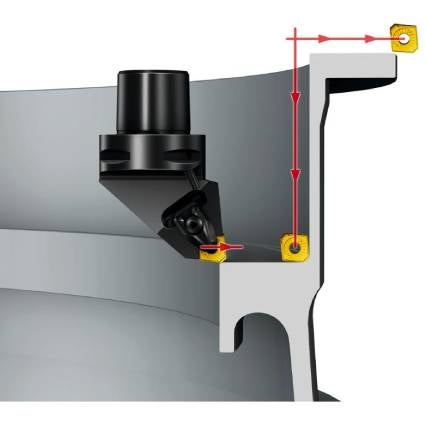
Quando si pianifica la tornitura di materiali esotici, design del componente, materiale e condizioni sono le basi. Se applicabile, stabilire come devono essere eseguite la prima fase, la fase intermedia e l'ultima fase di lavorazione in relazione alle condizioni del materiale e ai requisiti di qualità. La pianificazione dei percorsi utensile e il ricorso alla riduzione dell'avanzamento durante la programmazione saranno decisivi per entità dell'usura, tipo di utensile, tempi ciclo e sicurezza.
In questi materiali, l'azione di taglio …
… è notevolmente influenzata dall'avvicinamento del tagliente al pezzo. L'angolo di registrazione del tagliente, insieme alla geometria dell'inserto, è quello che decide prestazioni, durata utensile, sicurezza e risultati. Le forme degli inserti devono spesso essere scelte in relazione al taglio da effettuare. Tuttavia, dovrebbe essere sempre considerato il fatto che un piccolo angolo di registrazione favorisce le prestazioni e la durata utensile.
La scelta della qualità degli inserti deve avvenire anche in base all'angolo di registrazione. Tra le altre cose, questo angolo influisce sul tipo di usura ad intaglio del tagliente che, se troppo elevato, pregiudica i risultati e provoca la prematura rottura dell'utensile. Prevedere il giusto avvicinamento, quindi, significa anche poter scegliere la qualità d'inserto in grado di garantire non solo la produttività più elevata ma anche una lunga durata utensile e la necessaria sicurezza.

L'angolo di registrazione dell'utensile da taglio influisce su spessore truciolo, avanzamento, forze di taglio e lavorazioni possibili. Con i materiali esotici, la scelta di questo angolo ha conseguenze dirette sulla produttività e sull'affidabilità del processo, influendo su forma dell'inserto, raggio di punta e capacità di utilizzo del materiale dell'utensile. Gli inserti rotondi e gli inserti tipo xcel sono normalmente le scelte migliori.
La scelta del materiale dell'utensile (qualità d'inserto) dovrebbe essere determinata anche in base al tipo di operazione di tornitura in questione - sgrossatura, semifinitura o finitura - oltre che dalle condizioni del pezzo e dal tipo di taglio. Considerata la durezza di questi materiali, la deformazione plastica del tagliente dovrebbe sempre essere considerata il principale fattore di rischio quando si seleziona la qualità d'inserto (l'usura ad intaglio, come già detto, è legata soprattutto all'angolo di registrazione e alla profondità di taglio). La qualità degli inserti dovrebbe essere scelta tenendo conto anche della loro forma dato che ciò incide sulla robustezza e va valutato insieme ad avvicinamento, carico dei trucioli e tipo di taglio, continuo o interrotto. Per la lavorazione delle HRSA è quindi fondamentale utilizzare qualità specifiche.
I requisiti principali sono un elevato grado di durezza a caldo, il giusto livello di tenacità e una sufficiente adesione del rivestimento dell'inserto. Gli inserti multitaglienti per questi materiali dovrebbero essere caratterizzati da una geometria positiva, un tagliente affilato ma forte e un rompitrucioli relativamente aperto.
Definire i dati di taglio più adeguati è vitale per il successo con questi materiali. La velocità di taglio è limitata dalla combinazione tra velocità, avanzamento e profondità di taglio e può essere ottimizzata per fornire livelli superiori di produttività, sicurezza e qualità. La velocità di taglio è legata alla generazione di calore e ai suoi effetti sull'inserto; deve essere abbastanza alta da conferire al truciolo sufficiente plasticità ma non così alta da sbilanciare il materiale dell'utensile. Le velocità rientrano generalmente tra 130 e 260 sfm (40 ... 80 m/min) con inserti specifici in metallo duro e tra 490 e 1310 sfm (150 ... 400 m/min) con gli inserti in ceramica.
La velocità di avanzamento è il principale fattore che influisce su tempi di taglio e spessore del truciolo. Con i materiali esotici, questa velocità deve essere bilanciata ancora più attentamente in quanto i limiti sono relativamente stretti: nella sgrossatura, il truciolo deve essere massimizzato ma non tanto da sovraccaricare il tagliente mentre, nella finitura, il truciolo deve essere abbastanza spesso da evitare la generazione di calore eccessivo e l'incrudimento.
La profondità di taglio influisce spesso sull'avvicinamento del tagliente e, di conseguenza, deve rimanere al di sotto di un certo valore. Quando si usano inserti rotondi sulle HRSA, ad esempio, la profondità di taglio non dovrebbe superare il 15% del diametro dell'inserto. Per la profilatura, la profondità di taglio deve essere programmata attentamente. Essendo presenti cavità e spallamenti, è necessario non superare l'arco più adeguato di impegno del tagliente.
Per ciò che riguarda la durata utensile, è importante lavorare correttamente con la lunghezza di taglio a spirale (SCL). Fare questo significa poter prevedere e programmare i fermi macchina per il posizionamento dell'inserto e poter completare le passate, con un utensile usato alla giusta velocità, senza che il tagliente non riesca più ad assicurare la finitura superficiale.
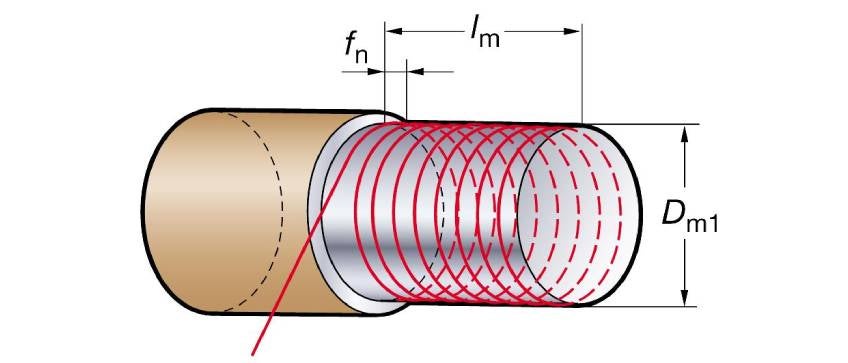
Il calcolo della lunghezza di taglio a spirale aiuta a prevedere il tempo o la lunghezza di taglio, in modo da ridurre il tempo di lavorazione e migliorare la finitura superficiale sui materiali esotici esigenti. I fermi macchina per il cambio inserto vengono quindi pianificati con la lunghezza di taglio a spirale per meglio adattarsi all'operazione e ai dati di taglio, in modo da ottimizzare la durata utensile e il tasso di utilizzo della macchina.
L'usura dell'utensile dipende molto …
… dalle elevate forze di taglio associate alle più elevate temperature del tagliente, che tendono a sviluppare certi tipi di usura del tagliente. I principali tipi di usura sono la già menzionata usura ad intaglio (un tipo di usura meccanica che si verifica in corrispondenza della linea di taglio); la deformazione plastica del tagliente - una conseguenza della combinazione di valori elevati di temperatura e pressione - e l'usura per abrasione, causata principalmente dai materiali più duri. Un altro tipo di usura è lo sfaldamento superiore degli inserti in ceramica, consistente nella perdita degli strati superiori del tagliente. L'avvicinamento del tagliente gioca un ruolo importante.
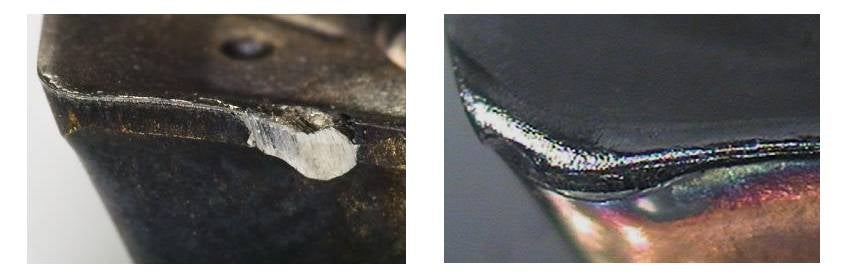
La scelta della qualità d'inserto non è così direttamente collegata alla sgrossatura e alla finitura dei materiali esotici come lo è per altri materiali. In effetti, la scelta della qualità è più un fattore di ottimizzazione - solo leggermente più complesso - che dipende dalla forma dell'inserto, dall'avvicinamento del tagliente e dal tipo di operazione. I modelli di usura distruttivi, come l'usura ad intaglio e la deformazione plastica, devono essere contenuti soprattutto dalla giusta combinazione di utensili, dati di taglio e metodo. Gli inserti in metallo duro, le moderne ceramiche sialon e, in una certa misura, le ceramiche whisker, sono spesso la scelta più adatta e ampiamente applicabile.
L'angolo di registrazione più adatto per la tornitura dei materiali esotici è piccolo, uguale o inferiore a 45 gradi. La condizione peggiore è quella in cui l'angolo di registrazione è di 90/0 gradi o la profondità di taglio è superiore al raggio di punta dell'inserto. La giusta ampiezza dell'angolo è associata a trucioli sottili e avanzamenti più elevati.
Per la tornitura delle HRSA, è l'angolo di registrazione dell'utensile a determinare se è meglio utilizzare un inserto con rivestimento PVD o CVD. Il rivestimento serve a proteggere dagli effetti termici. Il rivestimento PVD è adatto per un angolo di registrazione di 90/0 gradi mentre il rivestimento CVD per 45 gradi. La tornitura del titanio, d'altra parte, non trae alcun vantaggio dal rivestimento dell'inserto. In questo caso, è più importante assicurare la condizione del tagliente più adatta utilizzando, ad esempio, inserti rotondi per la finitura. Le nuove famiglie di inserti con rivestimento PVD assicurano elevata durezza e buona resistenza alla deformazione del tagliente e agli shock termici. Se combinate con taglienti affilati, possono eccellere anche nelle operazioni di sgrossatura e finitura di materiali con tendenza all'incollamento.
La giusta forma dell'inserto …
… è un importante fattore applicativo nella lavorazione di questi materiali. La forma rotonda (R) è diventata una delle principali raccomandazioni per questi materiali. L'inserto rotondo assicura resistenza per un tagliente affilato e positivo; uno spessore del truciolo variabile sul tagliente lungo che permette avanzamenti elevati; un grande raggio dell'inserto che non limita la velocità di avanzamento grazie alla finitura superficiale creata. L'inserto rotondo offre anche la flessibilità di programmazione necessaria a eseguire quelle operazioni di profilatura ed esecuzione di tasche richieste da molti componenti.
Un inserto di forma quadrata (S) è in alcuni casi il più adatto alla prima fase di lavorazione, grazie alla sua capacità di effettuare passate di sgrossatura in varie direzioni con un angolo di 45 gradi. L'inserto di forma rombica (C) è flessibile in termini di percorsi utensile e, se di tipo Xcel, assicura un'accessibilità ancora maggiore dell'utensile per la lavorazione di raccordi, spallamenti e cavità. Questa combinazione tra forma dell'inserto e angolo di registrazione di 45 gradi riduce anche le forze di taglio radiali, conferisce al truciolo uno spessore costante e riduce l'usura ad intaglio. Il risultato è una maggiore produttività, una più lunga durata utensile e una migliore sicurezza.
L'ottimizzazione del programma …
… è importante e quelle che seguono sono alcune raccomandazioni per migliorare le prestazioni, soprattutto quando si usano inserti rotondi fondamentalmente adatti ai materiali esotici:
- evitare la lavorazione a tuffo e alleggerire gli impatti; se queste passate sono necessarie, dimezzare la velocità di avanzamento,
- durante la tornitura su spallamento, l'avanzamento dovrebbe essere ridotto della metà o l'utensile dovrebbe raggiungere lo spallamento dove il raggio programmato è uguale al diametro dell'inserto (le linee guida prevedono che il raggio minimo programmato sia circa il 25% del diametro dell'inserto e che il raggio del componente equivalga al 75% del diametro dell'inserto. L'avanzamento del centro dell'utensile è per il raggio programmato),
- per la sgrossatura con inserti rotondi, lasciare che il raggio programmato sia uguale al diametro dell'inserto mentre, per la finitura, verificare che il raggio programmato sia superiore al diametro dell'inserto,
- per utilizzare completamente gli inserti, considerare percorsi utensile alternativi, passate multiple e lavorazione in entrambe le direzioni,
- proteggere gli inserti in ceramica con la pre-smussatura del pezzo e avanzare nello smusso,
- mantenere, per tutta la lavorazione, un equilibrio soddisfacente dell'angolo di registrazione rispetto all'arco di impegno dell'inserto. Limitare l'angolo è essenziale per ottenere buone prestazioni e l'uso di inserti rotondi può esaltare i vantaggi derivanti dall'uso delle moderne qualità d'inserto,
- evitare l'avvolgimento dei trucioli durante la profilatura o la lavorazione a tuffo per non sovraccaricare l'inserto, utilizzare percorsi utensile alternativi o un diametro dell'inserto più piccolo,
- considerare la tornitura trocoidale, dividendo il taglio in passate più piccole, specialmente durante l'esecuzione di tasche.
Cosa si dovrebbe considerare nel determinare tipi di utensili e metodi per la lavorazione di HRSA e titanio? Ecco gli aspetti principali di cui tener conto:
- Il refrigerante di precisione è praticamente irrinunciabile. I getti di precisione erogati dietro e in corrispondenza del tagliente, attraverso un sistema di adduzione interna, offrono molti vantaggi alle operazioni di tornitura, fresatura e foratura. L'innovativa tecnologia degli ugelli, disponibile come soluzione standard o speciale con vari campi di pressione, può essere applicata a tutti i tipi di macchina con adeguati sistemi di adduzione del refrigerante. Nelle nuove macchine, la pressione del refrigerante dovrebbe poter essere impostata a 70 bar per facilitare la rottura dei trucioli durante la tornitura del titanio ma, per la tornitura di HRSA, può essere utile disporre di pressioni fino a 200 bar a causa della presenza di trucioli difficili da rompere.
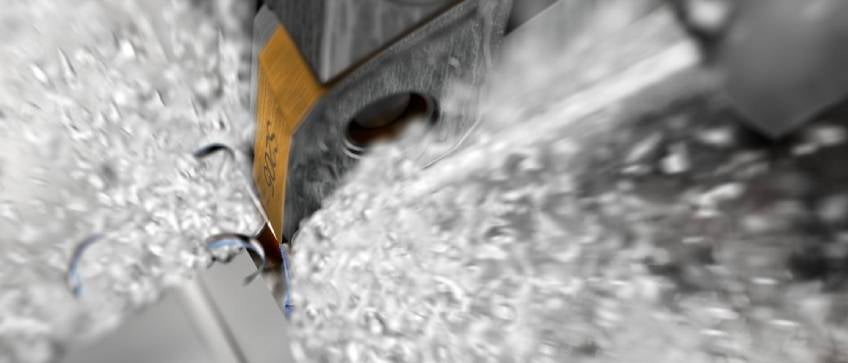
L'uso del refrigerante è un fattore applicativo decisivo nella lavorazione dei materiali esotici. Oggi, l'applicazione di refrigerante di precisione è una funzione high-tech, standard o speciale, così efficiente da fare una chiara differenza per il taglio, la formazione del truciolo, la durata utensile e la produttività. Generalmente, le alte temperature generate durante la lavorazione di questi materiali rendono necessario il raffreddamento ma, utilizzando inserti specifici e applicando il refrigerante attraverso un sistema di adduzione interna, in modo abbondante, ad alta pressione e con precisione, è possibile ottimizzare prestazioni e risultati.
- L'accessibilità è spesso un problema durante la tornitura dei materiali esotici. Considerando la complessità delle caratteristiche e la sporgenza degli utensili, è indispensabile che gli utensili e i metodi scelti siano quelli giusti. I sistemi modulari consentono di disporre di una soluzione affidabile, con lame utensile i cui taglienti si presentano ad angoli e sporgenze differenti. La gamma di adattatori e lame dovrebbe offrire la flessibilità necessaria a costruire quasi ogni tipo di utensile da un inventario limitato di utensili standard, in modo da adattarsi alle diverse configurazioni e assicurare l'accessibilità in spazi ristretti, esterni o interni. Le lame dovrebbero prevedere le necessarie distanze radiali e assiali per raggiungere in profondità le scanalature angolate con il refrigerante di precisione erogato sul tagliente attraverso l'utensile.
- Il materiale dell'utensile è un fattore al centro di qualsiasi operazione di lavorazione e, quando si tratta di materiali esotici, è particolarmente critico. Questo campo di applicazione richiede qualità specifiche e le giuste geometrie, privilegiando soprattutto i più recenti inserti in metallo duro e ceramica. Le qualità in metallo duro non rivestite hanno ancora un ruolo importante ma gli ultimi sviluppi nella tecnologia di rivestimento dell'inserto hanno permesso di ottenere inserti in metallo duro rivestiti che hanno migliorato le capacità del tagliente accorciando il tempo di taglio e prolungando la durata utensile.
- Per minimizzare la tendenza alle vibrazioni, è opportuno considerare l'integrazione del sistema antivibrante nelle barre di alesatura, nelle lame e nelle frese. Le tecnologie antivibranti hanno fatto grandi passi avanti e dovrebbero diventare una scelta ovvia quando le sporgenze dell'utensile rischiano di generare instabilità. Produttività, sicurezza del processo e qualità del componente sono elementi direttamente legati alla qualità e alla disponibilità degli utensili antivibranti. Senza questi utensili, numerose operazioni sarebbero semplicemente impossibili da eseguire: oggi, ad esempio, è possibile eseguire in modo molto efficiente e con eccezionali livelli di finitura operazioni di tornitura interna con sporgenze fino a quattordici volte il diametro (fino a 250 mm).